Autonomous Mobile Robots (AMR) for Warehouse Automation
Over the years, many different names have been coined for flexible transport systems on the market, from automated guided vehicle (AGV), autonomous mobile robot (AMR) to autonomous intelligent vehicle (AIV). Our Open Shuttles are autonomous and intelligent transport robots that help bring flexibility to the design of logistical processes. Find out more about our flexible solution for internal transport.
Intelligent AMR robots for flexible warehouse logistics
Are you looking to use automation to interconnect different areas of your warehouse and production? Do you need your goods to arrive at the right location in the right quantity and at the right time – while reserving the ability to make changes flexibly as needed?
Our autonomous mobile robots, or automated guided vehicles, make all this possible – automatically, with ease and efficiency. Infused with intelligent software, our Open Shuttles reliably carry out transport orders autonomously, navigating warehouse space freely while identifying and avoiding obstacles. This means they can be integrated in existing warehouse environments – no extra infrastructure needed. Our AMR robots offer maximum flexibility while increasing productivity and freeing up human resources for value-generating tasks. Our Open Shuttles AMRs are the smart, flexible way to automate your warehouse-internal material flow.
You are currently viewing a placeholder content from YouTube. To access the actual content, click the button below. Please note that doing so will share data with third-party providers.
More InformationLooking for an AMR for your warehouse?
Find out more about Open Shuttles by KNAPP!
AMR robots are the perfect solution for logistical challenges
Change is omnipresent in industry, whether due to ever-changing environmental and market situations, cost pressure or shortages in resources or qualified workers. To compensate for this, a quick, flexible solution to lower costs and boost efficiency is needed. With our Open Shuttles autonomous mobile robots, you can immediately tackle today’s challenges with ease. And if you want to make sure the system works in your environment, simply test the processes and layout beforehand to make implementation times even shorter.
Types of autonomous mobile robots
Thanks to their incredible flexibility and versatility, our autonomous mobile robots can be used in many areas of application. We offer different models to ensure that your requirements are covered:
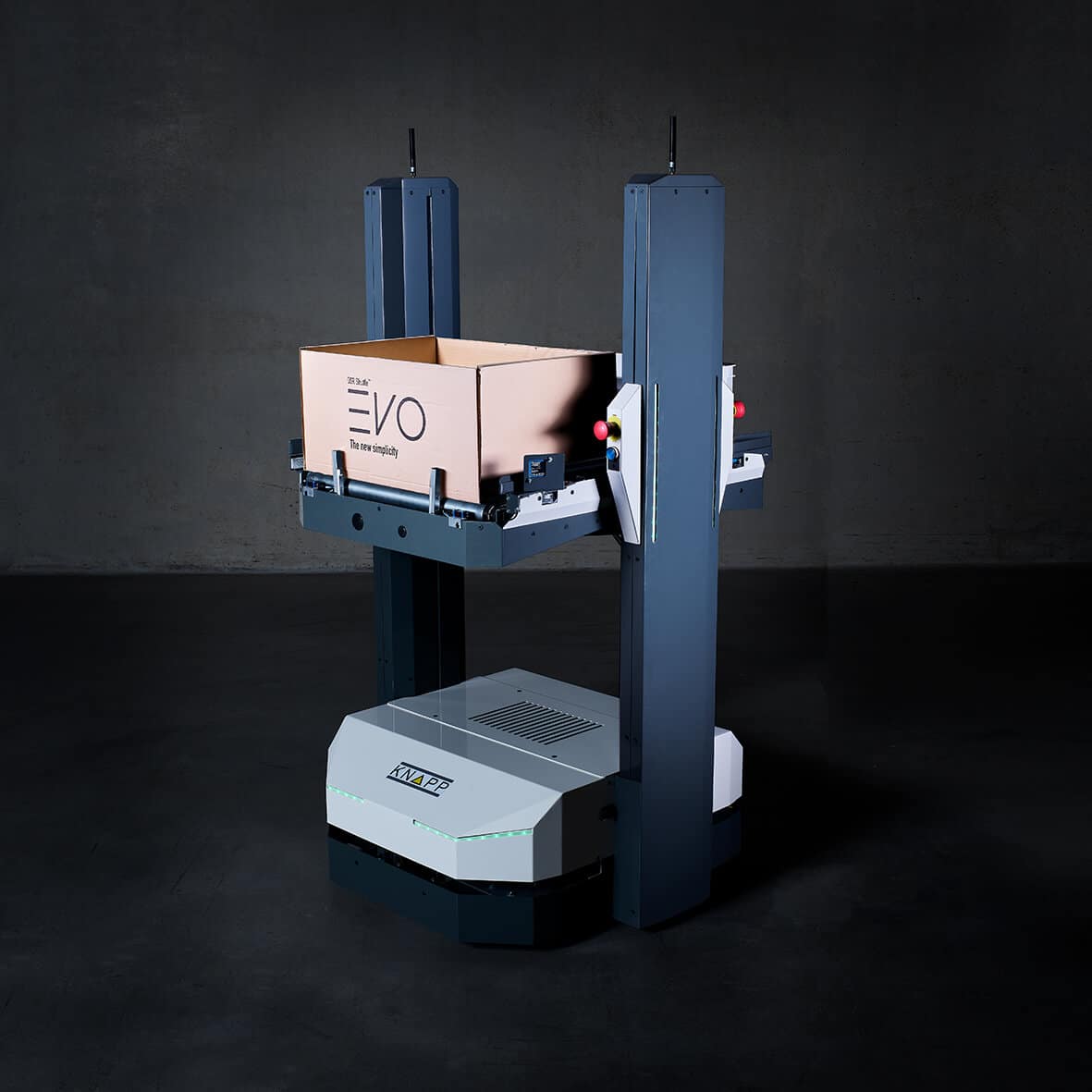
Open Shuttle
AMR for container transport
for transporting containers, cartons and trays
Payload of up to 120 kg (265 lb)
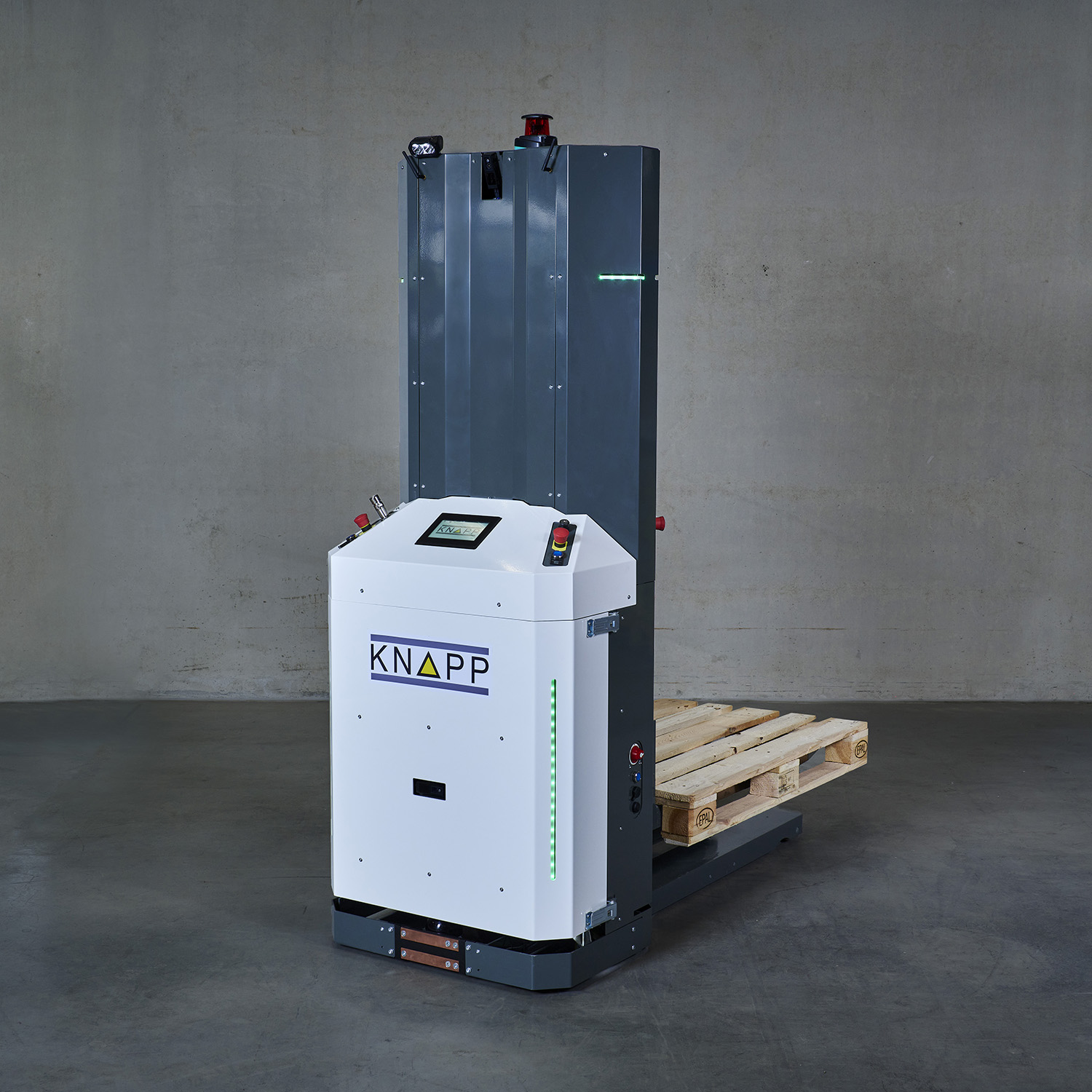
Open Shuttle Fork
AMR for pallet transport
for transporting pallets and special load carriers
Payload of up to 1,300 kg (2,866 lb)
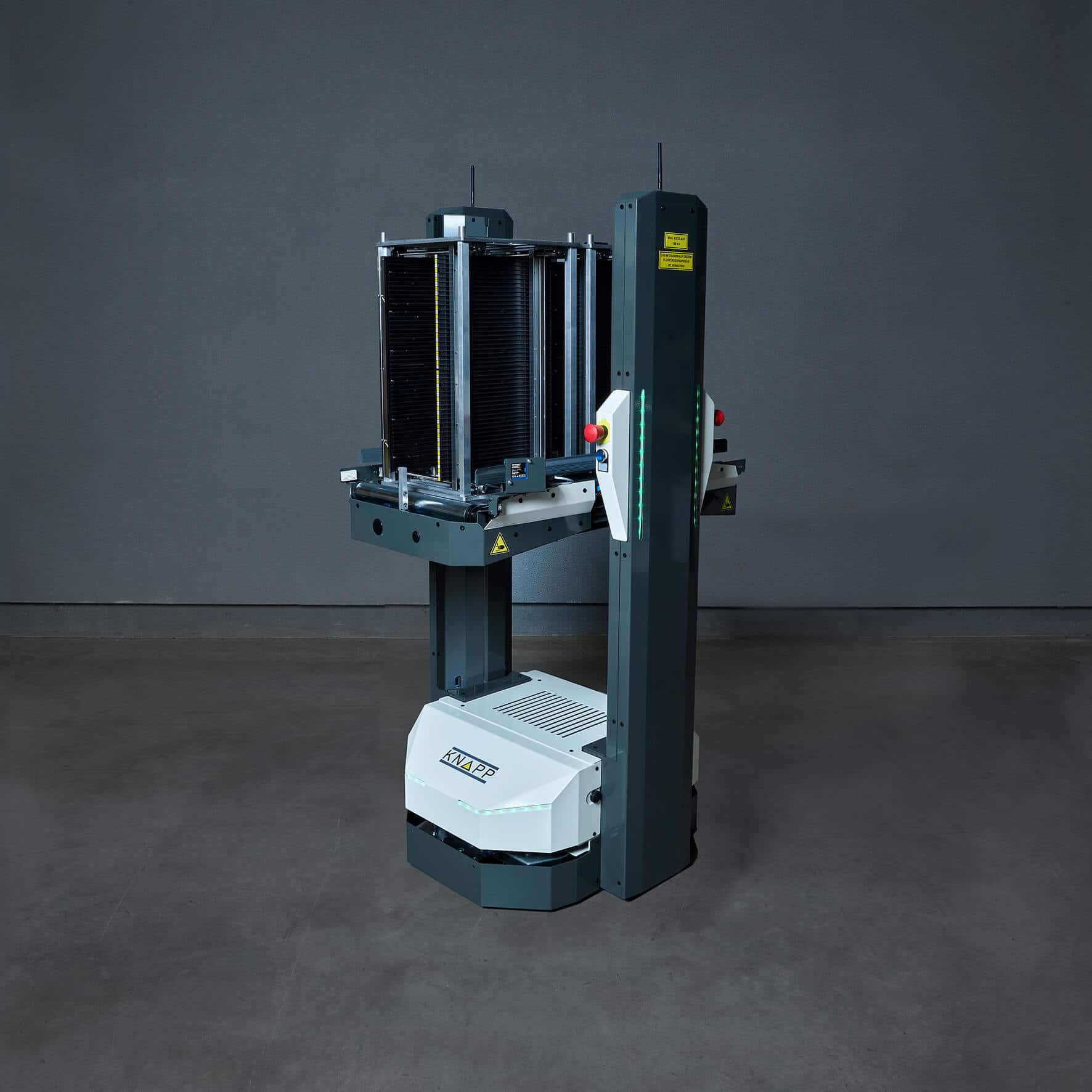
Open Shuttle
AMR for the electronics sector
For transporting printed circuit board magazines as well as containers, cartons and trays
Payload of up to 50 kg (110 lb)
Advantages of our autonomous mobile robots
Various applications of autonomous mobile robots
Our Open Shuttle AMRs are a solid alternative to stationary container and pallet conveyors. With our robots, you can link all areas of your warehouse flexibly and easily while performing various tasks:
- Performing internal transport with mixed fleets in one system
- Supplying work stations and production lines just in time
- Connecting to production machines
- Supporting the picking process
- Performing special and express transport tasks
- Connecting to packing and repacking stations
- Connecting storage systems and augmenting existing conveyer systems
- Supplying kanban racks, flow racks and pallet racks
What’s more, our Open Shuttles perfectly integrate into existing systems or act as a direct link to automated storage systems, such as our OSR Shuttle Evo or InduStore.
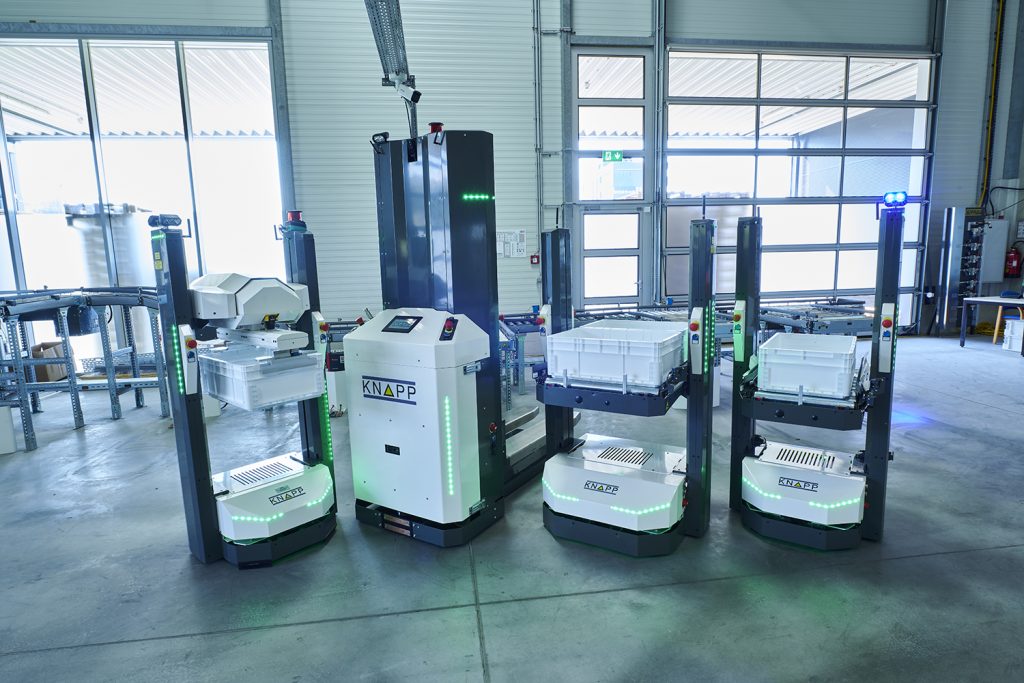
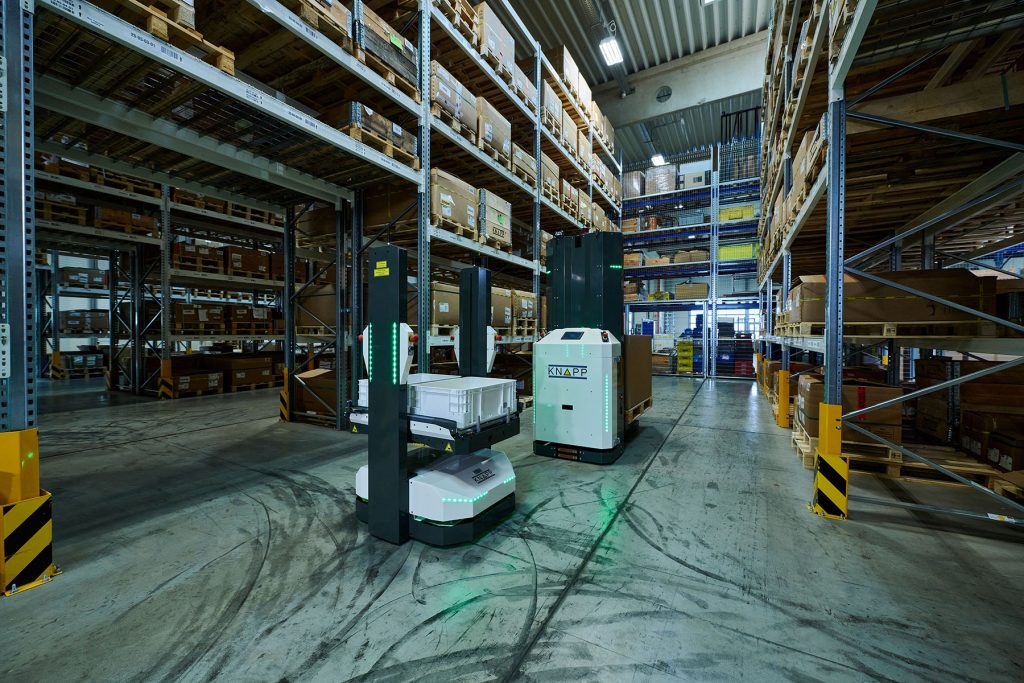
Scale your Open Shuttle fleet to meet your needs
You decide what your Open Shuttle fleet should look like. Whether you have two shuttles or over 100, the size of the fleet can be adapted to your current situation and changed at any time. Our range of AMR models with different load-handling devices can also be combined to form a versatile fleet.
Our intelligent fleet software makes it possible to efficiently visualize and control all transport resources. This also allows our robots to function in combination with other warehouse vehicles, such as AMRs and forklift trucks from other manufacturers.
How do KNAPP’s autonomous mobile robots work?
Find out more here.
Add-ons to complete your Open Shuttle AMR solution
Our autonomous mobile robots can be flexibly tailored to your needs using our innovative add-ons.
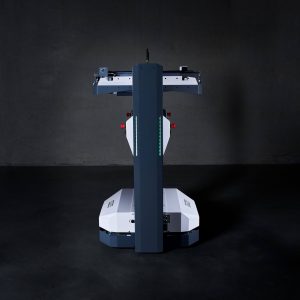
Integrated lifter
Our Open Shuttles can be equipped with a lifter to retrieve and deliver loads at different heights – from 550–1,500 millimeters (21.65 in–59.06 in) or from 0–1,200 millimeters (0–47.24 in) – and transfer them to different conveyors. This provides more flexibility when designing processes.
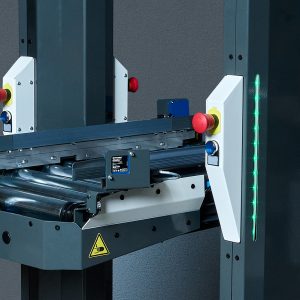
Integrated width adjustment
The load-handling device (LHD) can also be equipped with width adjustment, allowing the Open Shuttle to automatically adapt its LHD to the width of the load carrier. With the integrated lifter and width adjustment, the Open Shuttle flexibly adapts to both the height and the width of its load.
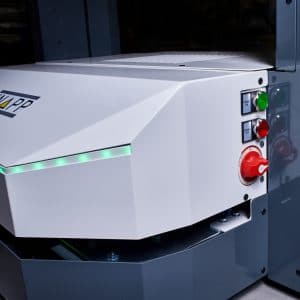
Indicator lights and sensors
Additional indicator lights and sensors increase the Open Shuttle’s visibility in warehouse areas with frequent traffic. To meet your requirements, our AMRs can be equipped as needed.
AMR robot integration made easy
At KNAPP, we know that every second is valuable and what system downtime means for your business. For this reason, our robots are quick and easy to implement. Installation only takes six simple steps and can be carried out while your warehouse is in operation.
How to install the Open Shuttle AMR robots in 6 easy steps >
Become an integrator for our autonomous mobile robots!
Open Shuttle – the new flexibility.
Find out which companies bank on our Open Shuttles:
You are currently viewing a placeholder content from YouTube. To access the actual content, click the button below. Please note that doing so will share data with third-party providers.
More InformationYou are currently viewing a placeholder content from YouTube. To access the actual content, click the button below. Please note that doing so will share data with third-party providers.
More InformationHow to get your flexible autonomous mobile robot
Our Open Shuttles can be acquired in a number of different ways. You have the following options depending on your needs and requirements:
Would you like to test, rent or purchase an Open Shuttle?
You are just a few steps away!
FAQs on automated guided vehicles (AGVs)
Automated guided vehicles follow specified, pre-set routines and processes, while autonomous mobile robots process information from their environment and autonomously make decisions. This blog post provides more information on the topic of AMRs and AGVs:Two Automated Guided Vehicle Systems, Compared
- Internal transport
- Supplying work stations and production lines
- Connecting production machines
- Supporting the picking process
- Performing special and express transport tasks
- Connecting to packing and repacking stations
- Connecting directly to storage systems
- Complementing an existing conveyor system
- Supplying kanban, flow and pallet racks
The space required for an AGV system depends on the size of the fleet and the required throughput. The Open Shuttles by KNAPP are some of the most space-effective on the market. For more information, get in touch with us at: kin.sales@knapp.com
KNAPP offers three different ways to integrate:
- The AMRs communicate directly with the customer’s higher-level system and receive transport orders from it (SAP integration available).
- The AMRs receive transport orders from the machine control systems in the form of sensor signals.
- The AMRs receive transport orders directly from employees, who generate the orders on a user-friendly interface.
The base price for an Open Shuttle starts at about 45,000 euros and will vary depending on the price and the equipment needed. There are also expenses associated with integration which depend on the project.
Depending on the complexity and number of vehicles, delivery times of three months or more can be expected.
After completing training, every customer can independently change maps, processes, and procedures using the user interface.
The Open Shuttles by KNAPP can be used and installed without a warehouse system or other product.
KNAPP offers transfer stations in the form of conveyors and flow racks for containers as well as the equipment necessary for efficient maintenance.
Explore our blog posts on warehouse automation and the value chain:

Optimize intralogistics processes and increase performance using automation. What is the right level of automation for your operation? In this post, we present various levels from innovative manual warehouses up to fully automatic systems.

Autonomous mobile robots (AMRs) facilitate flexible, efficient transport processes. Whether deployed in manufacturing, food retail or in distribution logistics – their range of use is wide. Discover more about this future-oriented technology.
