AutoPocket hebt das Distributionszentrum
„Elmsall Drive“ auf ein Next Level
Next plc ist bekannt als führender, britischer Anbieter von hochwertiger Damen-, Herren- und Kindermode sowie modernen Einrichtungsartikeln und Beauty. Die Waren von Next und Drittfirmen werden sowohl über 500 Geschäfte in Großbritannien und Irland als auch über den stark wachsenden Online-Handel angeboten. International ist der Konzern mit rund 200 Shops und über das Internet präsent. Über die Next-Online-Plattform kann das Unternehmen ein umfangreiches Sortiment anbieten und die Nachfrage der weltweit rund 8,6 Millionen Kunden nach Produktvielfalt erfüllen.
‚Let’s take it on‚ zieht sich als Leitspruch durch alle Bereiche der Next plc. Mit rund 45.000 Mitarbeiter:innen entwickelt das Unternehmen stetig seine Produkte und Prozesse weiter. Bereits vor Jahren spezialisierte sich Next auf die schnelle Bearbeitung von Kundenaufträgen und war Vorreiter mit der Zusage “Next-Day-Delivery“ für Bestellungen, die bis 23.00 Uhr am Vortag eintreffen. Dieser Service kann den Kunden nur durch ein ausgefeiltes, kosteneffizientes Logistikkonzept ermöglicht werden.
Taschensorter-Module
Sie sehen gerade einen Platzhalterinhalt von YouTube. Um auf den eigentlichen Inhalt zuzugreifen, klicken Sie auf die Schaltfläche unten. Bitte beachten Sie, dass dabei Daten an Drittanbieter weitergegeben werden.
Mehr InformationenModernisierung auf höchstem Niveau
In den letzten Jahren hat sich die Next plc rasant entwickelt. Neue Geschäftsfelder, wachsende Absatzkanäle, erhöhte Anforderungen und steigende Nachfragen im E-Commerce-Markt. Next hatte daher das Ziel seine Effizienz im Lager zu verbessern sowie Personal zu sparen und entschied sich, seine bestehende Anlage im Distributionszentrum „Elmsall Drive“ effizienter zu machen. Aus „Split Tray“ wurde „AutoPocket“: Die Lösung ist speziell darauf ausgelegt, komplexe Anforderungen von Lagern mit hohem Durchsatz zu vereinfachen und die Bearbeitungszeit von Kundenaufträgen zu verkürzen. Damit wird eine reibungslose und rasche Belieferung an den Endkunden gewährleistet.
Die größte Herausforderung für unser Team war die Integration des Systems in die bereits bestehende Infrastruktur des Distributionszentrums. Next vertraut auf den innovativen Charakter der Technologie und baut auf die umfassende Projekterfahrung von KNAPP.
Ziele von Next plc auf einen Blick
Mit unserer AutoPocket, der neuen Taschensorter-Generation, können wir die Durchlaufzeit der Aufträge erheblich reduzieren. Ich freue mich sehr, dass diese innovative Lösung der KNAPP Gruppe einen wichtigen Beitrag in der zukünftigen Entwicklung von Next leistet.
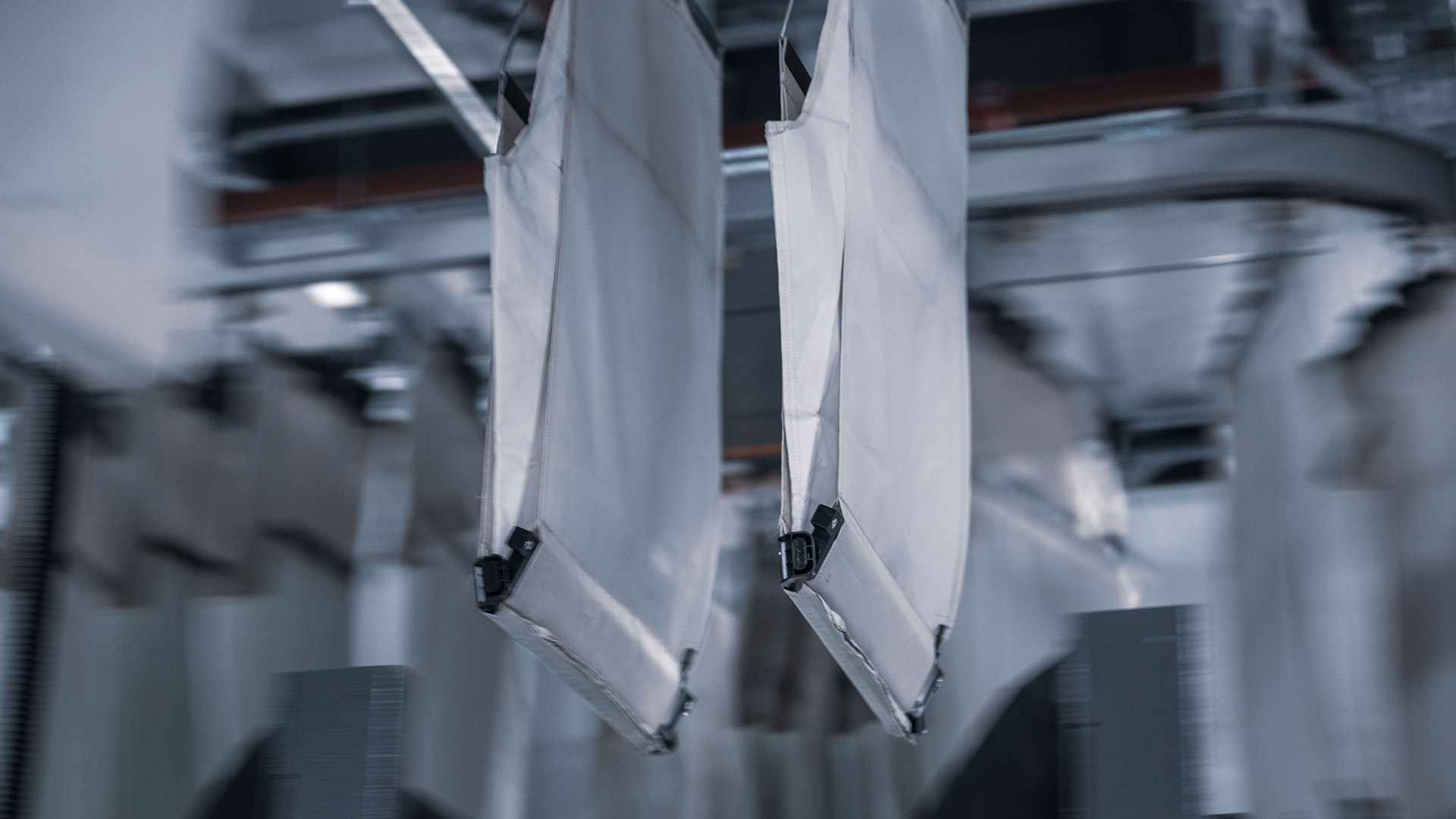
1 Tasche für 2 Fälle: Auftragsbearbeitung und Warenausgangssortierung
Bei Next findet die AutoPocket gleich 2 Anwendungen: 2 AutoPocket-Module werden zur hocheffizienten Konsolidierung und Sortierung von E-Commerce-Aufträgen eingesetzt, während 1 weiteres Modul auch als Warenausgangssorter genutzt wird. Die Kombination der AutoPocket-Sorter mit intelligenter Software erfüllt die hohen Leistungsanforderungen von Next und optimiert den Warenfluss von Kommissionierung bis Versand.
Handhabung von 240.000 Artikeln am Tag:
Einblicke in die Lösung
Das modernisierte Distributionszentrum „Elmsall Drive“ ist seit 2022 in Betrieb. Von hier aus beliefert Next seine Kunden weltweit. Welchen Weg nehmen die rund 240.000 Produkte pro Tag von der Kommissionierung bis zum Versand auf sich? Wir schauen uns die Lösung genauer an.
Dem Mitarbeiter werden am Beladeplatz automatisch volle Kommissionierbehälter aus dem Lager präsentiert. An 2 x 10 Taschen-Beladeplätzen werden je 750-1000 Produkte pro Stunde aus den Behältern entnommen, die Barcodes, zur Identifizierung der Ware, gescannt und der automatisch bereitgestellten Tasche zugeführt.
Vom Beladeplatz gelangen die Taschen zum Modulverteiler. Über diesen werden die Taschen – abhängig von der Systemlast – in die 2 AutoPocket-Module verteilt. Die beiden Module kommen insgesamt auf eine Leistung von 15.000 Artikeln pro Stunde. Der Modulverteiler ermöglicht eine ausgeglichene Auslastung des Taschensystems, was die Flexibilität und den Auftrags-Durchsatz erhöht.
Je nach Modulzuteilung gelangen die Taschen anschließend in den Auftragskonsolidierungspuffer. In 2 x 14 Puffern werden auf 2 Ebenen einzelne Artikel zwischengepuffert, bis alle Teile eines Auftrags vorhanden sind und zu einem Auftrag konsolidiert werden. Fertige Aufträge werden durch das intelligente Warehouse Control System automatisch aus dem rotierenden System ausgeschleust und zu den Packloops transportiert.
An den 6 Packloops mit insgesamt 240 Packwalls werden die Aufträge so lange rotierend gepuffert, bis sie automatisch bei voller Fahrt geöffnet und über Rutschen abgeworfen werden. Über diese gelangen die Artikel eines Auftrags zum Packplatz.
An den 60 Arbeitsplätzen, die über insgesamt 240 Abgaberutschen versorgt werden, verpacken die Mitarbeiter die Artikel eines Auftrags in eine Polybag. Diese werden anschließend auf einen Abzugsförderer gegeben, der mit einer erneuten Aufgabe für die Warenausgangssortierung verbunden ist.
An 6 Beladeplätzen werden die fertig gepackten Kundenaufträge erneut den Taschen der AutoPocket und somit dem Ausgangssortier-System zugeführt. Dieses kann bis zu 5.000 Pakete pro Stunde handhaben.
Die Pakete werden über den separaten Outbound Loop direkt auf 40 versanddienstleister-orientierte Abwurfstellen verteilt. Von dort aus beginnt der Weitertransport und somit die Reise der Pakete um die ganze Welt.
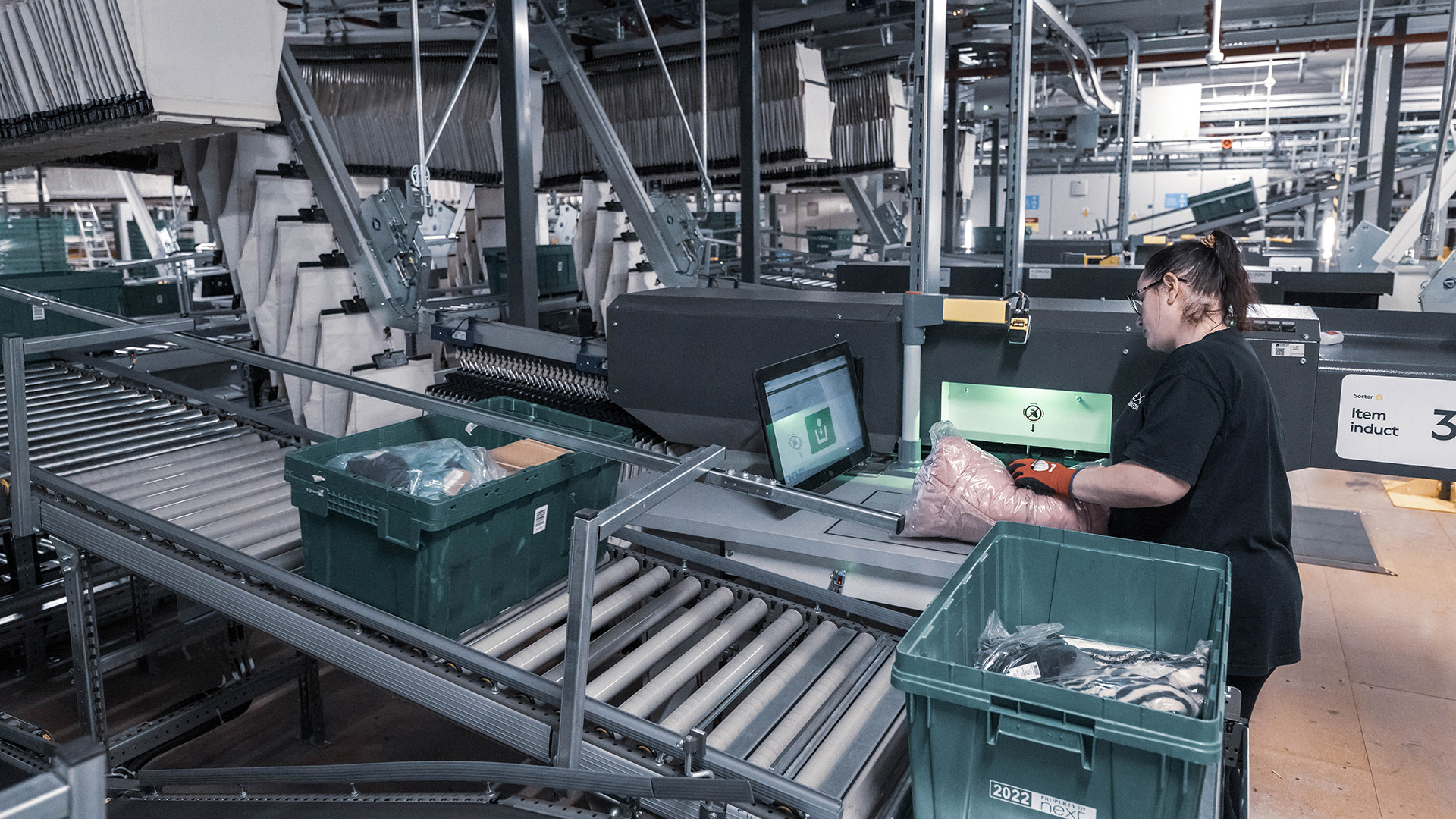
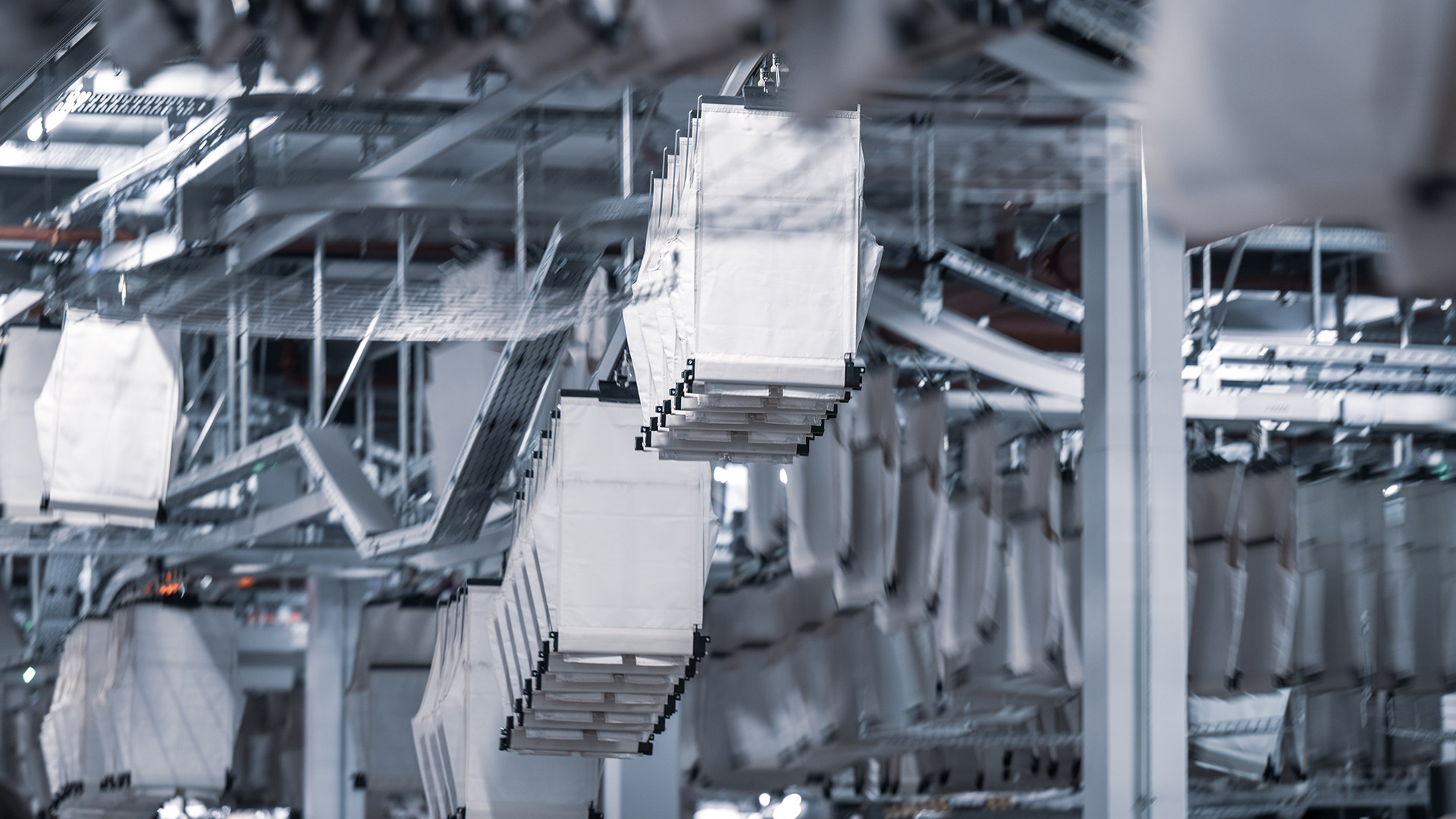
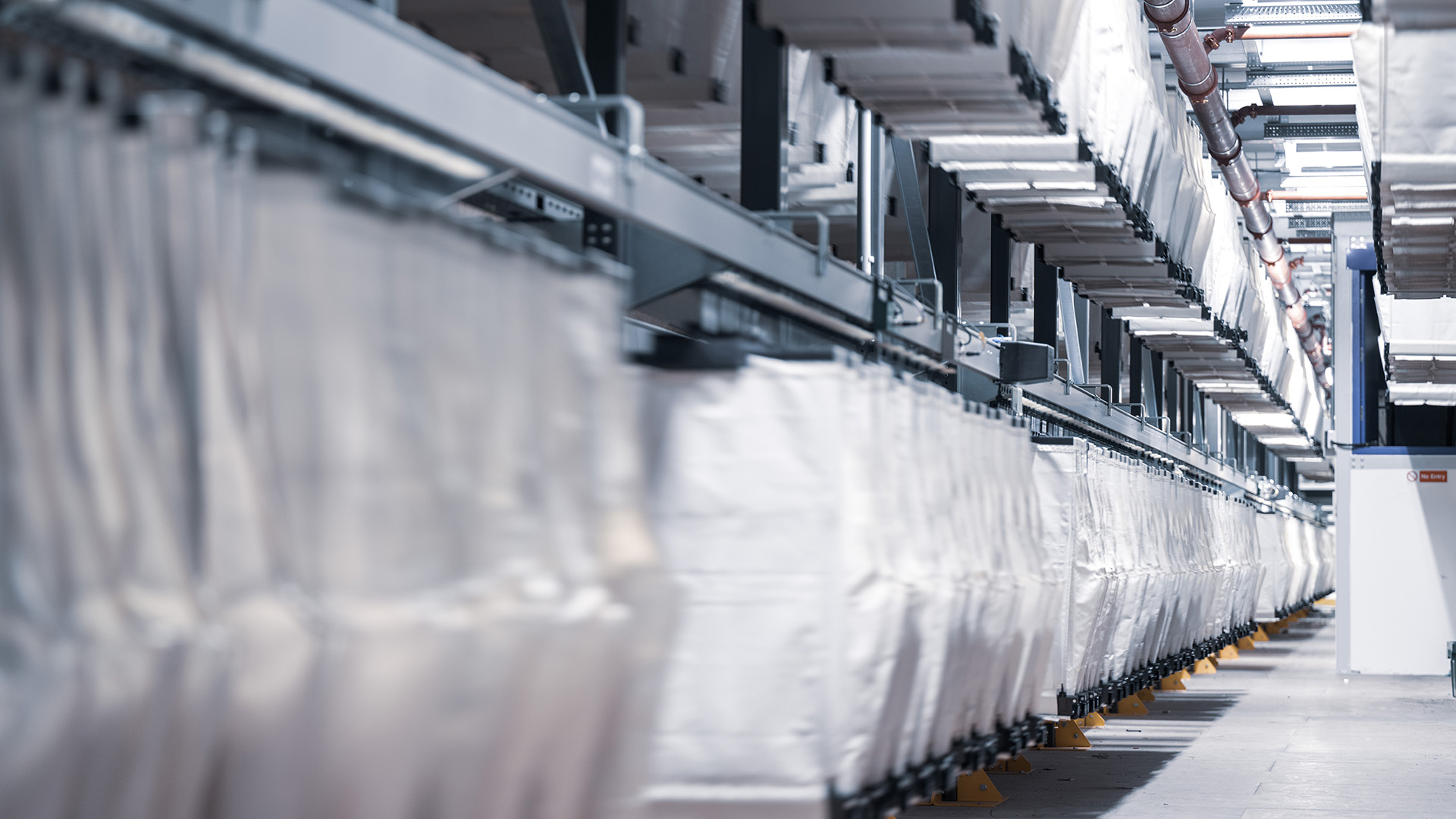
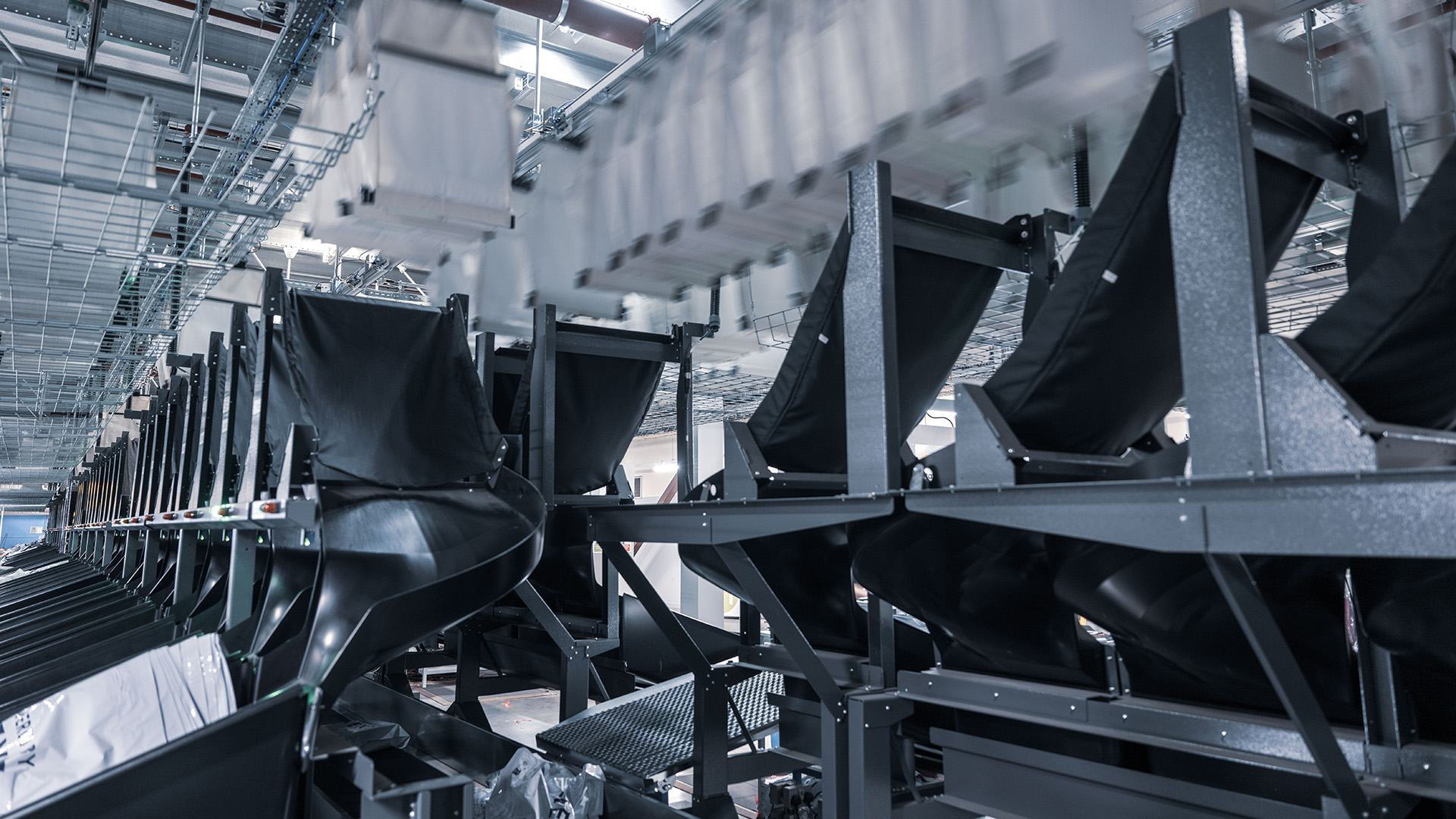
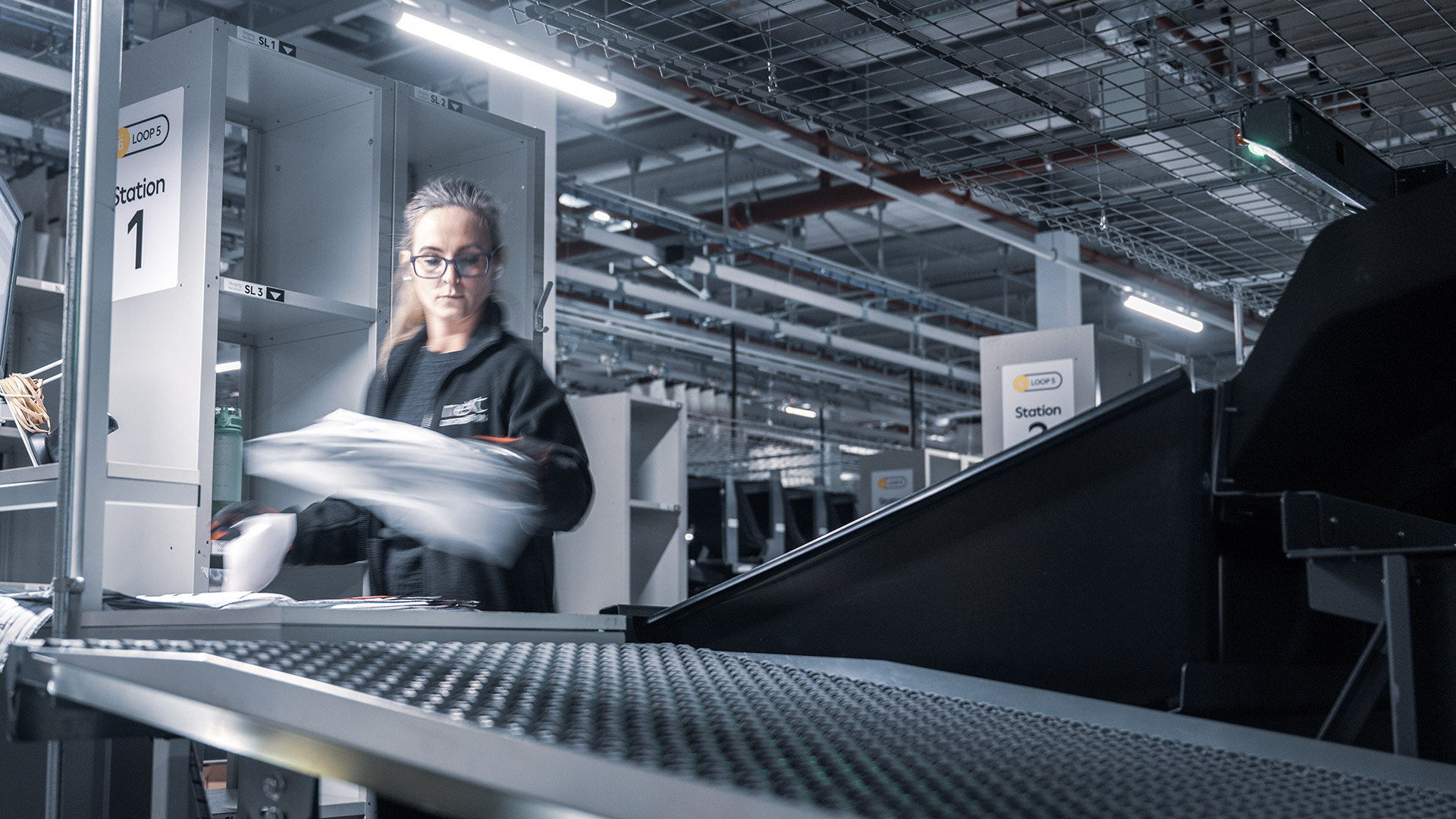
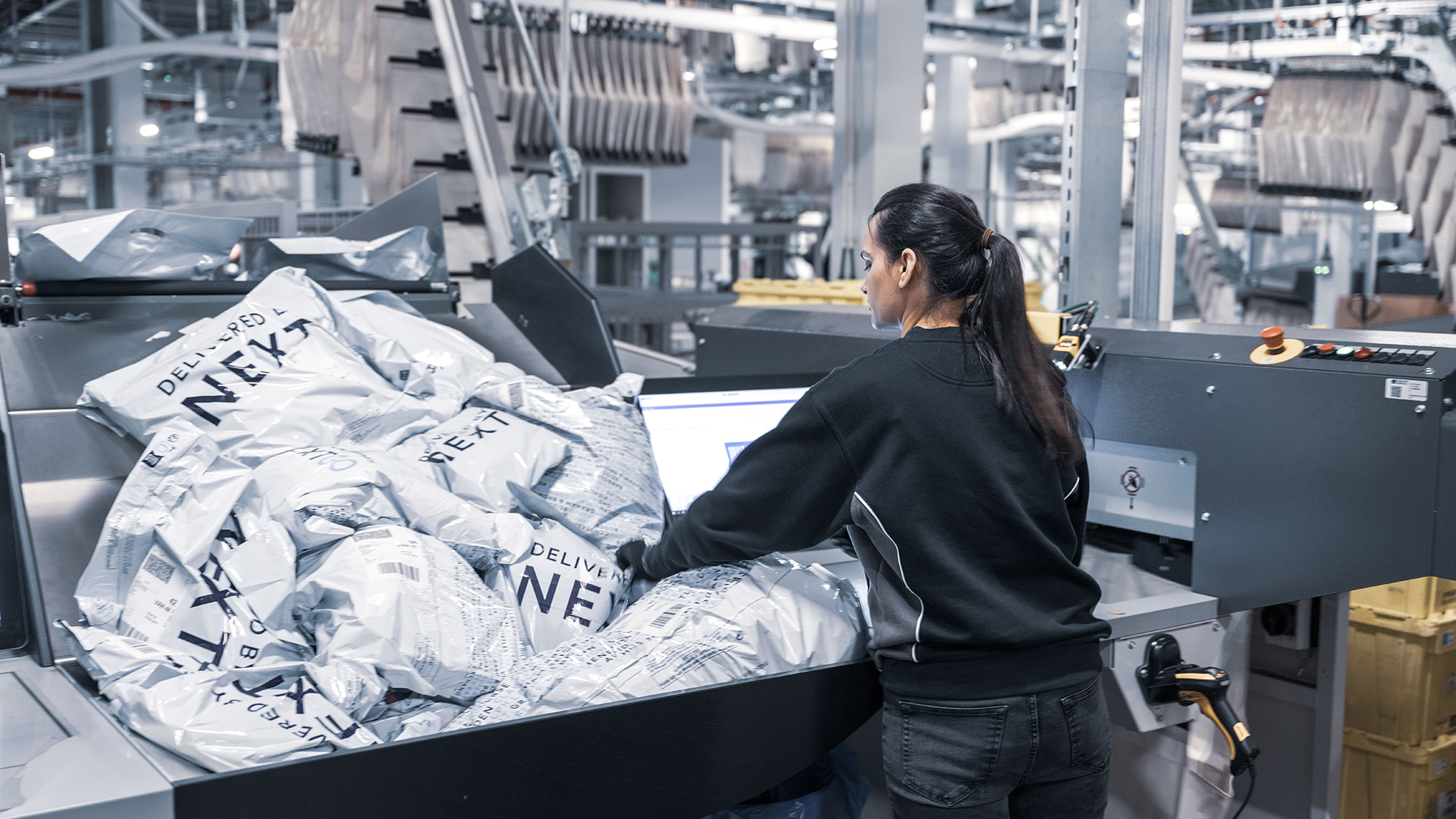
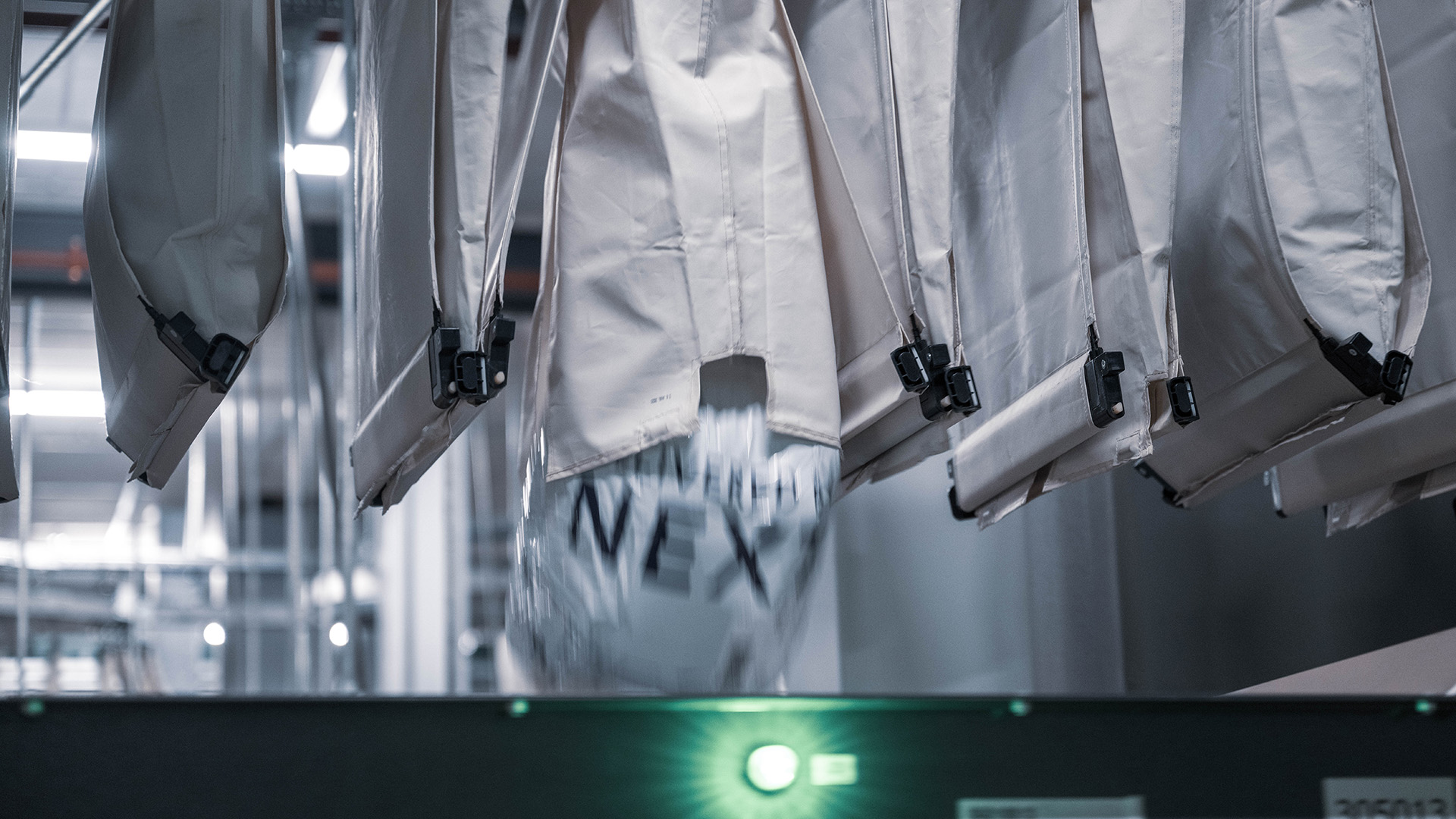
Die langjährige, großartige Zusammenarbeit mit Next ist geprägt von gegenseitigem Vertrauen und Zuverlässigkeit. Es macht mich stolz, dass wir wieder ein Projekt erfolgreich abgeschlossen haben, um Next auch in Zukunft partnerschaftlich unterstützen zu können.
Verkürzte Bearbeitungszeiten als Ergebnis
Die AutoPocket ist mittlerweile ein unentbehrlicher Bestandteil des Distributionsnetzwerks von Next geworden. Die Zahlen sprechen für sich: Die beiden eingesetzten AutoPocket-Module erreichen eine Leistung von 15.000 Artikeln pro Stunde, gleichzeitig wird die AutoPocket Technologie mit einem separaten Modul für die Warenausgangssortierung genutzt. Dieses ist auf eine Leistung von 5.000 Paketen pro Stunde ausgelegt. Dadurch ergeben sich verkürzte Durchlaufzeiten von der Kommissionierung bis zum Versand. Gleichzeitig spart Next ca. 35 % an Personalstunden pro Woche im Vergleich zu traditionellen Cross-Belt-Sortern.