B&R : la logistique intelligente au service de l’efficacité dans l’approvisionnement de la production
B&R Industrial Automation GmbH est leader international dans le domaine des solutions d’automatisation et constitue le centre international de l’automatisation de machines et d’usines au sein du groupe ABB. Avec un portefeuille complet de robotique, de technique de commande et de logiciels, l’entreprise développe des solutions de fabrication efficaces et viables. Son siège à Eggelsberg, en Autriche, réunit production, recherche et développement ainsi qu’un centre de formation et compte parmi les plus grands centres industriels d’Europe centrale.
Les processus logistiques du site d’Eggelsberg se distinguent par une forte dynamicité et des exigences changeantes. Afin de réagir avec souplesse aux exigences du nouvel entrepôt intelligent, de réduire la contrainte physique pour les employés et d’augmenter l’efficacité, B&R a opté pour l’automatisation des processus de production et de stockage.
Vous êtes actuellement en train de consulter le contenu d'un espace réservé de YouTube. Pour accéder au contenu réel, cliquez sur le bouton ci-dessous. Veuillez noter que ce faisant, des données seront partagées avec des providers tiers.
Plus d'informationsDe l’entrepôt à la production, de la réception des marchandises aux livraisons sortantes. L’automatisation nous permet de réagir avec plus de rapidité et de flexibilité tout en gagnant en efficacité et en productivité.
Michael Humer
Country Managing Director Sales Austria
B&R Industrial Automation
L’automatisation d’entrepôt vous intéresse aussi ?
Faites-vous conseiller par nos experts et expertes !
Efficacité, ergonomie et flexibilité grâce à l’automatisation d’entrepôt
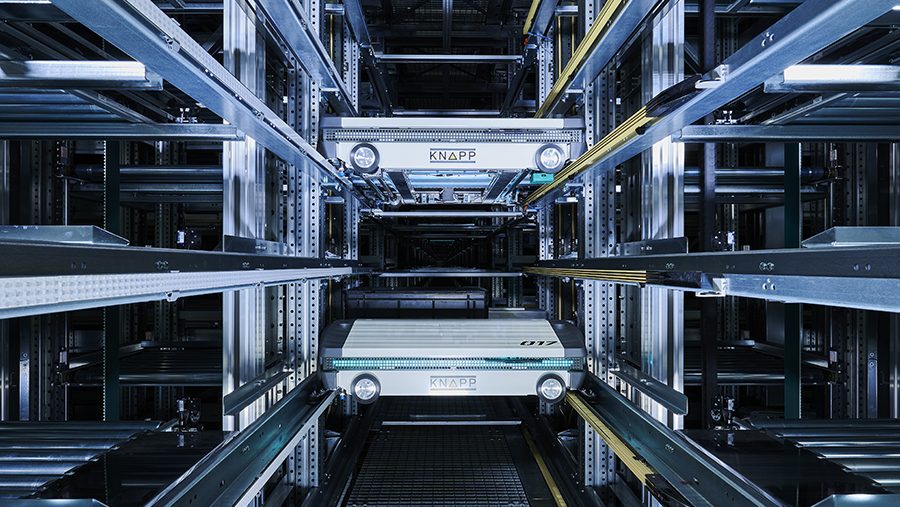
Solution logistique innovante pour B&R
La nouvelle solution d’automatisation se démarque par sa densité de stockage maximale, son prélèvement produit-vers-l’homme hautement efficace et ses transports de marchandises flexibles. Le système de stockage et de récupération automatisé Evo Shuttle, qui offre une structure de stockage de haute densité, constitue le cœur de l’installation. Des postes de travail produit-vers-l’homme de la série Pick-it-Easy sont directement reliés au système et permettent un prélèvement ergonomique grâce à la technologie Pick-to-Light. Les postes de travail de reconditionnement dans les zones d’entrée et de sortie des marchandises sont reliées au système de navettes par des convoyeurs. Les Open Shuttle, nos robots mobiles autonomes (AMR), ainsi que les trains logistiques assurent entièrement l’approvisionnement de la production. Une solution logicielle sur mesure, composée de KiSoft One pour la mise en réseau des processus, KiSoft SCADA pour la visualisation et KiSoft FCS pour le contrôle de la flotte, complètent la solution intégrale.
Les chiffres parlent d’eux-mêmes : grâce à la densité de stockage plus élevée et aux temps d’accès raccourcis, le débit de l’entrepôt a augmenté de 35 % et la cadence de prélèvement de 50 %.
Nous nous sommes décidés pour la solution d’automatisation de KNAPP car elle permet une nette augmentation de la performance, grâce à une densité de stockage plus élevée, des temps d’accès réduits et un rendement plus important.
Roman Seitweger
Head of Production Austria
B&R Industrial Automation
Processus fluides pour l’approvisionnement de la production
01 Entrée des marchandises
Les marchandises sont livrées sur palettes. Elles sont dépalettisées et mises en conteneurs aux stations de reconditionnement ergonomiques. Elles sont ensuite saisies dans le système, pesées par une balance intégrée puis transférées sur un convoyeur. Le système de convoyage est monté au plafond de l’entrepôt et transporte les conteneurs dans le système de stockage et de récupération automatisé. L’espace au sol de l’entrepôt reste disponible grâce au système de convoyage monté au plafond.
02 Stockage
L’Evo Shuttle offre un stockage dynamique et précis des pièces de petite taille. Le système met 91 622 emplacements de stockage à disposition, pour des conteneurs de trois hauteurs différentes. Les conteneurs les moins hauts sont stockés empilés, pour une densité de stockage optimale. Pour cela, une station d’empilage et de dépilage équipée d’une technologie de mesure a été spécialement développée et intégrée à la solution. Elle assure l’empilage des conteneurs avant l’entrée en stock et leur dépilage après la sortie du stock.
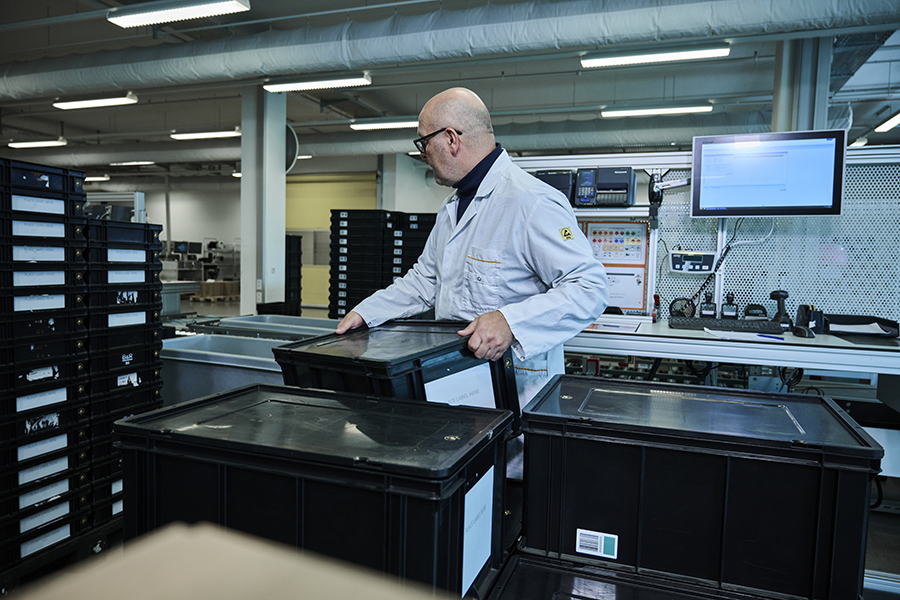
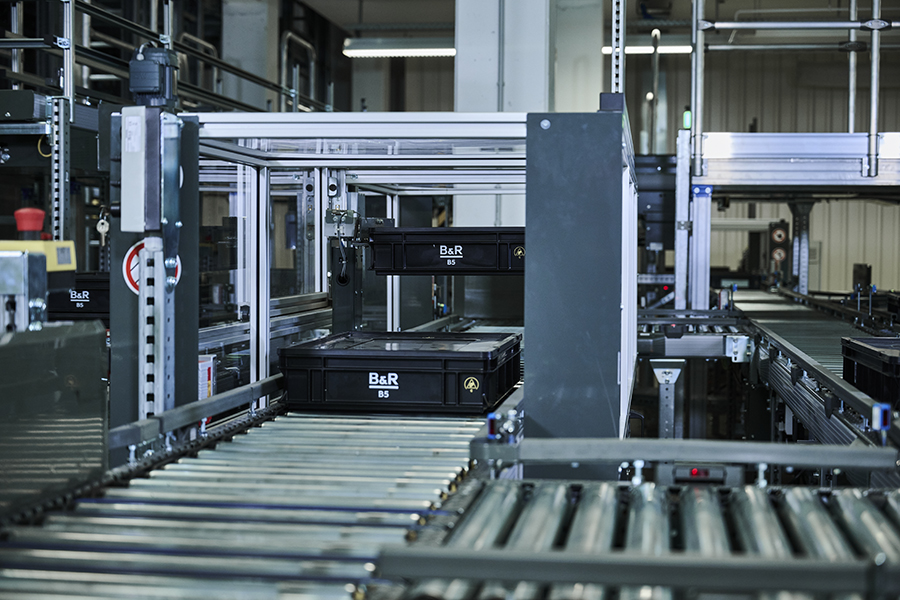
03 Prélèvement
Les marchandises destinées à la production et à l’expédition sont prélevées à quatre postes de travail ergonomiques de la série Pick-it-Easy. Les composants requis sont sortis du système de navettes et acheminés aux postes de travail selon le principe du produit-vers-l’homme. Des kits sont ainsi préparés pour la production, et les commandes pour l’expédition. Celles-ci sont ensuite stockées temporairement dans l’Evo Shuttle. Le processus de prélèvement se base sur des rayonnages kanban dotés d’afficheurs Pick-to-Light pour les composants à forte rotation.
04 Sortie du stock
Une fois la commande d’expédition ou de préparation pour production terminée, les conteneurs sont acheminés hors de l’Evo Shuttle par un système de convoyage. Les commandes sont traitées par les employés et placées sur les palettes correspondantes. Celles-ci sont ensuite récupérées par des trains logistiques. Les conteneurs de composants destinés à la production sont mis à disposition sur les points de transfert aux Open Shuttle. Les robots mobiles autonomes reçoivent alors automatiquement une commande de transport via le logiciel.
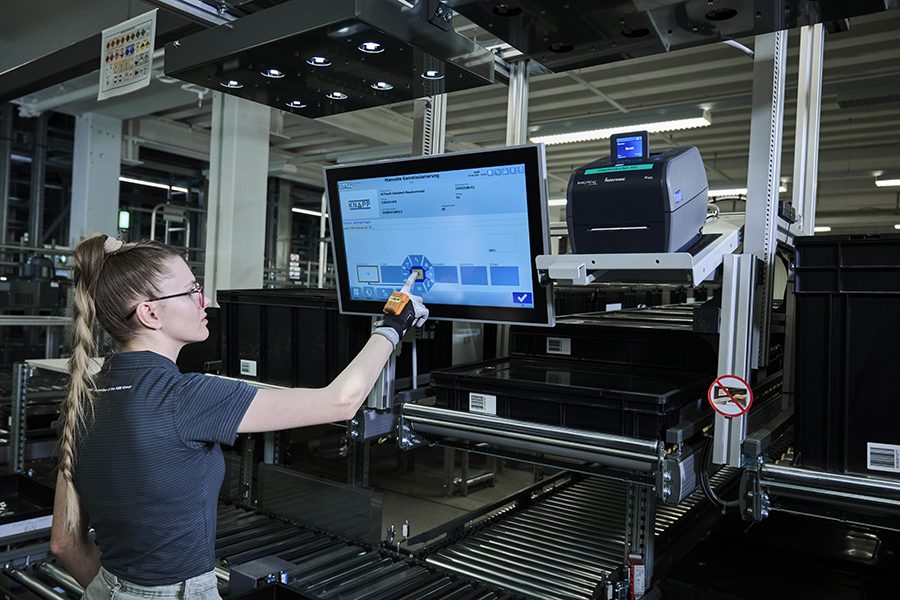
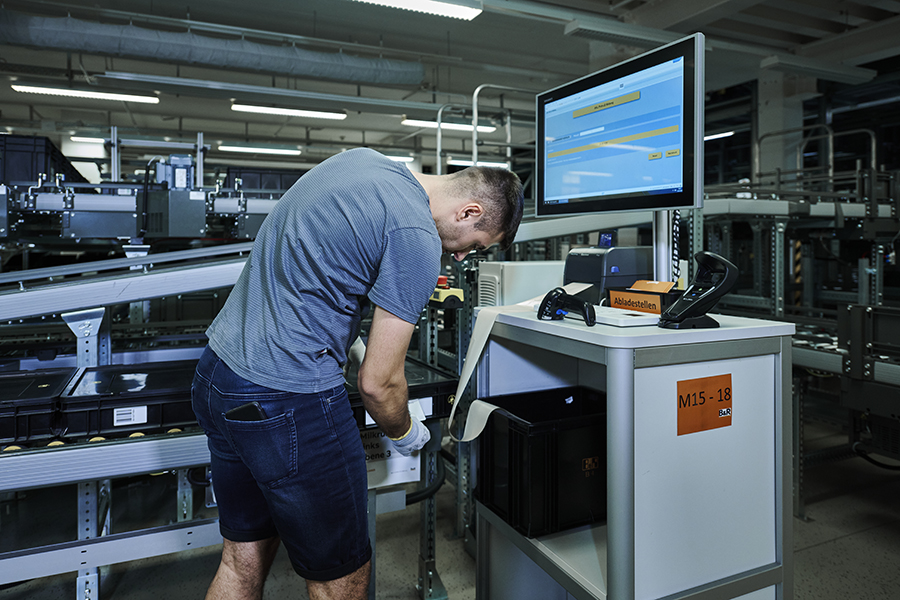
05 Approvisionnement de la production
Les trains logistiques et les Open Shuttle relient le système de stockage et de récupération automatisé aux lignes de production. Les conteneurs de composants sont transportés dans la zone de production par les AMR, puis mis à disposition sur un système de convoyage par des employés. Les Open Shuttle récupèrent ensuite les conteneurs vides ainsi que les pièces produites et les ramènent dans l’Evo Shuttle pour leur stockage temporaire.
06 Expédition
Les trains logistiques récupèrent les palettes de conteneurs préparés du système de stockage pour petites pièces et les transportent à la zone de conditionnement. Les commandes préparées y sont conditionnées dans des cartons avant d’être expédiées. Les conteneurs vides sont ensuite ramenés et entrés en stock dans le système de navettes.
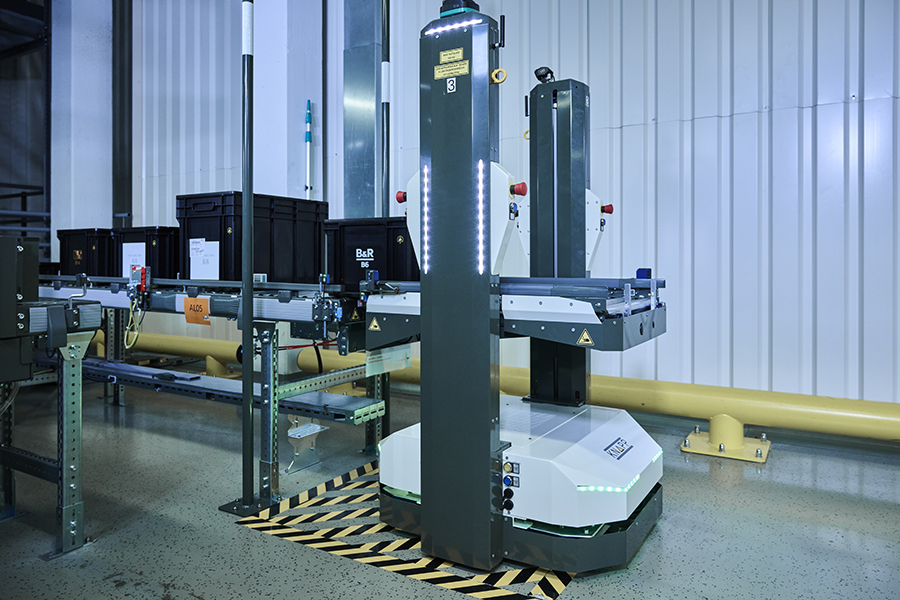
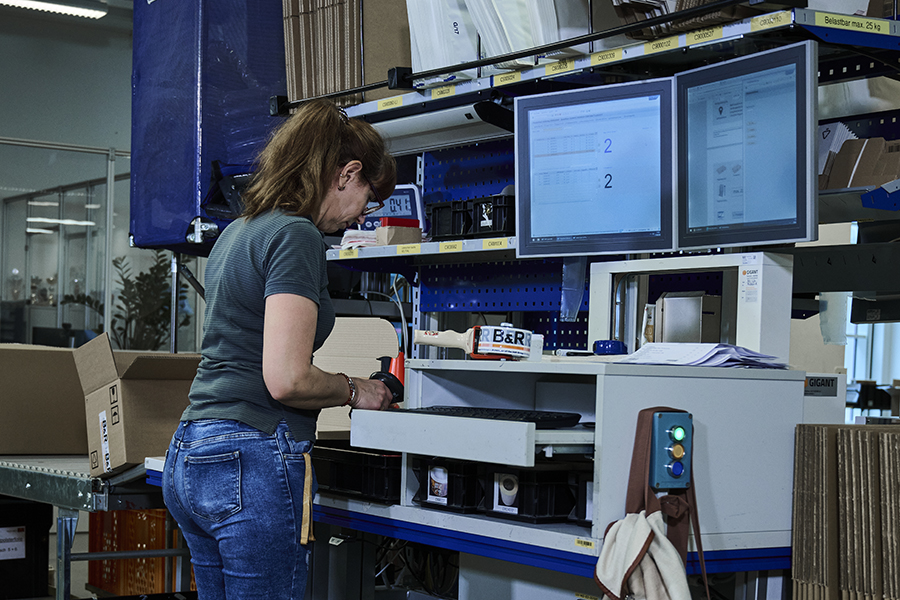
emplacements de stockage
navettes
entrées et sorties du stock par heure
lignes de commande de prélèvement par jour
Smart Factory avec logiciels intelligents et services complets
B&R et KNAPP : des partenaires solides pour des solutions innovantes
Ce qui était initialement une simple relation fournisseur-client s’est développé pour devenir un partenariat stratégique. Alors que notre installation logistique ultramoderne est exploitée au site d’Eggelsberg, nos robots mobiles autonomes fonctionnent avec des systèmes de commande signés B&R. Cette réciprocité souligne les compétences technologiques de nos deux entreprises et prouve que cet échange de savoir-faire mène au succès. À l’avenir, ce partenariat doit encore être renforcé, notamment avec l’intégration de processus associés dans la solution d’automatisation.
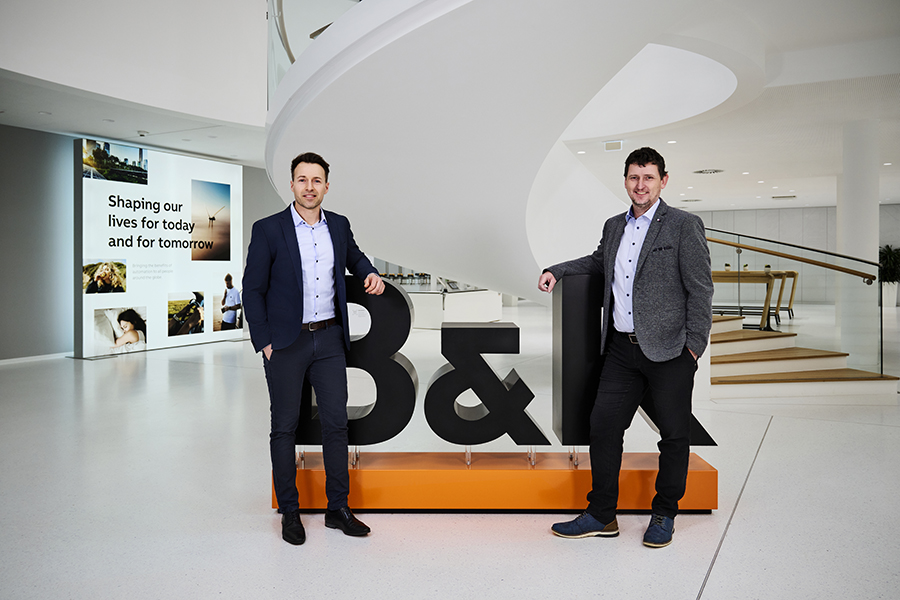
L’intralogistique automatisée s’est révélée être un véritable moteur pour l’efficacité. Il s’agit maintenant d’intégrer des processus associés tels que le pilotage et la planification de la production, le réapprovisionnement ou encore le conditionnement.
Michael Humer
Country Managing Director Sales Austria
B&R Industrial Automation