By automating your intralogistics, you optimize your processes and raise efficiency. But how much automation is right for your business? In this blog post, we introduce you to the different degrees of automation: from a completely manual warehouse using intelligent software to the fully automatic manufacturing of the future. Discover more.
Key Takeaways
The call for more efficient intralogistics
Intralogistics plays an important role in the profitability of a company and includes all the processes and systems involved in the internal transport, storage and order processing of goods and materials. With rising cost pressure, skilled labor shortages as well as technological progress, automation for intralogistics is becoming increasingly important. That’s because the new challenges call for a more flexible and efficient design of storage and transport processes. In this context, let’s take a closer look at the advantages of automation solutions before we go into the various technologies and stages.
The advantages of automation
Automating intralogistics offers companies many opportunities to increase efficiency and stay competitive. Here are the most important advantages:
Automation technologies
Intralogistics systems are automated using a variety of innovative technologies:
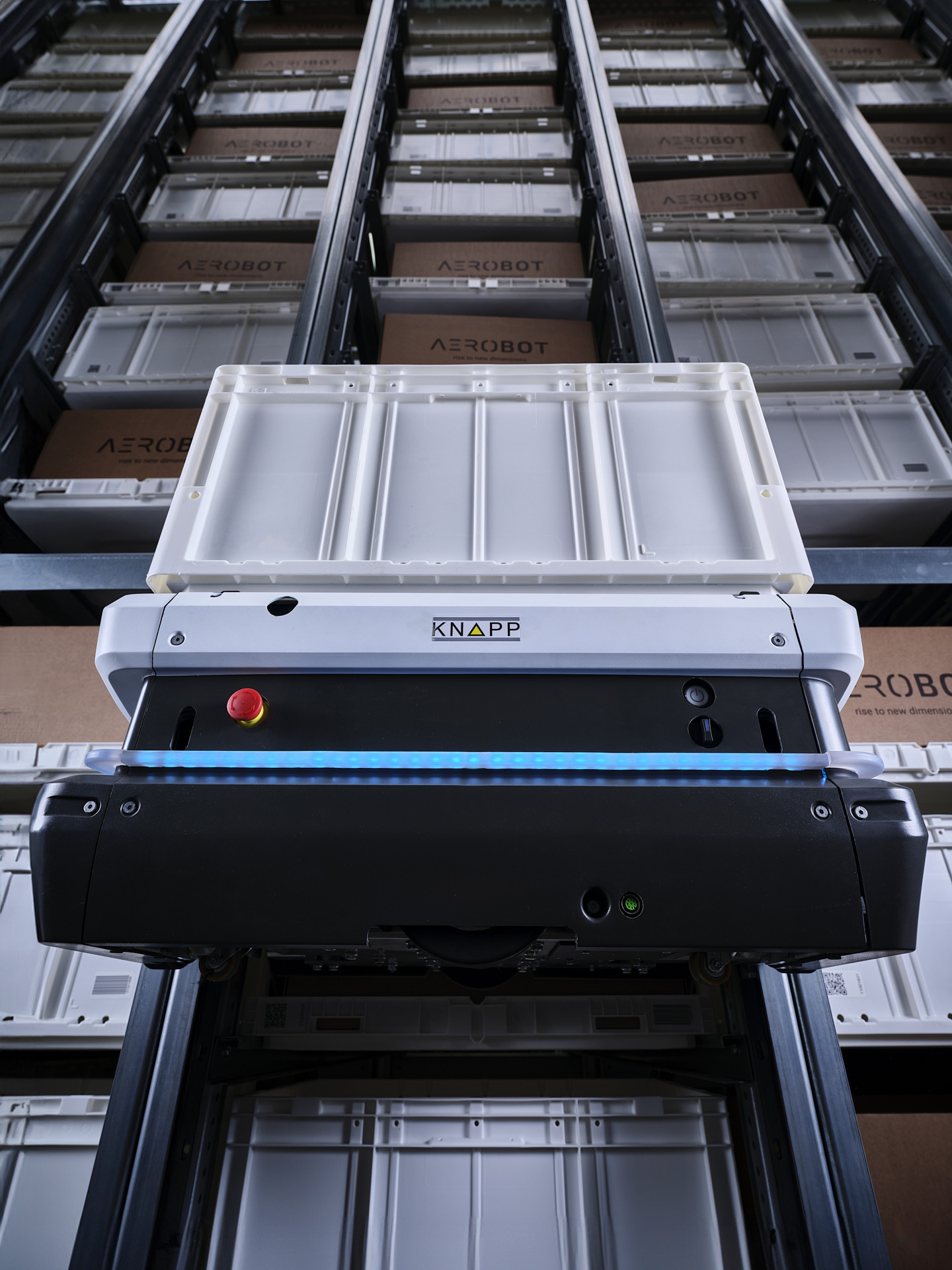
Our comprehensive KNAPP portfolio means we can offer customized automation solutions for every requirement. Our portfolio ranges from simple stacker cranes to innovative storage and transport robotics and highly efficient storage and retrieval systems. Our intelligent software rounds out what we offer as a supplier of complete solutions.
Automation in intralogistics from 0 – 100 %
What form does automation take in today’s intralogistics? Depending on the requirements and goals, automation can be used in many different ways, from semi-automation where humans work side-by-side with machines to full automation where processes are carried out with little to no human intervention. Let’s take a closer look at the possibilities for the varying degrees of automation.
No automation: a manual warehouse with intelligent software
Automation in intralogistics is often associated with large warehouse solutions and a lot of technology. For smaller companies, this is likely too much automation and too great an investment. A high-tech warehouse is not always the solution. With innovative software and ergonomic work stations, individual processes and existing steps in production can be efficiently and intelligently designed and optimized.
Best practice at Jerich International:
work station with integrated image processing system
At Jerich International, quality checks are made on vehicle body parts at a state-of-the-art work station equipped with an integrated image processing system. The Vision Smartdesk helps personnel to check the parts. The actual images are compared with expected images. Thanks to real-time feedback, quality deficiencies are immediately pointed out, and personnel are given optimal support while working.
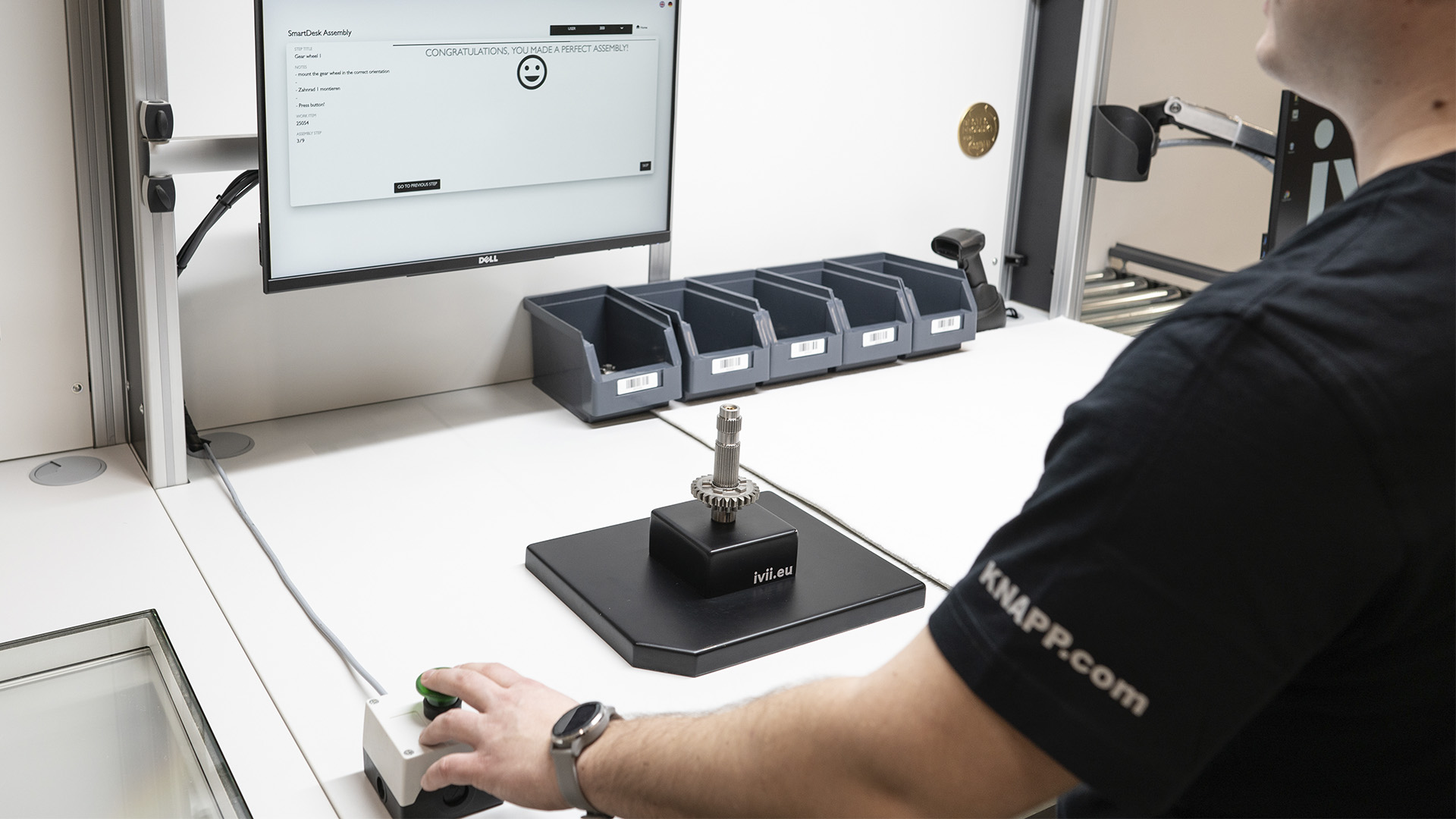
25 % automation: manual warehouse and automated transport processes
A great first step in automation is using an autonomous mobile robot (AMR) to handle internal transport jobs. These robots connect individual locations with each other and ensure the flow of goods. Automating transport makes sense and allows personnel to concentrate on value creation instead of pushing around heavy boxes. The required parts are supplied to the work stations and production lines just-in-time. What’s more, an automated guided vehicle system can easily be integrated into existing structures.
Best practice at Fronius:
AMR automates transport processes
Fronius, a worldwide leader in welding, battery charging and photovoltaic systems is using Open Shuttles for internal transport. The Open Shuttle Fork, an autonomous mobile robot for pallet transport, connects the goods-in and goods-out areas with the production cells and supplies them automatically with goods. Even where there is a lot of traffic, these AMRs navigate safely through the halls. The space-effective transport solution was implemented without having to make changes to the existing infrastructure. Thanks to the intelligent fleet control software KiSoft FCS, Fronius can make changes on their own.
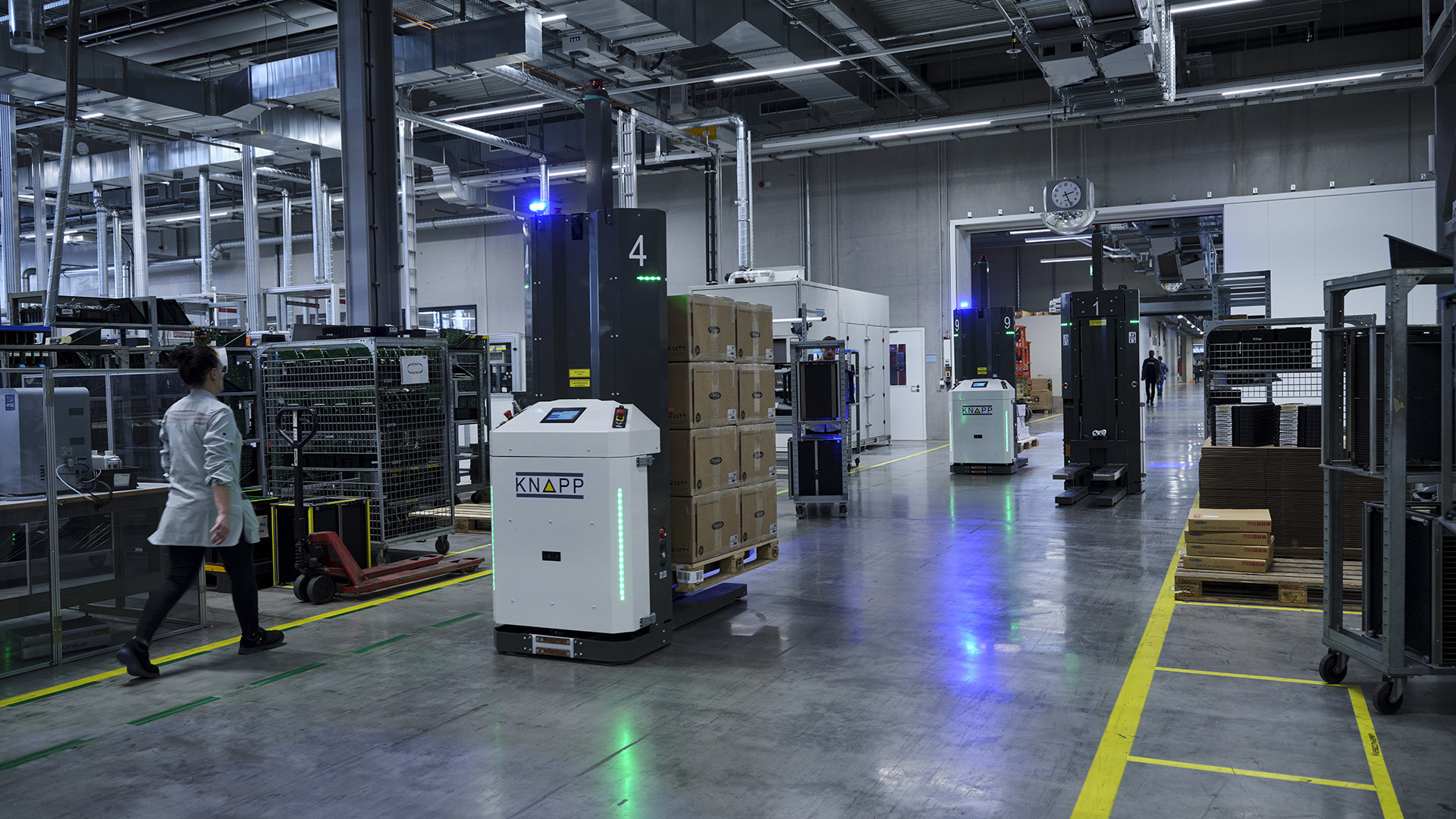
50 % automation: automated small parts warehouse (ASRS) and ergonomic work stations
If what matters is high-performance and space-saving storage of small parts, along with supplying work stations quickly and efficiently, then it is worth investing in an automated storage system. Companies have many possibilities here: from a simple stacker crane system to innovative warehouse robotics to shuttle systems. Here, the storage system is connected directly to modern work stations for goods-in, goods-out, assembly and picking processes. An intelligent warehouse management system controls and monitors the processes centrally. Our blog “Shuttle vs Bots: Which Storage Technology is the Better Choice? goes in depth on this topic.
Best practice at Getriebebau NORD:
warehouse automation for efficient processes
The automated small parts warehouse Evo Shuttle supports the logistics hub of Getriebebau NORD in Bargteheide, Germany, helping to supply materials worldwide as well as to production and the onsite storage facilities. Through the software KiSoft One, NORD controls and monitors the processes. The ergonomic work stations of the “Pick-it-Easy” series support personnel in goods-in as well as in picking. In goods-out, modern packing stations are available for shipping. The storage system is connected to the work stations through the conveyor system. Thanks to its optimal use of space and efficient processes, the solution is a winner.
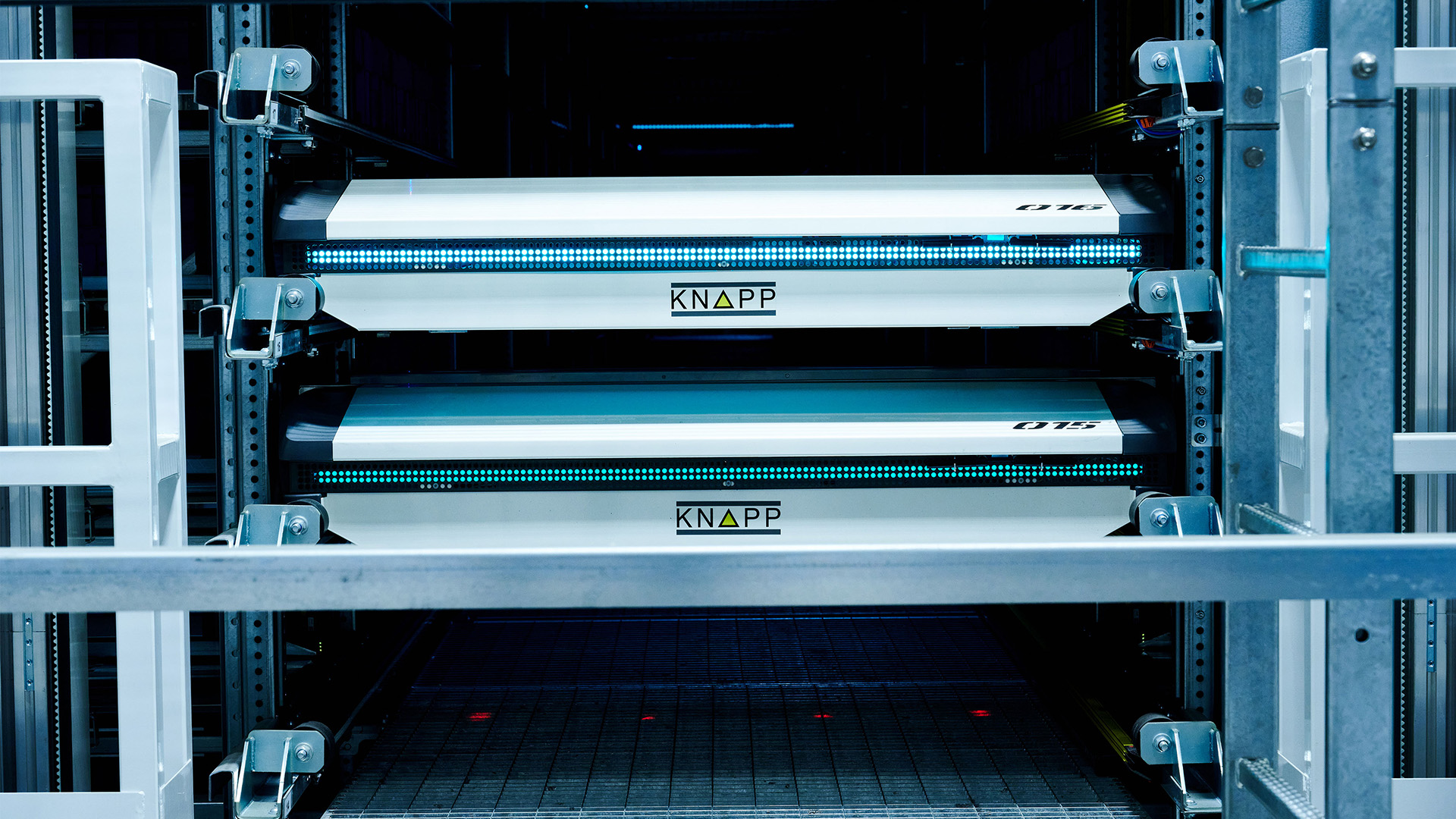
75 % automation: innovative logistics solution knows all the tricks
The higher the degree of automation, the more areas and processes are connected with each other and covered by innovative technologies. At the center is an automated storage system with ergonomic work stations and direct connection to autonomous mobile robots or tugger trains. The software has a major role to play while assistance and image processing programs make an innovative add-on.
Best practice at Magna Assamstadt:
innovative logistics solution for production supply
Magna, one of the world’s largest automotive suppliers, invested in a comprehensive automation solution at their Assamstadt, Germany, location in order to increase their real net output ratio. The company relies on the automatic small parts system Evo Shuttle in combination with the Open Shuttle autonomous mobile robots for their intralogistics. Multifunctional work stations are directly connected to the storage system and are supplied with goods just-in-time and just-in-sequence. Transport orders between the storage system and the production lines in the adjacent halls are handled by the Open Shuttles. The highly modern automation solution ensures efficient and flexible production processes.
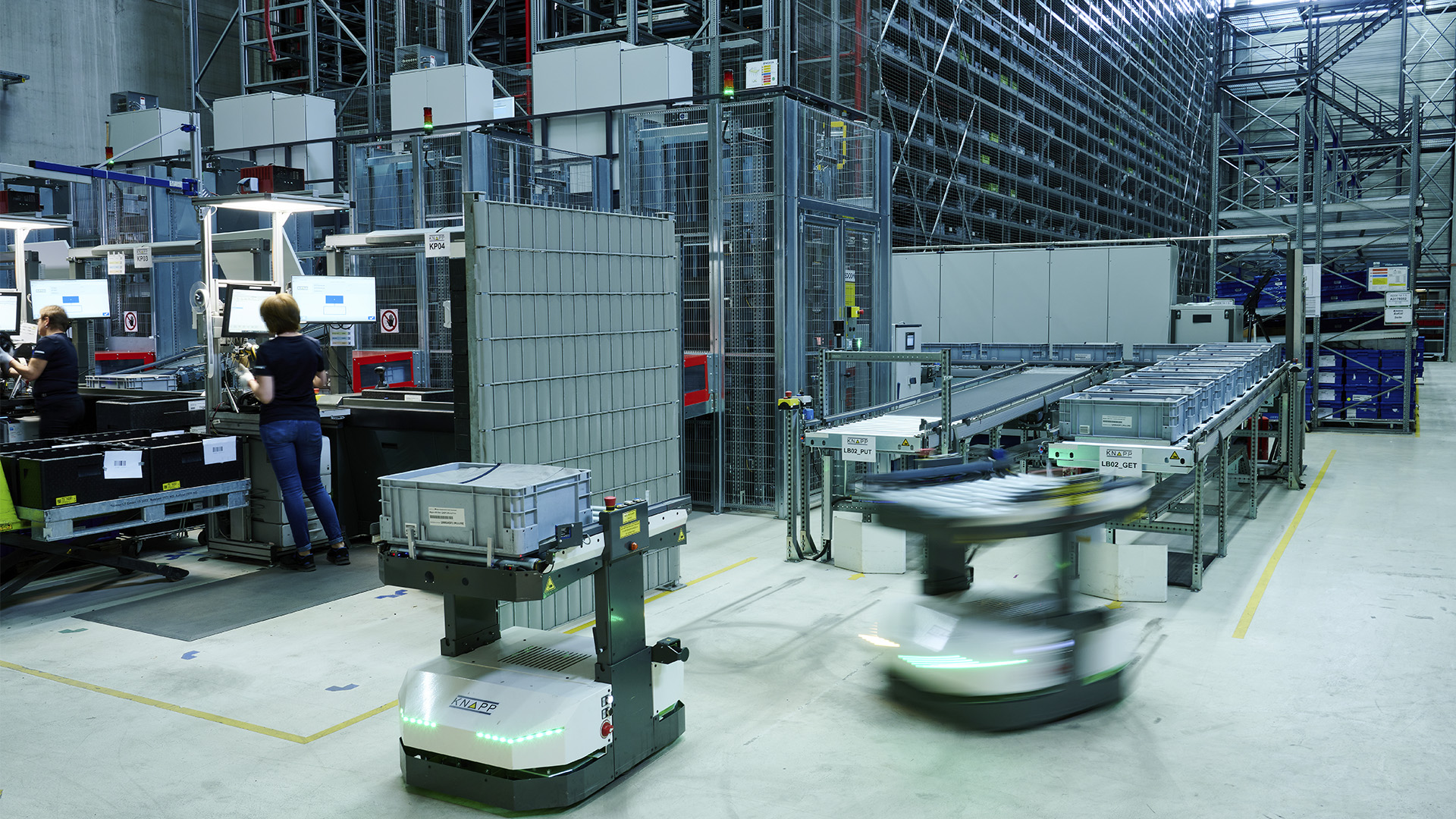
100 % automation: fully automated intralogistics
Fully automated logistics does not mean a warehouse devoid of human beings. What it really means is a warehouse full of technologies, where humans and machines work closely together. This includes the warehousing, transport, picking and packing of goods. By using robots, autonomous vehicles and intelligent software solutions, processes can be almost completely automated. Everything is coordinated like clockwork for efficient, fast, and error-free operation. As a result, large quantities of data are generated, which must be optimally used as well.
Read more about it in our blog Smart Manufacturing: The Future of Production.
Best practice at Würth:
smart production ensures optimal processes
The automation solution at Würth Industrie Service includes an all-round intelligent package of technologies and software. The company relies on several picking robots, the Pick-it-Easy Robots, to handle the rapid picking and in shipping, to do the palletizing. The Open Shuttles handle all the internal transport processes fully automatically. The Evo Shuttle storage systems handle all the storage, consolidation, sequencing, dispatch buffering and picking processes. A Fastbox sequences orders quickly and accurately. Order processing is carried out according to the goods-to-person principle at the numerous multifunctional work stations. A comprehensive software solution allows the individual processes to be integrated into a network for intelligent automation. Data is analyzed using an analytics tool from which optimization steps are derived with respect to system operation and maintenance. Perfect, complete automation.
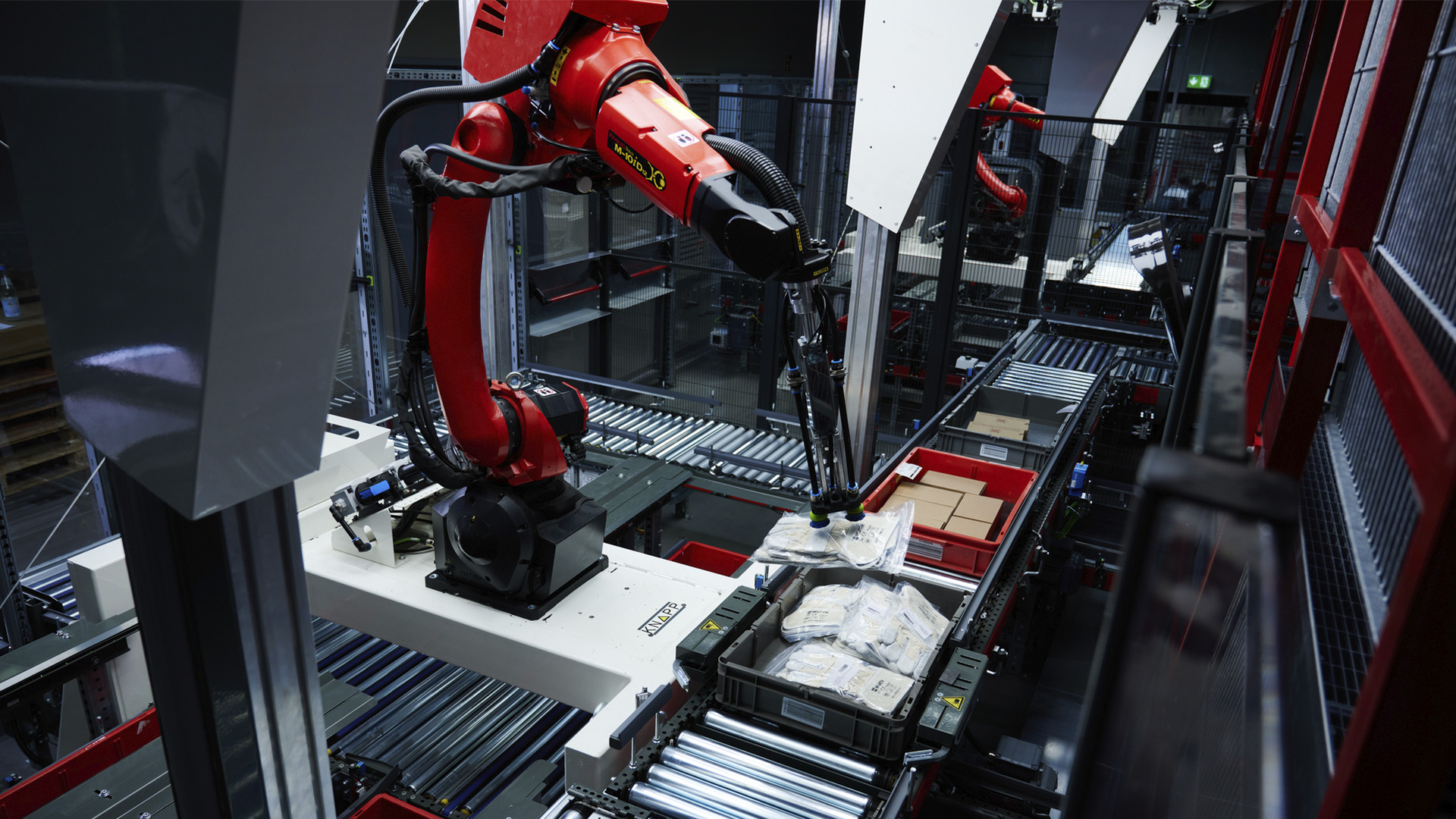
Conclusion and outlook
In the future, intralogistics automation will be indispensable for boosting competitiveness. The earlier companies get going with new and innovative technologies, the better they will be able to keep pace with the rapid developments in this area. Technological advances, whether they come in the form of innovative warehouse robotics or artificial intelligence, bring more efficiency and flexibility to warehousing and manufacturing processes. The key to success for every company, however, lies in a well thought-through strategy which considers the right degree of automation and the right technologies.
Further reading recommendations

Autonomous mobile robots (AMRs) facilitate flexible, efficient transport processes. Whether deployed in manufacturing, food retail or in distribution logistics – their range of use is wide. Discover more about this future-oriented technology.

What does the smart factory of the future look like? Find out more about our vision for smart manufacturing!

Especially in times like these, supply plays a central role. Which trends and market developments are influencing the manufacturing industry? How can we respond to these challenges? The first part of this post on intelligent production supply will focus on these issues.
Additional Information
Let’s talk about what the optimal level of automation would be for your logistics processes. Just drop us a line at blog@knapp.com.