B&R: Smart Logistics Drives Efficiency in Production
The B&R Industrial Automation GmbH, located in Austria, is a worldwide leading manufacturer of automation solutions and the global center for machine and factory automation for the ABB Group. With a comprehensive portfolio of robotics, control systems and software, the company develops complete solutions that are both efficient and future-proof. Their headquarters in Eggelsberg, Austria, is home to manufacturing, R&D and a modern educational and training center and is one of the largest industrial hubs in central Europe
B&R’s logistics processes in Eggelsberg are highly dynamic and characterized by changing requirements. To be able to flexibly respond to their customers’ requirements, reduce physical strain for employees and increase efficiency, B&R decided to automate their manufacturing and storage processes.
You are currently viewing a placeholder content from YouTube. To access the actual content, click the button below. Please note that doing so will share data with third-party providers.
More InformationFrom the warehouse to production, from goods-in to outbound delivery – automation makes it possible to respond to changes faster and more flexibly while simultaneously becoming more efficient and productive.
Michael Humer
Country Managing Director Sales Austria
B&R Industrial Automation
Curious about warehouse automation?
Contact our experts today.
Efficiency, ergonomics and flexibility thanks to warehouse automation
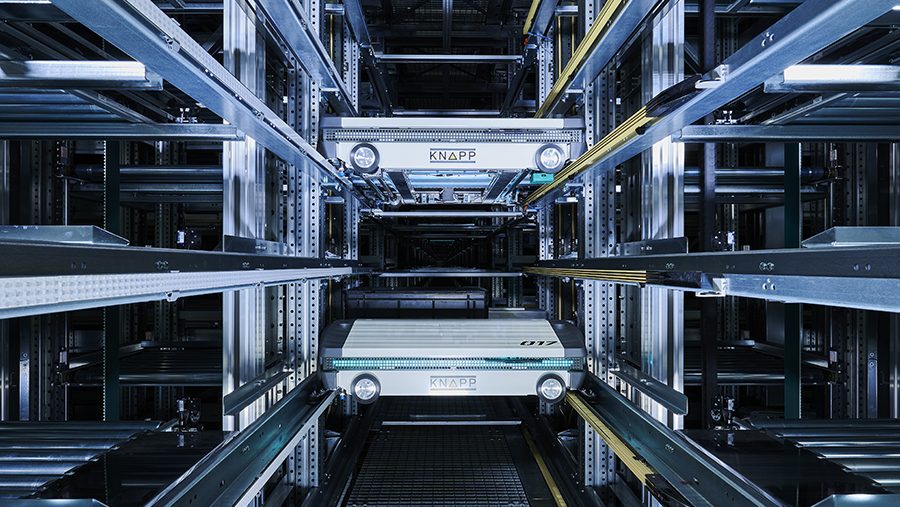
Innovative logistics solution for B&R
The new automation solution really scores with maximum storage density, highly-efficient goods-to-person picking and flexible goods transport. The heart of the system is the automated small parts warehouse Evo Shuttle, which provides high storage density. For ergonomic picking, the connected Pick-it-Easy work stations allow goods-to-person picking and feature Pick-to-Light technology. The decanting work stations in the goods-in area are also connected to the Evo Shuttle as well as the goods-out area by KNAPP’s conveyor system. Our Open Shuttles, a type of autonomous mobile robot (AMR), as well as tugger trains, supply the manufacturing stations based on need. A custom software solution including KiSoft One to intelligently connect all the processes, KiSoft SCADA for visualization and KiSoft FCS for the control of the entire fleet rounds out the all-in-one solution.
The numbers speak for themselves: Thanks to the higher storage density and faster access times, warehouse throughput was increased by 35 % and picking throughput by as much as 50 %.
We chose KNAPP’s automation solution because it gives us clear gains in performance with respect to efficiency and speed and includes greater storage density, faster access to stored materials and an overall increase in throughput at the facility.
Roman Seitweger
Head of Production Austria
B&R Industrial Automation
Seamless processes for production logistics at B&R
01 Goods-in
Goods enter the warehouse on pallets. The goods are separated and repacked into containers at the ergonomic decanting work stations. Once registered in the system, the goods are weighed on an integrated scale before being transferred onto the conveyor system. The conveyor system is suspended from the hall ceiling and conveys the containers to the automated small parts warehouse. Mounting the conveyor system to the ceiling left space free in the hall.
02 Storage
The Evo Shuttle provides dynamic, precise storage for small parts. The system has 91,622 storage locations for three different heights of containers. For optimal storage density, the shortest containers are stored stacked. A special stacker/destacker station with integrated measurement technology was developed especially for this solution. Its purpose is to ensure these containers are stacked or separated fully automatically during the storage and retrieval processes.
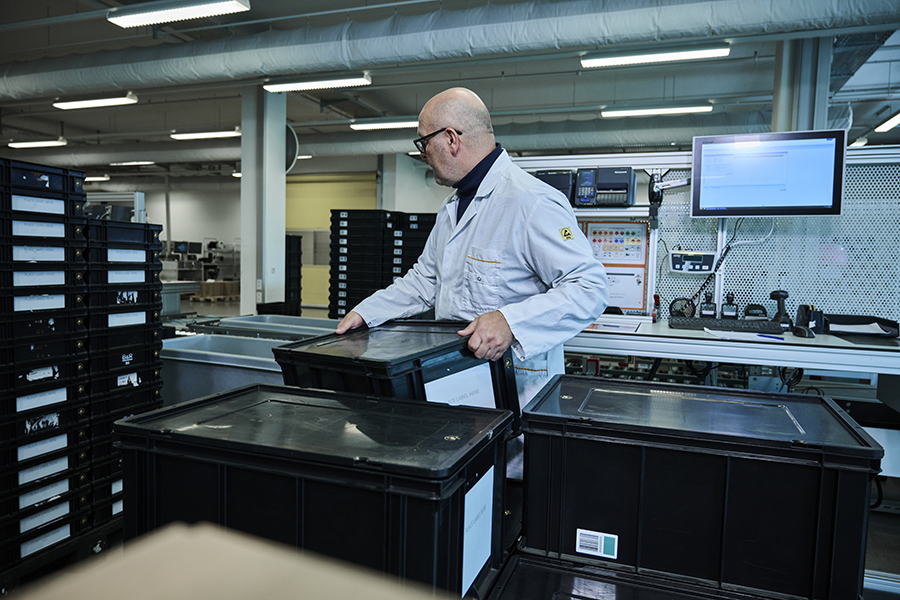
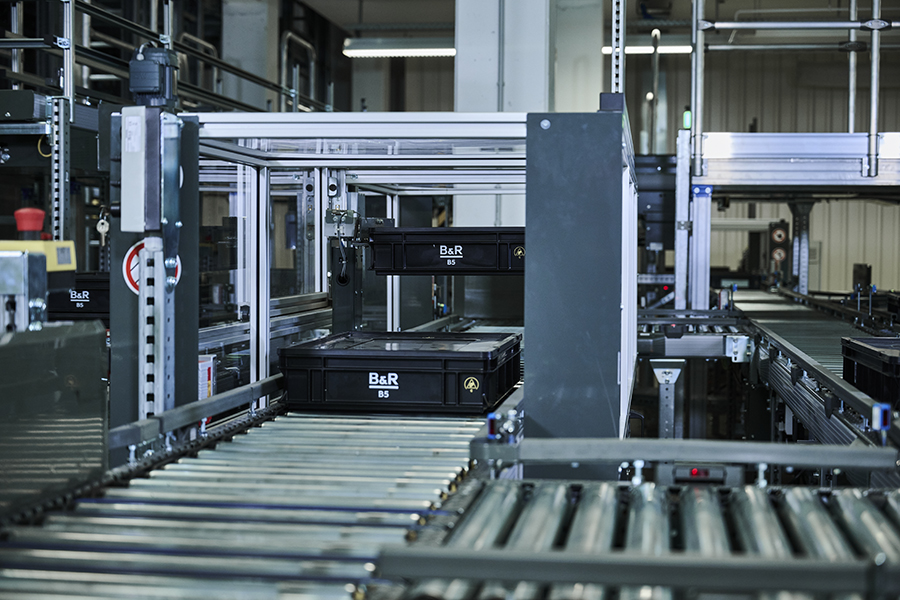
03 Picking
Goods are picked for either manufacturing or shipping at one of the four ergonomic Pick-it-Easy work stations. The required components are supplied to the work stations from the shuttle warehouse according to the goods-to-person principle. Both kits for manufacturing and orders for shipping are picked and buffered in the Evo Shuttle. Fast moving components are picked at kanban racks equipped with Pick-to-Light displays.
04 Retrieval of goods
After a shipping or manufacturing order is completed, the containers are retrieved from the Evo Shuttle via the conveyor. Whole orders are processed by employees and placed on the respective order pallet which is then picked up by a tugger train. Individual containers with components for manufacturing are supplied to the transfer position for the Open Shuttles. The software generates the transport orders for the autonomous mobile robots.
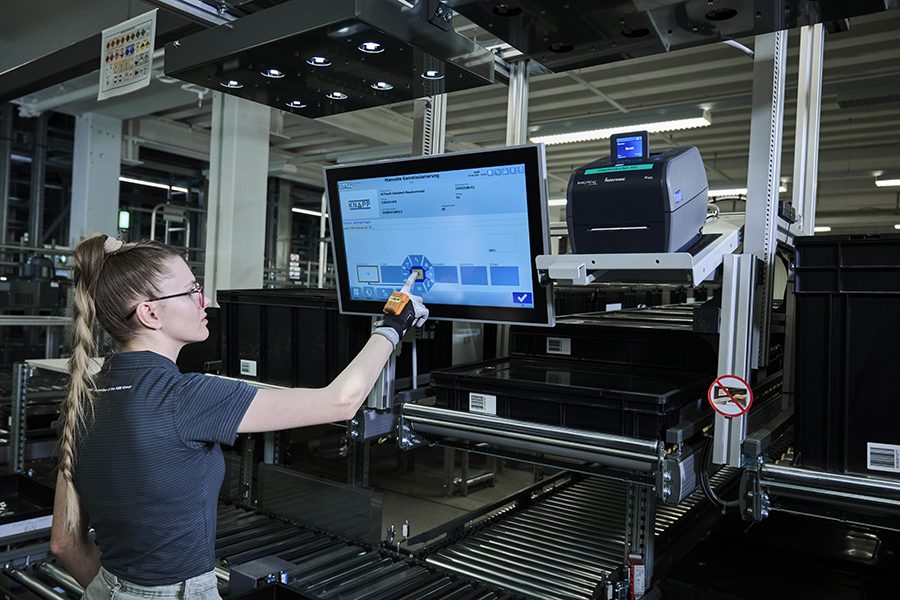
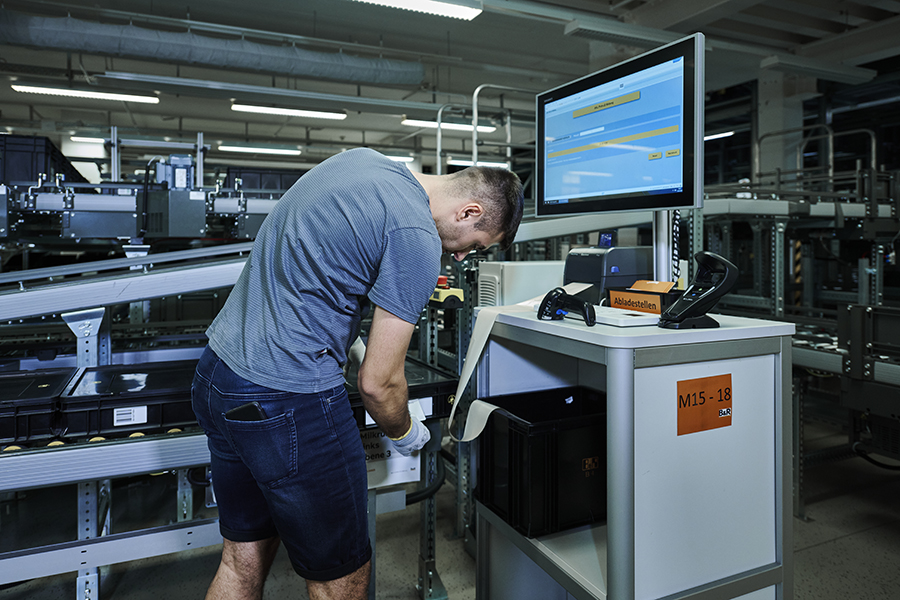
05 Supply to manufacturing
Tugger trains and Open Shuttles connect the automatic small parts warehouse seamlessly with the manufacturing lines. The AMRs transport containers with components to manufacturing, placing them on a conveyor for the employee. Empty containers and finished parts are picked up by the Open Shuttles and transported back to the Evo Shuttle for temporary storage.
06 Shipping
Tugger trains pick up pallets from the goods retrieval area at the small parts warehouse and transport them to the packaging area. The completed orders are packed into cartons and shipped. Empty containers are then returned to the shuttle system and stored.
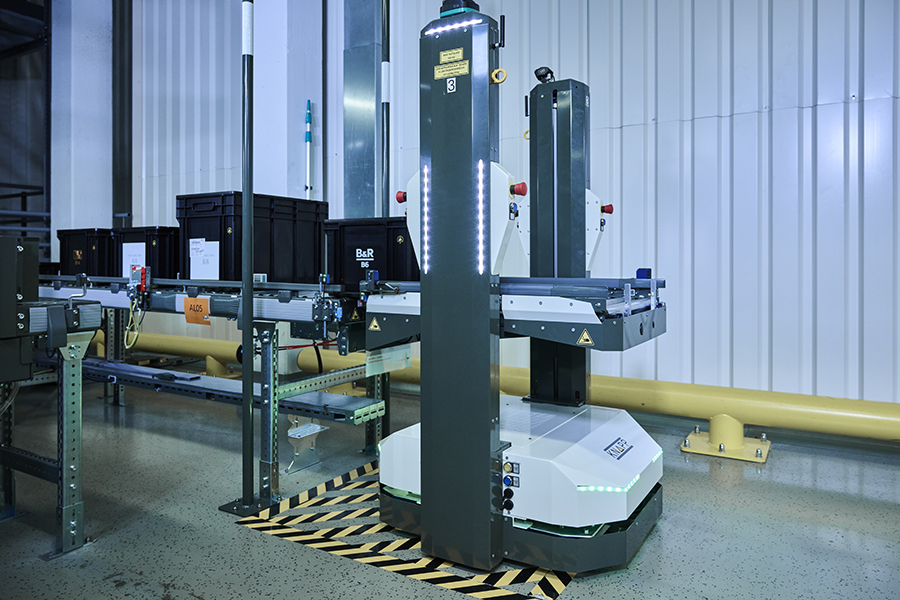
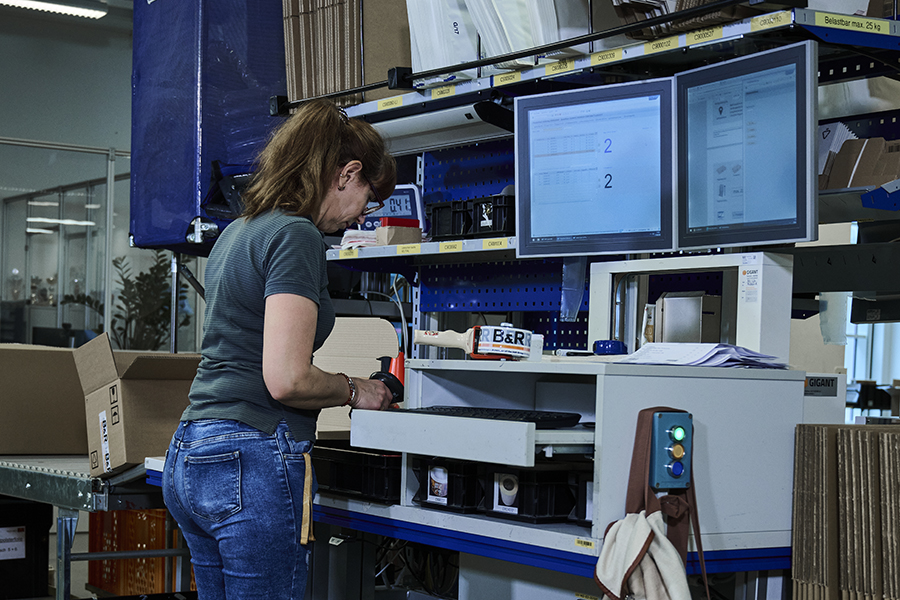
storage locations
shuttles
storage and retrieval movements/hour
order lines/day in picking
Smart factory with intelligent software and complete service
B&R and KNAPP: Strong partners for innovative solutions
Although B&R and KNAPP began in a classic customer-supplier relationship, it developed into a strategic partnership. In Eggelsberg, they rely on our high-tech logistics system, while the control systems from B&R form an integral part of our autonomous mobile robots. This reciprocal partnership underlines the technical competence of both companies and demonstrates how shared know-how leads to success. In the future, the partnership will be expanded by integrating the adjacent processes into the automation solution.
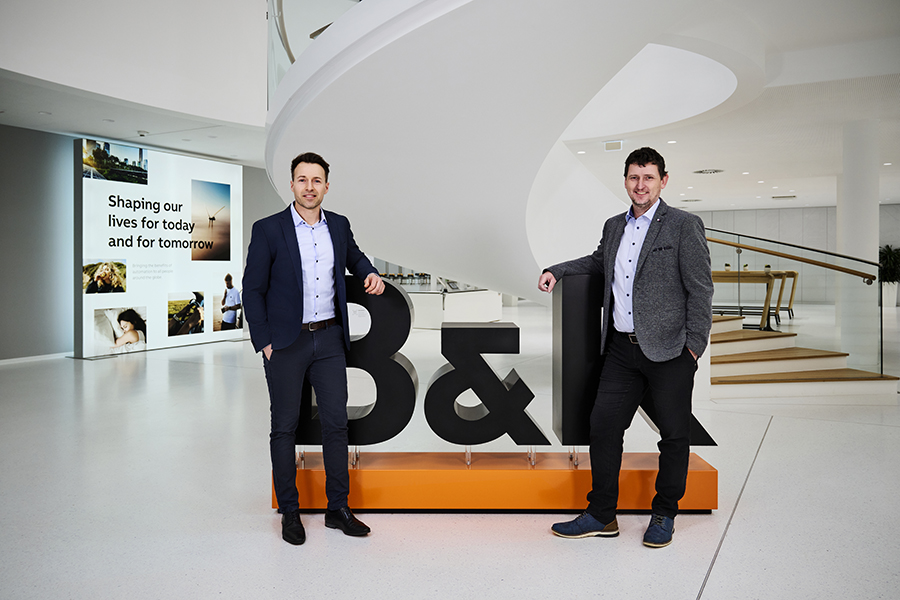
Automating our intralogistics has made our internal processes a lot more efficient. Now we’re working to seamlessly integrate adjacent processes, such as manufacturing control, replenishment processes and packing.
Michael Humer
Country Managing Director Sales Austria
B&R Industrial Automation