Innovative Shuttle Storage System for Getriebebau NORD
Getriebebau NORD has been developing, producing and distributing drive systems since 1965 and is the leading provider of complete solutions in their sector worldwide. In addition to standard drive technologies, the company provides concepts for specific applications and offers a broad range of products for many sectors. The site in Bargteheide, Germany ships components to their subsidiaries worldwide and assembles products that arrive from the various production plants.
The innovative Evo Shuttle, a KNAPP shuttle storage system, supports the logistics hub in Bargteheide in supplying materials worldwide as well as to production and the onsite storage facilities. What’s unique is that KNAPP equipped the automated small parts warehouse with Getriebebau NORD’s very own drive technology. The new automation solution really scores high thanks to optimal use of floorspace and its scalability.
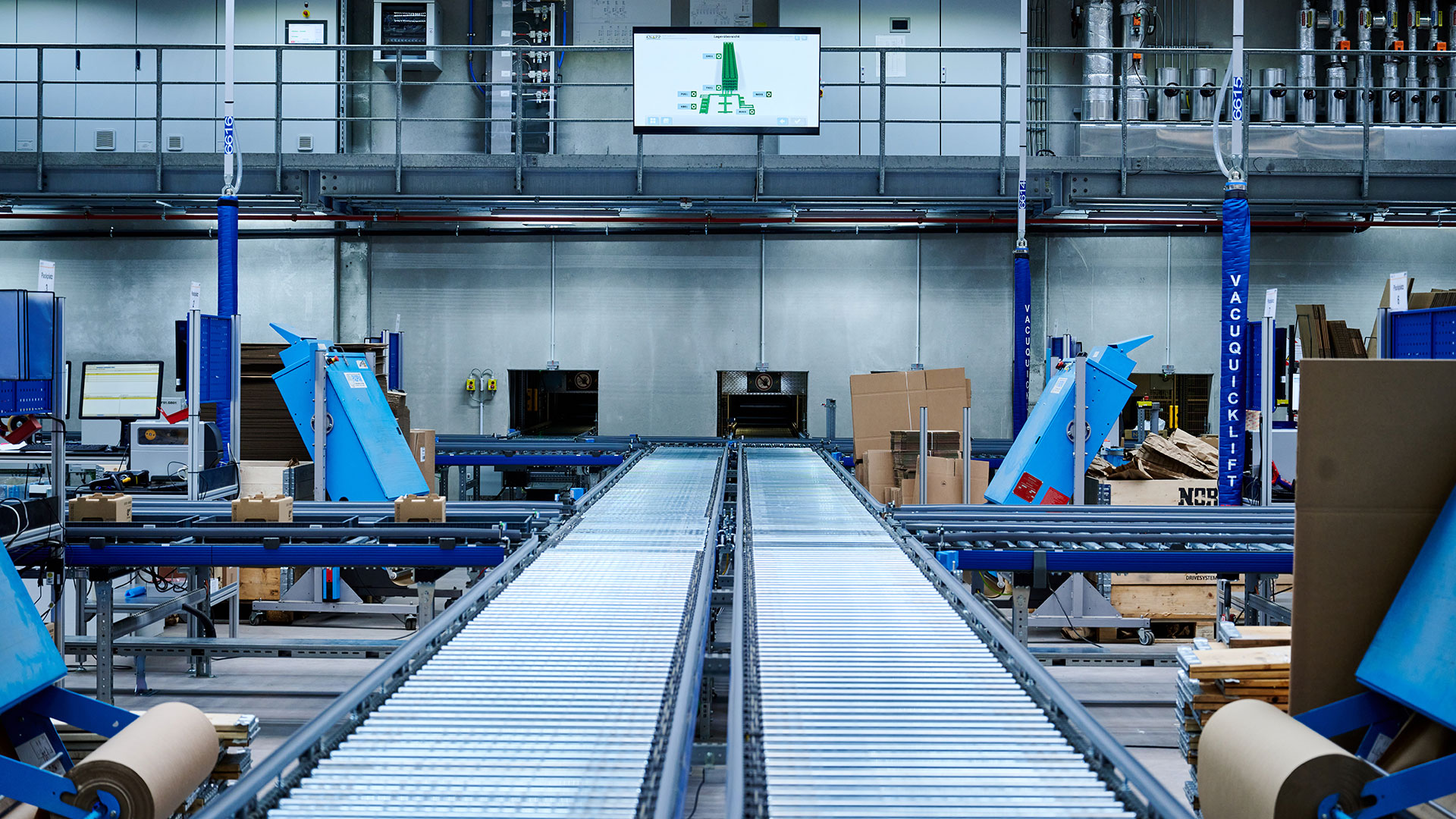
The different heights for storage in the Evo Shuttle allowed the space to be used much more efficiently at the site, raising the supply of small parts and on-site distribution to a whole new level.
Jörg Niermann
Head of Marketing, NORD DRIVESYSTEMS
Curious about logistics automation?
Contact our experts today.
Central supply for subsidiaries worldwide
Getriebebau NORD offers drive solutions, electric and gear motors and frequency converters. The Bargteheide location is the hub for the company’s worldwide logistics, providing materials to the 48 international subsidiaries. Over the past years, the supply of materials from suppliers has been steadily improving, which led to a heavy workload for the existing warehouse solution. The existing systems are designed primarily for pallet storage. Rising volumes of small parts and the increased demand on the picking lines will be covered by an automated small-parts warehouse (AS/RS).
Requirements for the Getriebebau NORD shuttle storage system
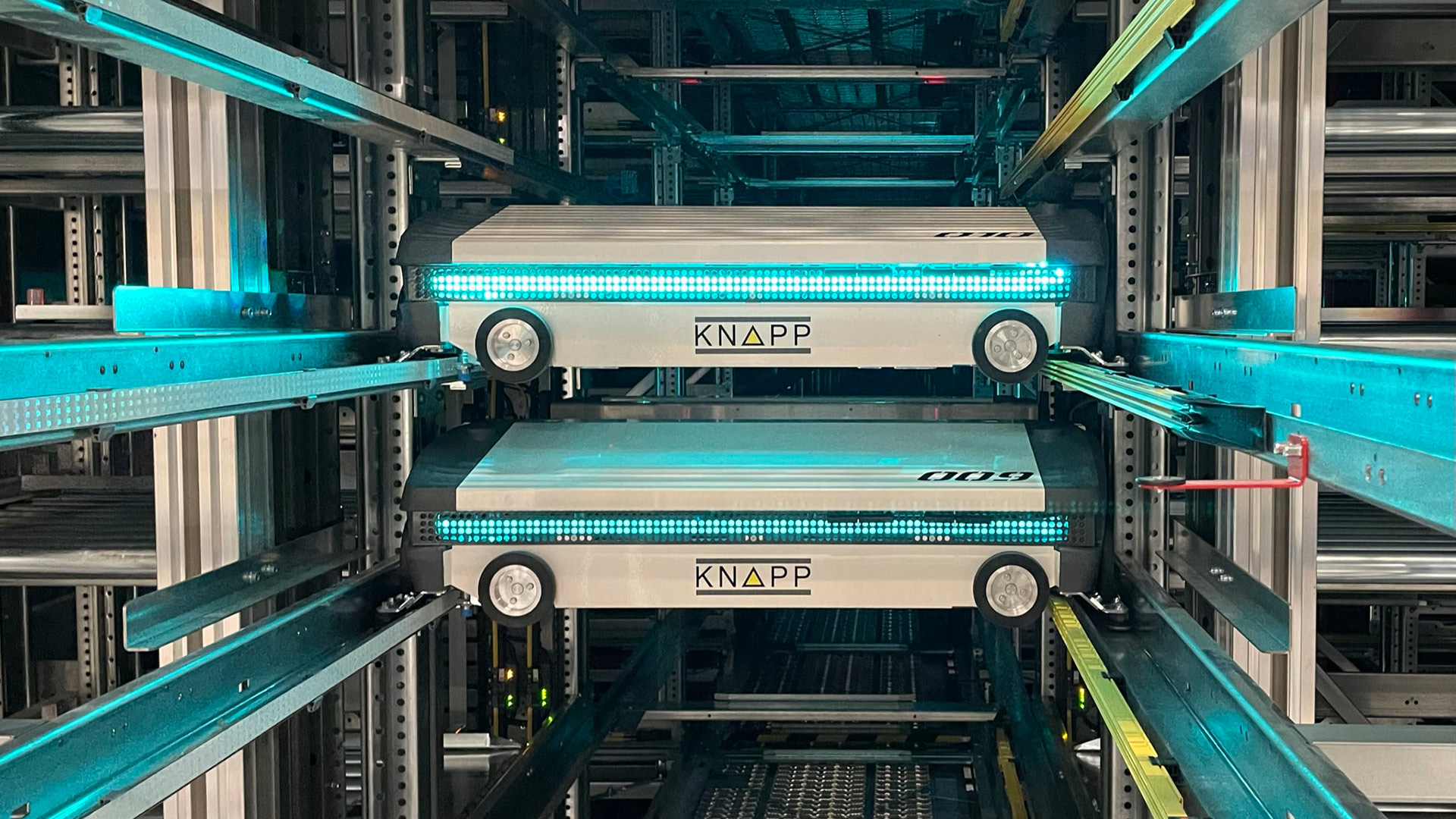
Evo Shuttle: Optimal use of space and a scalable solution
With an analysis of necessary movements in hand, Getriebebau NORD decided on the Evo Shuttle automated small parts warehouse. The optimal use of space and scalability were important in choosing this solution.
The new shuttle system handles three basic processes at Getriebebau NORD: It supports various assembly processes, supplies the onsite storage facilities with small parts and ensures the international supply of materials at pack stations located directly at the automated small parts. KiSoft One is the brain behind the scenes, keeping track of everything and controlling all the processes. What makes the new logistics hub extra special is that the automated small parts warehouse for Getriebebau NORD was equipped with their very own drive technology.
An analysis of the necessary movements showed that KNAPP’s shuttle system was the best fit for our requirements. The effective use of space as well as the scalability of the KNAPP solution convinced us.
Jörg Niermann
Head of Marketing, NORD DRIVESYSTEMS
levels
shuttles
storage locations
double cycles / hour
multifunctional work stations
pack stations
Are you interested in automating your company’s warehouse?
Find out more about our solutions:
A glimpse into the solution at Getriebebau NORD
The new automation solution has been operating at Getriebebau NORD since 2021. For the international supply of materials from the Evo Shuttle, the goods-to-person method was implemented in full. Work station ergonomics were improved along with the output. Read on to find out more about the storage processes at the company.
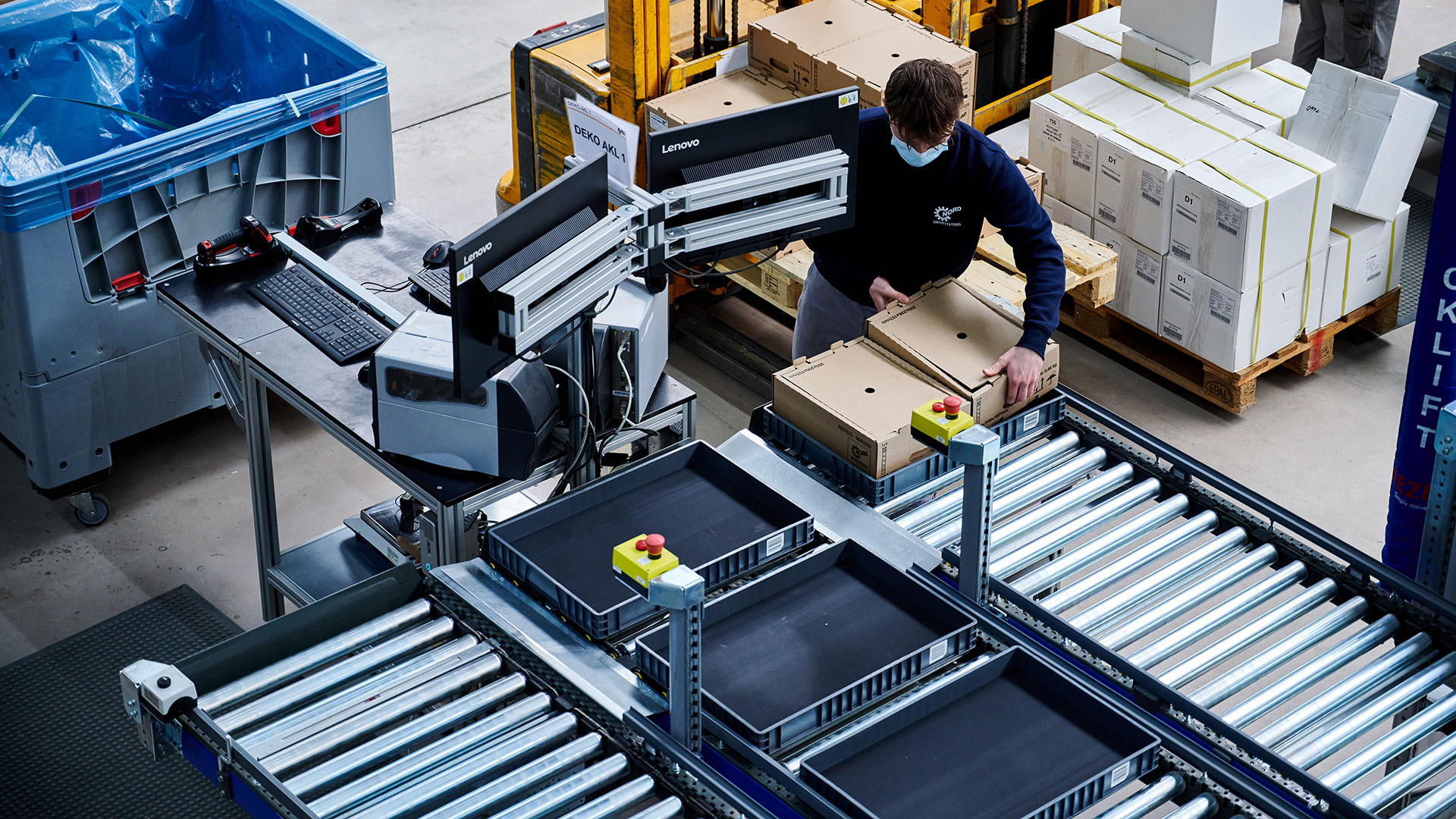
1) Goods-in
In the goods-in area, four Pick-it-Easy work stations make it easy for employees to register the goods in the system. The ergonomic work stations and intuitive operation of the easyUse user interfaces optimally support the employees in their work. Incoming goods are first registered at the work stations and repacked onto trays. An empty tray buffer supplies the trays to the work station. Then, the load carriers are conveyed into the Evo Shuttle. Contour and weight checks are made automatically along the way.
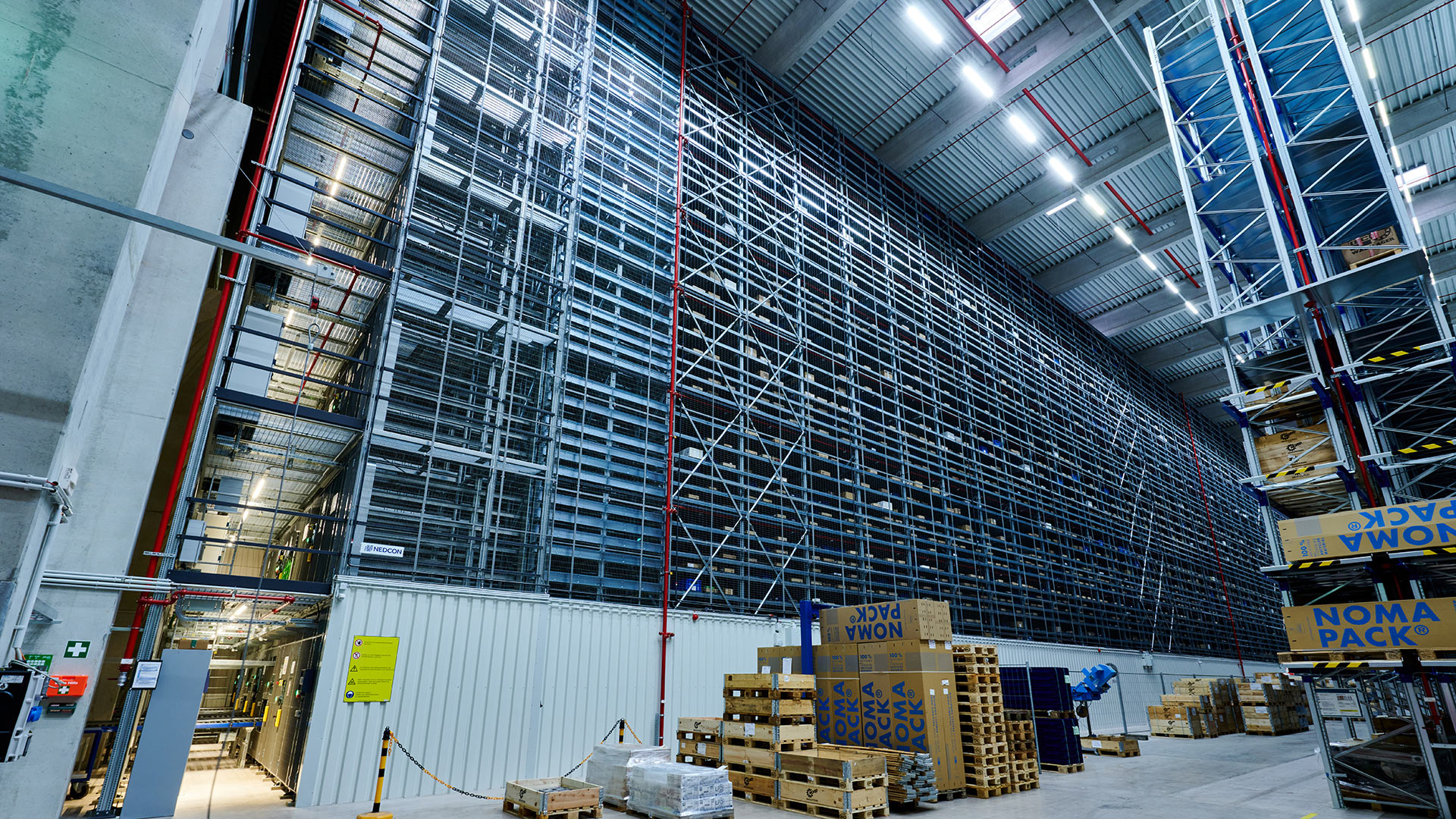
2) Storage in the Evo Shuttle
Trays and containers are efficiently stored, double-deep, in the Evo Shuttle. On 44 levels, 44 shuttles constantly store and retrieve load carriers in three storage aisles, transferring them to one of two lifts. The Evo Shuttle can switch aisles in certain cross aisles, allowing any shuttle in a level to access every storage location in that level. When small parts are needed for picking or packing, the KiSoft One software gets the order from NORD’s warehouse management system, SAP® WM, and transmits it to the warehouse control system. The required load carriers are retrieved from storage.

3) Picking
At the Pick-it-Easy Flex work stations, three processes are carried out.
- Picking to supply assembly: Parts are picked to carts and then brought to the assembly halls.
- Picking for the onsite storage facilities: Parts are picked to pallets and transported to the storage locations.
- Pre-picking for shipping parts worldwide: Small parts are pre-picked and temporarily stored on trays in the Evo Shuttle.
All the parts needed for picking are retrieved from the Evo Shuttle and conveyed to the work stations. The system guides the employees through the whole picking procedure.
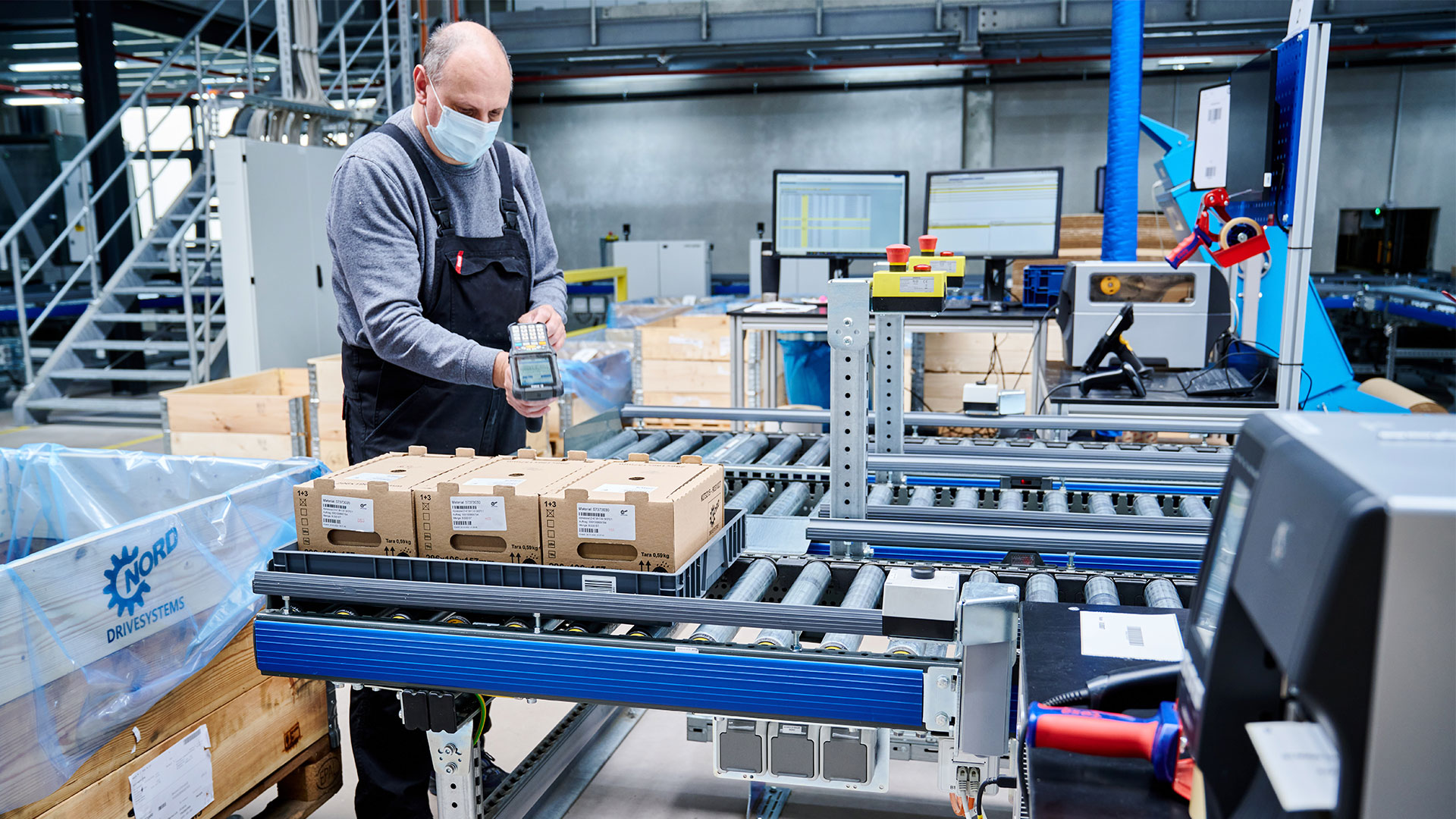
4) Packing and shipping
When the orders are ready for shipping, the pre-picked trays are retrieved from the Evo Shuttle and conveyed to the eight pack stations. The orders are assembled, packed and stacked on pallets. The pallets are then transported to the shipping department. Empty trays go back to the empty tray buffer and are supplied to the goods-in area.
With respect to logistics, we see a flexible and international partner in KNAPP, one we can imagine working with on a long-term basis on projects designed to raise the logistics at our other locations to a whole new level.
Jörg Niermann
Head of Marketing, NORD DRIVESYSTEMS
A partnership with a future
Partnership and mutual trust make shared projects a success. As a manufacturer of drive technology, NORD also supplies KNAPP with drive units for their conveyors. At this installation in particular, the teams from KNAPP and NORD worked well together from the start of planning all the way to installation. KNAPP delivered the desired performance in the automated small parts warehouse and after the final project acceptance, the project was transferred to Customer Service for ongoing support.
Find out more about our Customer Service >