SCHUNK ist globaler Technologiepionier in der Spanntechnik, Greiftechnik und Automatisierungstechnik. Rund 3.700 Mitarbeitende in zehn Werken und 34 eigenen Ländergesellschaften sowie Vertriebspartner in über 75 Ländern sichern eine intensive Marktpräsenz. Am Standort Brackenheim-Hausen in Deutschland produziert das Unternehmen Greifer und Automatisierungskomponenten. Um die Produktionsversorgung von manuell auf automatisiert umzustellen, hat sich SCHUNK für die Implementierung eines Open Shuttles entschieden. Der autonome mobiler Roboter (AMR) sorgt für effiziente Prozesse und spielt Mitarbeiter:innen für wertschöpfende Tätigkeiten frei.
Wir sprachen mit Pascal Weiland, Leiter Montage & Logistik Gripping Technology & Automation Technology bei SCHUNK, über die Gründe für die Automatisierung, die Wahl des Open Shuttles und über die neue Lösung.
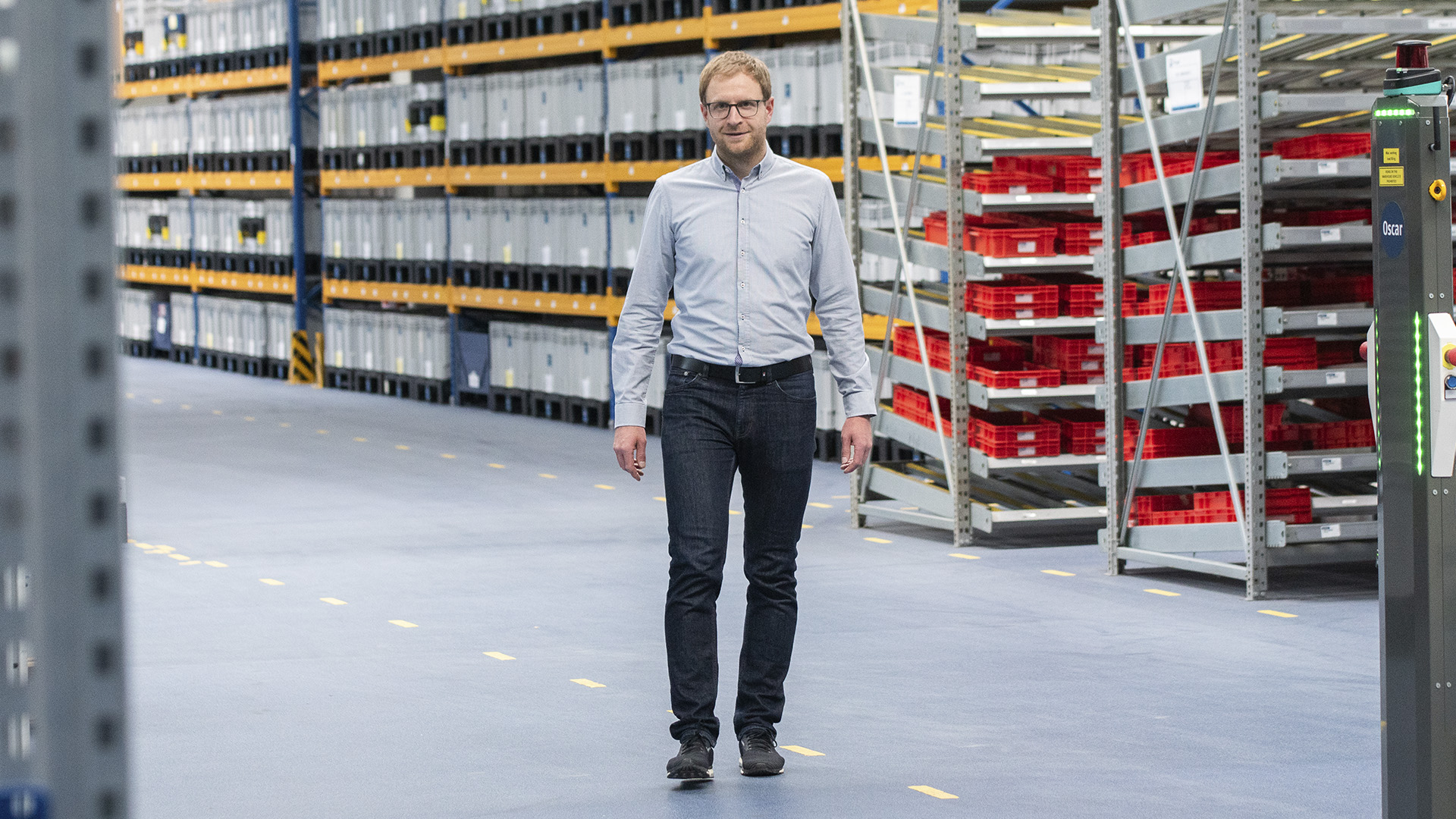
SCHUNK setzt auf autonome mobile Roboter zur Prozessoptimierung
Warum hat sich SCHUNK für den Einsatz von autonomen mobilen Robotern am Standort Brackenheim-Hausen entschieden?
Weiland: Es gab bereits erste Erfahrungen mit einem fahrerlosen Transportsystem, die wenig erfolgreich waren. Wir haben das Thema neu aufgesetzt, weil wir von der Technologie überzeugt sind. Mit KNAPP haben wir nicht nur den richtigen Partner, sondern auch das richtige Produkt gefunden, um erfolgreiche Erfahrungen zu sammeln. Aus folgenden Gründen haben wir uns für den Einsatz von AMR entschieden:
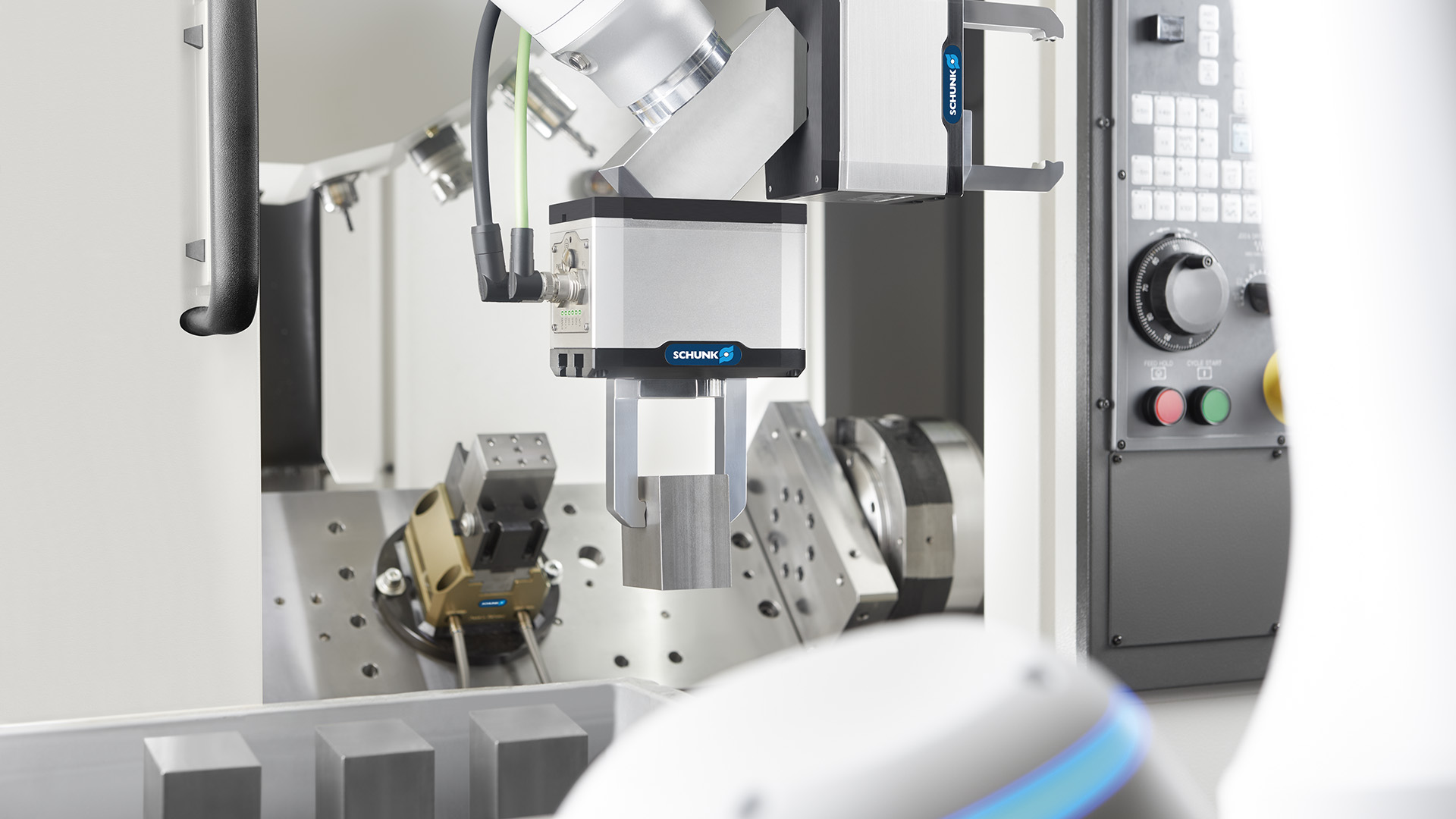
KNAPP als Partner mit langjähriger AMR-Erfahrung
Warum hat sich SCHUNK für das Open Shuttle von KNAPP entschieden?
Weiland: Wir von SCHUNK haben uns mit dem System seit 2016 beschäftigt. Bereits damals war KNAPP unser Favorit, weil das System unseren Transportanforderungen am besten entsprochen hat. Insbesondere ging es um den Transport von Behältern in der Größe 300 x 400 mm, die KNAPP als Standardlösung anbietet. Bis zur endgültigen Entscheidung für ein AMR-System hatte KNAPP auch die Höhenverstellung, also den integrierten Hub, umgesetzt. Dieser stand von Beginn an auf unserer Wunschliste. So hat das Open Shuttle noch besser unseren Ansprüchen entsprochen.
Weiland: Auch die langjährige Erfahrung hat für uns eine entscheidende Rolle gespielt. Wir wollten eine Lösung, die technisch ausgereift ist. Hier hatten wir bei KNAPP großes Vertrauen.
Weiland: Es ist uns wichtig, selbstständig Änderungen und Anpassungen vornehmen zu können. Das war ein entscheidender Punkt, denn wir von SCHUNK sind ein sehr flexibles, agiles Unternehmen, in dem sich Prozesse durchaus ändern können. Deshalb kam für uns keine Lösung in Frage, bei der wir auf externe Unterstützung angewiesen sind. Unser Anspruch war es, dass unser Personal auf die AMR-Lösung geschult ist und wir die Möglichkeit und die Berechtigung haben, kleine Änderungen wie z.B. Lokalitätsveränderungen von Übergabestellen selbst vornehmen zu können. Und das ermöglicht KNAPP seinen Kunden. In diesem Zusammenhang haben wir den Aufbau und den Inbetriebnahmeprozess begleitet, waren darin eingebunden und sind so bereits geschult worden.
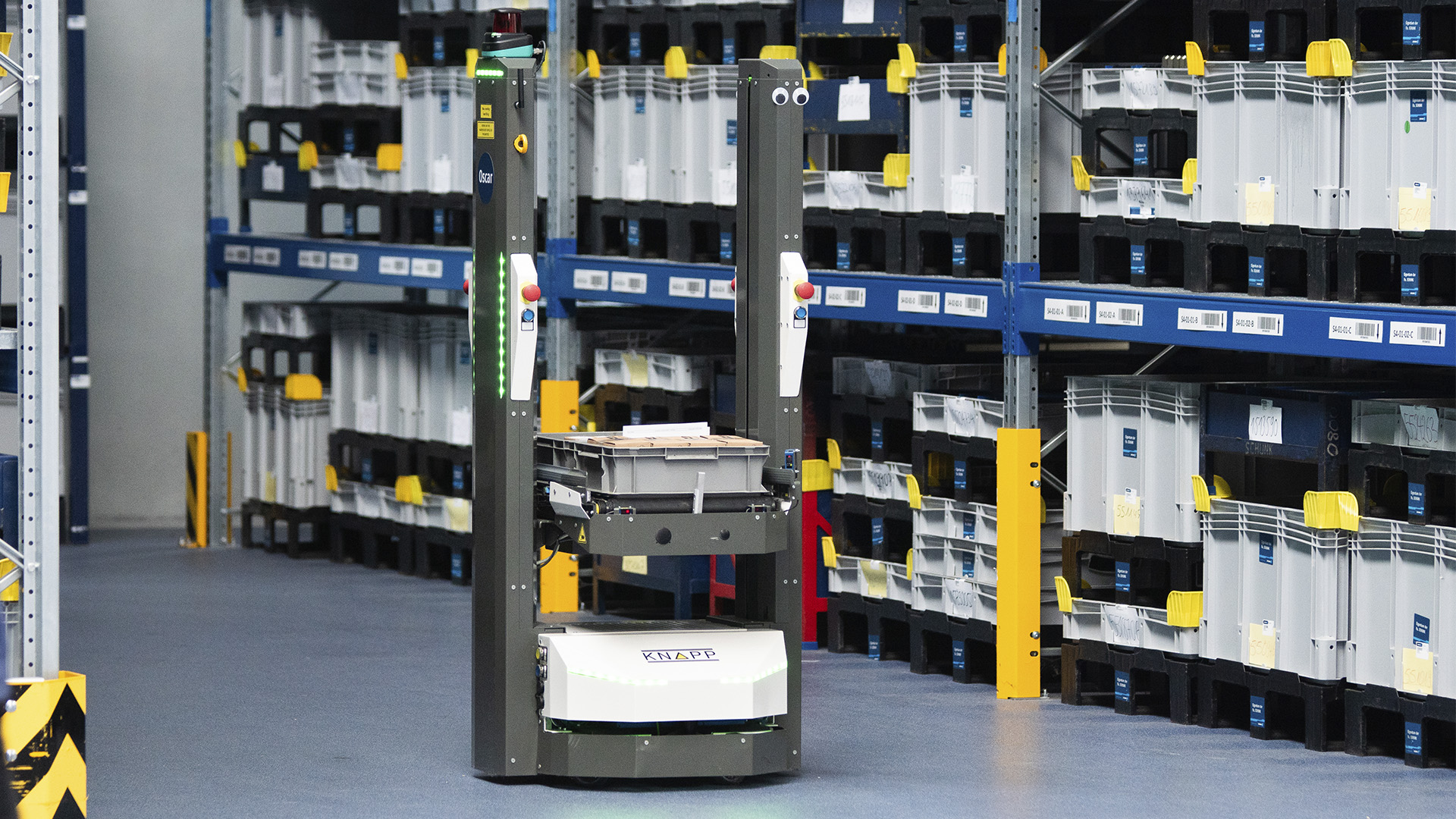
Mobiler Roboter: Interne Transportprozesse bei SCHUNK
Alle Fakten auf einen Blick:
Transport von 2 Behältern à 25kg
3 iO-Module zur Steuerung von 5 Schnelllauftoren und 4 Brandschutztoren
Welche Transportprozesse werden mit dem Open Shuttle abgewickelt?
Weiland: Wir sind am Standort Brackenheim-Hausen für die Produktion von Greifern und Automatisierungskomponenten zuständig. Das Open Shuttle übernimmt im innerbetrieblichen Transport folgende Prozesse:
- Transport der Einzelkomponenten von der Logistik an die Montagelinien, wo sie zu fertigen Schwenk- bzw. Greifeinheiten montiert werden und
- Abtransport der fertigen Einheiten zurück ins Lager
Das Open Shuttle transportiert die Einzelkomponenten der Greifer einschließlich der Auftragspapiere zu den einzelnen Montageteams. An den Montagelinien werden die Teile zusammengebaut, einer Qualitätskontrolle unterzogen und schließlich in fertige Produktkartons verpackt. Sowohl die an den Montagelinien benötigten Einzelkomponenten als auch die fertig verpackten Endprodukte werden vom Open Shuttle in Behältern zum Versandlager transportiert, wo sie bis zum nächsten Montageschritt bzw. bis zur Auslieferung zwischengelagert werden.
Maßgeschneiderte, intelligente Automatisierungslösung
Welche Besonderheiten hat die neue Automatisierungslösung?
Weiland: Die Übergabe der Behälter an die Montagelinien sowie an das Kleinteilelager erfolgt über Durchlaufregale mit Rollenbahnen, die mit einer Stellplatzsensorik ausgestattet sind. Sobald der Behälter auf eine Lichtschranke stößt, wird ein Auftrag ausgelöst und das Open Shuttle holt den Behälter zum Transport ab. Wir haben uns für diese Lösung entschieden, da sie technisch einfach ist, auf Gewichtskraft basiert und mit wenig Elektronik auskommt. Die Sensorik überwacht die Stellplätze an Quelle und Ziel und meldet den Bedarf zur Abholung, bzw. wenn Platz für eine Anlieferung ist, an das System. Dadurch werden Transportaufträge automatisch generiert und Leerläufe vermieden. Bei der Implementierung weiterer Montagelinien bauen wir die Durchlaufregale selbst und beziehen die Auslösemechanismen, Orientierungsdreiecke, Sensorik und iO-Module als Bausatz von KNAPP.
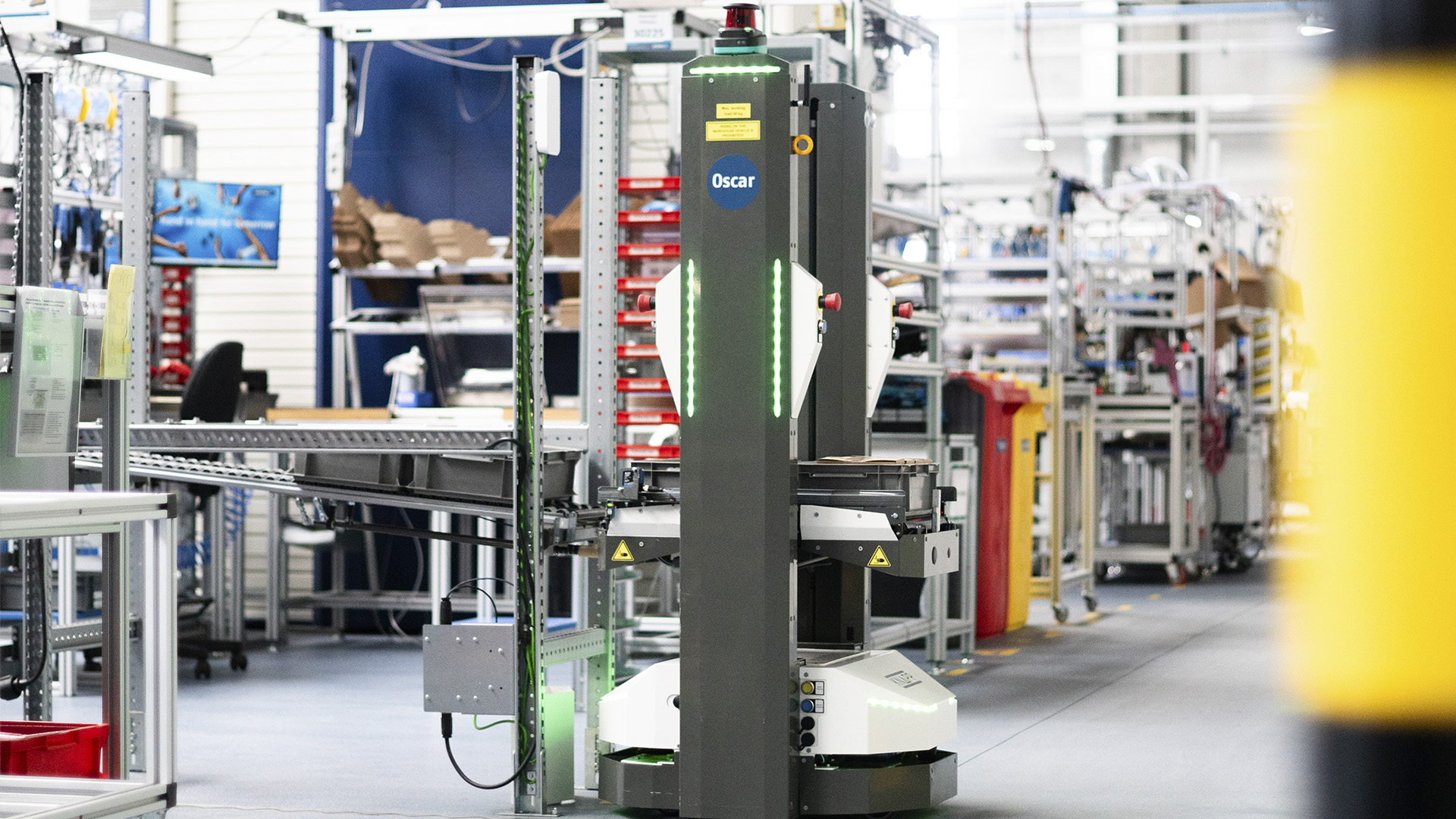
„Da wir die Durchlaufregale selbst bauen können, sind wir in der Einbindung weiterer Montagelinien schneller und flexibler. Wir können Gestelle verändern und erweitern, je nachdem, wie wir sie brauchen.“
Weiland: Auf der Wegstrecke zwischen den einzelnen Montagelinien und dem Kleinteilelager befinden sich fünf Schnelllauftore, die über ein Modul mit dem Open Shuttle in Verbindung stehen. Wenn der autonome mobile Roboter zum Tor fährt, öffnet es sich automatisch. Ebenso befinden sich an diesen Durchfahrten auch Brandschutztore, die im Bedarfsfall zufahren. In diesem Bereich darf das Fahrzeug aus brandschutztechnischen Gründen nicht halten. KNAPP hat uns hier sehr souverän geholfen, da sie bereits Erfahrung mit diesen Themen und Lösungen umgesetzt hatten. Mit dem sogenannten iO-Modul fragt der AMR ab, ob ein Brandfall vorliegt oder nicht, und verhindert so auch ein Einfahren in den Korridor vor dem Brandschutztor. Es funktioniert sehr zuverlässig und ohne Schwierigkeiten.
Oscar: ein autonomer mobiler Roboter als neuer Kollege
Wie zufrieden sind Sie mit der Lösung, den innerbetrieblichen Transport mit dem Open Shuttle abzuwickeln?
Weiland: Wir sind sehr zufrieden mit Oscar, so nennen wir das Open Shuttle. Vielleicht kurz zur Herkunft des Namens: die ersten zwei Buchstaben „OS“ sind die Anfangsbuchstaben des Open Shuttles, und CAR für Open Shuttle Car. Daher OSCAR. Wenn wir bei uns im Haus vom Open Shuttle sprechen, dann immer vom Oscar. Wir kommen sehr gut klar mit unserem Oscar, er ist technologisch zuverlässig und funktioniert. Natürlich war am Anfang eine gewisse Skepsis seitens des Personals vorhanden. Das hätte ich so gar nicht erwartet, da wir selbst in der Automatisierung tätig sind und effizienzsteigernde Maßnahmen bisher kein Thema waren. Das hat sich aber sehr schnell gelegt und das Personal hat den Nutzen des Open Shuttles erkannt. Darüber hinaus kam bei der Akzeptanz auch noch das freundliche Erscheinungsbild mit den blinkenden Lämpchen z.B. beim Abbiegen hinzu. Oscar wirkt freundlich und ist kein beängstigendes Konstrukt.
Zusammenarbeit auf Augenhöhe
Wie würden Sie die Zusammenarbeit mit KNAPP beschreiben?
Weiland: Die Zusammenarbeit ist professionell und vertrauensvoll. Falls es Probleme gibt, kann man bei KNAPP immer nachfragen und man findet gemeinsam eine Lösung. Wir fühlen uns sehr gut betreut, auch serviceseitig.
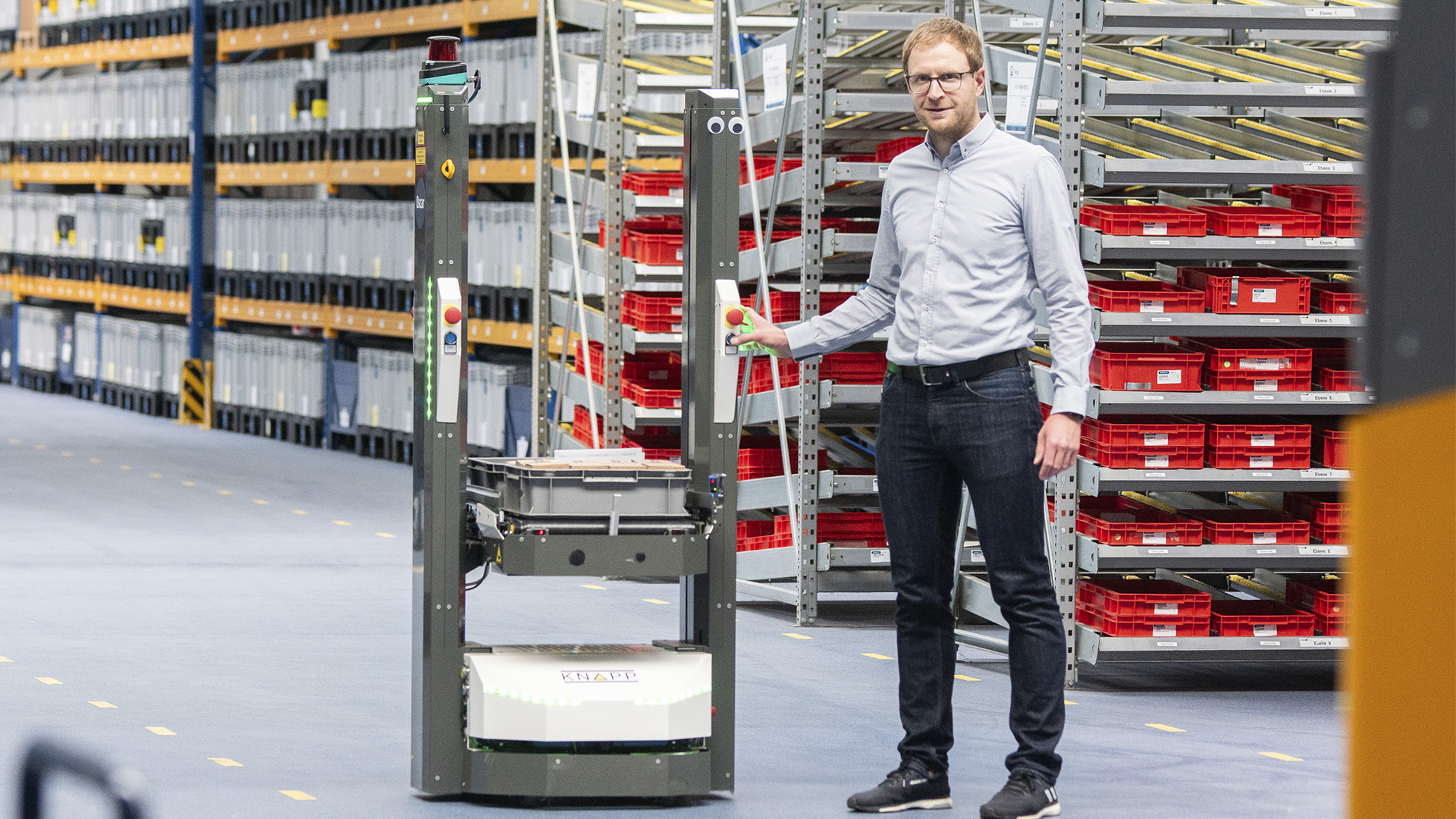
„Unser mobiler Roboter, den wir intern ‚Oscar‘ nennen, erledigt zuverlässig seine Aufgaben. Mit KNAPP erleben wir eine professionelle, partnerschaftliche Zusammenarbeit auf Augenhöhe. Wir fühlen uns hervorragend betreut.“
Sind weitere Automatisierungsschritte für die Zukunft geplant?
Weiland: Wir haben am Standort Brackenheim-Hausen mit einem Open-Shuttle-Projekt gestartet und wollen langfristig an weiteren Standorten Vorteile aus dem Einsatz der AMR generieren. Oscar war unser Startprojekt, da wir am Anfang nicht einschätzen konnten, wie ausgelastet er sein würde. Wir waren nicht sicher, wie schnell er fahren kann und wie er sich auf den Werksverkehr auswirkt. Wir sind mit dem Leistungsdurchsatz jetzt sehr zufrieden. Oscar soll auf Dauer nicht alleine bleiben und weibliche Verstärkung bekommen. Das ist aber erst für Jahresende bzw. Anfang kommenden Jahres geplant. Namen haben wir noch keinen, aber ich bin offen für Vorschläge.
Weiterführende Leseempfehlungen

Autonome mobile Roboter (AMR) ermöglichen flexible und effiziente Transportprozesse. Ob in der Fertigungsindustrie, im Lebensmittelhandel oder in der Distributionslogistik – die Einsatzgebiete sind vielfältig. Erfahren Sie mehr über die zukunftsweisende Technologie.

Platzsparend, flexibel und anpassbar – so sollte die neue Automatisierungslösung von PC Electric sein. Mit dem FTS von KNAPP wurde man fündig. Erfahren Sie mehr über die Entwicklungszusammenarbeit und das Leuchtturmprojekt im Interview.
