Lagerautomatisierung für die Industrie
Lagerautomatisierung ist der Schlüssel zu mehr Wettbewerbsfähigkeit in der Industrie. Denn die Produktion der Zukunft ist intelligent, flexibel und vernetzt. Mit effizienten Lösungen optimieren wir Ihre Produktionsversorgung und internen Transportprozesse.
Performancesteigerung durch intelligente Produktionslogistik
Eine optimal abgestimmte und intelligente Produktionslogistik spielt eine zentrale Rolle für die Wettbewerbsfähigkeit von produzierenden Unternehmen. Denn die Herausforderungen der Branche sind enorm. Wechselnde Umwelt- und Marktsituationen, Fachkräftemangel, Platzmangel und immer steigende Komplexität fordern neue Lösungsansätze in der Industrie. Lagerautomatisierung ist der Schlüssel für die Performancesteigerung in Ihrem Unternehmen.
Denn Sie wollen dynamische Systeme mit einer stärkeren Vernetzung? Und darüber hinaus Investitionssicherheit und maximale Flexibilität bei sich ändernden Anforderungen? Unsere Lösungen zur Lagerautomatisierung stehen für mehr Wirtschaftlichkeit, Effizienz, Ergonomie und Qualität im Unternehmen. Mit neuen Denkansätzen und einem Mix aus innovativen und bewährten Technologien eröffnen wir neue Möglichkeiten für die produzierende Industrie. Denn unsere Mission lautet:
Wir verstehen Ihr Business und bringen mit innovativen Logistiklösungen das Plus an Flexibilität in Ihre Prozesse.
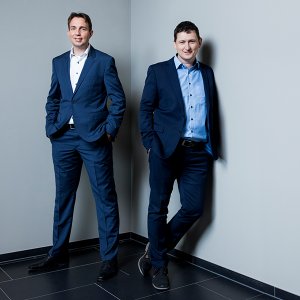
Haben Sie Fragen? Wir sind gerne für Sie da!
Stefan Lechner & Christian Brauneis
Vice Presidents Business Unit Industry
Email: kin.sales@knapp.com
„Wir wissen über die Wertigkeit der Prozesssicherheit im Herzen eines jeden Unternehmens – der Produktion – Bescheid und sehen es als Aufgabe, mit unserem Know-How optimale Lösungen zu entwickeln. Durch innovative Technologien und den Einsatz von intelligenter Software werden Prozesse optimal vernetzt und anpassungsfähig gestaltet. Wir setzen mit unseren Gesamtlösungen auf eine Smart Production.“
Christian Brauneis
Vice President Business Unit Industry
Sie interessieren sich für die Lagerautomatisierung in Ihrem Unternehmen?
Erfahren Sie mehr über unsere Lösungen und Referenzen!
Lösungen zur Lagerautomatisierung in der Industrie
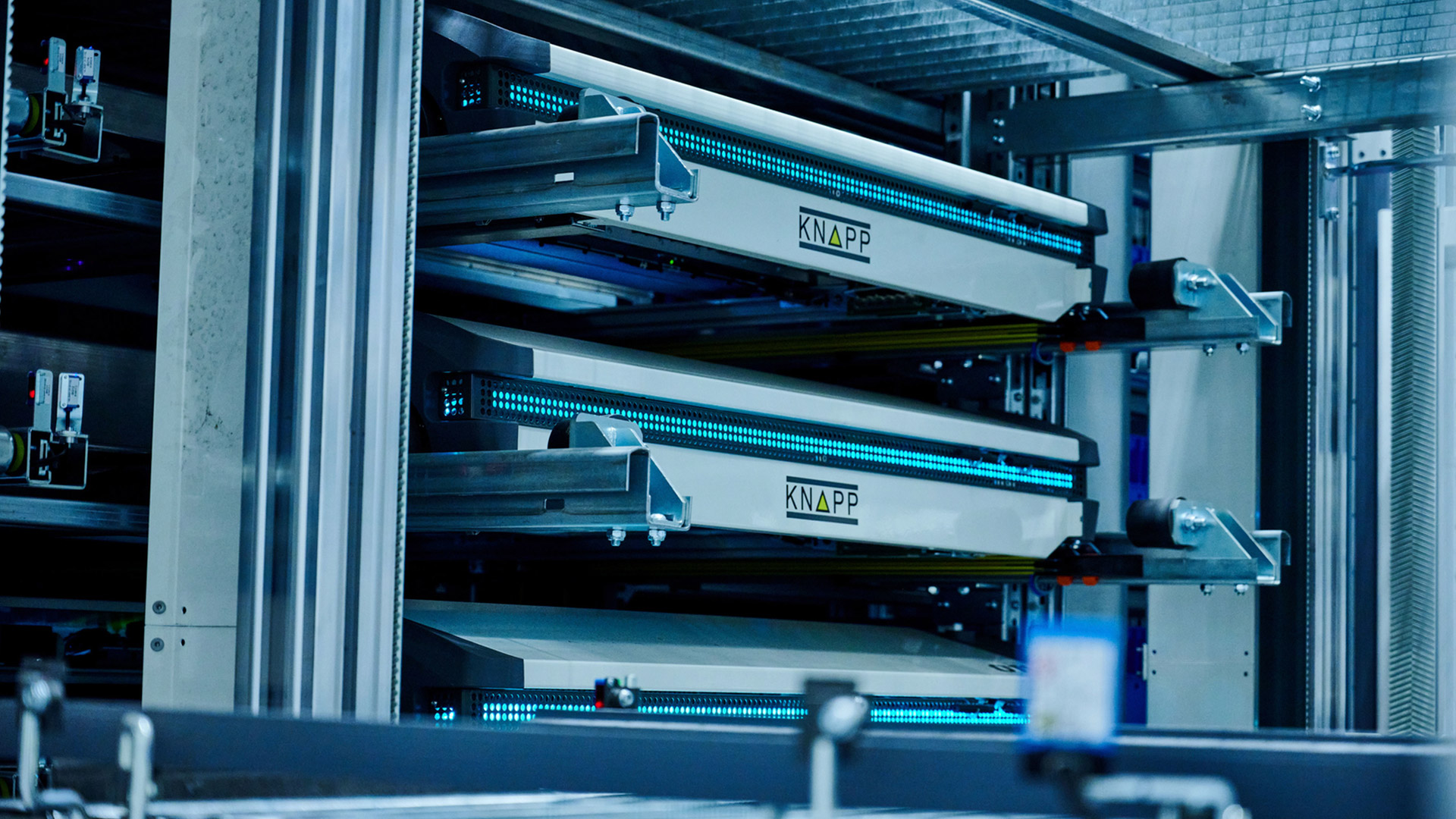
Automatische Lagersysteme für effiziente Produktionsprozesse
Automatisches Kleinteilelager, Regalbediengerät oder Puffertürme – wir bieten für jede Anforderung die optimale logistische Lösung. Unsere Lagersysteme unterstützen Prozesse wie Kommissionieren, Puffern, Sequenzieren von Waren und Aufträgen sowie die Versorgung von Arbeitsplätzen. Erfahren Sie mehr über unsere smarten Lösungen:
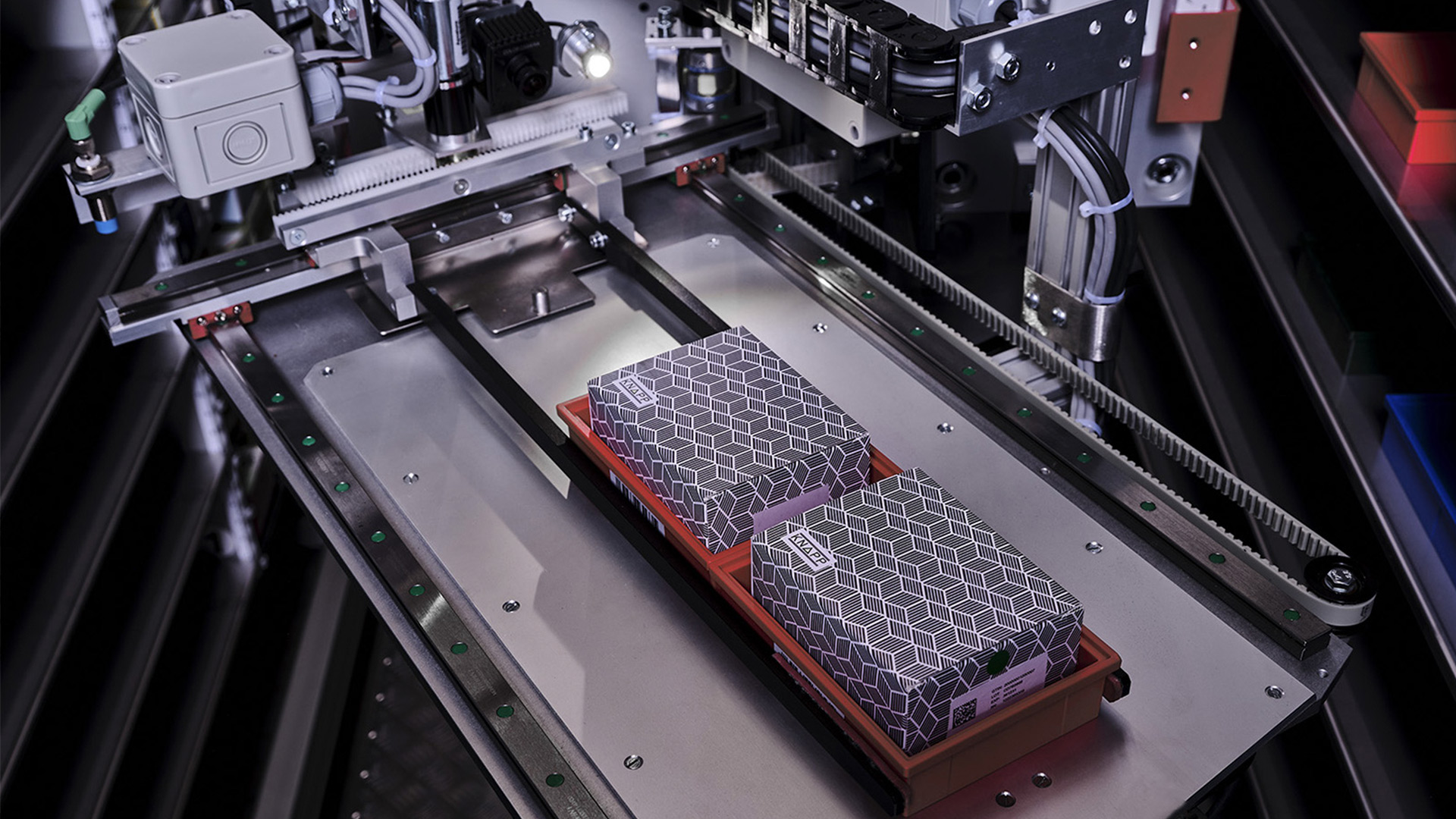
Lager- und Kommissionierautomaten
für höhere Performance
Der InduStore ist als Lager- und Kommissionierautomat die passende Lösung für Industrieanwendungen. Das System eignet sich für die Bevorratung auf Einzelstückbasis, als Lager zur Produktionsversorgung oder als Ersatzteillager. Erfahren Sie mehr über das System:
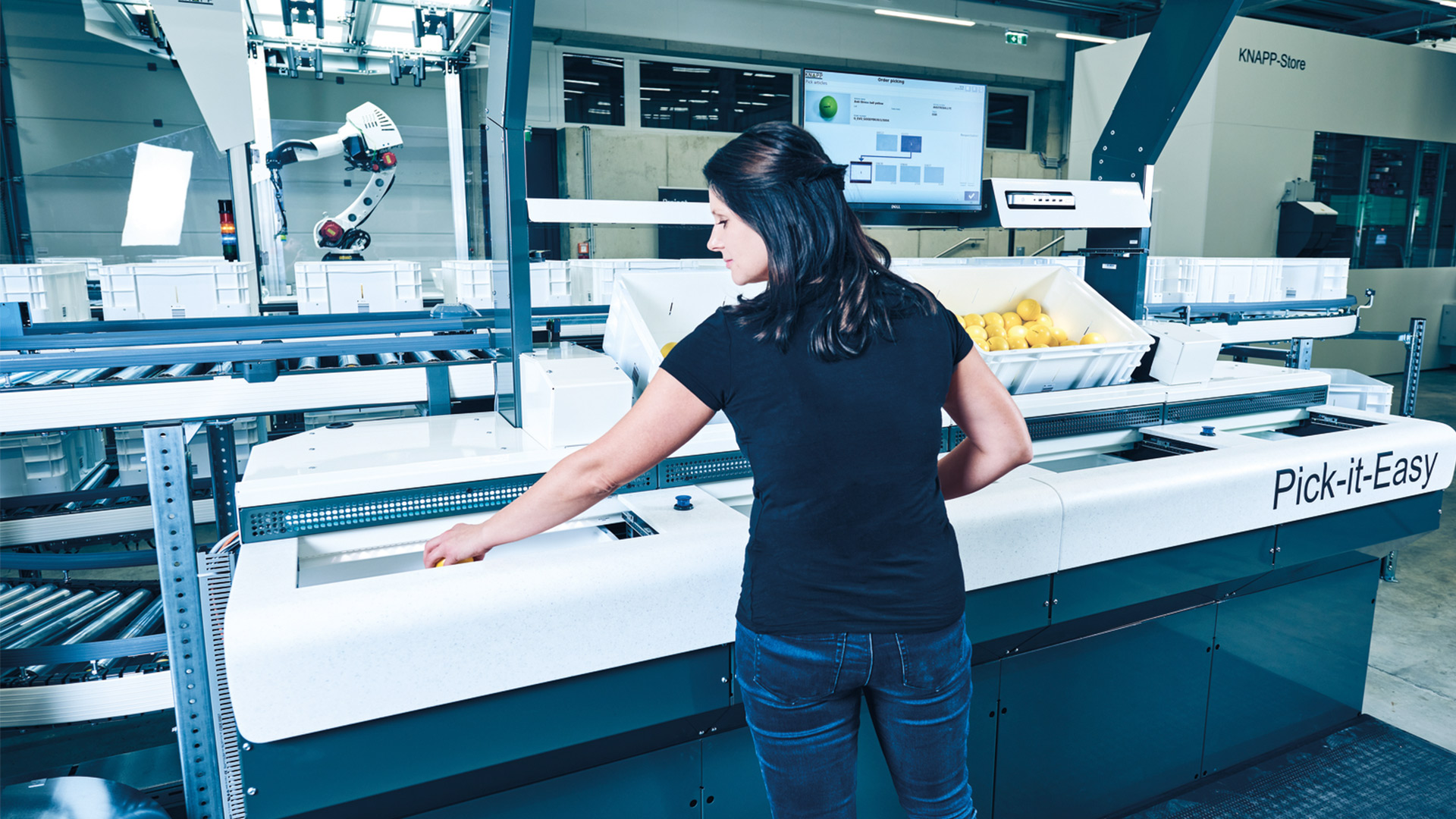
Ergonomische und intelligente Arbeitsstationen
Unsere Arbeitsstationen vereinen Ergonomie, Effizienz und Qualität. Das Ware-zur-Person-Prinzip sorgt für eine optimale Auftragsbearbeitung und zufriedene Mitarbeiter:innen. Die smarten Arbeitsplätze mit intelligentem Kamerasystem ermöglichen eine 100%ige Qualitätskontrolle. Erfahren Sie mehr über unser Angebot:
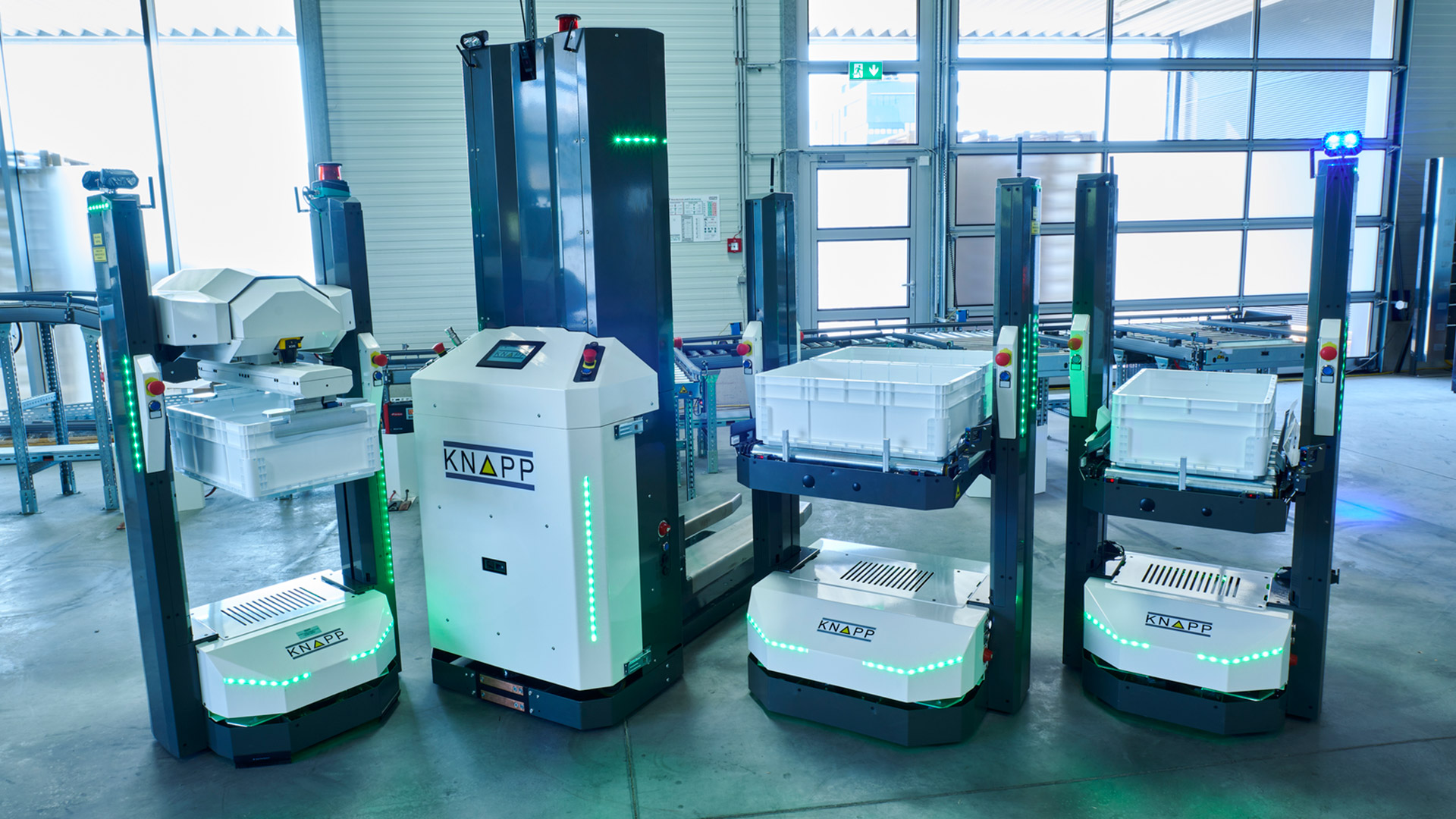
Fahrerlose Transportsysteme für mehr Flexibilität
Unsere intelligenten, fahrerlosen Transportsysteme ermöglichen eine flexible Gestaltung von Logistik-Prozessen. Sie automatisieren interne Transporte und vernetzen effizient unterschiedliche Produktionsbereiche. Erfahren Sie mehr über unsere autonomen mobilen Roboter (AMR):
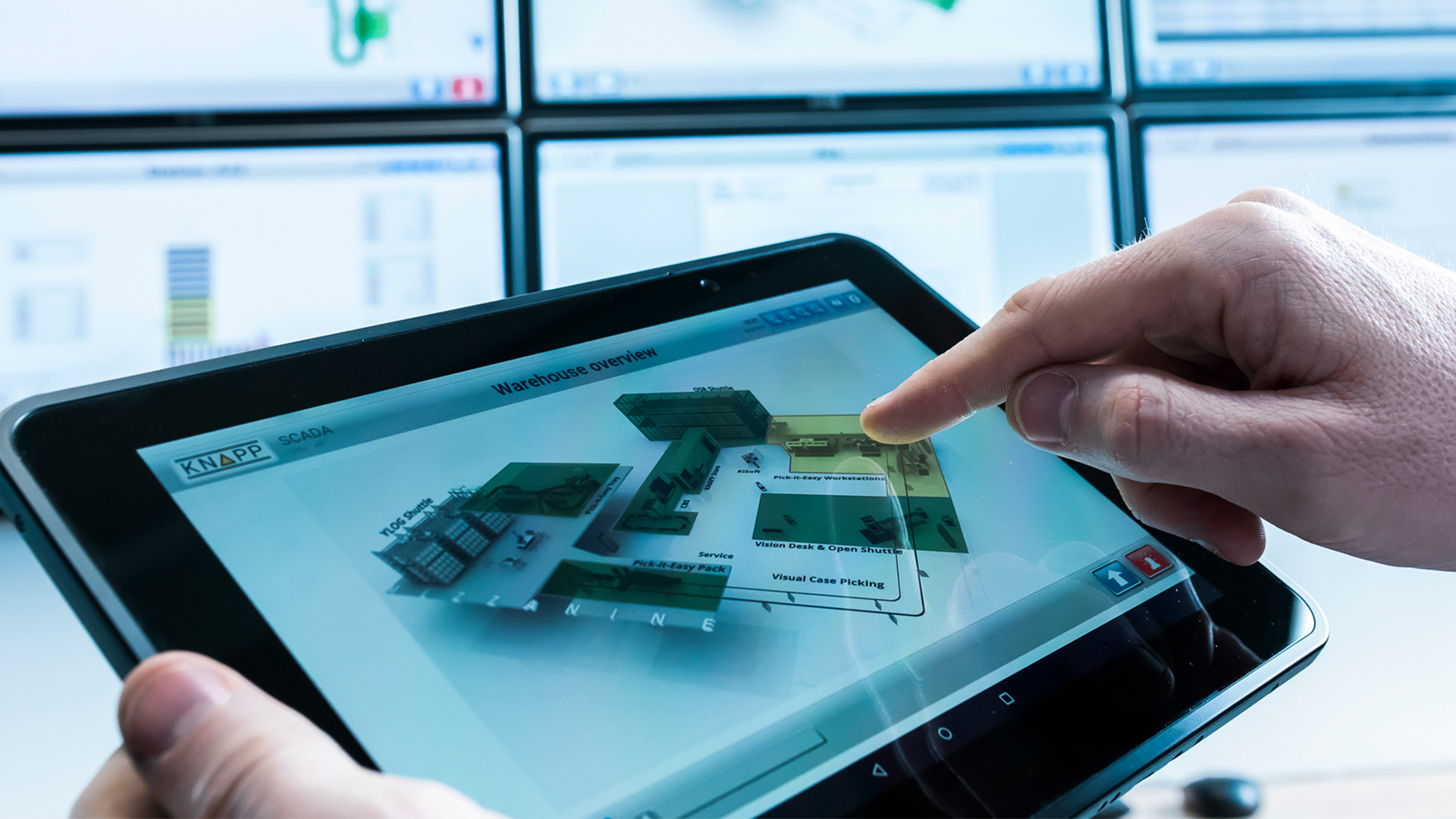
Software für die Lagerautomatisierung
Das Herzstück jeder Lagerautomatisierung ist die Software. Als Value Chain Tech Partner bieten wir umfassende All-in-One-Software-Lösungen, intelligente Flottenkontroll-Software, Software zur Ressourcenplanung uvm. Je nach Bedarf decken wir Prozesse mit unseren Produktlinien KiSoft und SAP® EWM by KNAPP ab. Erfahren Sie mehr über unsere umfassenden Software-Lösungen:
Vorteile für die Produktionslogistik
Die Automatisierung der Produktionslogistik bietet für produzierende Unternehmen umfangreiche Vorteile:
Referenzen:
Unsere Lösungen für die Lagerautomatisierung in der Industrie
Unternehmen weltweit setzen auf die Zusammenarbeit mit KNAPP. Wir unterstützen Sie bei der Optimierung von Produktionsprozessen, Lagerflächen und innerbetrieblichen Transporten. Unsere Lösungen sprechen für sich:
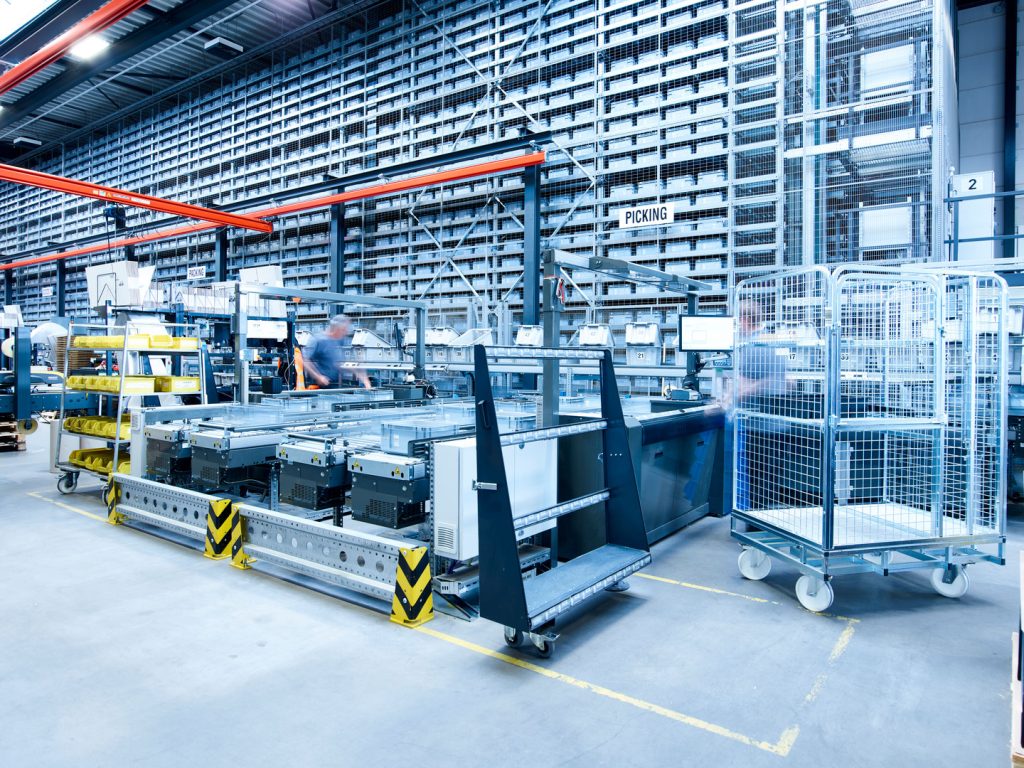
Terberg Benschop B.V.: Installierte Lösung schafft Basis für künftiges Unternehmenswachstum
Um eine steigende Anzahl an Aufträgen abwickeln zu können, wurden mehrere Prozesse bei Terberg in einem automatischen Lagersystem zentralisiert. Je nach Auftrag wird für die Produktion, Montaglinie oder für den Ersatzteilversand kommissioniert. Die Versorgung erfolgt bedarfsgerecht just-in-time.
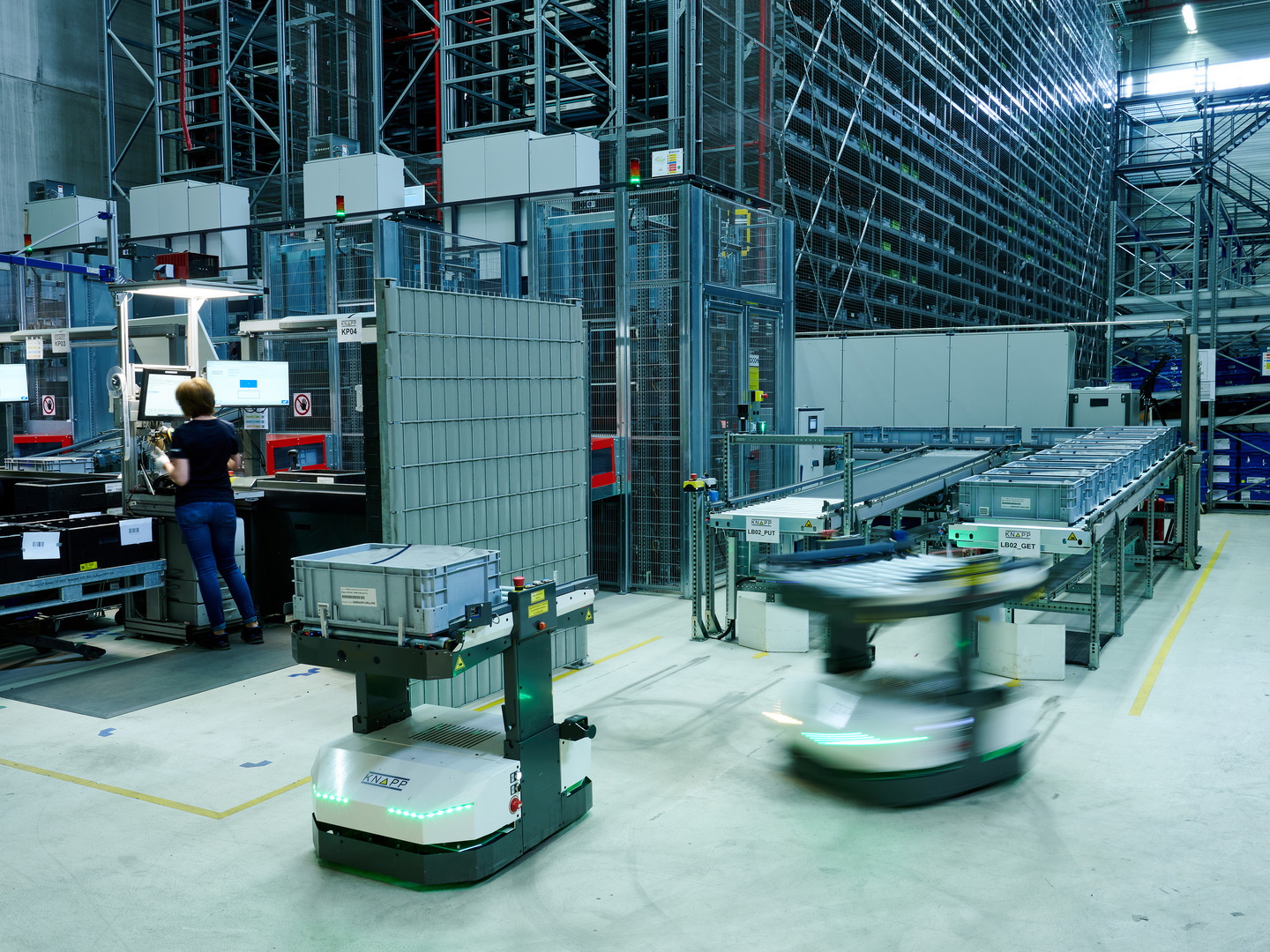
Magna Spiegelsysteme: Optimierte Versorgung der Produktion und Assemblierung
Mit der automatisierten Lösung von KNAPP ist es Magna gelungen, die schnellere Verfügbarkeit von Teilen sicherzustellen, den internen Verkehr zu reduzieren und das Lager personenfrei zu bedienen. Basis ist eine multifunktionale Shuttle-Anlage in Kombination mit autonomen mobilen Robotern.
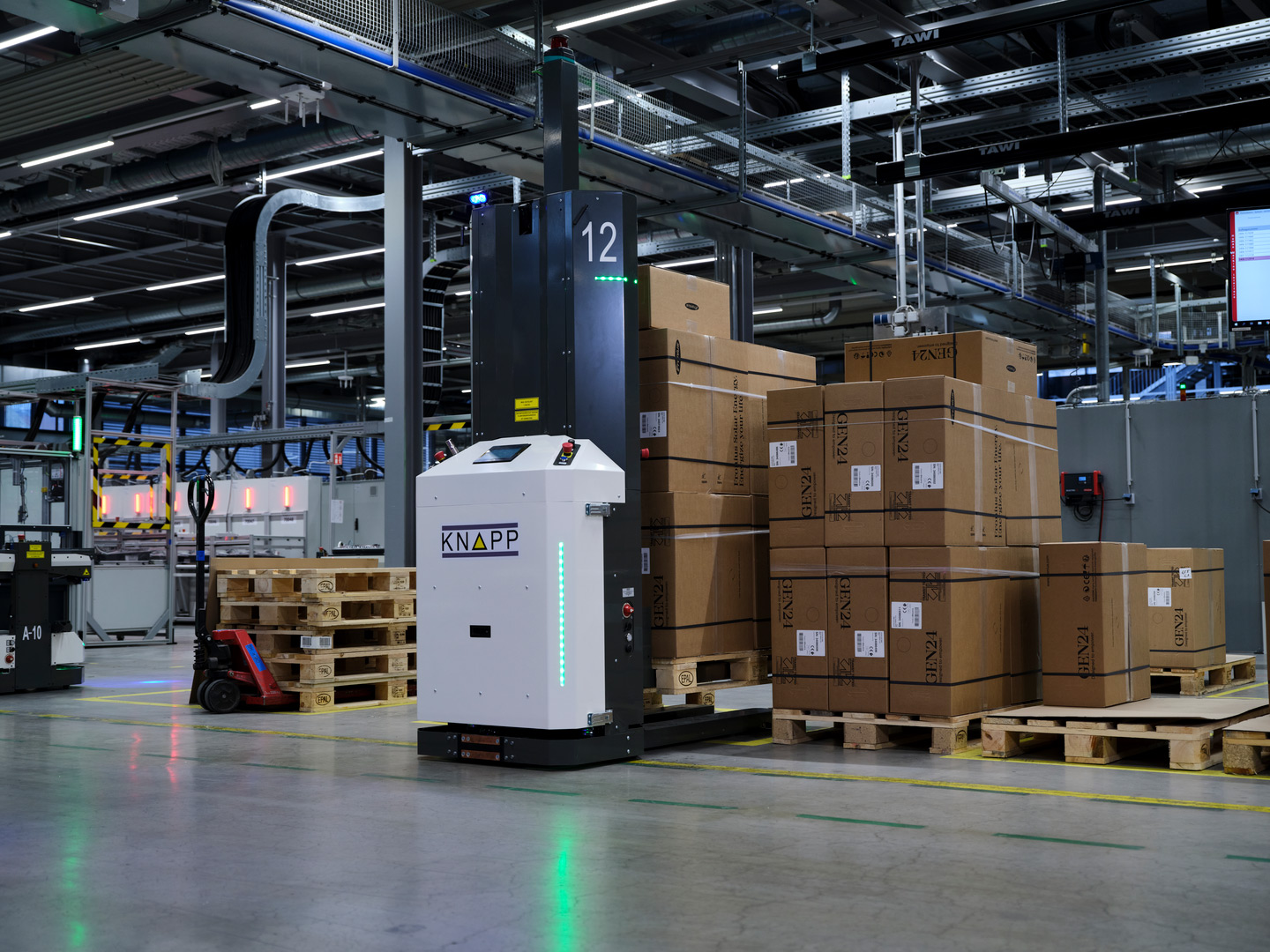
Fronius: Automatisierter Palettentransport mit AMR für flexible Produktionsversorgung
Die innovativen Open Shuttle Fork automatisieren die Produktionsversorgung und den innerbetrieblichen Transport bei Fronius. Mit der neuen Lösung kann das Unternehmen flexibel und selbständig Änderungen vornehmen sowie manuelle und automatisierte Aufträge in einem System verwalten.
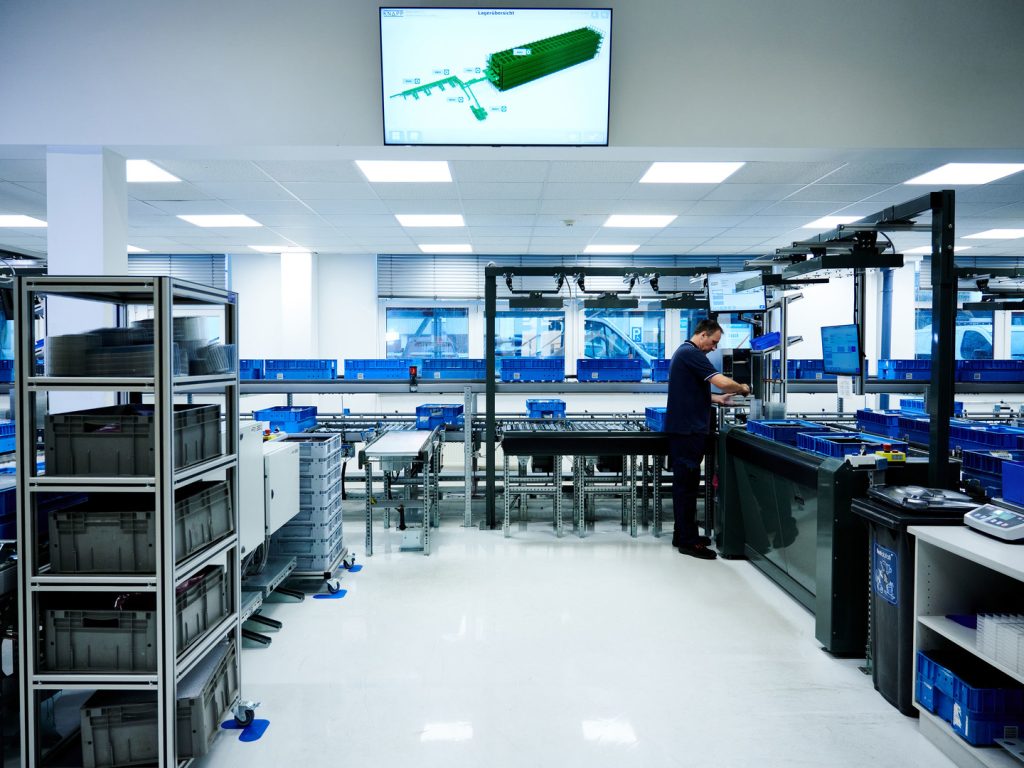
Knorr-Bremse: Prozessoptimierung durch maßgeschneidertes System
Knorr-Bremse hat die Leistungsfähigkeit im Kleinteilelager um den Faktor drei gesteigert. Grundlage ist eine multifunktionale Shuttle-Anlage in Kombination mit Kommissionierarbeitsplätzen und deckenmontierter Fördertechnik. Erfahren Sie mehr über die Lösung, die verschiedene Prozesse effizient abdeckt.
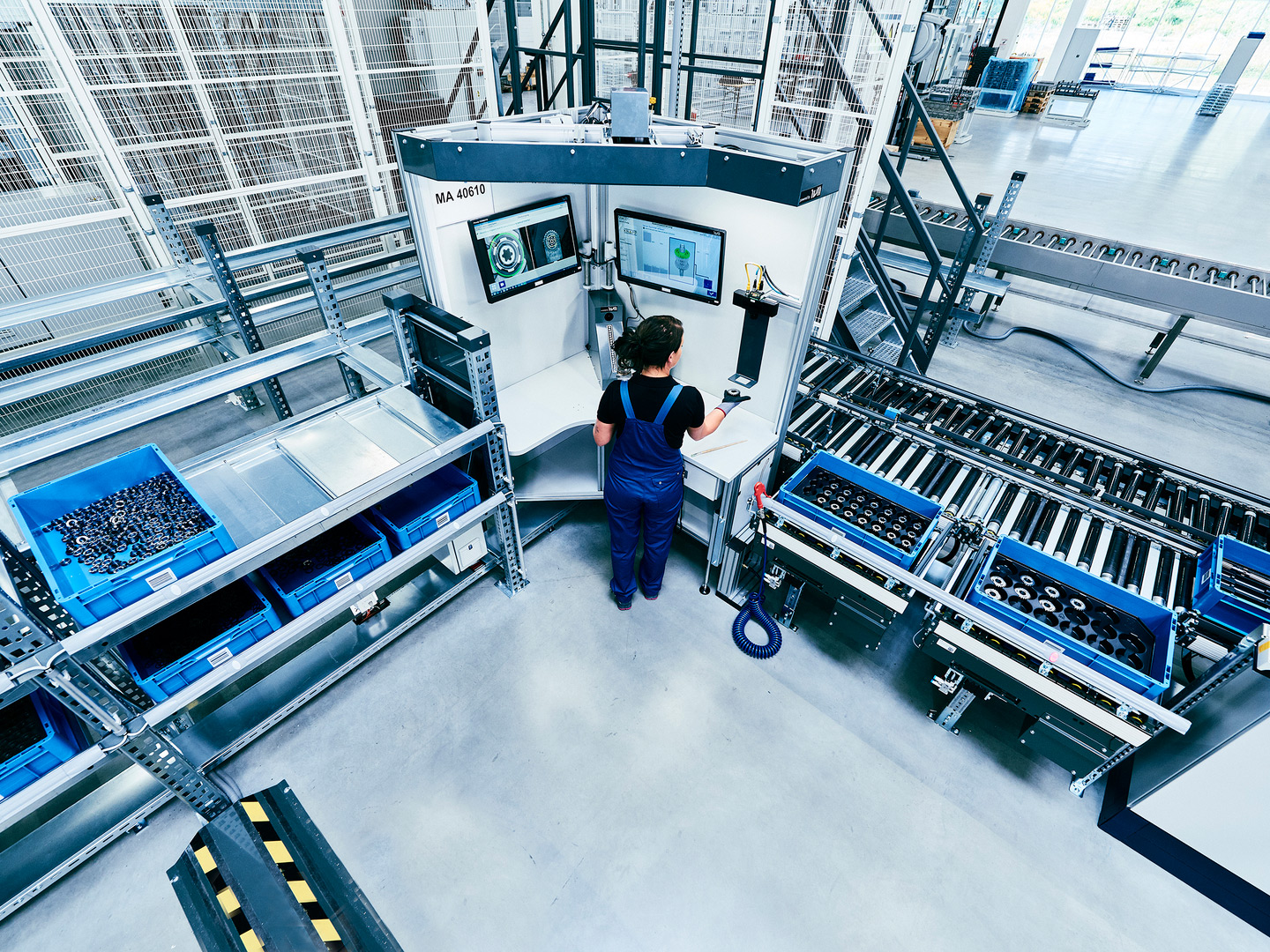
Pankl Racing AG: Null-Fehler-Strategie im gesamten Fertigungsprozess
Ein automatisches Kleinteilelager versorgt bei Pankl die Montagearbeitsplätze nach dem Ware-zur-Person-Prinzip. Moderne Bilderkennungs- und Bildverarbeitungstechnologie überprüft jeden Arbeitsschritt und sorgt für einen fehlerfreien Zusammenbau und lückenlose Verfolgbarkeit. Ein Paradebeispiel für eine Smart Production.
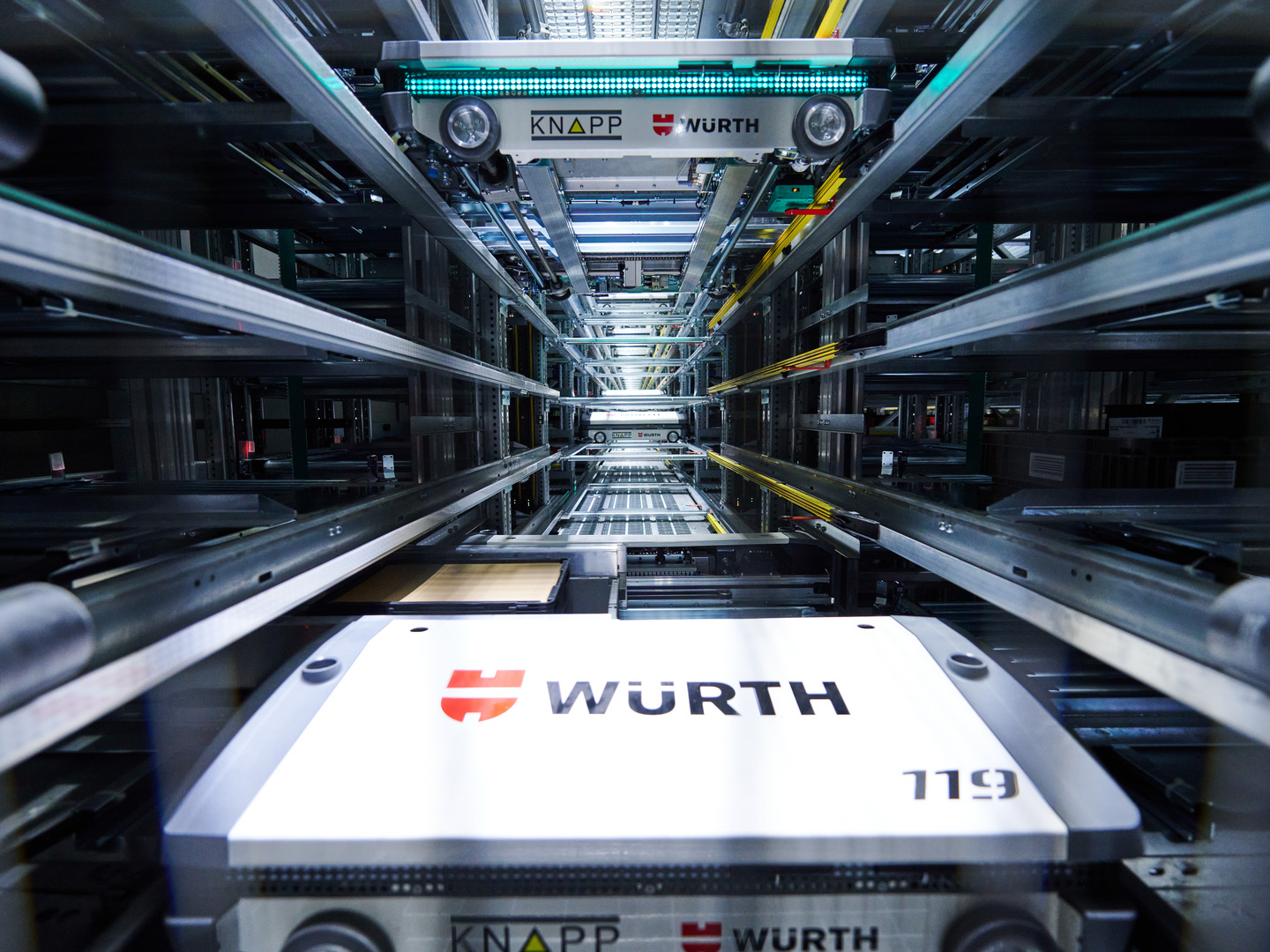
Würth: Intelligente Automatisierung in der Logistik
Bei Würth kommen modernste Robotik-Technologien zum Einsatz. Von der Lagerung über die Kommissionierung und den Versand bis hin zum internen Transport werden logistische Prozesse vollautomatisch abgewickelt. Als langjähriger Partner unterstützen wir in der kontinuierlichen Weiterentwicklung.
Referenzen:
Unsere Lösungen für die Lagerautomatisierung in der Industrie
Unternehmen weltweit setzen auf die Zusammenarbeit mit KNAPP. Wir unterstützen Sie bei der Optimierung von Produktionsprozessen, Lagerflächen und innerbetrieblichen Transporten. Unsere Lösungen sprechen für sich:
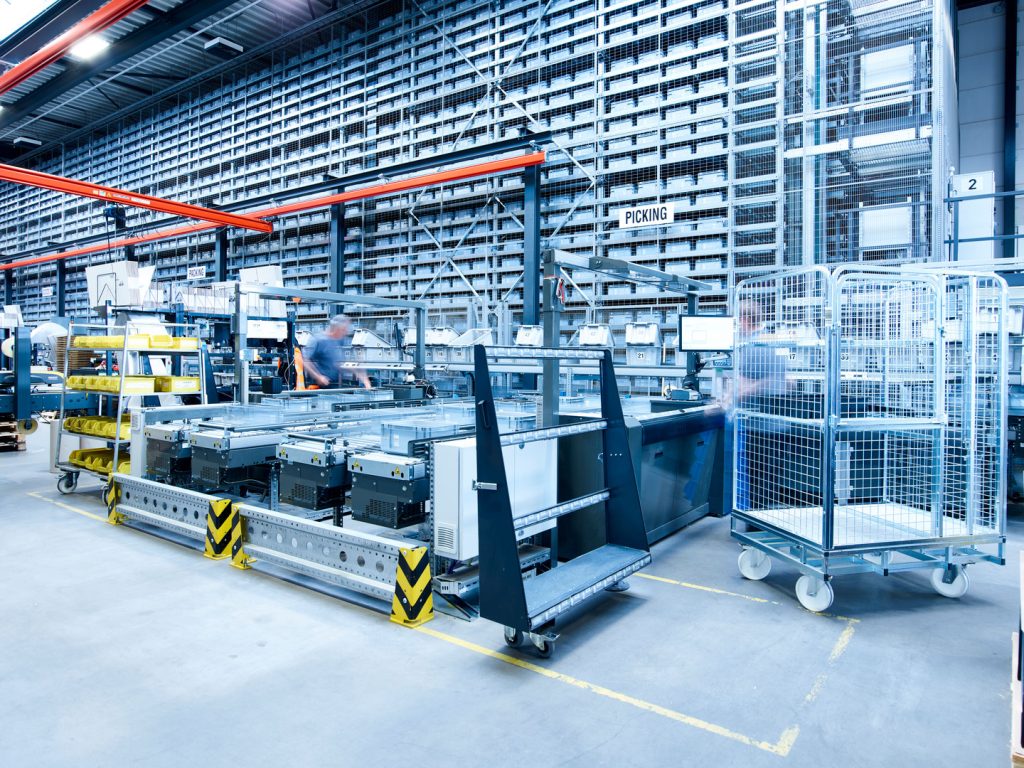
Terberg Benschop B.V.: Installierte Lösung schafft Basis für künftiges Unternehmenswachstum
Um eine steigende Anzahl an Aufträgen abwickeln zu können, wurden mehrere Prozesse bei Terberg in einem automatischen Lagersystem zentralisiert. Je nach Auftrag wird für die Produktion, Montaglinie oder für den Ersatzteilversand kommissioniert. Die Versorgung erfolgt bedarfsgerecht just-in-time.
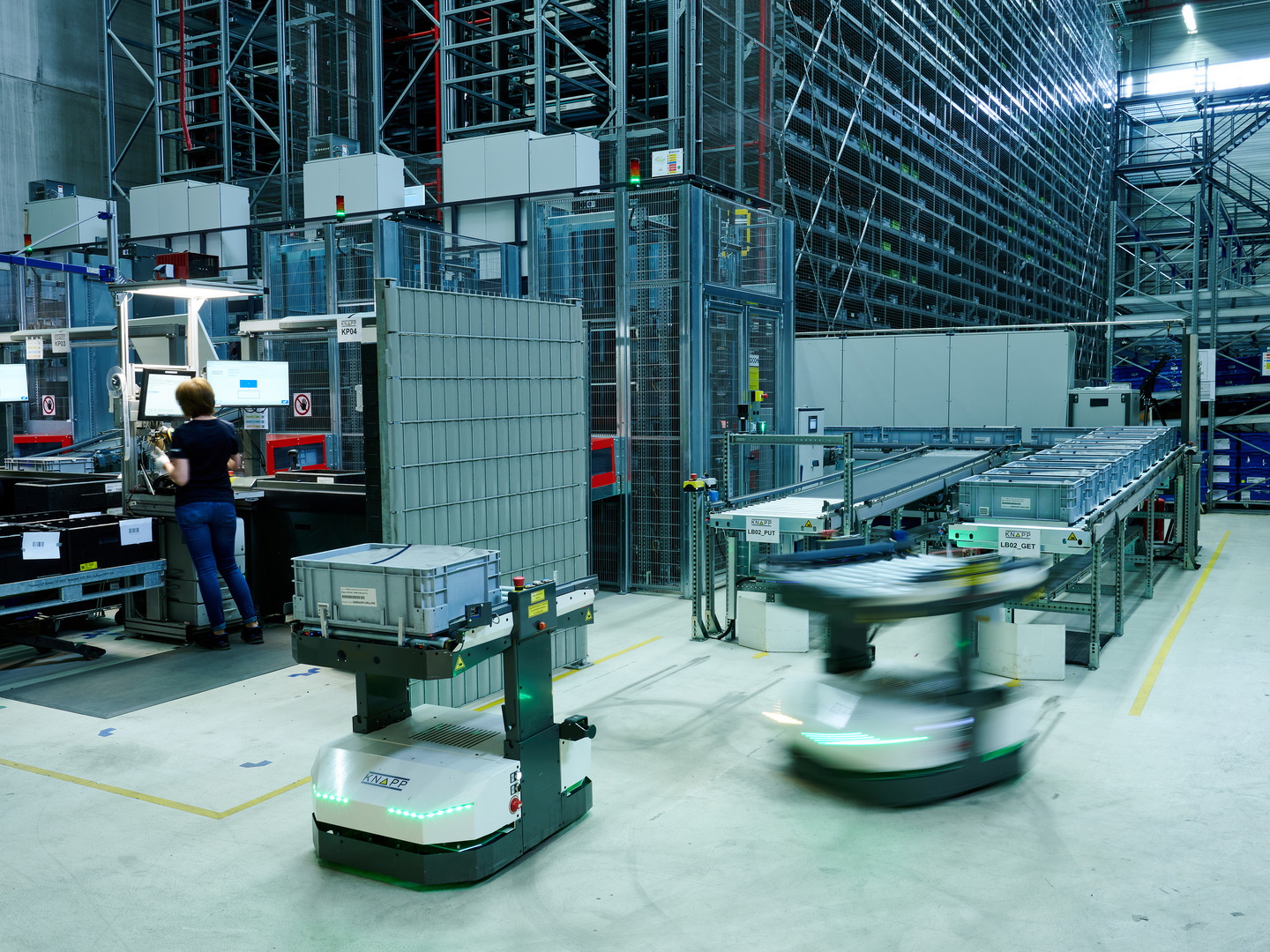
Magna Spiegelsysteme: Optimierte Versorgung der Produktion und Assemblierung
Mit der automatisierten Lösung von KNAPP ist es Magna gelungen, die schnellere Verfügbarkeit von Teilen sicherzustellen, den internen Verkehr zu reduzieren und das Lager personenfrei zu bedienen. Basis ist eine multifunktionale Shuttle-Anlage in Kombination mit autonomen mobilen Robotern.
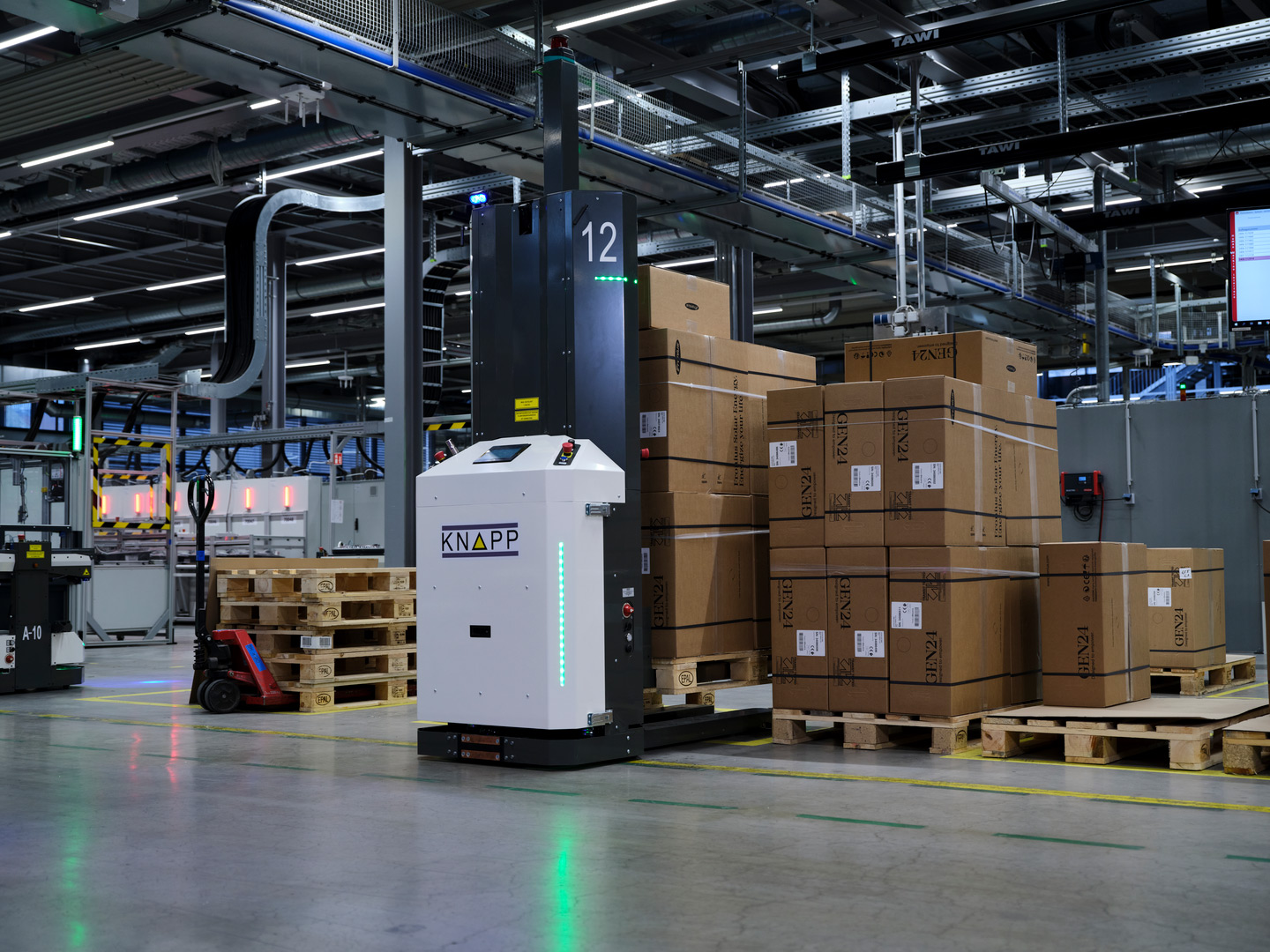
Fronius: Automatisierter Palettentransport mit AMR für flexible Produktionsversorgung
Die innovativen Open Shuttle Fork automatisieren die Produktionsversorgung und den innerbetrieblichen Transport bei Fronius. Mit der neuen Lösung kann das Unternehmen flexibel und selbständig Änderungen vornehmen sowie manuelle und automatisierte Aufträge in einem System verwalten.
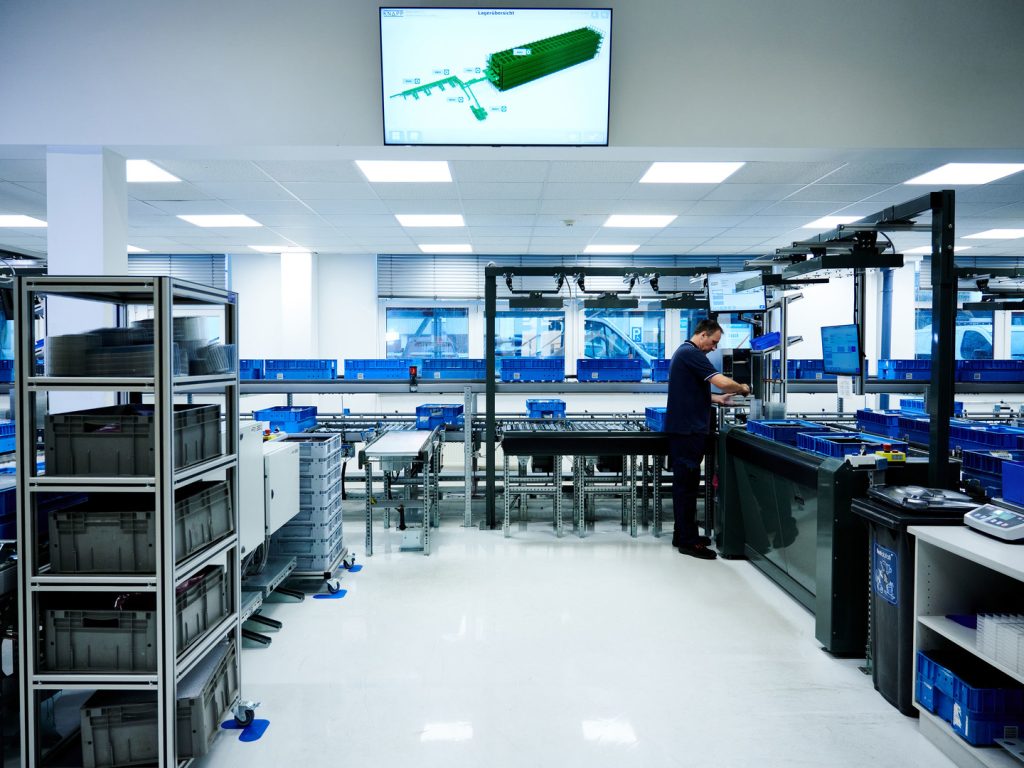
Knorr-Bremse: Prozessoptimierung durch maßgeschneidertes System
Knorr-Bremse hat die Leistungsfähigkeit im Kleinteilelager um den Faktor drei gesteigert. Grundlage ist eine multifunktionale Shuttle-Anlage in Kombination mit Kommissionierarbeitsplätzen und deckenmontierter Fördertechnik. Erfahren Sie mehr über die Lösung, die verschiedene Prozesse effizient abdeckt.
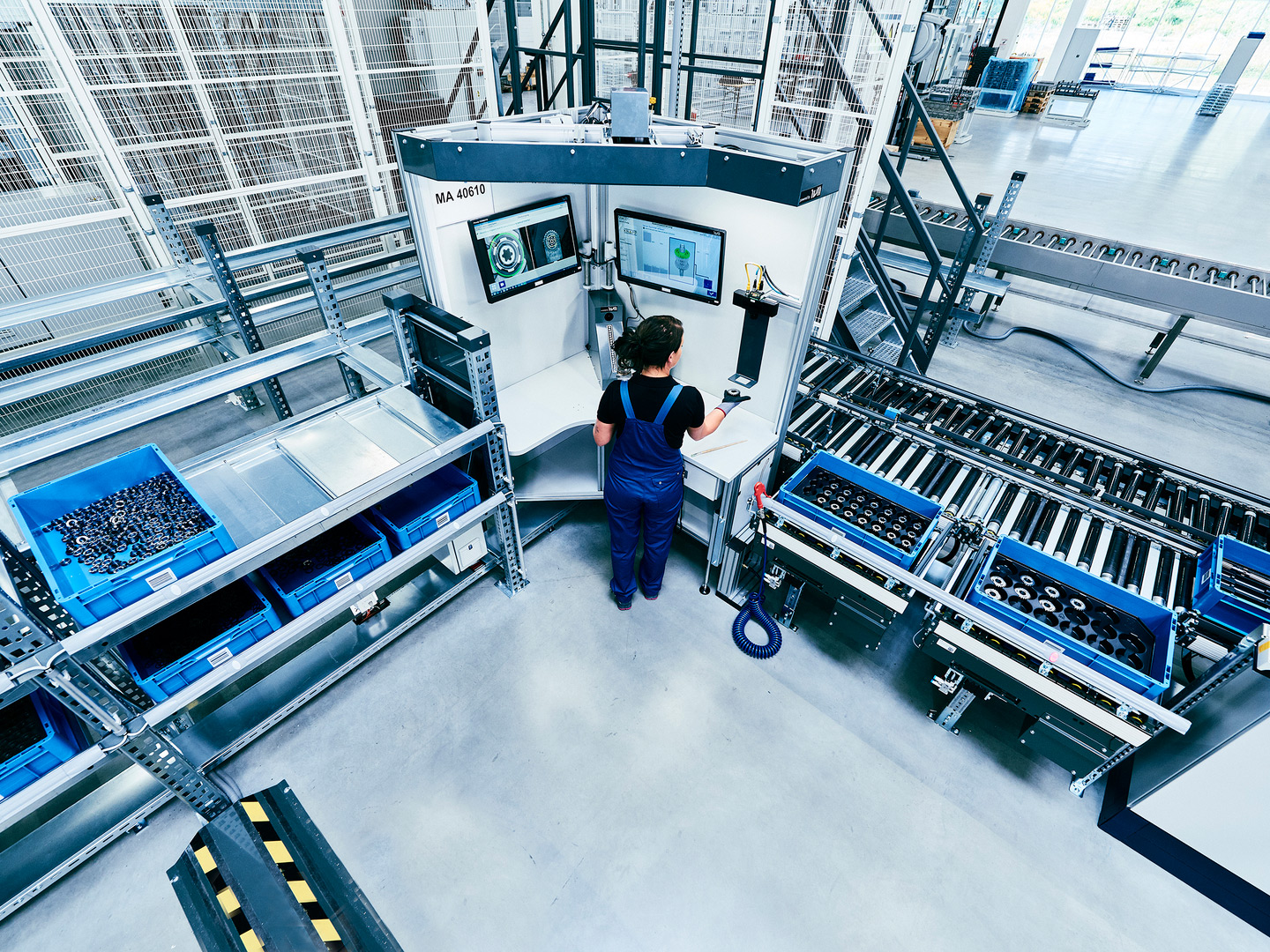
Pankl Racing AG: Null-Fehler-Strategie im gesamten Fertigungsprozess
Ein automatisches Kleinteilelager versorgt bei Pankl die Montagearbeitsplätze nach dem Ware-zur-Person-Prinzip. Moderne Bilderkennungs- und Bildverarbeitungstechnologie überprüft jeden Arbeitsschritt und sorgt für einen fehlerfreien Zusammenbau und lückenlose Verfolgbarkeit. Ein Paradebeispiel für eine Smart Production.
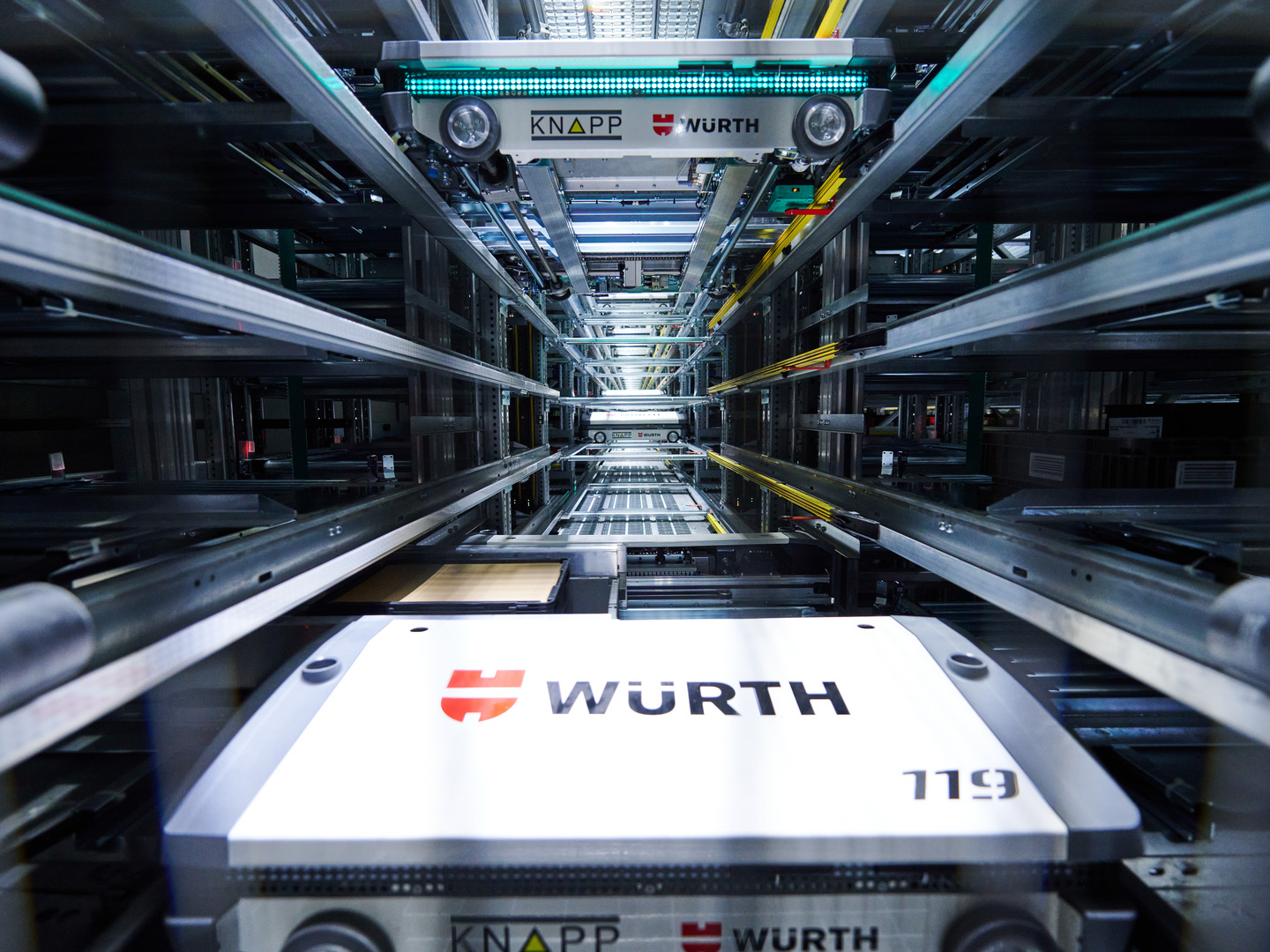
Würth: Intelligente Automatisierung in der Logistik
Bei Würth kommen modernste Robotik-Technologien zum Einsatz. Von der Lagerung über die Kommissionierung und den Versand bis hin zum internen Transport werden logistische Prozesse vollautomatisch abgewickelt. Als langjähriger Partner unterstützen wir in der kontinuierlichen Weiterentwicklung.
Globales Servicenetzwerk & zuverlässiger Partner
Unser internationales Customer Service betreut Ihr Logistiksystem weltweit
und rund um die Uhr, an 365 Tagen im Jahr.
Erfahren Sie mehr über unsere Leistungen – vom lückenlosen Support bis hin zur Optimierung der Anlage!
Lagerautomatisierung für die Industrie -
diese Unternehmen vertrauen auf uns:
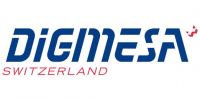
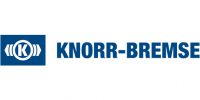
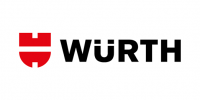
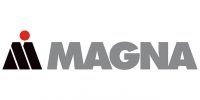
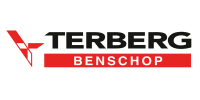
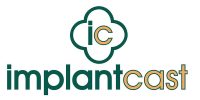
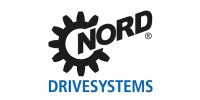
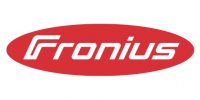
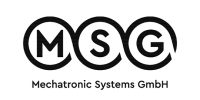
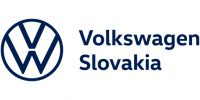
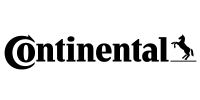
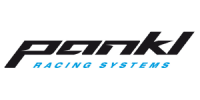
Sie interessieren sich für unsere Lösungen zur Lagerautomatisierung in der Industrie?
Wir informieren Sie gerne!
Spannende Blogbeiträge rund um
Automatisierung von Lager und Value Chain

Durch die Automatisierung der Intralogistik Prozesse optimieren und Leistung steigern. Welches Maß an Automatisierungsgrad ist für Ihren Betrieb sinnvoll? In diesem Beitrag stellen wir unterschiedliche Ausbaustufen vor: vom innovativen manuellen Lager bis hin zur Vollautomatisierung.

Höhere Effizienz, optimierte Geschwindigkeit und kürzere Durchlaufzeiten – diese Vorteile bietet SCHUNK der Einsatz des autonomen mobilen Roboters Open Shuttle. Erfahren Sie mehr über die flexible Lösung und die Zusammenarbeit mit KNAPP im Interview.

Die neue EU-Verpackungsverordnung 2025 (PPWR) bringt einige Neuerungen. Finden Sie hier einen Überblick zu den Vorgaben und möglichen Maßnahmen!