SCHUNK is a global technology partner for workholding, gripping and automation technologies. Around 3,700 employees at ten factories and 34 subsidiaries and sales offices in more than 75 countries throughout the world ensure a strong market presence. The company produces grippers and automation components at their location in Brackenheim-Hausen, Germany. To automate their manual production supply, SCHUNK decided to implement the Open Shuttle. The autonomous mobile robot (AMR) ensures efficient processes and frees employees for value creation.
We spoke with Pascal Weiland, Head of Assembly & Logistics Gripping Technology & Automation Technology at SCHUNK, about the reasons for automating, selecting the Open Shuttle and implementing the new solution.
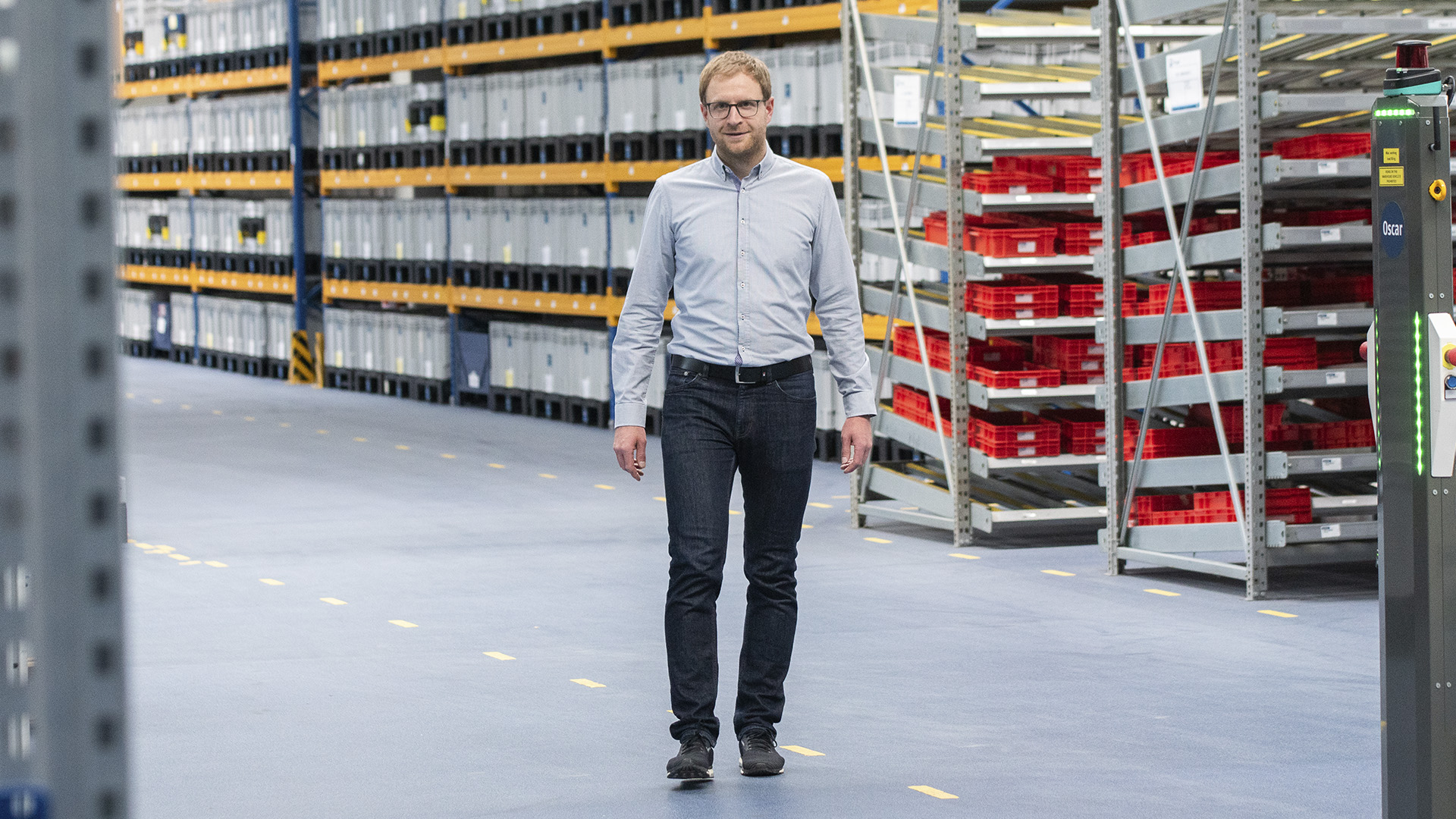
SCHUNK relies on automated mobile robots for process optimization
Why did SCHUNK choose to use autonomous mobile robots at the Brackenheim-Hausen location?
Weiland: Our initial experiences with an automated guided vehicle system was not as successful as we hoped, but we were certain the technology would make a difference, so we decided to give it another try. With KNAPP, we not only found the right partner, but also the right product for gaining valuable experience. These are the reasons we decided to implement an AMR:
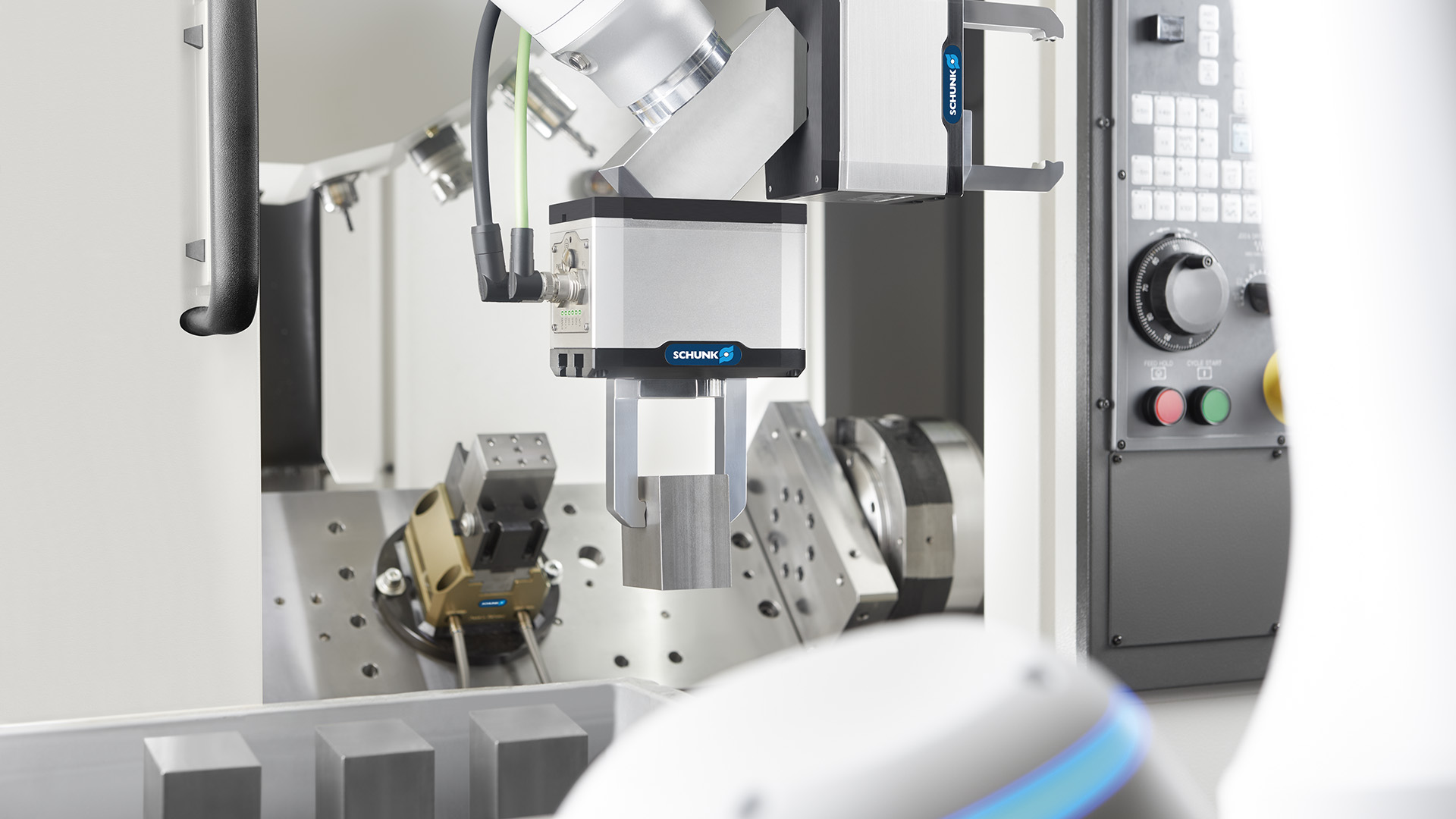
KNAPP – the experienced AMR partner
Why did SCHUNK opt for the Open Shuttle by KNAPP?
Weiland: We have been using the system at SCHUNK since 2016. At the time, KNAPP was the favorite because their system best suited our transport needs. In particular, we were interested in the transport of 300 x 400 mm (12 x 16 in) containers, which KNAPP had as a standard solution. By the time we decided on an AMR system, KNAPP had introduced their integrated lifter, which could access different heights. This had been on our wish list from the very beginning and is why the Open Shuttle matched our requirements better than other options.
Weiland: Having years of experience was also an important factor in our decision. We wanted a technically advanced solution, and we had great confidence in KNAPP.
Weiland: For us, it was important to be able to make changes on our own. This was crucial as SCHUNK is a very flexible, agile company in which changes to processes can be expected. We did not want a solution that would make us dependent on external support when we needed change. We wanted our personnel to be trained to use the AMR solution, giving us the option to make minor adjustments such as changing the location of the transfer stations independently. KNAPP makes it possible for their customers and brought us directly into the setup and startup process, so we got our training in the system right from the start.
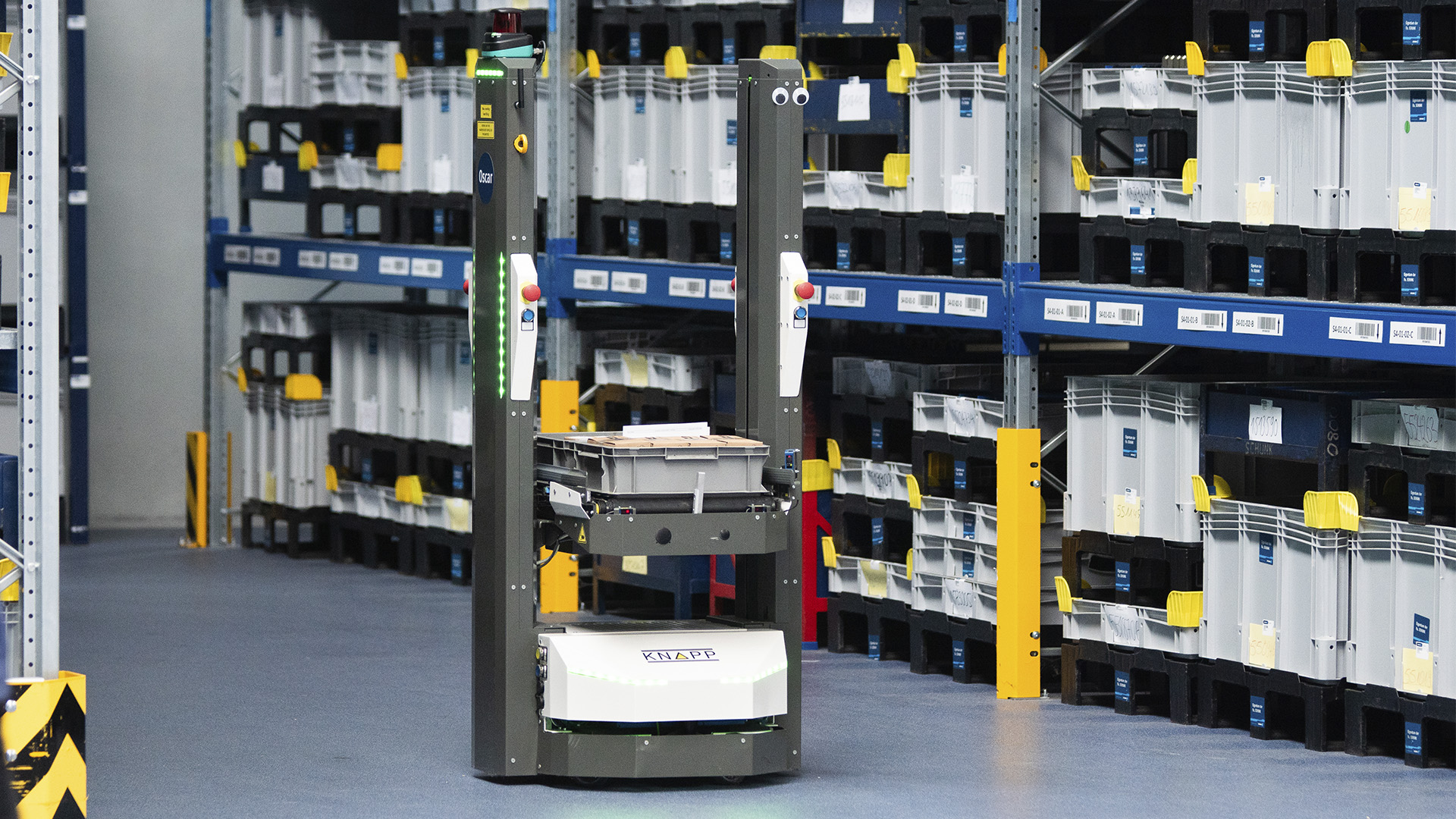
Mobile robots: Internal transport processes at SCHUNK
All the facts at a glance:
Transports 2 containers up to 25 kg (55 lb)
3 I/O modules to control 5 rapid action doors and 4 fire doors
Which transport processes are handled by the Open Shuttle handle?
Weiland: In Brackenheim-Hausen, we are responsible for manufacturing grippers and automation components. The Open Shuttle handles the following internal transport processes:
- Transporting the separate components to the assembly line where they are assembled as gripper units and
- Transporting the finished units back to the warehouse.
The Open Shuttle transports the individual components of the gripper, including any papers involved, to the individual assembly teams. At the assembly lines, the parts are assembled, checked for quality and then packed into finished product cartons. The individual components needed at the assembly lines as well as the completely packaged end products are transported in containers to the shipping warehouse, where they are temporarily stored until needed for the next step of assembly or until being shipped out.
Customized, intelligent automation solution
What are the special features of the automation solution?
Weiland: Containers are transferred to the assembly lines and the small parts warehouse via flow racks with roller conveyors that are equipped with sensors. As soon as the container blocks the optical sensor, an order is triggered for the Open Shuttle to come pick up the container for transport. We selected this solution for its technical simplicity as it handles the weights we need and has few electronic components. The sensors monitor the storage locations at both source and target and signal the system when there are containers to be picked up and when there is space to accept a container. Transport orders are thus automatically generated and empty runs avoided. When implementing further assembly lines, we build the flow racks ourselves and obtain kits from KNAPP for the trigger mechanism, orientation triangle, sensors and I/O modules.
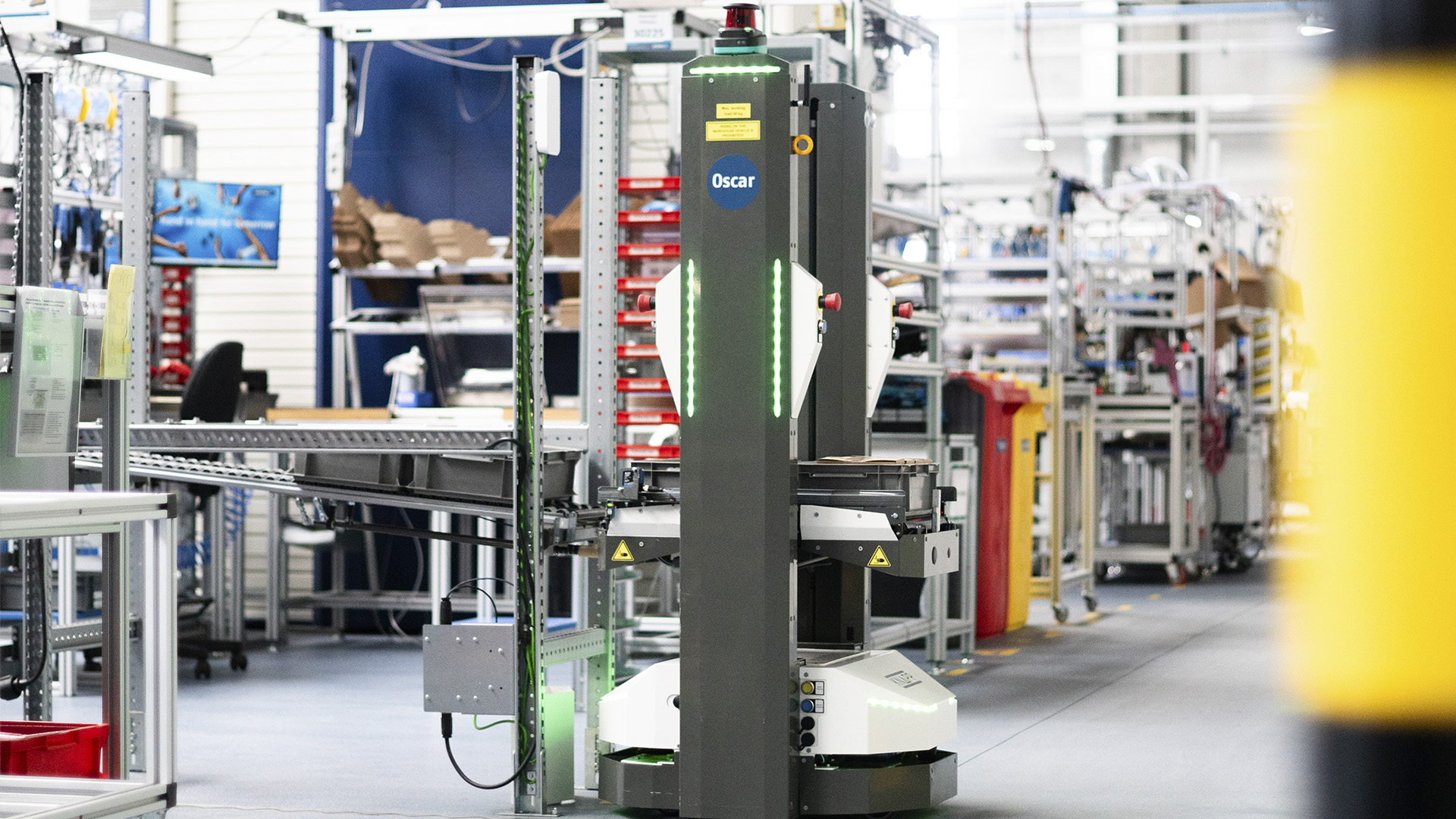
“Since we build the flow racks ourselves, we are faster and more flexible to connect with further assembly lines. We can change the frames and expand exactly how we need it.”
Weiland: Along the path between the individual assembly lines and the small parts warehouse are five rapid action doors that communicate with the Open Shuttle via a module, so when the autonomous mobile robot approaches the door, it opens automatically. Fire doors are also located here, which close when necessary. The robot is not allowed to stop in these throughways because it would interfere with the fire door. KNAPP knew exactly how to help us in this matter, having already had experience with the issue from other solutions. The AMR uses its I/O module to check whether there is a fire or not, which prevents it from entering the corridor in front of the fire door. This system functions reliably without problems.
Oscar: The new guy is an AMR
How satisfied are you with the solution handling internal transport using the Open Shuttle?
Weiland: We are very happy with Oscar, which is the name we gave our Open Shuttle. We came up with the name by combining OS for Open Shuttle and CAR for the Open Shuttle as a vehicle. Thus Oscar. Among ourselves, when we talk about the Open Shuttle, it’s always just “Oscar”. We get along well with Oscar, who is technologically reliable and a good worker. In the beginning, our personnel was a bit skeptical about Oscar. This surprised me because we are in the automation sector ourselves and, up until then, there had been no issues when we worked on increasing our efficiency. However, our personnel got over it very quickly once they saw how useful the technology was. Acceptance was also helped by the friendly appearance of the robot with its blinkers always signaling when it would make a turn. Oscar seems friendly – he’s no robomonster.
Working together as equals
Tell us about working with KNAPP.
Weiland: KNAPP works very professionally and has earned our trust. Should problems arise, you can always ask and be certain they will find a solution with you. We felt well taken care of, including with respect to customer service.
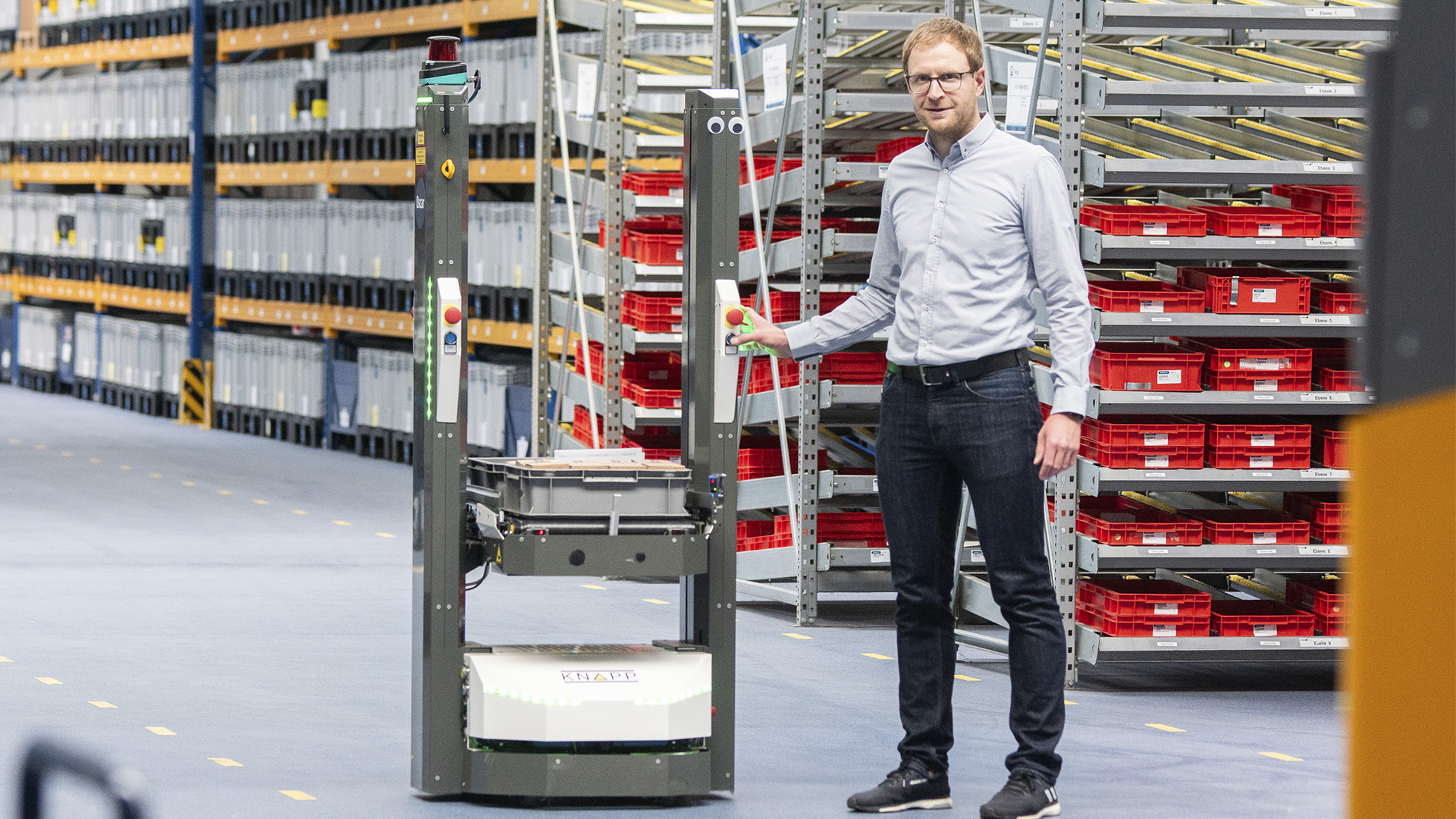
“Our mobile robot, who we call ‘Oscar’, reliably carries out its tasks. With KNAPP, we experienced a very professional working relationship among equals. We felt very well taken care of.”
Have you made plans to take further steps in automation in the future?
Weiland: We started at the Brackenheim-Hausen location with an Open Shuttle project and, over the long term, we’d like to benefit from the use of AMRs at other locations. Oscar was our starting project because we couldn’t gauge the extent of his capacity at first. We were unsure of how fast he would move and what effect he’d have on our indoor traffic, but now we are very satisfied with his performance. Oscar will not remain alone for long and will soon have a friend to work with. The addition is planned for the end of this year or the beginning of next year. We don’t have a name yet, but I am open for suggestions.
Further reading recommendations

Autonomous mobile robots (AMRs) facilitate flexible, efficient transport processes. Whether deployed in manufacturing, food retail or in distribution logistics – their range of use is wide. Discover more about this future-oriented technology.

