SCHUNK est un pionnier technologique mondial dans les domaines de la technique de serrage, de la technique de préhension et de la technique d’automatisation. Environ 3 700 collaborateurs dans dix usines et 34 filiales nationales en propre ainsi que des partenaires commerciaux dans plus de 75 pays assurent une présence forte sur le marché. Sur le site de Brackenheim-Hausen en Allemagne, l’entreprise produit des préhenseurs et des composants d’automatisation. Pour faire passer l’approvisionnement de la production manuel à l’automatisation, SCHUNK a choisi de mettre en œuvre un Open Shuttle. Le robot mobile autonome (AMR) garantit des processus efficaces et libère les collaborateurs et collaboratrices pour des activités à valeur ajoutée.
Nous avons parlé avec Pascal Weiland, Responsable Montage & Logistique Gripping Technology & Automation Technology chez SCHUNK, des raisons de l’automatisation, du choix de l’Open Shuttle et de la nouvelle solution.
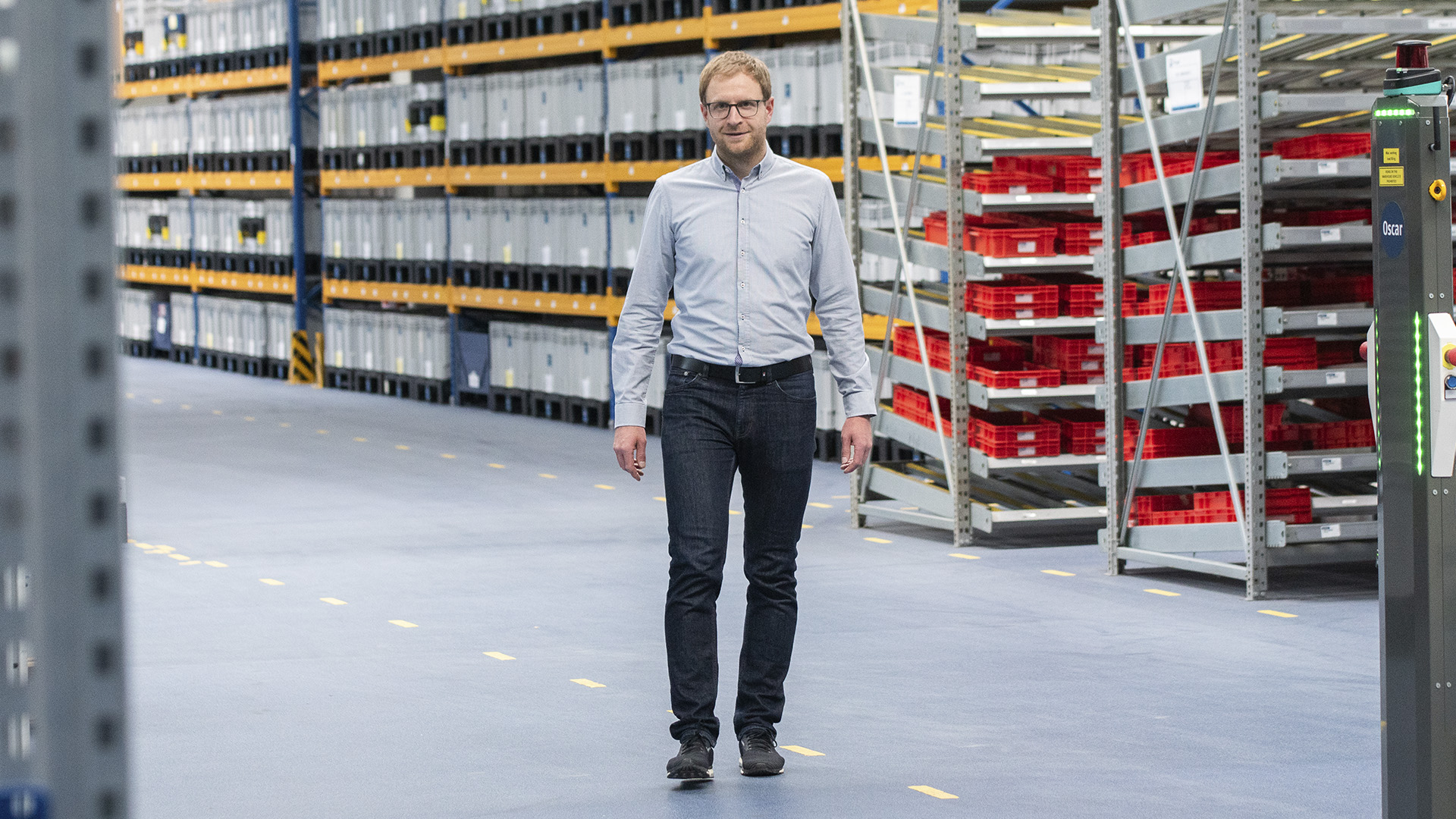
SCHUNK mise sur les robots mobiles autonomes pour optimiser ses processus
Pourquoi SCHUNK a-t-il choisi d’utiliser des robots mobiles autonomes sur le site de Brackenheim-Hausen ?
Weiland : Nous avions déjà expérimenté un système de chariots sans conducteur sans grand succès. Nous avons relancé le sujet car nous croyons en cette technologie. Avec KNAPP, nous avons trouvé non seulement le bon partenaire mais aussi le bon produit pour une expérience réussie. Nous avons choisi d’utiliser les AMR pour les raisons suivantes :
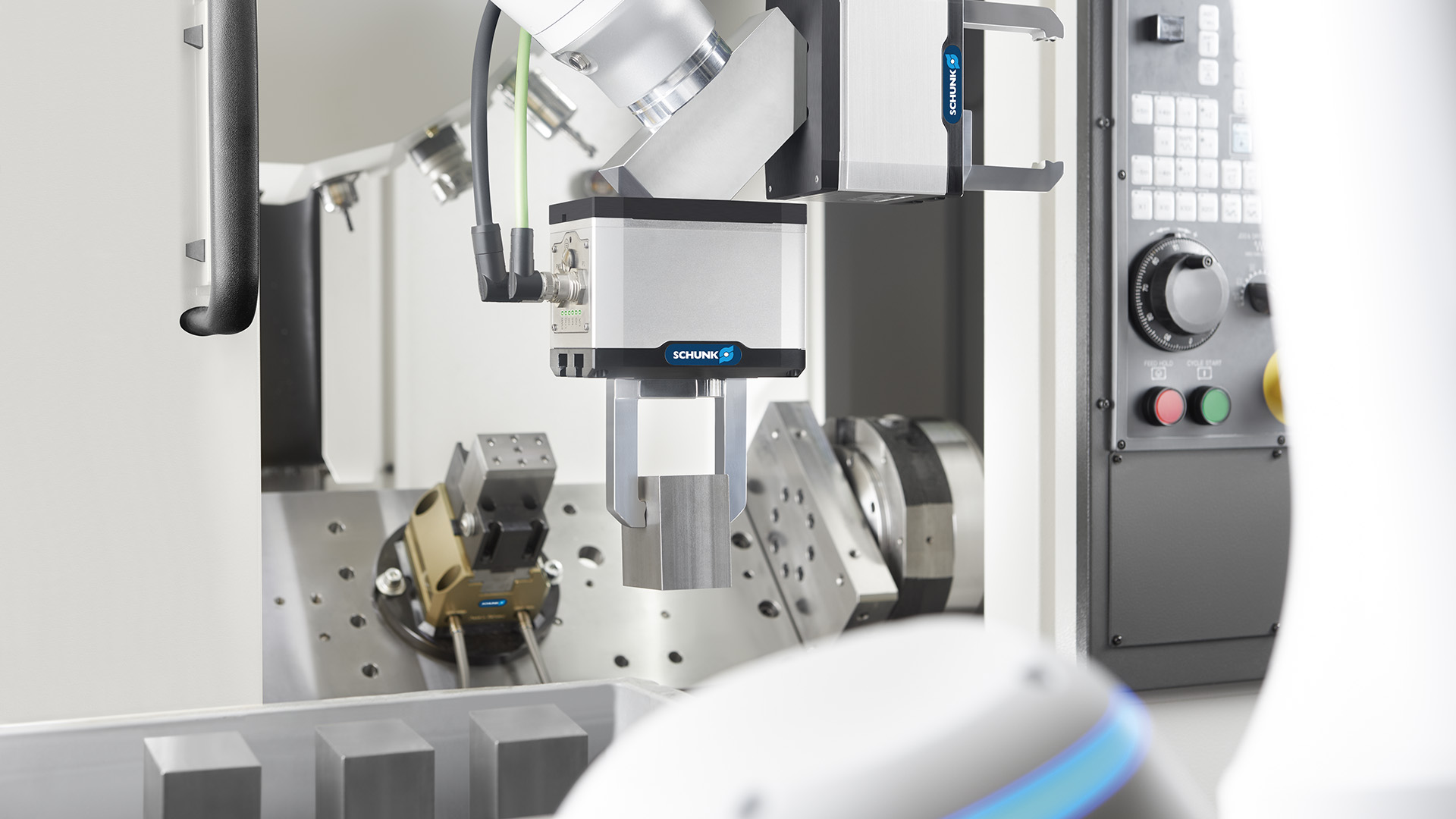
KNAPP comme partenaire avec une expérience AMR de longue date
Pourquoi SCHUNK a-t-il choisi l’Open Shuttle de KNAPP ?
Weiland : Chez SCHUNK, nous nous intéressons à ce système depuis 2016. À ce moment-là déjà, KNAPP était notre favori car son système correspondait le mieux à nos exigences en matière de transport. Il s’agissait tout particulièrement de transporter des conteneurs de taille 300 x 400 mm que KNAPP propose comme solution standard. Le temps que nous choisissions définitivement un système AMR, KNAPP avait développé en plus le réglage en hauteur, c’est-à-dire le levage intégré. Celui-ci figurait dès le départ sur notre liste de souhaits. Ainsi, l’Open Shuttle répondait encore mieux à nos attentes.
Weiland : La longue expérience a aussi joué un rôle décisif pour nous. Nous voulions une solution qui soit au point techniquement. Nous avions sur ce point une grande confiance en KNAPP.
Weiland : Il était important pour nous de pouvoir effectuer les modifications et les adaptations de manière autonome. C’était un point décisif pour nous car chez SCHUNK, nous sommes une entreprise très flexible et agile dans laquelle les processus peuvent tout à fait changer. C’est pourquoi il n’était pas question pour nous de recourir à une solution qui nous obligerait à faire appel à une aide extérieure. Nous voulions que notre personnel soit formé à la solution AMR et que nous ayons la possibilité et les droits d’effectuer nous-mêmes des petites modifications comme des changements de localisation des points de transfert. Et KNAPP offre cette possibilité à ses clients. Dans cette optique, nous avons accompagné la mise en place et le processus de mise en service, nous y avons été impliqués et avons ainsi déjà été formés.
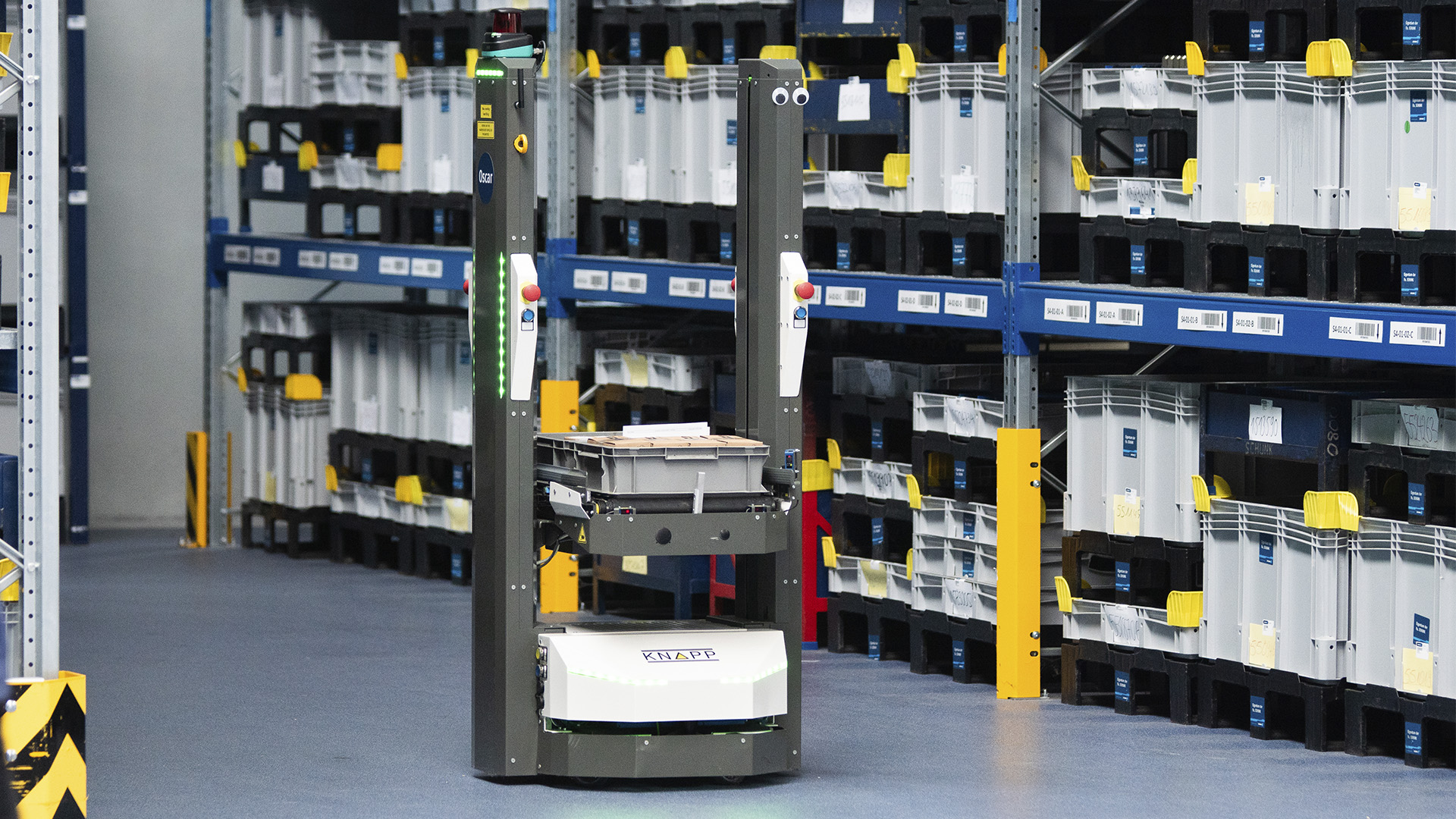
Robot mobile : processus de transport internes chez SCHUNK
Tous les faits en un coup d’œil :
Transport de 2 conteneurs de 25 kg
3 modules I/O pour la commande des 5 portes rapides et des 4 portes coupe-feu
Quels sont les processus de transport traités avec l’Open Shuttle ?
Weiland : Sur le site de Brackenheim-Hausen, nous sommes responsables de la production des préhenseurs et des composants d’automatisation. L’Open Shuttle se charge des processus suivants pour le transport interne à l’entrepôt :
- Transport des composants individuels de la logistique aux lignes de montage où ils sont montés pour former des unités de pivotement et de préhension et
- Retour des unités terminées à l’entrepôt
L’Open Shuttle transporte les composants individuels des préhenseurs, documents de commande compris, aux différentes équipes de montage. Les pièces sont assemblées au niveau des lignes de montage, sont soumises à un contrôle qualité puis emballées dans des cartons de produits terminés. L’Open Shuttle transporte aussi bien les composants individuels dont les lignes de montage ont besoin que les produits finis dont le conditionnement est terminé dans des conteneurs vers l’entrepôt d’expédition, où ils sont stockés temporairement, en attendant la prochaine étape de montage ou leur livraison aux clients.
Une solution d’automatisation sur mesure et intelligente
Quelles sont les particularités de la nouvelle solution d’automatisation ?
Weiland : Le transfert des conteneurs aux lignes de montage ainsi qu’à l’entrepôt pour petites pièces s’effectue au moyen de rayonnages dynamiques avec des convoyeurs à rouleaux équipés de capteurs d’emplacement de stockage. Dès que le conteneur rencontre une barrière lumineuse, une commande est déclenchée et l’Open Shuttle va chercher le conteneur pour le transporter. Nous avons opté pour cette solution parce qu’elle est techniquement simple, qu’elle repose sur la force du poids et nécessite peu d’électronique. Les capteurs surveillent les emplacements de stockage au niveau de la source et de la destination et signalent au système le besoin de transfert ou la place disponible pour une livraison. Ainsi, les commandes de transport sont générées automatiquement et les parcours à vide sont évités. Lors de la réalisation de nouvelles lignes de montage, nous monterons nous-mêmes les rayonnages dynamiques et KNAPP nous fournira les mécanismes de déclenchement, les triangles d’orientation, les capteurs et les modules I/O sous forme de kits.
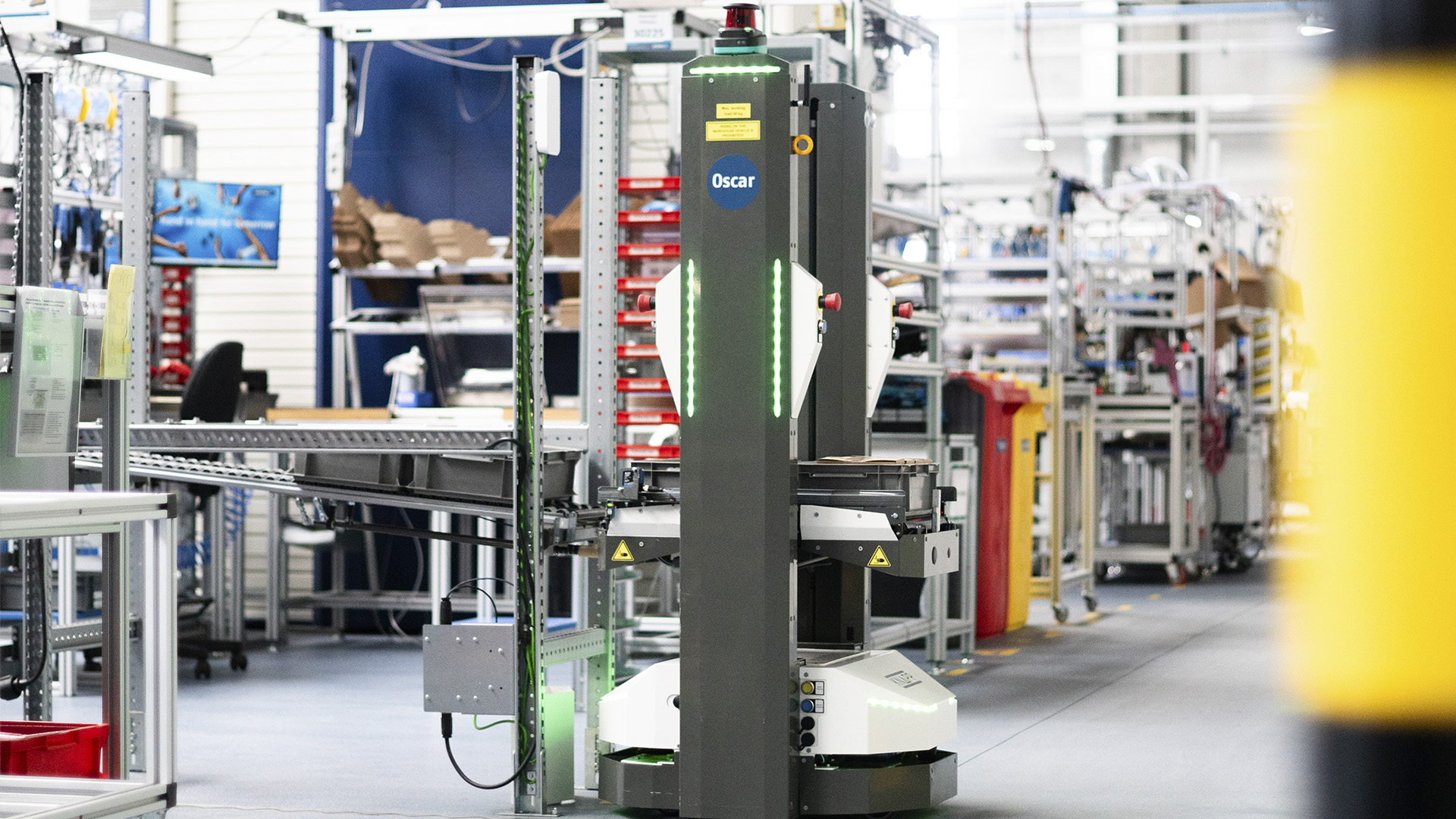
« Comme nous pouvons construire nous-mêmes les rayonnages dynamiques, nous pouvons intégrer d’autres lignes de montage plus vite et de manière plus flexible. Nous pouvons modifier et étendre les supports en fonction de nos besoins ».
Weiland : Sur le chemin entre les différentes lignes de montage et l’entrepôt pour petites pièces se trouvent cinq portes rapides qui sont reliées à l’Open Shuttle via un module. Lorsque le robot mobile autonome arrive à la porte, elle s’ouvre automatiquement. De même, des portes coupe-feu se trouvent également sur ces passages, qui se ferment en cas de besoin. Le véhicule ne doit pas s’arrêter dans cette zone pour des raisons de sécurité incendie. KNAPP nous a grandement aidé car ils avaient déjà de l’expérience dans ces sujets et solutions mis en œuvre. Grâce au module dit I/O, l’AMR demande s’il y a un cas d’incendie ou non et empêche ainsi également l’entrée dans le couloir devant la porte coupe-feu. Cela fonctionne de manière fiable et sans problème.
Oscar : un robot mobile autonome comme nouveau collègue
Êtes-vous satisfait de la solution qui consiste à effectuer le transport interne avec l’Open Shuttle ?
Weiland : Nous sommes très satisfaits d’Oscar, c’est ainsi que nous appelons l’Open Shuttle. Un mot sur l’origine du nom : les deux premières lettres, OS, sont les deux initiales d’Open Shuttle et CAR vient d’Open Shuttle Car. Cela donne OSCAR. Quand nous parlons chez nous de l’Open Shuttle, c’est toujours Oscar. Nous nous entendons très bien avec Oscar, il est technologiquement fiable et il fonctionne. Naturellement, au départ, le personnel était un peu sceptique. Je ne m’y attendais pas car nous sommes nous-mêmes actifs dans l’automatisation et que les mesures pour augmenter l’efficacité n’avaient jamais été un problème à ce jour. Mais cela a changé très vite et le personnel a vu les avantages de l’Open Shuttle. Il a été d’autant mieux accepté qu’il a l’air sympathique avec ses petites lumières clignotantes, quand il tourne par exemple. Oscar a l’air sympathique et n’est pas une construction effrayante.
Coopération d’égal à égal
Que pouvez-vous nous dire de la coopération avec KNAPP ?
Weiland : La coopération est professionnelle et repose sur la confiance. En cas de problèmes, on peut toujours contacter KNAPP et on trouve ensemble une solution. Nous nous sentons très bien accompagnés, aussi du point de vue des services.
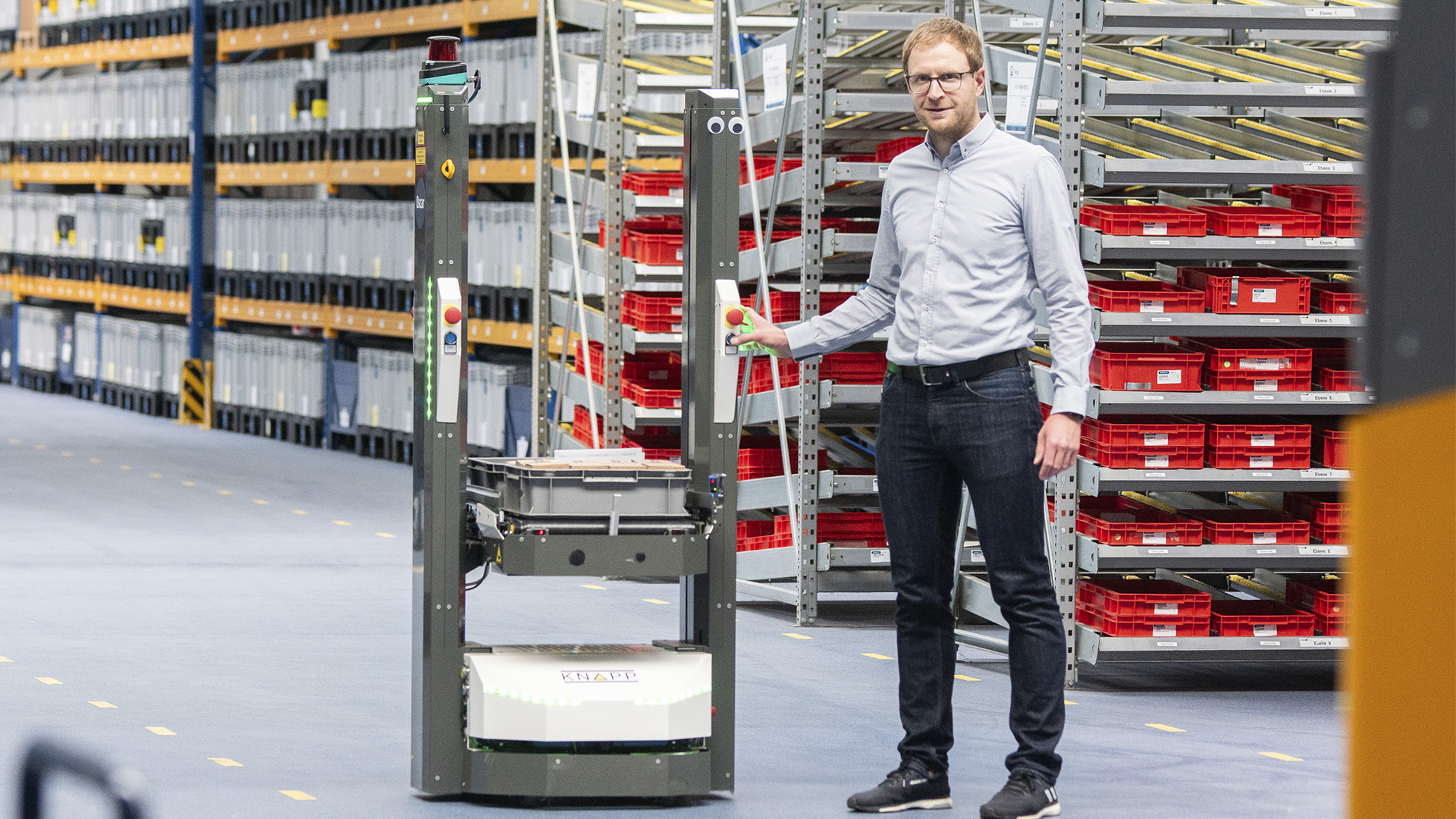
« Notre robot mobile, que nous appelons en interne « Oscar », se charge de ses tâches de manière fiable. Avec KNAPP, la coopération est professionnelle, partenariale et d’égal à égal. Nous nous sentons parfaitement pris en charge ».
D’autres étapes d’automatisation sont-elles prévues à l’avenir ?
Weiland : Nous avons commencé sur le site de Brackenheim-Hausen par un projet Open Shuttle et voulons à long terme profiter des avantages de l’utilisation des AMR sur d’autres sites. Oscar était notre premier projet car nous ne pouvions pas évaluer au départ le taux d’occupation qu’il aurait. Nous n’étions pas sûr de sa rapidité ni des conséquences qu’il aurait sur la circulation dans l’usine. Nous sommes maintenant très satisfaits de sa performance. À terme, Oscar ne va pas rester seul et va recevoir un renfort féminin. Cela est prévu seulement pour la fin de l’année, voire le début de l’année prochaine. Nous n’avons pas encore de nom, mais je suis ouvert aux suggestions.
Recommandations de lecture

Les robots mobiles autonomes (AMR) permettent des processus de transport flexibles et efficaces. Que ce soit dans l’industrie manufacturière, dans le commerce alimentaire ou dans la logistique de distribution – les domaines d’application sont variés. Nous vous en disons plus sur cette technologie d’avenir.

