Automatisation d’entrepôt pour l’industrie
L’automatisation d’entrepôt est la clé pour plus de compétitivité dans l’industrie. À l’avenir, la production sera intelligente, flexible et connectée. Nous optimisons l’approvisionnement de votre production et vos processus de transport internes avec des solutions efficaces.
Augmentation de la performance grâce à une logistique de production intelligente
Une logistique de production intelligente et parfaitement adaptée joue un rôle central dans la compétitivité des entreprises de production. Les défis que le secteur doit relever sont énormes. Les situations changeantes en matière d’environnement et de marché, le manque de personnel qualifié, le manque de place et la complexité sans cesse grandissante demandent de nouvelles solutions dans l’industrie. L’automatisation d’entrepôt est la clé pour l’augmentation de la performance dans votre entreprise.
Vous souhaitez avoir des systèmes dynamiques avec un réseau plus solide ? Qui plus est de la sécurité d’investissement et une flexibilité maximale pour répondre aux exigences qui évoluent ? Nos solutions d’automatisation d’entrepôt sont synonymes de plus de rentabilité, d’efficacité, d’ergonomie et de qualité dans l’entreprise. Avec de nouvelles approches et un mixte de technologies innovantes et éprouvées, nous offrons de nouvelles possibilités pour l’industrie de production. Car telle est notre mission :
nous comprenons votre activité et vous apportons un plus en matière de flexibilité de vos processus grâce à nos solutions logistiques innovantes.
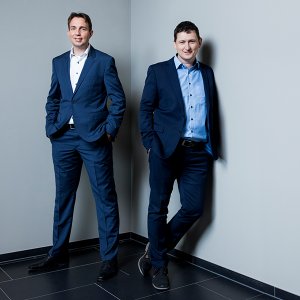
Avez-vous des questions ?
Nous sommes là pour vous !
Stefan Lechner & Christian Brauneis
Vice Presidents Business Unit Industry
E-mail: kin.sales@knapp.com
« Nous savons la valeur de la sécurité des processus au cœur de chaque entreprise – de la production – et nous considérons que notre tâche est de développer des solutions optimales avec notre savoir-faire. Les technologies innovantes et l’utilisation de logiciels intelligents permettent de connecter les processus de manière optimale et de les concevoir pour qu’ils soient évolutifs. Avec nos solutions complètes, nous misons sur une Smart Production.«
Christian Brauneis
Vice President Business Unit Industry
Vous vous intéressez à l’automatisation d’entrepôt au sein de votre entreprise ?
Découvrez nos solutions et nos références !
Solutions pour l’automatisation d’entrepôt dans l’industrie
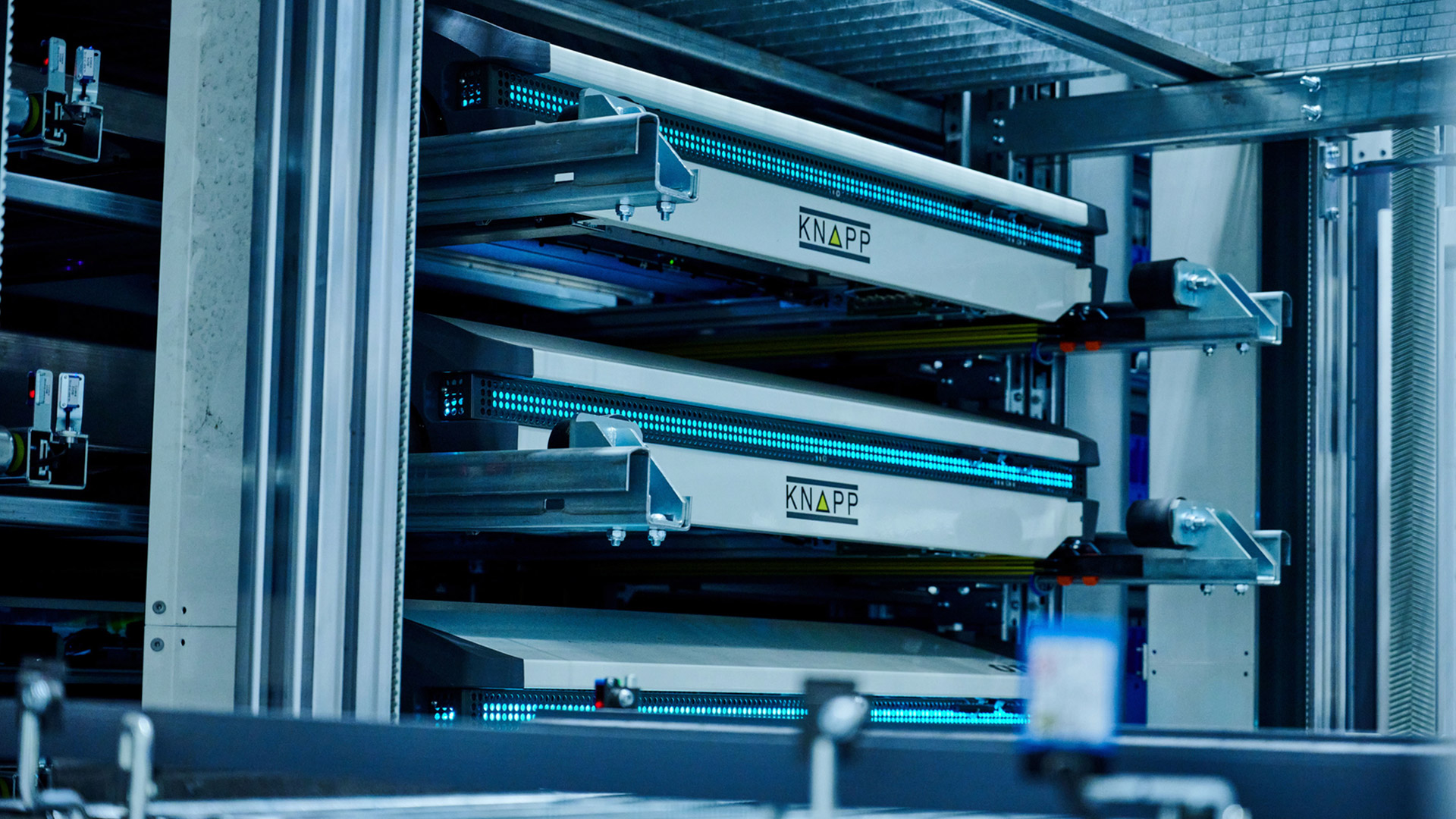
Systèmes d’automatisation d’entrepôt pour des processus de production efficaces
Entrepôt automatisé pour petites pièces, transtockeur RBG ou tours de stockage – nous répondons à toutes les exigences avec une solution logistique optimale. Nos systèmes de stockage prennent en charge des processus tels que le prélèvement, le stockage temporaire, le séquencement des marchandises et des commandes ainsi que l’approvisionnement des postes de travail.
Découvrez nos solutions intelligentes :
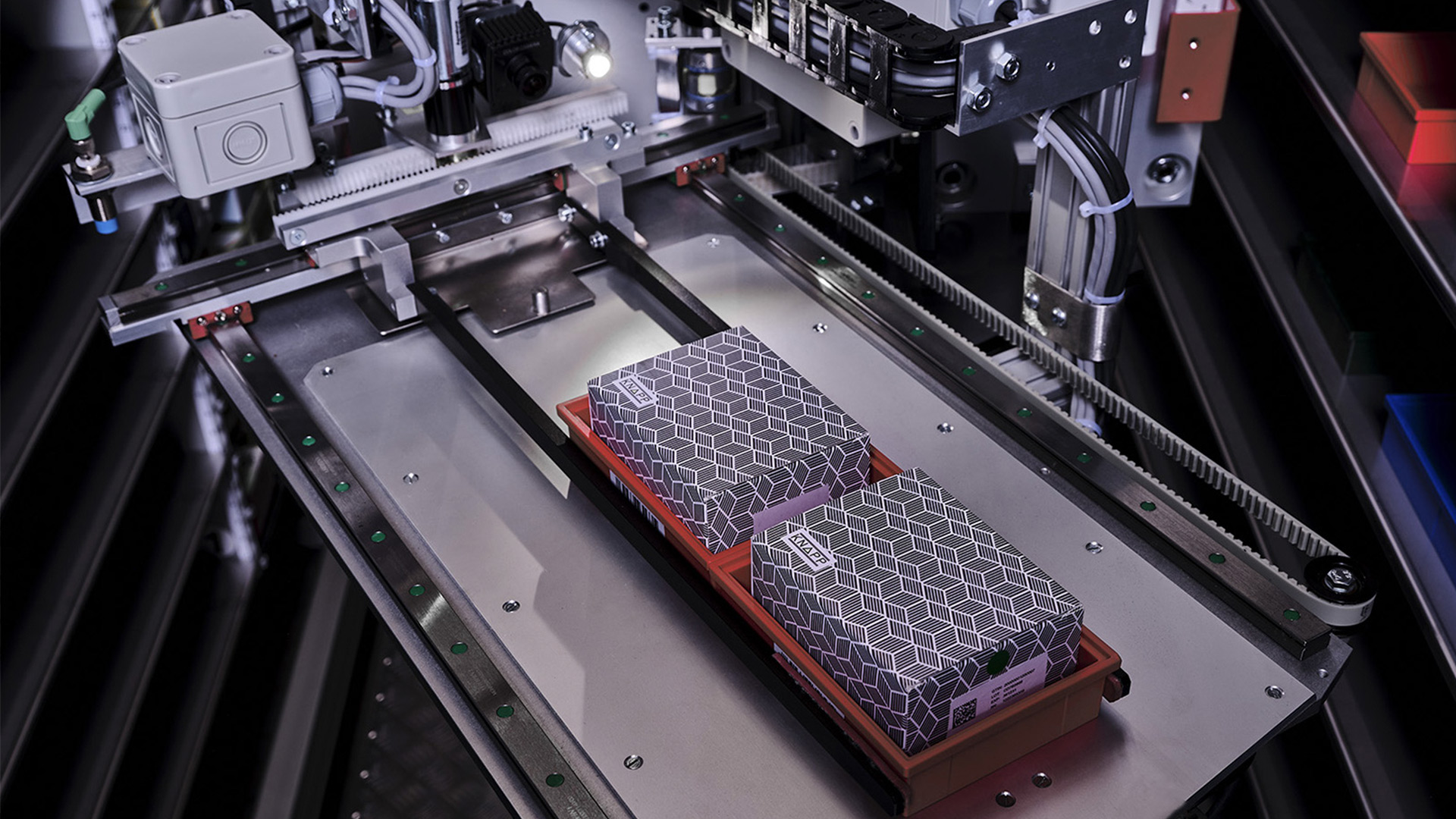
Automates de stockage et de prélèvement
pour une meilleure performance
InduStore, l’automate de stockage et de prélèvement, est LA bonne solution pour les applications industrielles. Le système convient pour le stockage d’articles à l’unité, comme entrepôt pour l’approvisionnement de la production et comme stock de pièces de rechange. Découvrez le système :
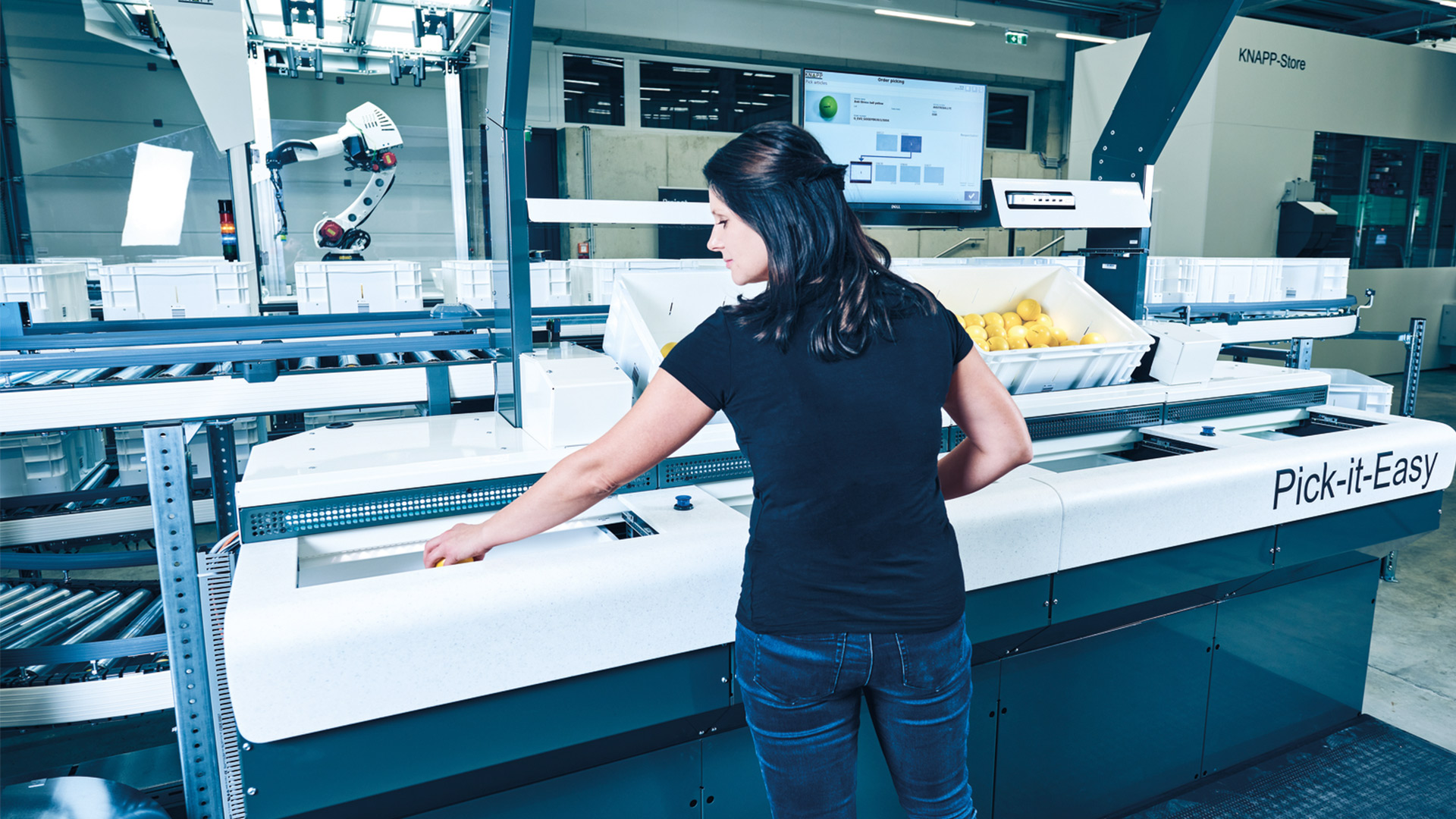
Postes de travail ergonomiques et intelligents
Nos postes de travail allient ergonomie, efficacité et qualité. Le principe du « produit-vers-l’homme » garantit un traitement optimal des commandes et la satisfaction du personnel. Les postes de travail intelligents avec un système de caméras intelligent permettent un contrôle qualité à 100 pour cent.
Découvrez nos offres :
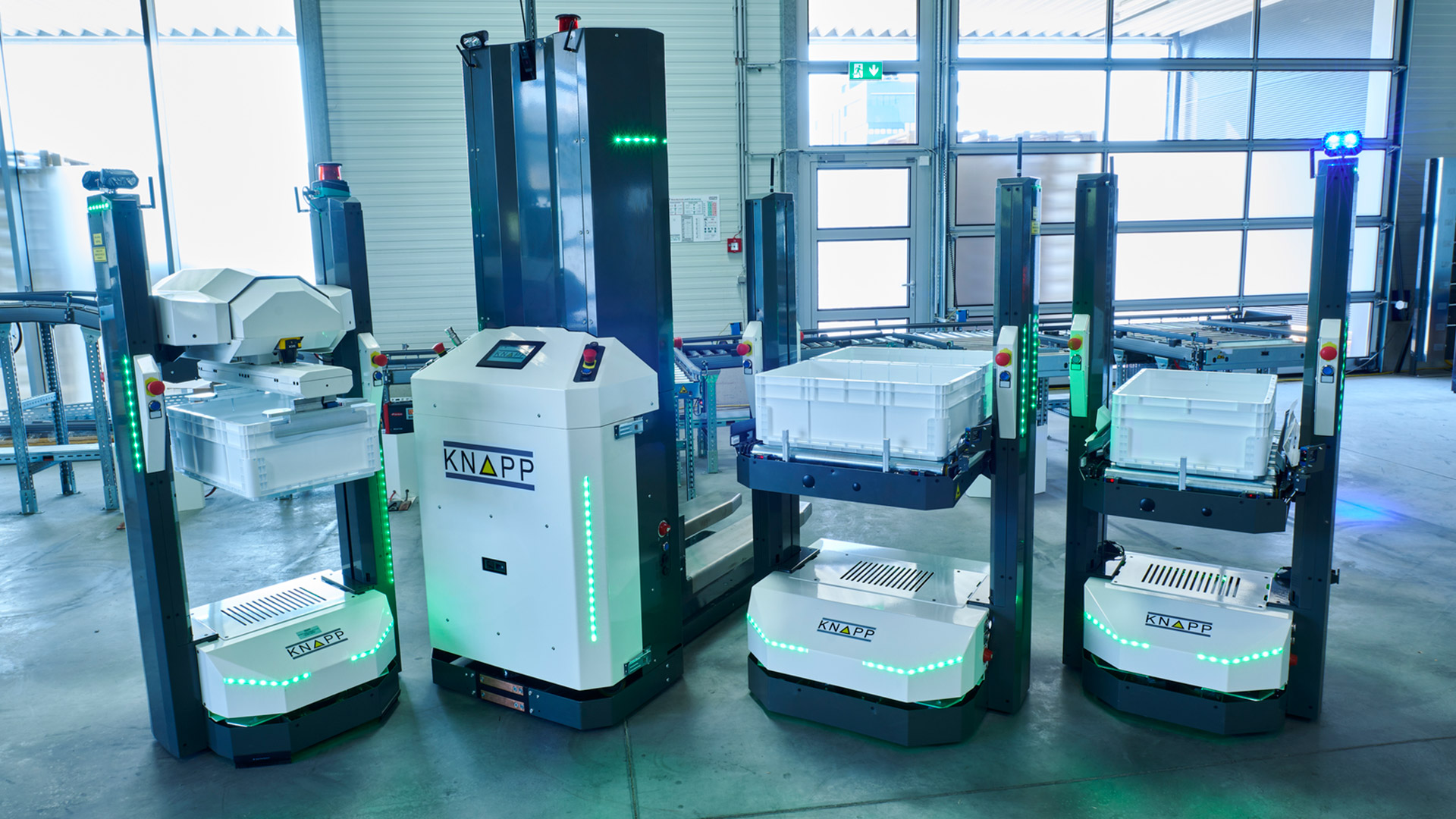
Des véhicules à guidage automatique pour plus de flexibilité
Nos véhicules à guidage automatique intelligents permettent une conception flexible des processus logistiques. Ils automatisent les transports internes et relient efficacement les différents domaines de production.
Découvrez nos robots mobiles autonomes (RMA) >
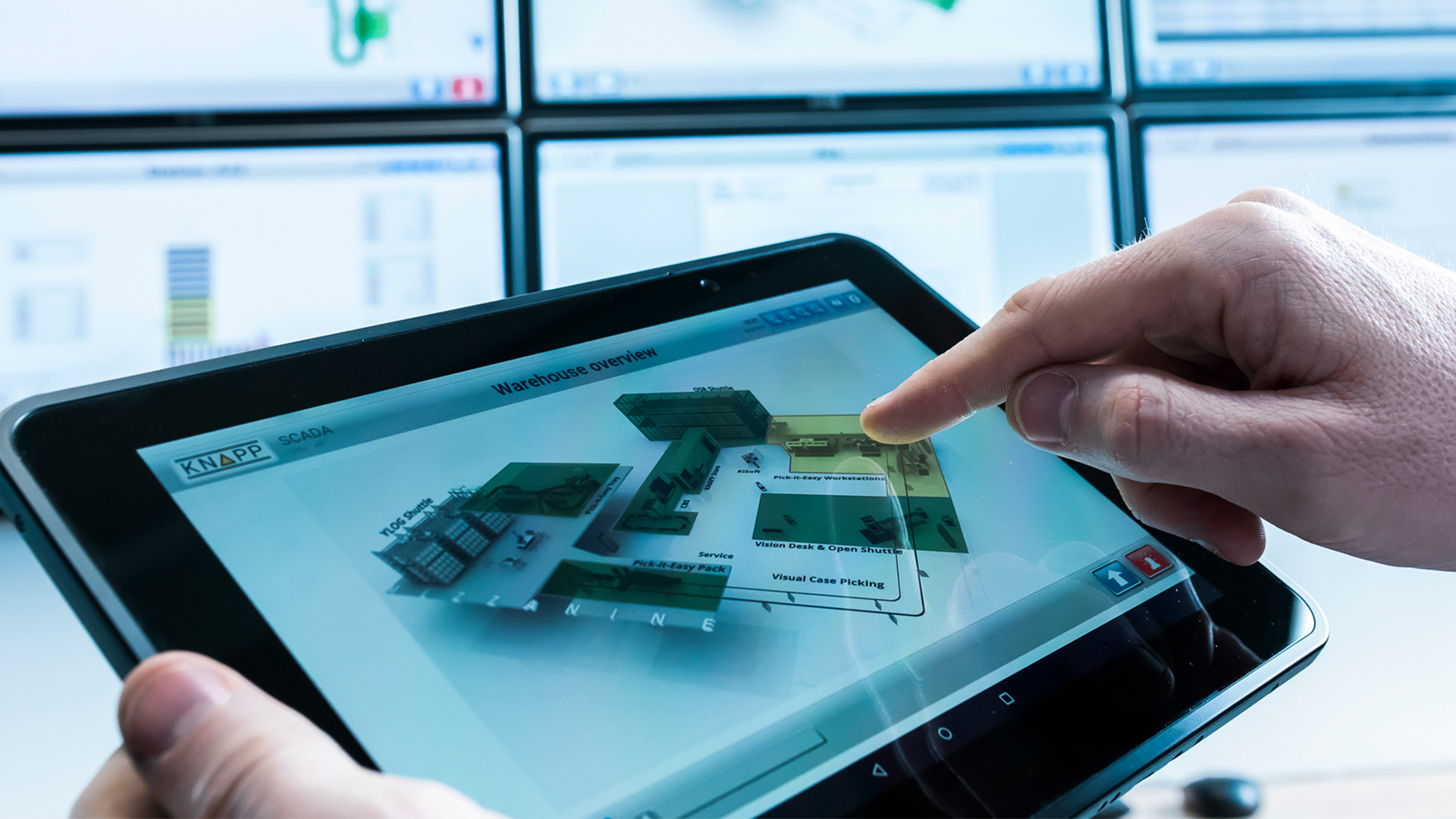
Un logiciel pour automatiser l’entrepôt
Le logiciel est au cœur de toute automatisation d’entrepôt. En tant que Value Chain Tech Partner, nous proposons des solutions logicielles complètes tout en un, un logiciel de contrôle de la flotte, un logiciel de planification des ressources, etc. En fonction des besoins, nous couvrons les processus avec nos lignes de produits KiSoft et SAP® EWM by KNAPP.
Découvrez nos solutions logicielles complètes :
Avantages pour la logistique de production
L’automatisation de la logistique de production offre de nombreux avantages aux entreprises de production :
Référence :
nos solutions pour l’automatisation d’entrepôt dans l’industrie
Des entreprises dans le monde entier misent sur une collaboration avec KNAPP. Nous vous aidons à optimiser les processus de production, les surfaces de stockage et les transports internes. Nos solutions parlent d’elles-mêmes :
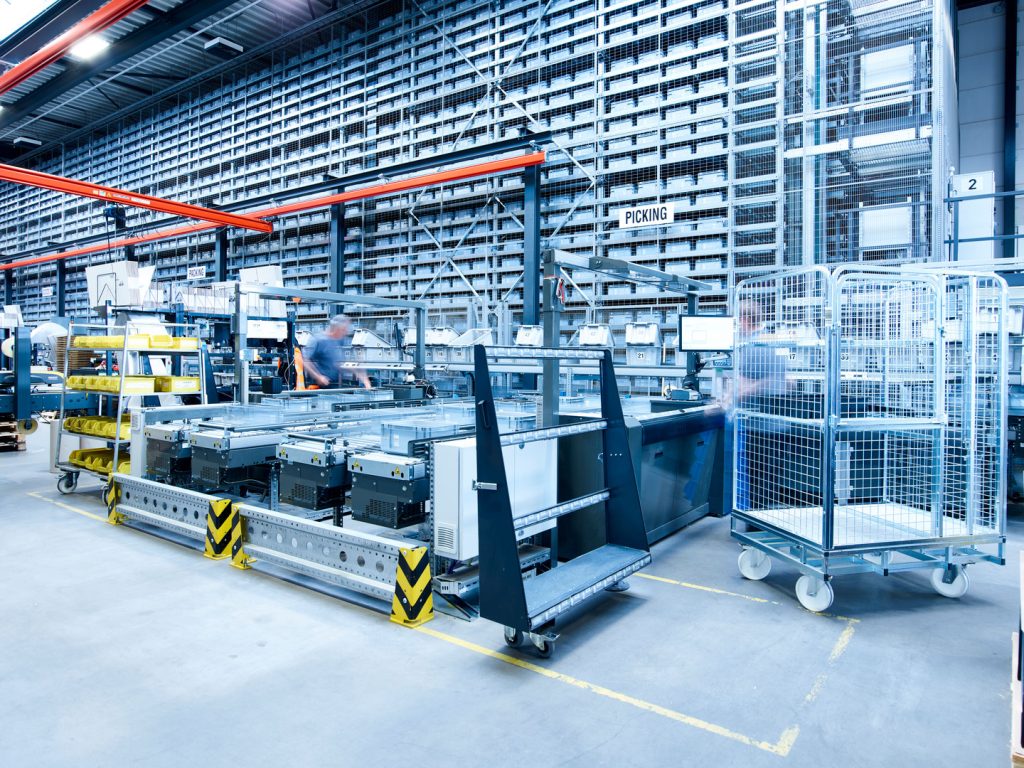
Terberg Benschop B.V. : la solution installée pose les bases de la croissance future de l’entreprise
Pour pouvoir traiter le nombre croissant de commandes, plusieurs processus ont été centralisés dans un seul système de stockage automatique chez Terberg. Selon la commande, le prélèvement s’effectue pour la production, la ligne de montage ou la livraison des pièces de rechange. L’approvisionnement est effectué en fonction des besoins et juste à temps.
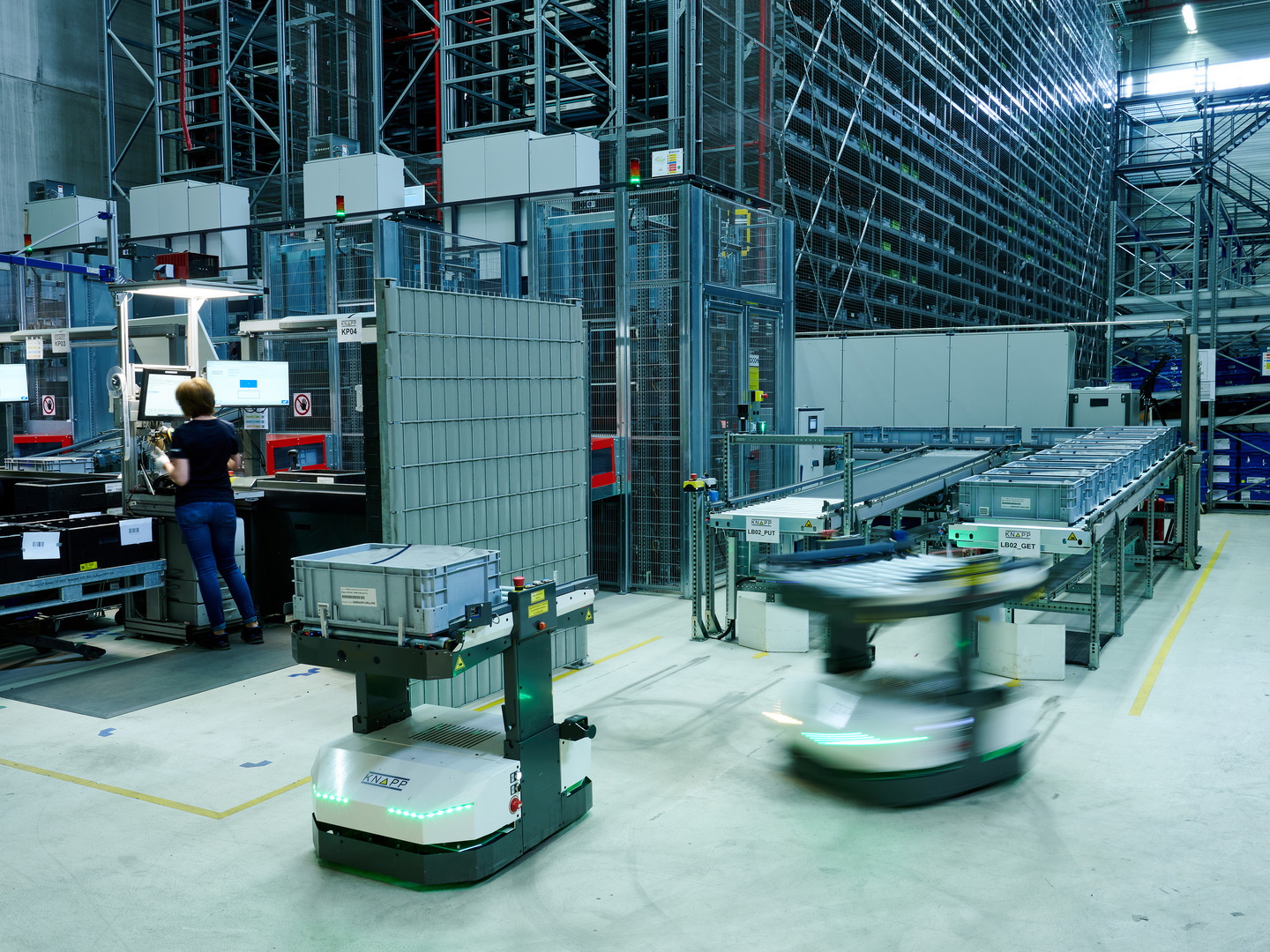
Magna Spiegelsysteme : approvisionnement optimisé de la production et de l’assemblage
Avec la solution automatisée de KNAPP, Magna réussit à garantir la disponibilité plus rapide des pièces, à réduire le trafic interne et à utiliser l’entrepôt sans personnes. Celle-ci est basée sur une installation multifonctionnelle composée de navettes et associée à des robots mobiles autonomes.
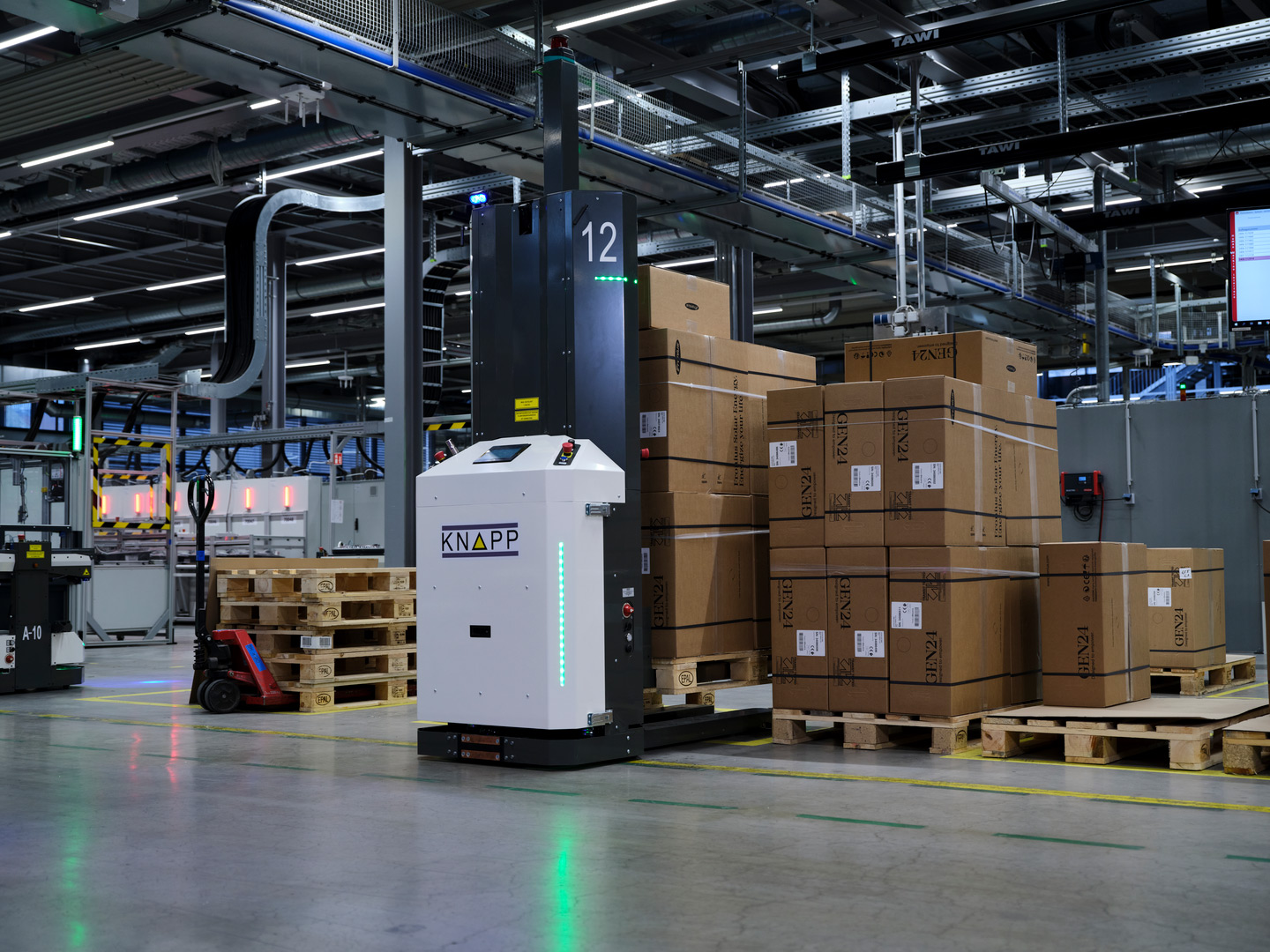
Fronius : transport automatisé de palettes avec les RMA pour un approvisionnement flexible de la production
Les Open Shuttle Fork innovants automatisent l’approvisionnement de la production et le transport interne chez Fronius. Grâce à la nouvelle solution, l’entreprise peut effectuer des modifications de manière flexible et autonome et gérer les commandes automatisées dans un système.
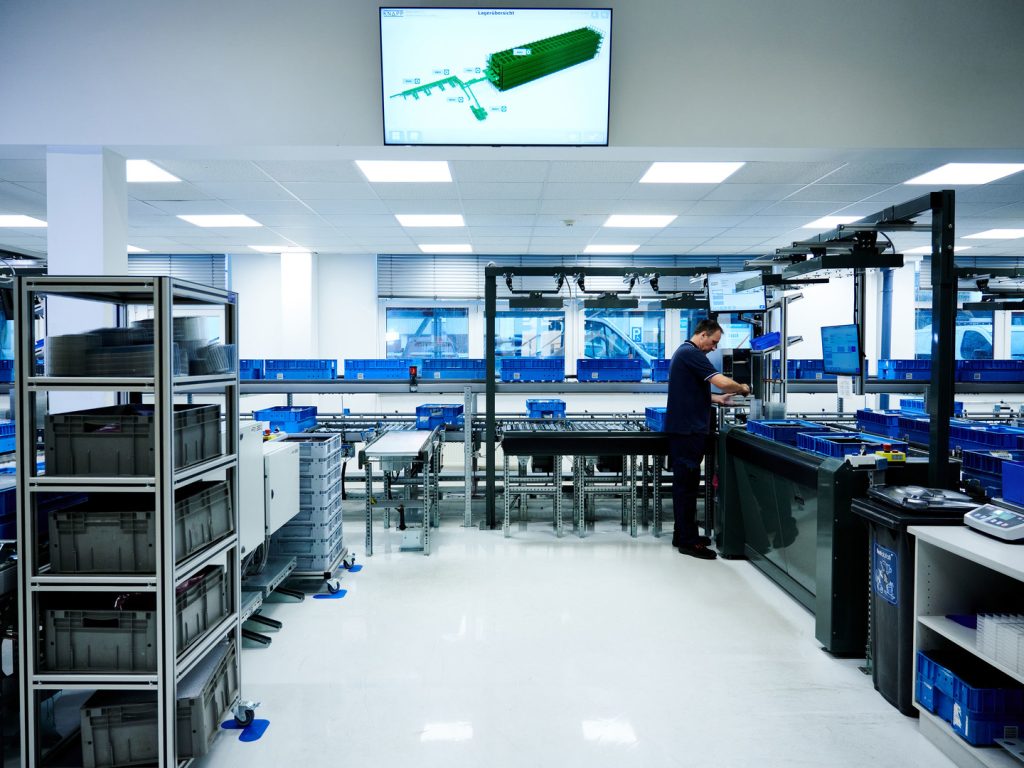
Knorr-Bremse : optimisation des processus grâce à un système sur mesure
Knorr-Bremse a multiplié par trois la performance de son entrepôt pour petites pièces grâce à une installation multifonctionnelle composée de navettes et associée à des postes de préparation et un système de convoyage monté au plafond. Découvrez la solution qui couvre efficacement les différents processus.
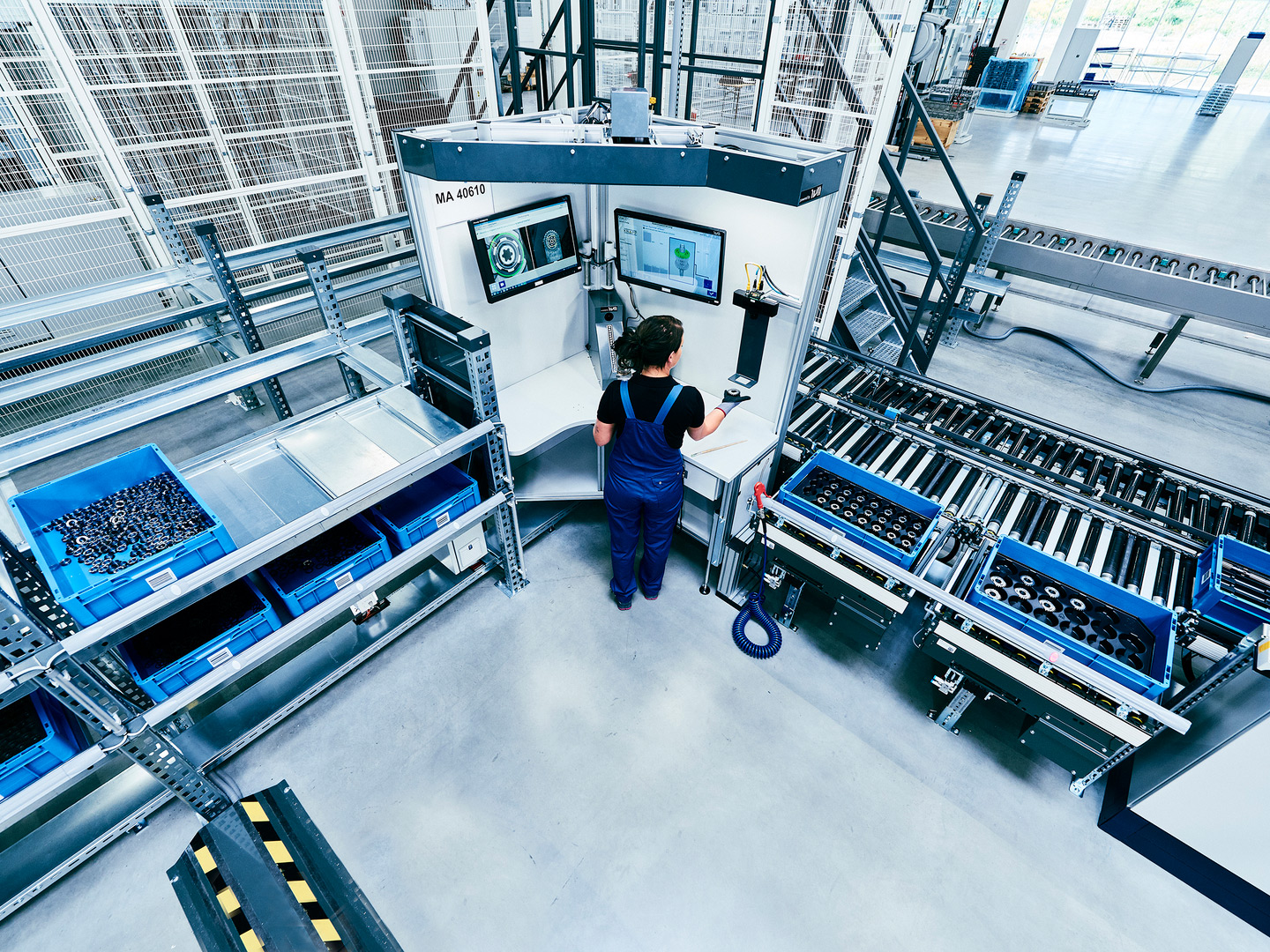
Pankl Racing AG : stratégie zéro défaut dans l’ensemble du processus de fabrication
Un entrepôt automatisé pour petites pièces approvisionne les postes de travail de montage selon le principe du produit-vers-l’homme. Une technologie moderne de reconnaissance et de traitement d’images contrôle chaque étape de travail et garantit un assemblage sans erreur et une traçabilité sans faille. Un parfait exemple de production intelligente.
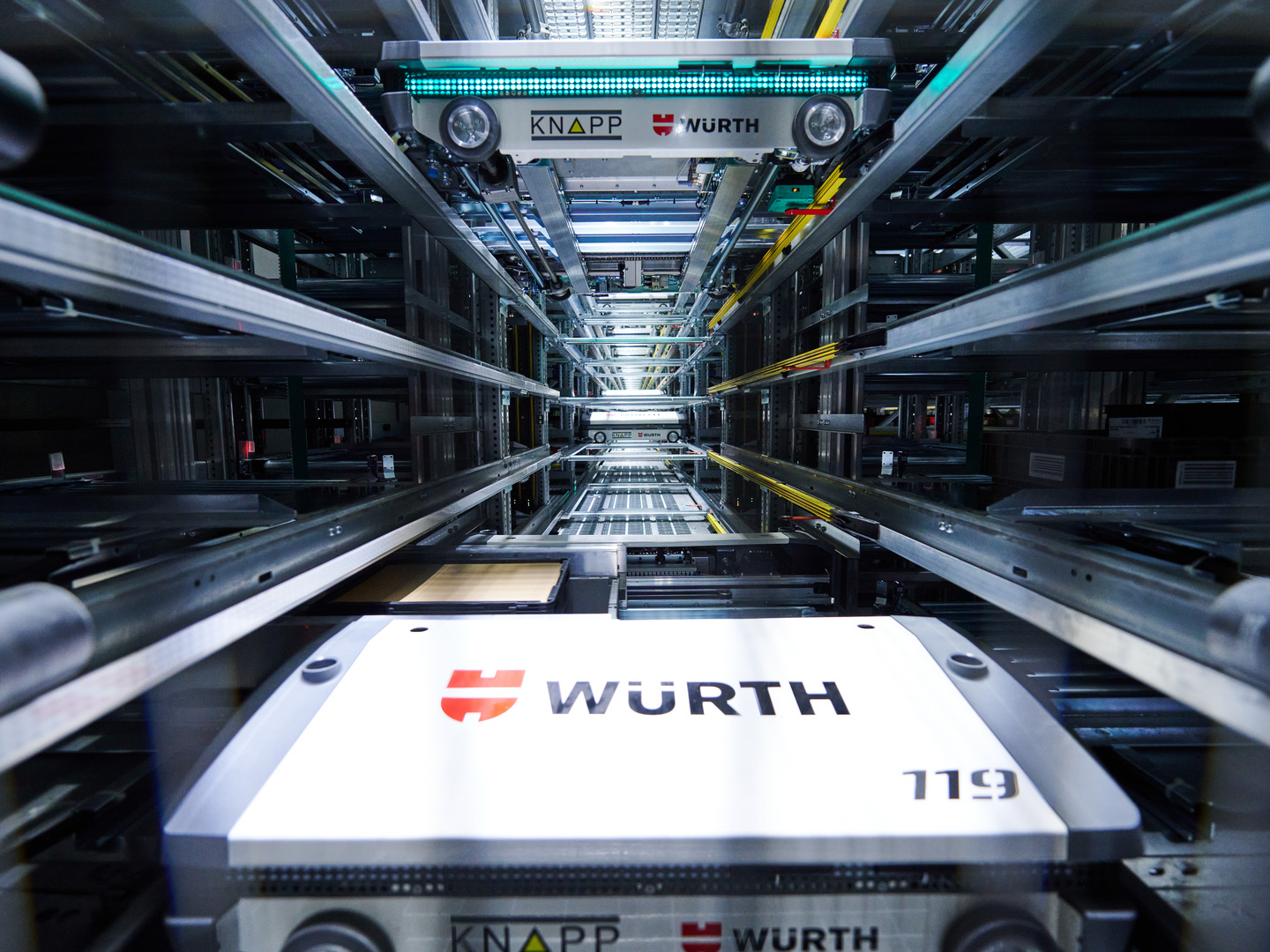
Würth : automatisation intelligente dans la logistique
Les technologies robotiques les plus modernes sont utilisées chez Würth. Du stockage à l’expédition, en passant par le prélèvement et le transport interne, les processus logistiques sont exécutés entièrement automatiquement. En tant que partenaire de longue date, nous apportons notre assistance dans le développement continu.
Référence :
nos solutions pour l’automatisation d’entrepôt dans l’industrie
Des entreprises dans le monde entier misent sur une collaboration avec KNAPP. Nous vous aidons à optimiser les processus de production, les surfaces de stockage et les transports internes. Nos solutions parlent d’elles-mêmes :
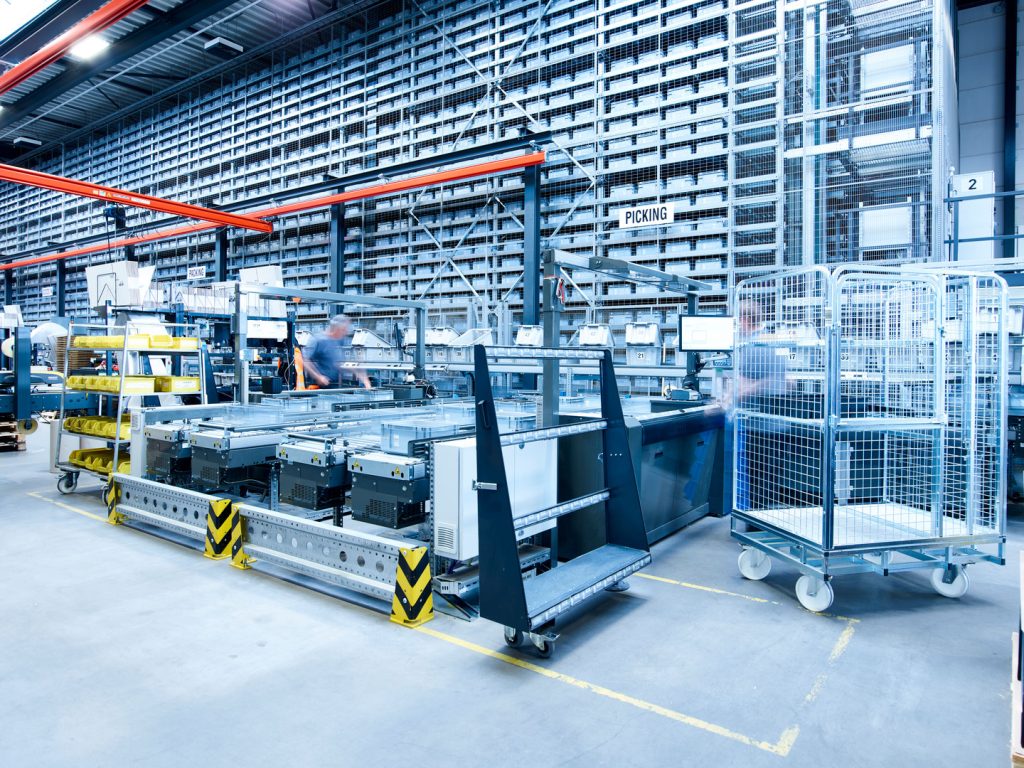
Terberg Benschop B.V. : la solution installée pose les bases de la croissance future de l’entreprise
Pour pouvoir traiter le nombre croissant de commandes, plusieurs processus ont été centralisés dans un seul système de stockage automatique chez Terberg. Selon la commande, le prélèvement s’effectue pour la production, la ligne de montage ou la livraison des pièces de rechange. L’approvisionnement est effectué en fonction des besoins et juste à temps.
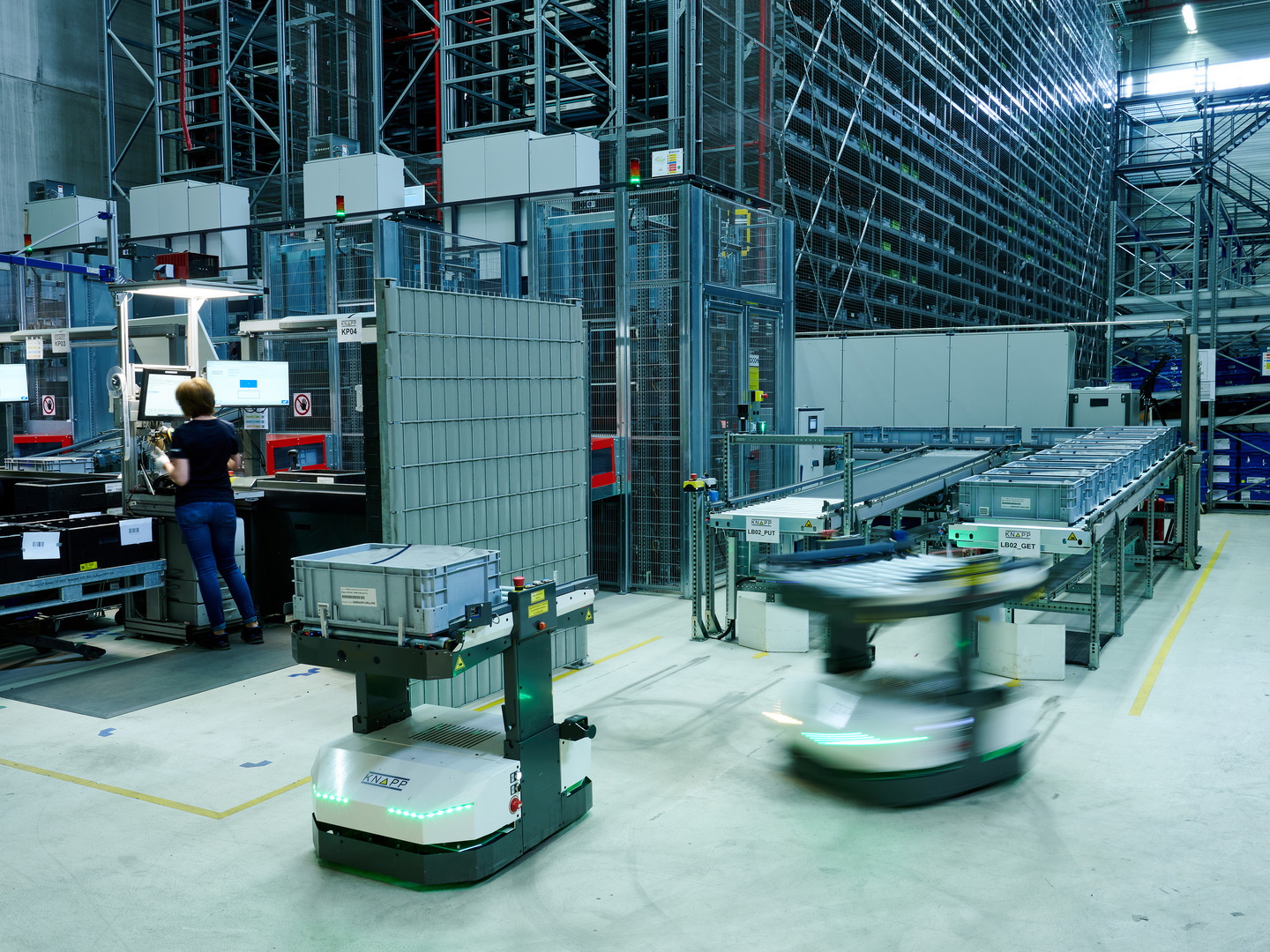
Magna Spiegelsysteme : approvisionnement optimisé de la production et de l’assemblage
Avec la solution automatisée de KNAPP, Magna réussit à garantir la disponibilité plus rapide des pièces, à réduire le trafic interne et à utiliser l’entrepôt sans personnes. Celle-ci est basée sur une installation multifonctionnelle composée de navettes et associée à des robots mobiles autonomes.
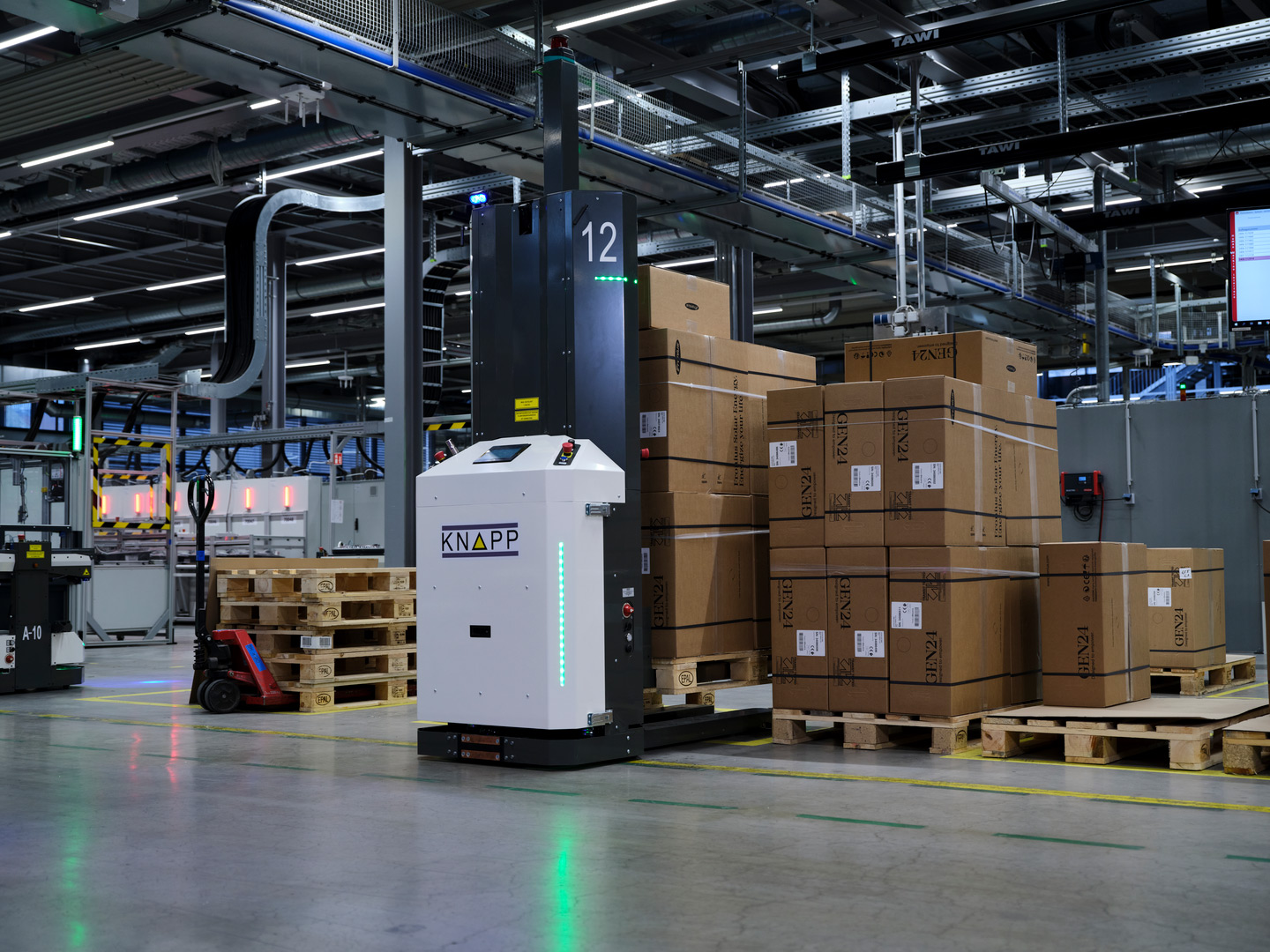
Fronius : transport automatisé de palettes avec les RMA pour un approvisionnement flexible de la production
Les Open Shuttle Fork innovants automatisent l’approvisionnement de la production et le transport interne chez Fronius. Grâce à la nouvelle solution, l’entreprise peut effectuer des modifications de manière flexible et autonome et gérer les commandes automatisées dans un système.
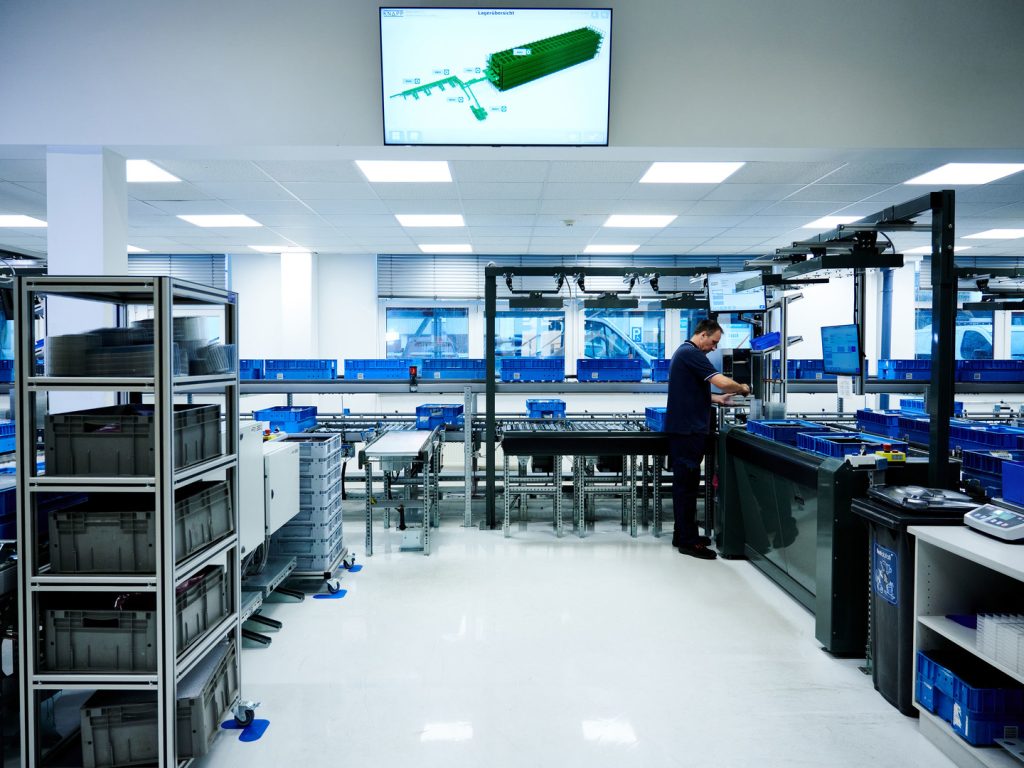
Knorr-Bremse : optimisation des processus grâce à un système sur mesure
Knorr-Bremse a multiplié par trois la performance de son entrepôt pour petites pièces grâce à une installation multifonctionnelle composée de navettes et associée à des postes de préparation et un système de convoyage monté au plafond. Découvrez la solution qui couvre efficacement les différents processus.
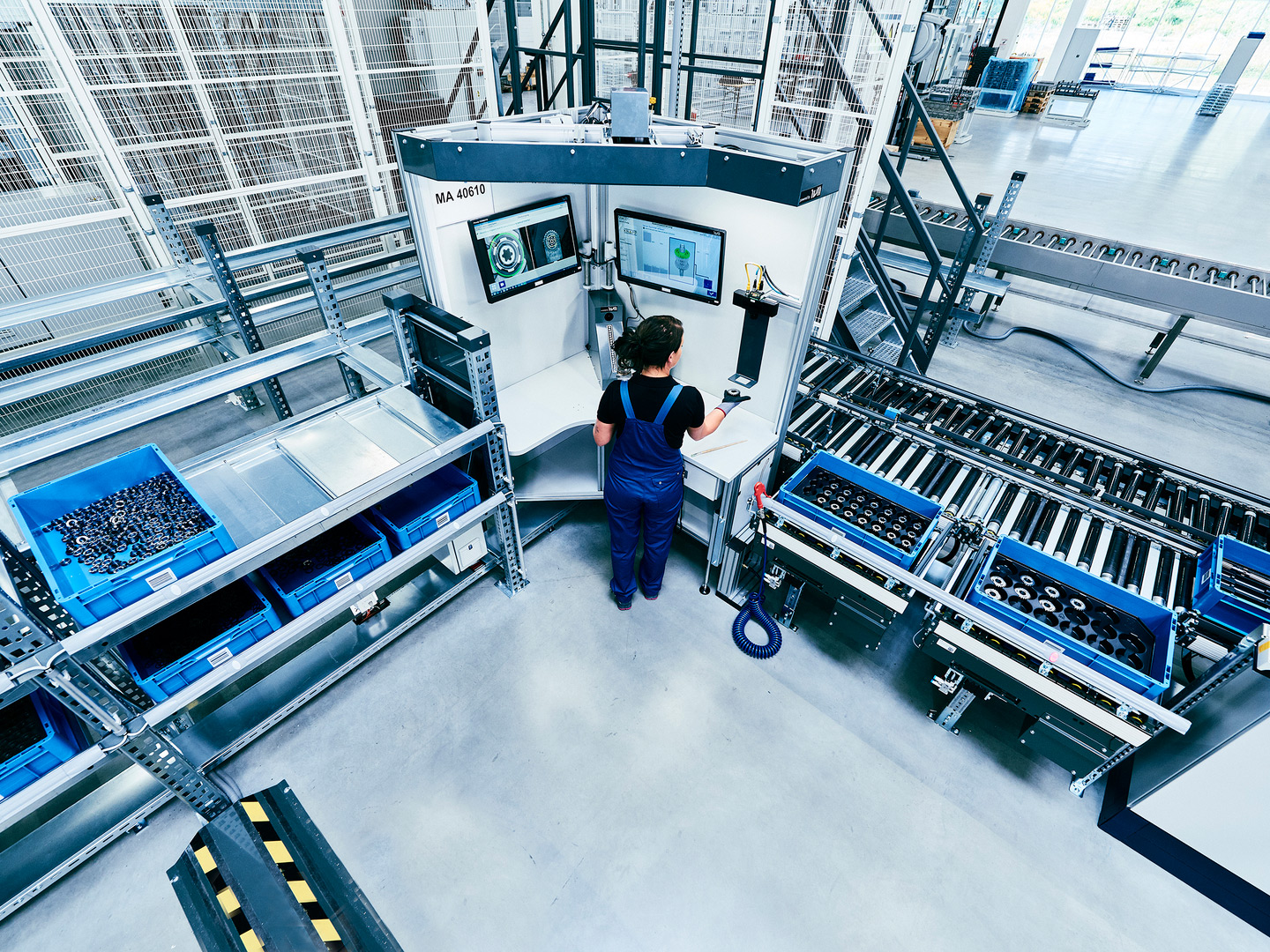
Pankl Racing AG : stratégie zéro défaut dans l’ensemble du processus de fabrication
Un entrepôt automatisé pour petites pièces approvisionne les postes de travail de montage selon le principe du produit-vers-l’homme. Une technologie moderne de reconnaissance et de traitement d’images contrôle chaque étape de travail et garantit un assemblage sans erreur et une traçabilité sans faille. Un parfait exemple de production intelligente.
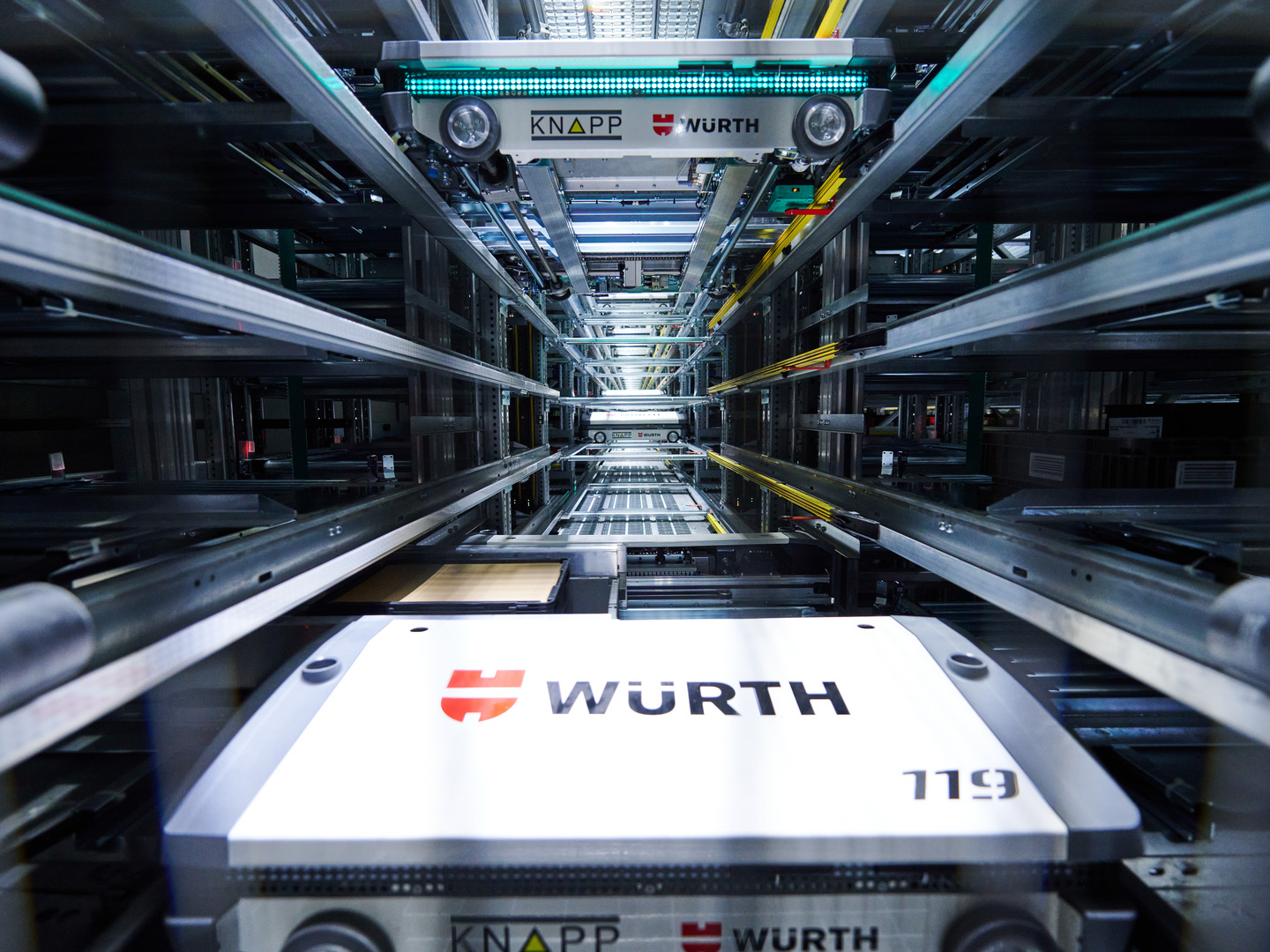
Würth : automatisation intelligente dans la logistique
Les technologies robotiques les plus modernes sont utilisées chez Würth. Du stockage à l’expédition, en passant par le prélèvement et le transport interne, les processus logistiques sont exécutés entièrement automatiquement. En tant que partenaire de longue date, nous apportons notre assistance dans le développement continu.
Réseau de services global et partenaire fiable
Notre Service Client international s’occupe de votre système logistique dans le monde entier 24h/24 et 365 jours par an.
Découvrez nos services – de l’assistance non-stop à l’optimisation de l’installation !
Automatisation d’entrepôt pour l’industrie –
ces entreprises nous font confiance :
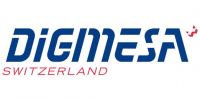
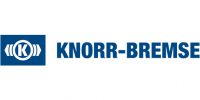
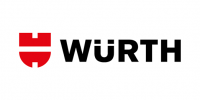
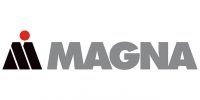
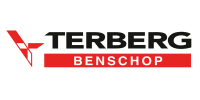
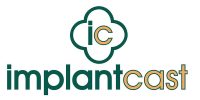
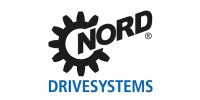
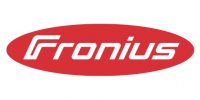
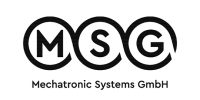
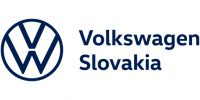
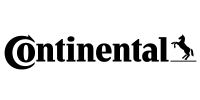
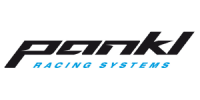
Vous vous intéressez à nos solutions pour l’automatisation d’entrepôt dans l’industrie ?
Nous vous informons volontiers !
Articles de blog passionnants sur
l’automatisation de l’entrepôt et de la chaîne de valeur

Optimiser les processus et accroître la performance grâce à l’automatisation de l’intralogistique. Quel degré d’automatisation convient à votre entreprise ? Dans cet article, nous présentons les différentes formes que peut prendre un aménagement : de l’entrepôt manuel innovant à l’automatisation complète.

Une efficacité plus élevée, une vitesse optimisée et des durées de parcours plus courtes – tels sont les avantages que l’utilisation du robot mobile autonome procure à SCHUNK. Découvrez l’utilisation de la solution flexible et la coopération avec KNAPP.

Le nouveau règlement européen 2025 (PPWR) apporte quelques nouveautés. Voici un aperçu de ses directives et des mesures que vous pouvez prendre !