Walmart’s Next Generation Fulfillment Centers
Walmart Inc. is a leading omnichannel retailer that relies on state-of-the-art technologies to offer the optimal customer experience.
Rising demand in e-commerce as well as the need to improve efficiency along the entire supply chain led Walmart to embark with us on a transformational mission. The aim was nothing less than to bring about revolutionary change to the company’s distribution centers.
Together, we have already built 4 of these ultra-modern fulfillment centers – the Next Generation Fulfillment Centers – and a fifth is soon to come. The state-of-the-art logistics centers have reduced a process involving 12 steps to just five steps, completely supported by software, which has also significantly improved the user experience for Walmart customers.
You are currently viewing a placeholder content from YouTube. To access the actual content, click the button below. Please note that doing so will share data with third-party providers.
More InformationKNAPP helps us to deliver everyday low costs so that we can deliver everyday low prices for our customers.
David Guggina
EVP, Chief eCommerce Officer, Walmart
Would you like to re-align your value chain??
Let our experts advise you.
Putting the ultra-modern logistics centers to the test
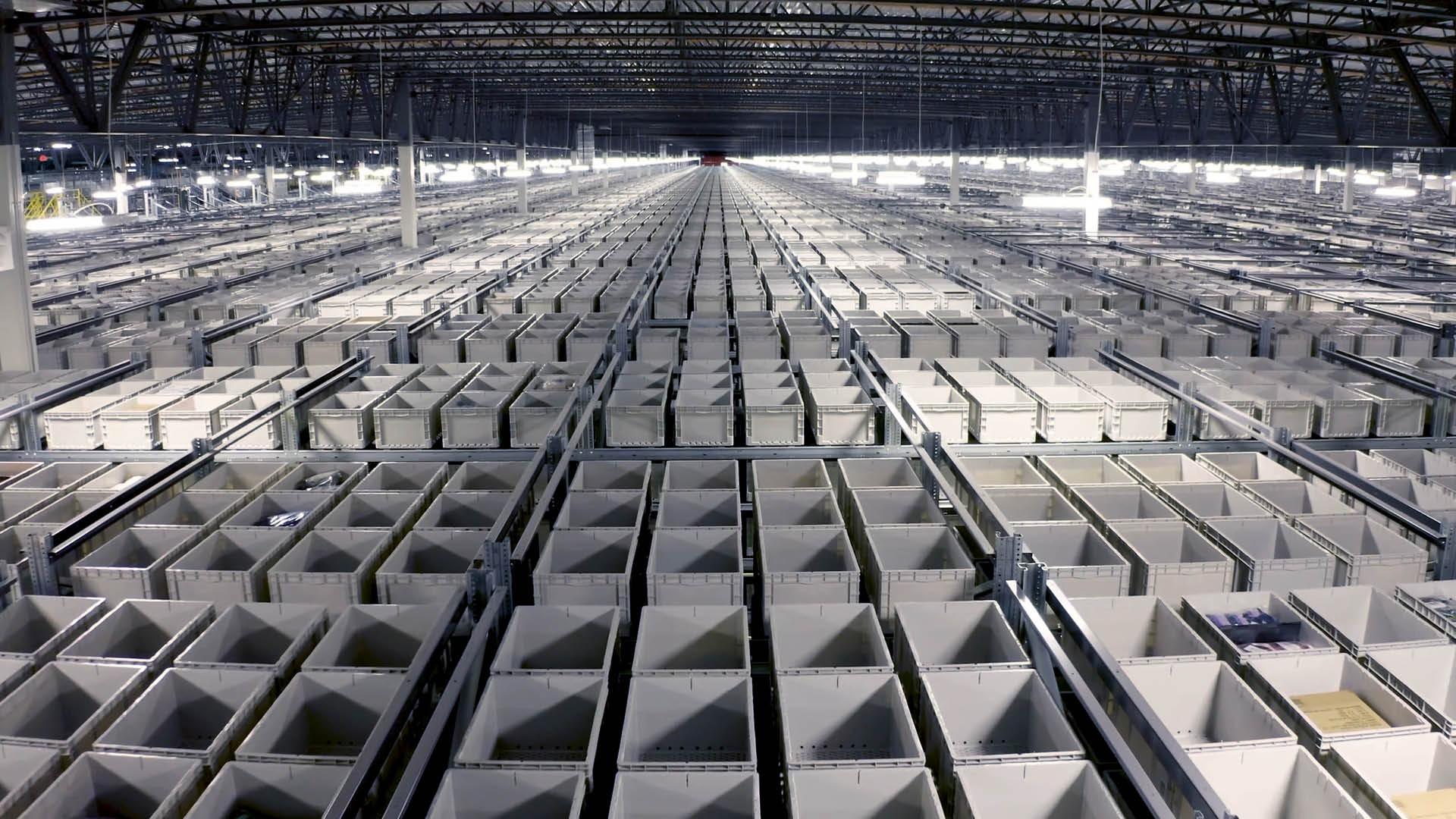
We doubled our storage capacities compared to our traditional fulfillment centers.
David Guggina
EVP, Chief eCommerce Officer, Walmart U.S.
Would you like to re-align your value chain?
Let our experts advise you.
5 central storage processes
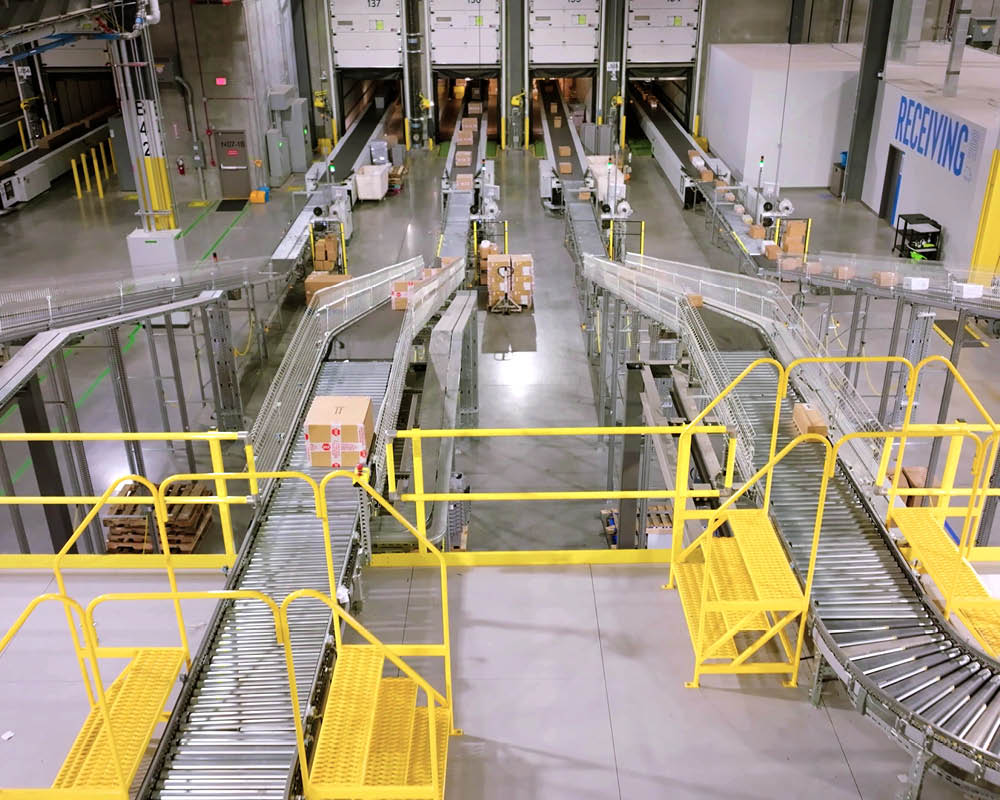
1) Unloading
At Walmart, unloaded cartons are either temporarily stored in the Evo Shuttle 2D automatic storage system or are conveyed directly to the decanting area. On the way, the cartons run through a scan tunnel. Here is where the “auto receive” takes place, automatically accepting delivery of the cartons. The process includes registering the weight, dimensions and labels of every carton.
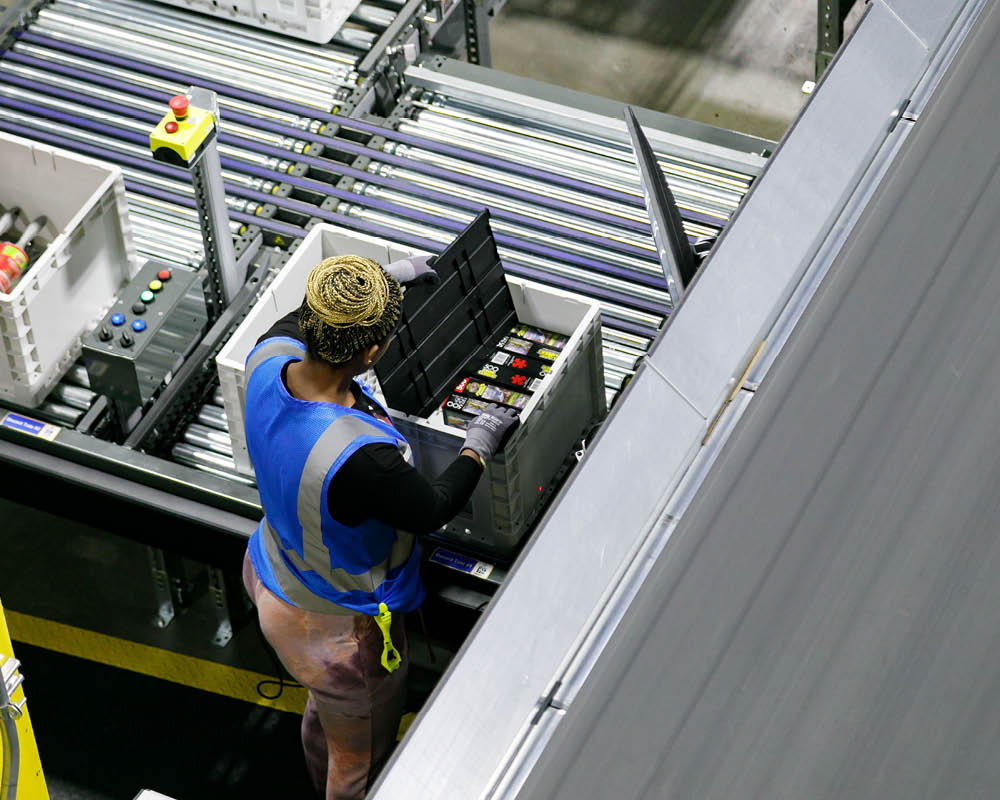
2) Decanting and putaway
Employees working at the decanting stations empty the cartons arriving there and transfer the items to a storage container. Several container configurations are available. These newly filled storage containers move along a conveyor belt towards the Evo Shuttle 2D automatic storage system, where they enter storage. One of the system’s shuttles takes up the container and transports it to one of the million storage locations within the system. The shuttle storage system was designed to be especially compact, utilizing the entire height of the hall to ensure optimal storage density.
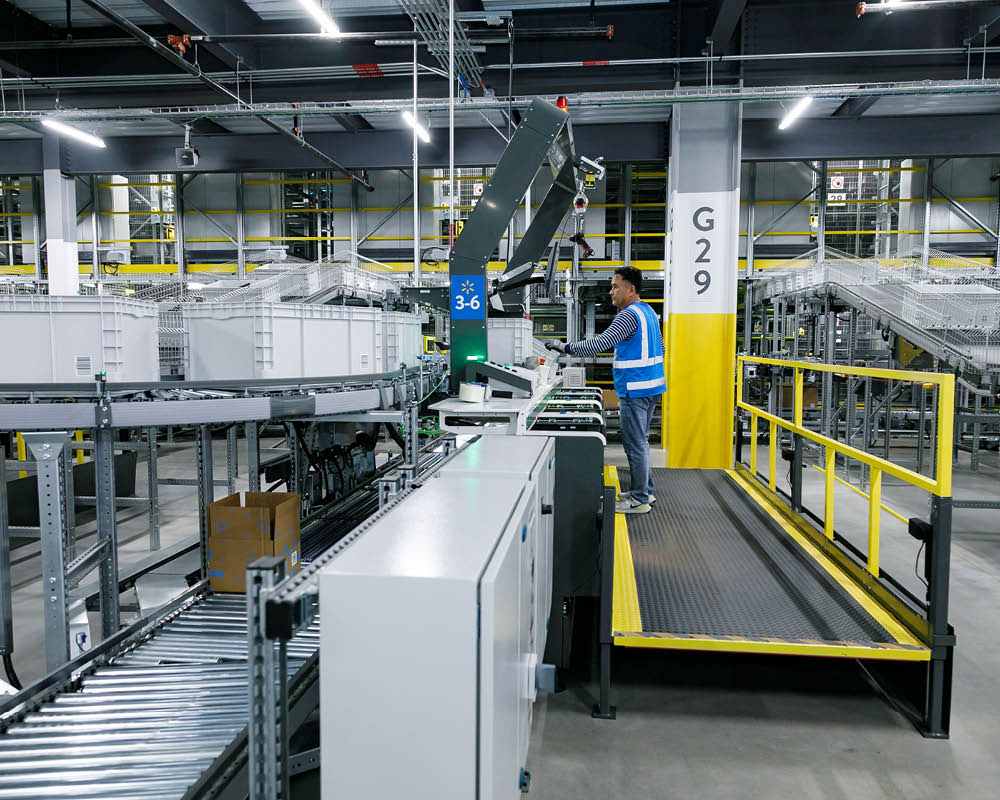
3) Picking
As soon as a customer order comes in, the source container is automatically retrieved from the Evo Shuttle 2D, transported to a lift and then on to one of the goods-to-person work stations of the Pick-it-Easy Evo series. Employees pick the order at one of the ergonomic, height-adjustable work stations. Here, 4 orders can be processed at the same time. If the order will not be shipped in a carton, it is initially picked into a container.
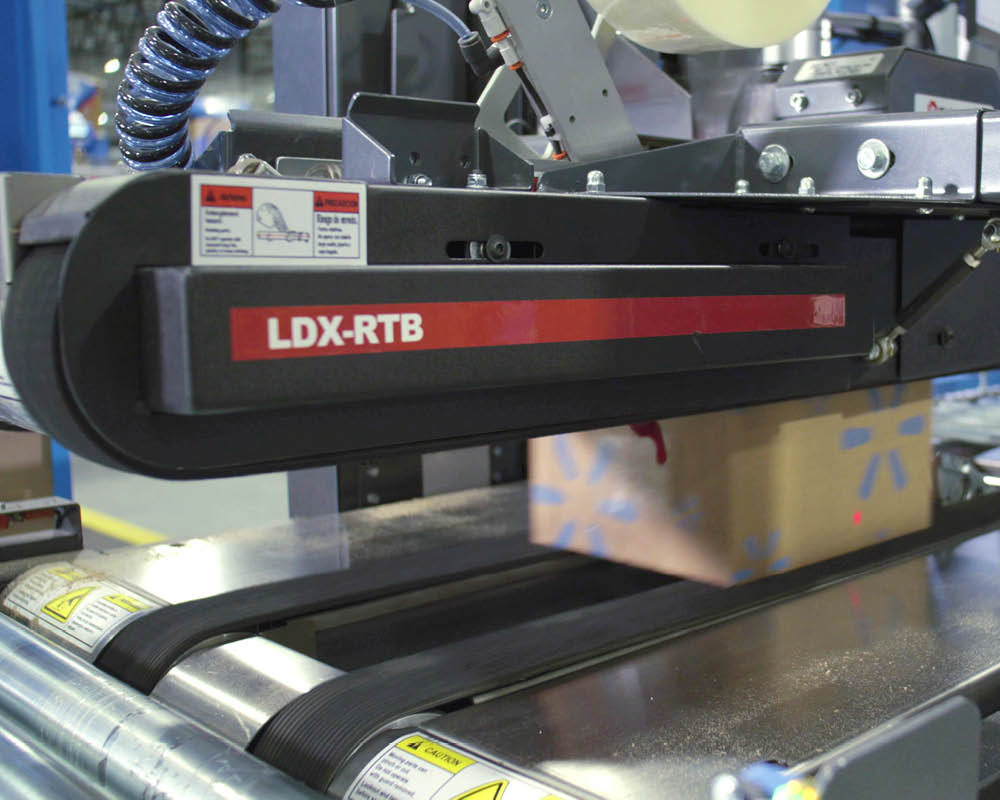
4) Packing
Orders that are picked to containers at the goods-to-person work stations are transported to the pack stations. Picked in batches, the orders are placed into the assigned shipping package with filling material to secure them during transport. The completed order is closed with adhesive tape, scanned and weighed, either automatically or semi-automatically, and provided with an address label. This process eliminates repetitive tasks and improves safety while simultaneously increasing speed, efficiency and precision.
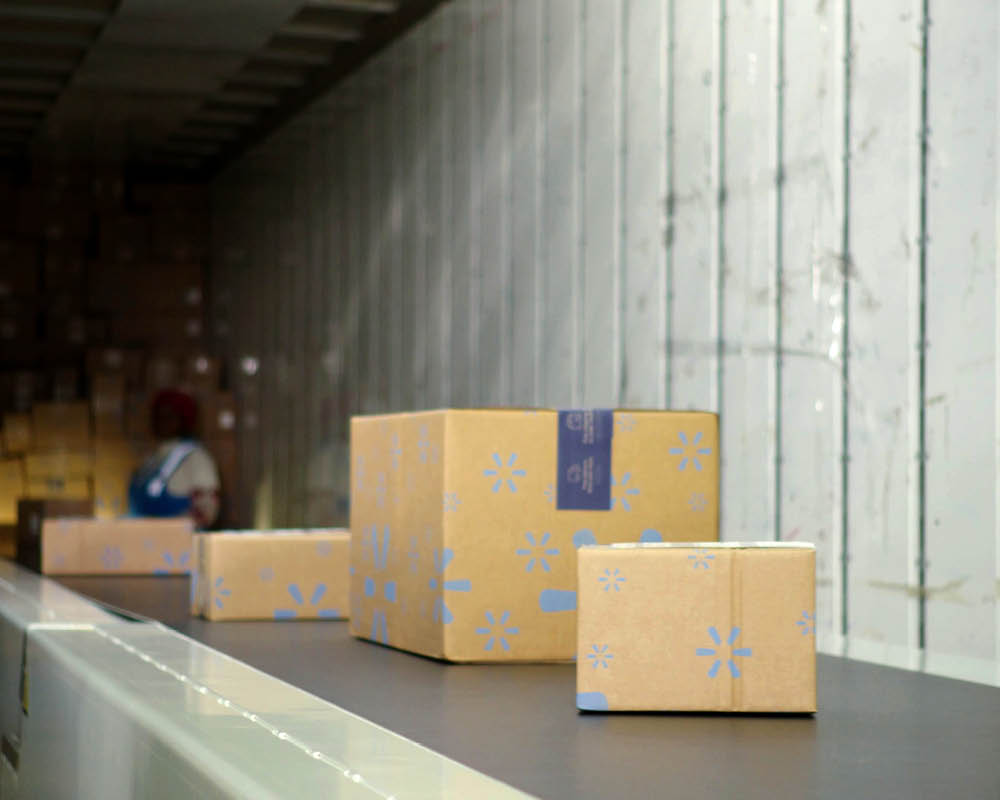
5) Shipping
Once packing is completed, orders are automatically transported to the assigned zone and loaded onto vehicles that handle the last mile for the deliveries, either from Walmart transport services or a 3PL.
Customized shuttle solution for maximum storage capacity
million storage locations per warehouse
times more SKUs
One central focus of the Next Generation Fulfillment Centers is the automated storage and retrieval system, the Evo Shuttle 2D.
The scalable shuttle solutions installed at Walmart are some of the largest of their kind worldwide. One Walmart Next Generation Fulfillment Center offers space for nearly 2 million containers in a custom Evo Shuttle system. The automatic system’s high storage density ensures that Walmart can make optimal use of their available storage space, resulting in space for ten times as many SKUs as in a traditional fulfillment center. The automated storage system allows Walmart to process double the number of customer orders per day, so Walmart can ship items to their customers faster and, at the same time, provide a positive work environment for their employees.
Software and service to order
We also rely on customized software and service solutions to meet Walmart’s individual requirements for its state-of-the-art logistics centers. Our KiSoft suite ensures that all the processes in Walmart’s Next Generation Fulfillment Centers function smoothly and efficiently. Supplementary digital services and our trained KNAPP employees are also always at Walmart’s side.
Other things Walmart relies on: