AutoPocket fait passer le centre de distribution « Elmsall Drive » au Next level
Next plc est connu comme le leader britannique de la mode haut de gamme pour femmes, hommes et enfants, ainsi que pour ses articles d’ameublement et de beauté modernes. Les marchandises de Next et de sociétés tierces sont proposées à la fois dans plus de 500 magasins en Grande-Bretagne et en Irlande et dans le commerce en ligne, qui connaît une forte croissance. Au niveau international, le groupe est présent avec environ 200 boutiques et sur Internet. Via sa plateforme en ligne, Next peut offrir un vaste assortiment et satisfaire à la demande de quelque 8,6 millions de clients dans le monde qui recherchent une plus grande diversité des produits.
« Let’s take it on » est la devise de Next plc qui se retrouve dans tous les domaines de l’entreprise. Employant près de 45 000 personnes, l’entreprise ne cesse de développer ses produits et ses processus. Next s’est spécialisé il y a de nombreuses années déjà dans le traitement rapide des commandes clients et a été un précurseur en proposant la « livraison le lendemain » pour les commandes arrivant avant 23 heures la veille. Seule une conception logistique sophistiquée et rentable permet d’offrir ce service aux clients.
15 000 articles par heure
Vous êtes actuellement en train de consulter le contenu d'un espace réservé de YouTube. Pour accéder au contenu réel, cliquez sur le bouton ci-dessous. Veuillez noter que ce faisant, des données seront partagées avec des providers tiers.
Plus d'informationsModernisation au plus haut niveau
Ces dernières années, Next plc a connu un développement rapide. Nouveaux domaines d’activité, canaux de vente en expansion, exigences accrues et demandes croissantes sur le marché du commerce électronique. Next avait donc pour objectif d’améliorer son efficacité dans l’entrepôt et d’économiser du personnel et a par conséquent décidé d’augmenter l’efficacité de son installation existante dans le centre de distribution « Elmsall Drive ». « Split Tray » est devenu « AutoPocket » : la solution est conçue spécialement pour simplifier les exigences complexes des entrepôts ayant un débit important et raccourcir les temps de traitement des commandes clients. Cela garantit une livraison rapide et facile aux clients finaux.
Le plus grand défi pour notre équipe était d’intégrer le système dans l’infrastructure déjà existante du centre de distribution. Next a confiance dans le caractère innovant de la technologie et s’appuie sur la vaste expérience de projets de KNAPP.
Objectifs de Next plc en bref
« Avec notre AutoPocket, la nouvelle génération de trieurs à pochettes, nous pouvons réduire considérablement la durée de parcours des commandes. Je suis ravi que cette solution innovante du groupe KNAPP contribue grandement au développement futur de Next ».
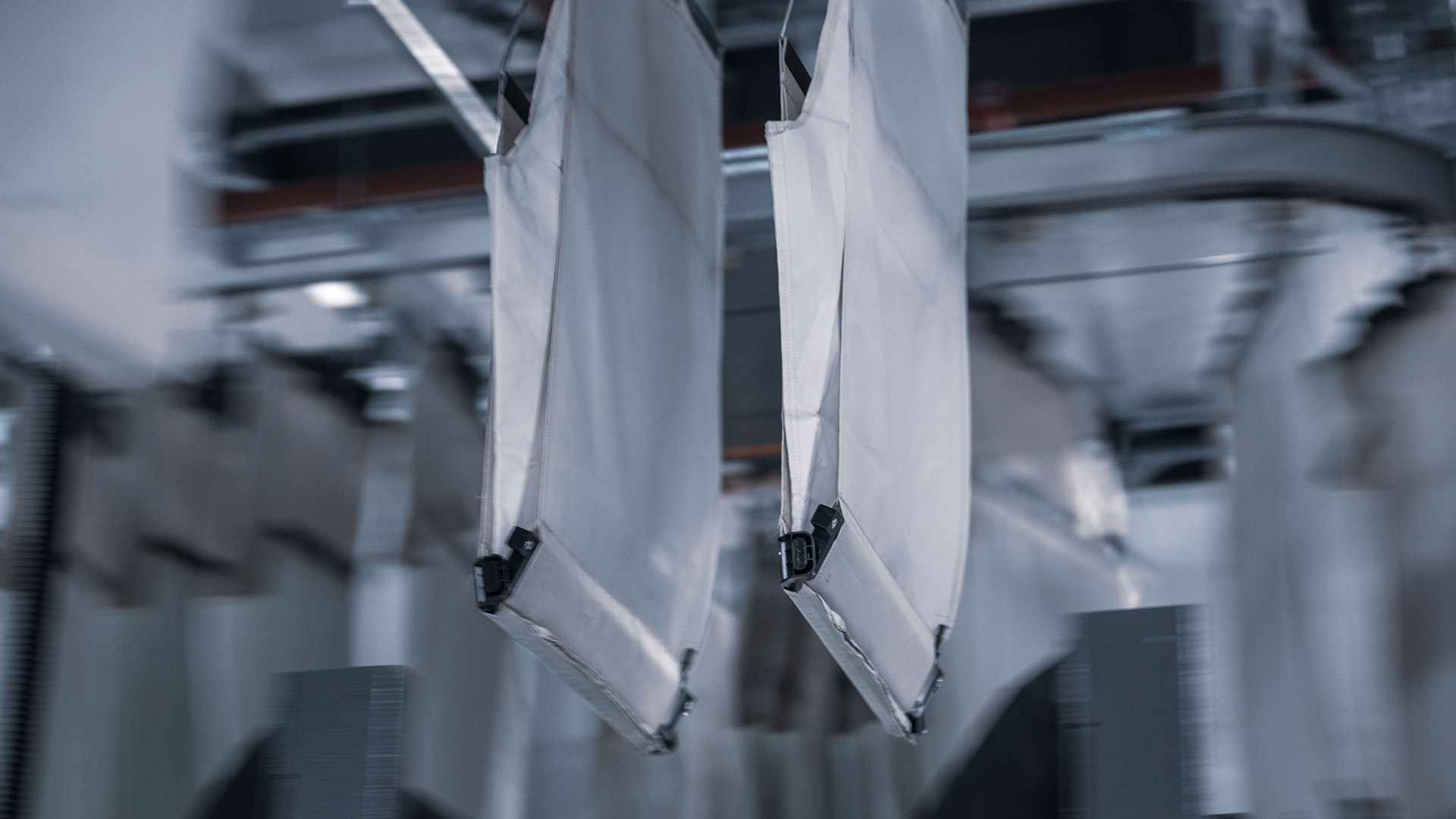
1 pochette pour 2 cas d’utilisation : traitement des commandes et tri des marchandises sortantes
Chez Next, notre AutoPocket trouve 2 applications en même temps : 2 modules AutoPocket sont utilisés pour une consolidation et un tri hautement efficaces des commandes e-commerce, tandis qu’1 autre module sert également de trieur répartiteur pour la sortie des marchandises. La combinaison du trieur AutoPocket et du logiciel intelligent répond aux exigences de rendement élevées de Next et optimise le flux de marchandises de la préparation des commandes à l’expédition.
Gestion de 240 000 articles par jour : aperçu de la solution
Le centre de distribution modernisé « Elmsall Drive » est en service depuis 2022. Depuis ce site, Next livre ses clients dans le monde entier. Quel chemin les quelque 240 000 produits parcourent-ils chaque jour de la préparation des commandes à l’expédition ? Regardons la solution de plus près.
Des conteneurs de prélèvement pleins venant de l’entrepôt sont présentés automatiquement à l’employé au poste de chargement. Aux 10 postes de chargement des pochettes par module, soit 20 en tout, sont prélevés des conteneurs respectivement 750-1 000 produits par heure, les codes-barres sont scannés pour identifier la marchandise puis amenés à la pochette mise à disposition automatiquement.
Du poste de chargement, les pochettes sont transportées au répartiteur modulaire. Ce dernier répartit les pochettes – en fonction de la charge du système – dans les 2 modules AutoPocket. Les deux modules ont en tout une performance de 15 000 articles par heure. Le répartiteur modulaire permet d’équilibrer la charge de travail du système à pochettes, ce qui augmente la flexibilité et le rendement des commandes.
En fonction de la répartition modulaire, les pochettes arrivent ensuite dans le buffer de consolidation des commandes. Dans les 14 buffers par module, soit 28 en tout, les articles individuels sont stockés temporairement sur 2 niveaux, jusqu’à ce que toutes les pièces d’une commande soient disponibles et soient consolidées en une commande. Grâce au système de pilotage de l’entrepôt intelligent (WCS), les commandes terminées sont éjectées automatiquement du système rotatif et transportées vers les boucles d’emballage.
Les commandes sont stockées temporairement en rotation au niveau des 6 boucles d’emballage avec en tout 240 « Packwalls » (panneaux d’emballage) jusqu’à ce qu’elles soient ouvertes automatiquement à pleine vitesse et soient larguées via les glissières. Les articles d’une commande arrivent ensuite à la station d’emballage via les glissières.
Aux 60 postes de travail qui sont approvisionnés à l’aide de 240 glissières de dépose, les employés emballent les articles d’une commande dans un polybag. Ces polybags sont ensuite placés sur une voie d’évacuation qui est associée à une nouvelle dépose des marchandises pour leur tri sortant.
Aux 6 postes de chargement, les commandes clients dont l’emballage est terminé sont amenées de nouveau aux pochettes de l’AutoPocket et donc au système de tri des marchandises sortantes. Ce dernier peut traiter jusqu’à 5 000 colis par heure.
Les colis sont directement répartis sur 40 points de dépose orientés vers les services d’expédition via la boucle sortante séparée. C’est à partir de là que commence le transport ultérieur et donc le voyage des colis dans le monde entier.
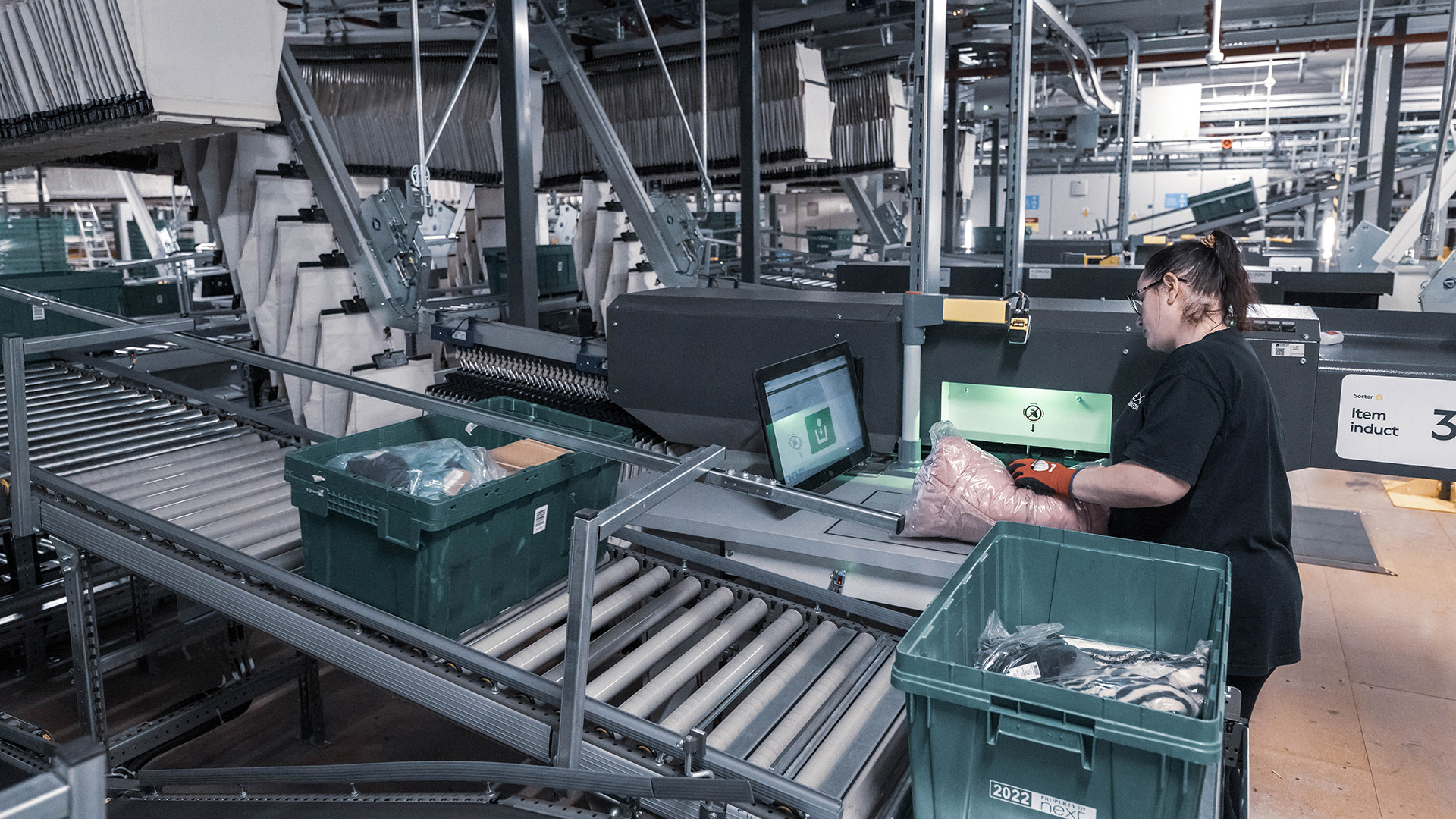
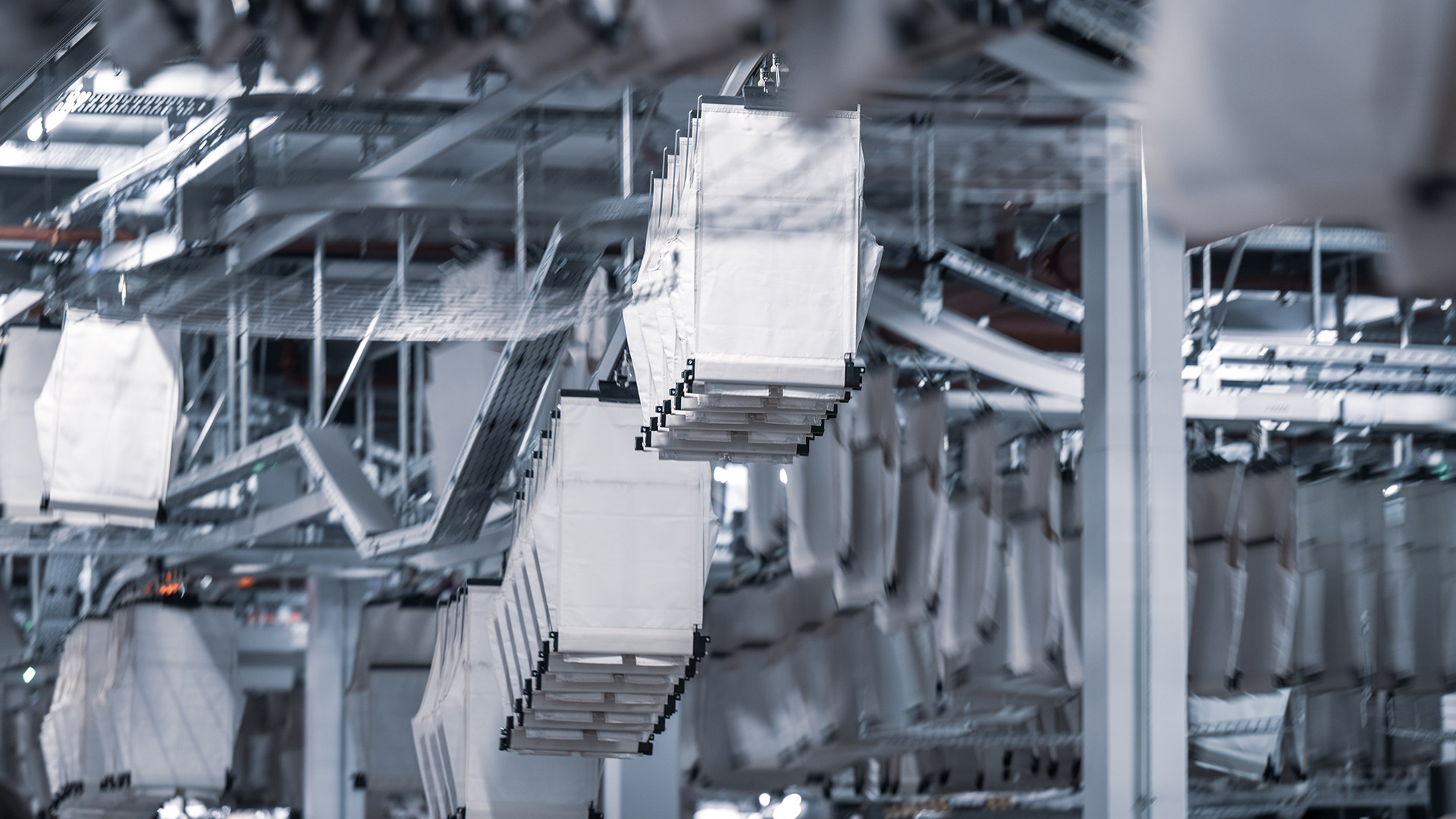
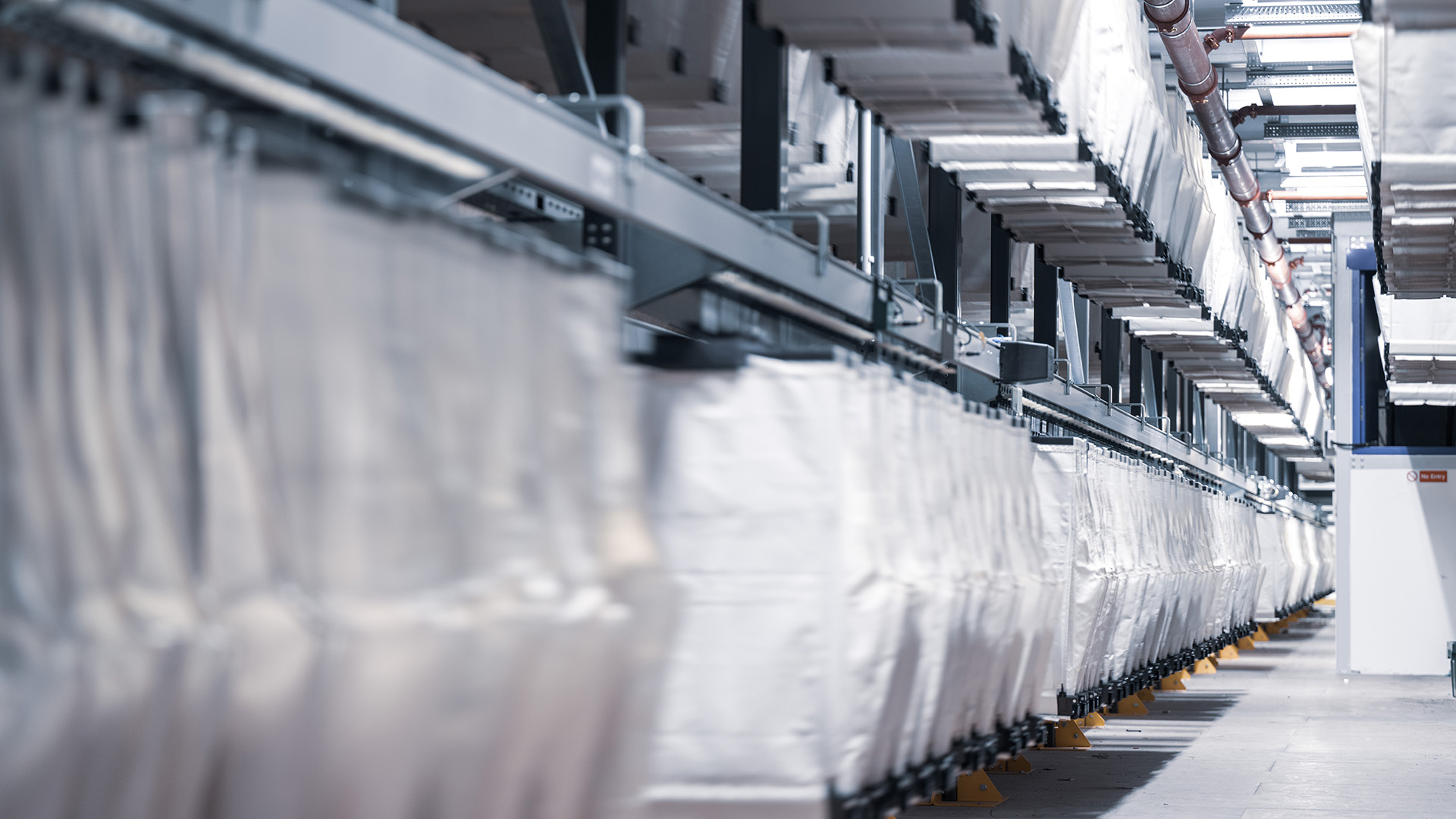
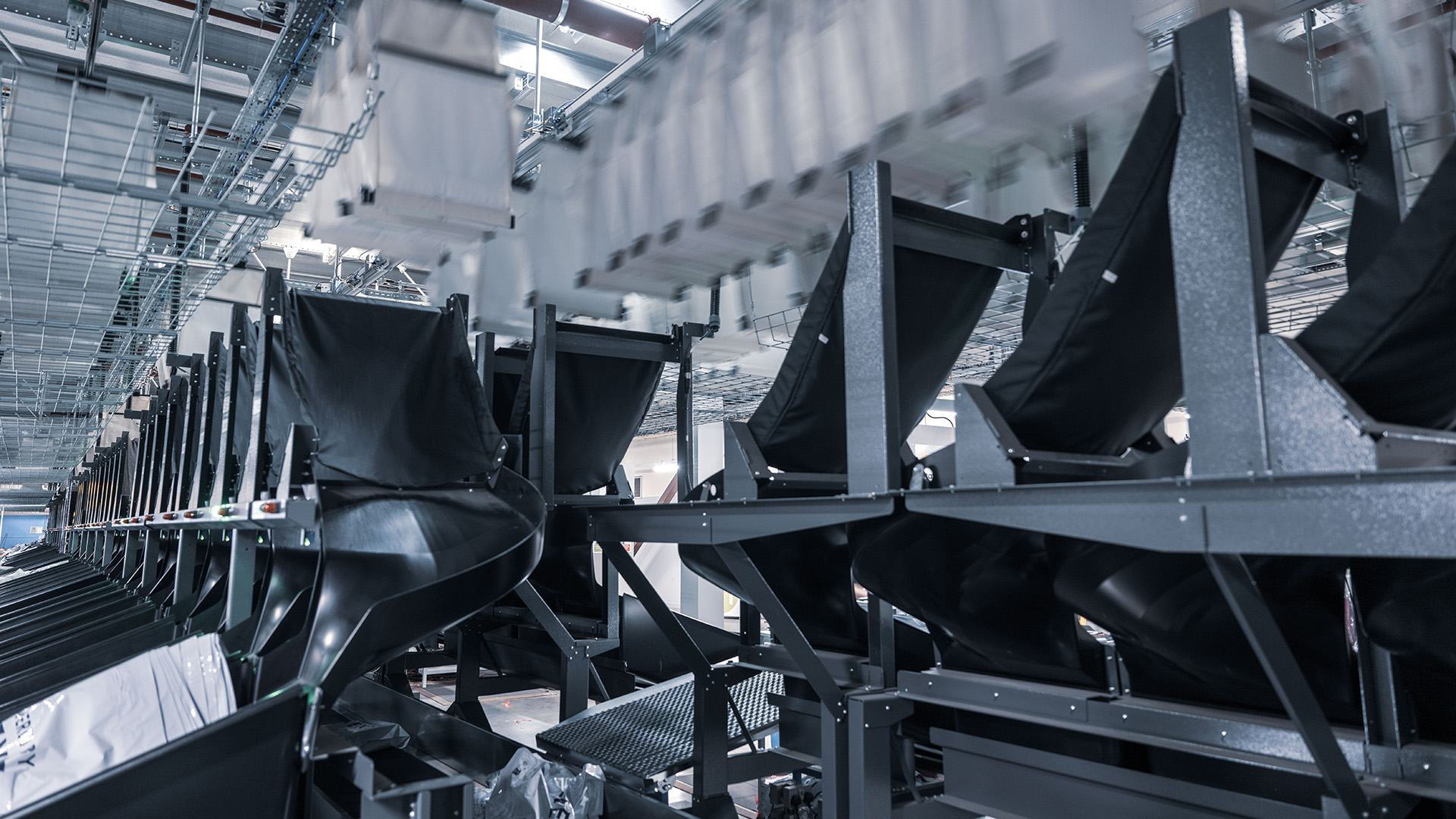
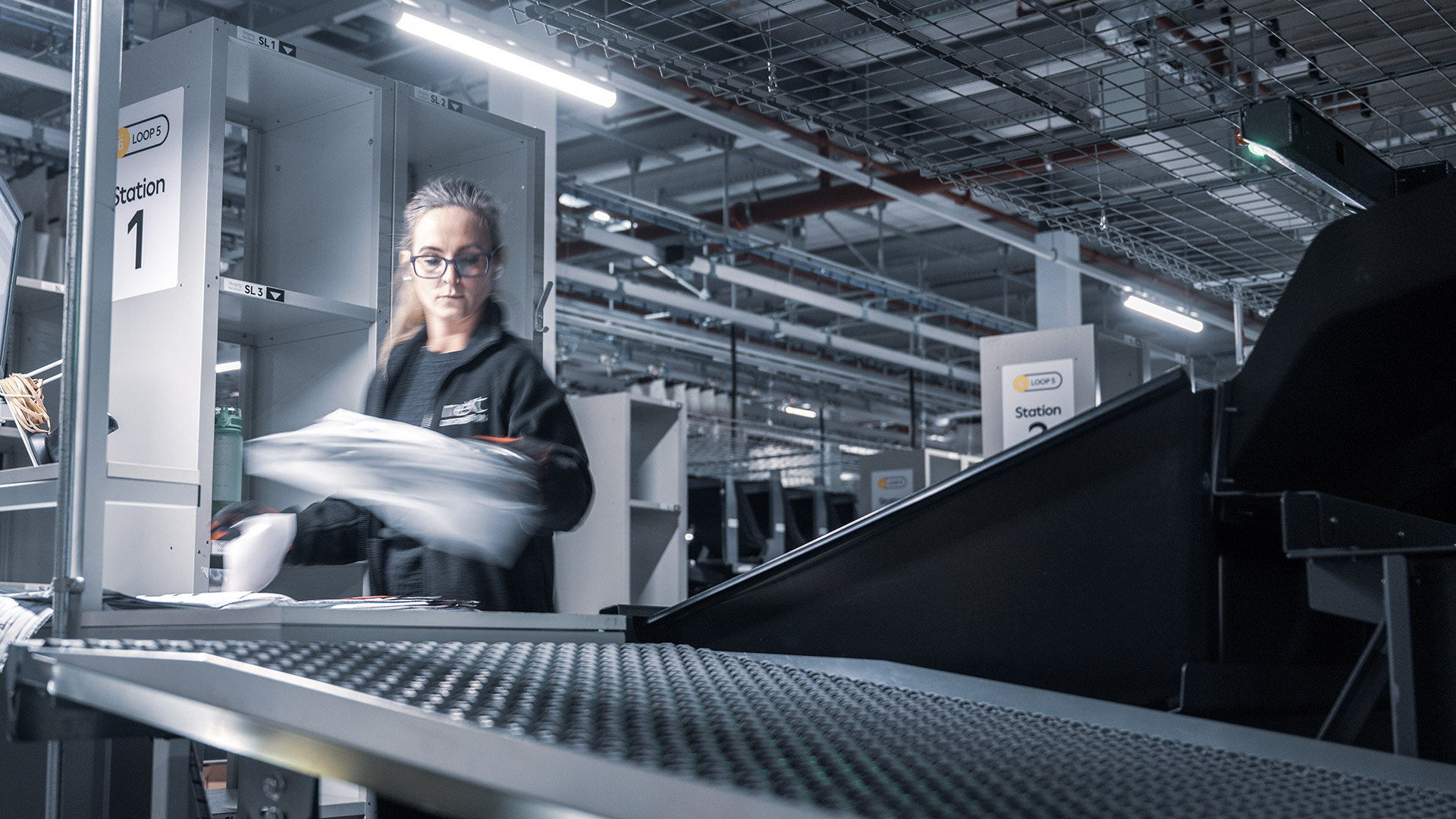
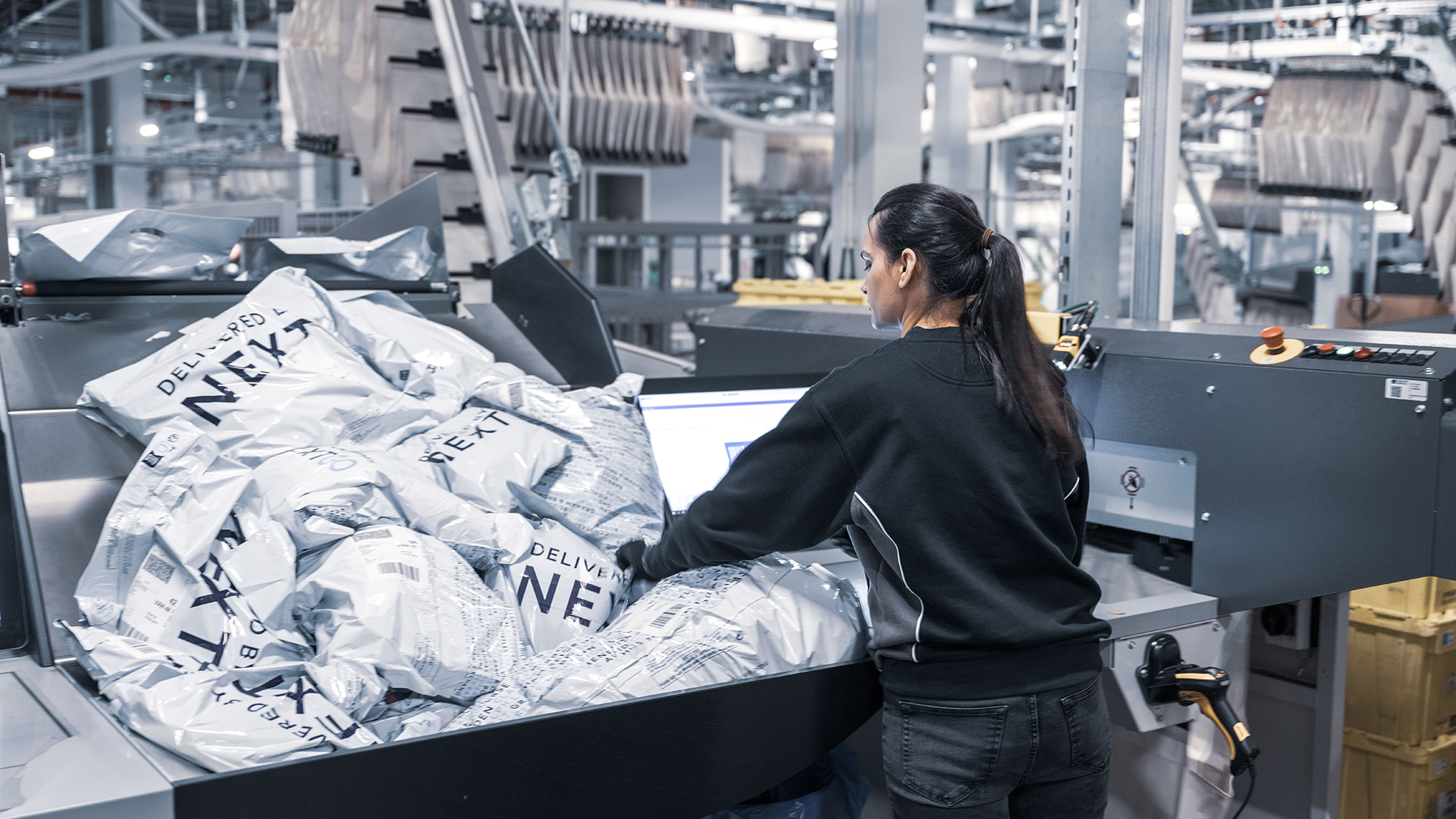
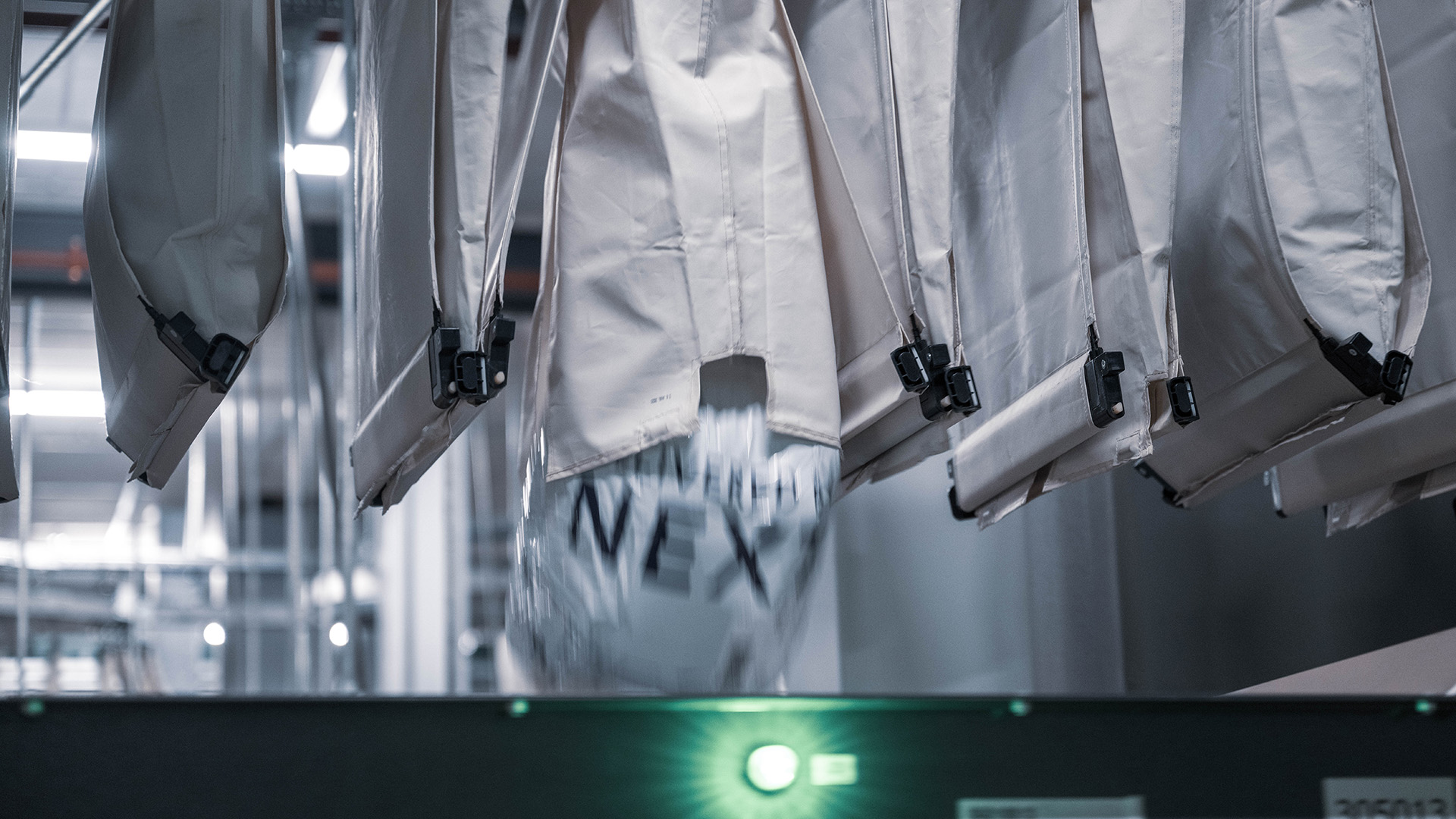
« Notre longue et formidable collaboration avec Next se caractérise par une confiance et une fiabilité mutuelles. Je suis fier que nous ayons de nouveau mené à bien un projet qui nous permettra de continuer à soutenir Next à l’avenir grâce à notre partenariat ».
Résultat : des durées de traitement plus courtes
L’AutoPocket est devenu un élément indispensable du réseau de distribution de Next. Les chiffres parlent d’eux-mêmes : les deux modules AutoPocket utilisés ont une performance de 15 000 articles par heure ; dans le même temps, la technologie AutoPocket est utilisée avec un module séparé pour le tri des marchandises sortantes. Ce module est conçu pour une performance de 5 000 colis par heure. Cela permet des durées de parcours plus courtes du prélèvement à l’expédition. Dans le même temps, Next économise environ 35 % d’heures de travail par semaine par rapport aux trieurs à bandes croisées traditionnels.