Steady growth at Würth Austria meant that the company had reached the limits of their existing resources. The project was characterized by partnership, resulting in a modern, innovative expansion that harmonized the ecologic, social and economic aspects.
For many years, KNAPP has been our go-to partner when it comes to new logistics solutions. Together, we were able to develop a future-proof solution. Our order fulfilment is now more efficient and productive than ever. We are now well prepared for future requirements.
New orientation for sustainability
One important aspect of the modernization was to reduce the environmental impact of the site. We rely on technologies and processes providing environmentally friendly order processing, with optimal quality.
Decanting and order start
The goods must always be ready at hand; therefore, the goods move straight from decanting to storage in the shuttle system. At the start of an order, a shipping carton is set up for it by an automatic carton erector. Reusable containers are used for in-company deliveries at Würth. Routing labels allocate cartons and containers to specific customers. This label is important for internal transport within the warehouse and for other processes in the warehouse.
Productivity and Ergonomic design
When it comes to picking, the latest shuttle generation for the OSR Shuttle™ Evo and the innovative Pick-it-Easy Evo work station combine maximum efficiency and productivity in an ergonomic design.
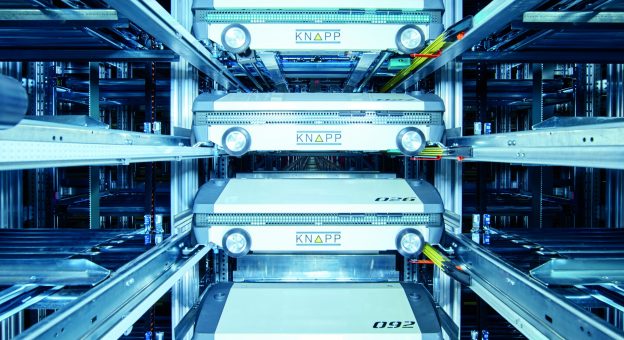
Efficient processes thanks to dynamic storage
The OSR Shuttle™ Evo supplies the connected Pick-it-Easy work stations with goods just in time. Every work station has access to every article in the system. Available space is optimally used thanks to the flexible rack system and streamlined design. The OSR Shuttle™ Evo is designed for future expansion. The number of shuttles and lifts can be scaled to adapt the system performance to any given requirements. The shuttle system provides storage locations for around 57,000 cartons in 3 rack lines with 41 levels. Aside from storage containers, completed dispatch cartons are also temporarily stored in the racks until they are ready to be dispatched. Over 100 shuttles constantly take the containers and cartons wherever they are needed – the OSR Shuttle™ Evo supplies the connected Pick-it-Easy Evo work stations and the dispatch robots flexibly and in the correct sequence.
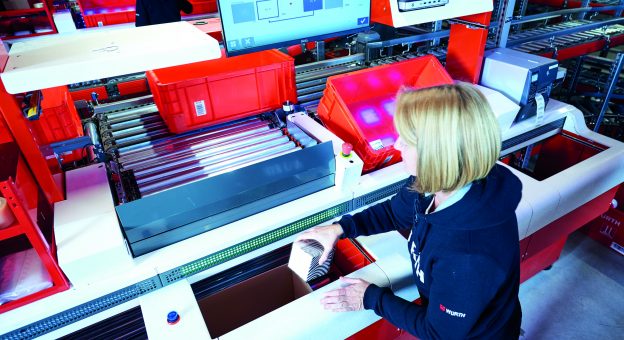
Pleasant working conditions thanks to ergonomics
Würth takes its social responsibility towards its 300 employees at the location very seriously. For this concern, we had the ideal answer: Our Pick-it-Easy Evo work stations. Orders are filled at six all-in-one work stations. Our OSR Shuttle™ Evo supplies the work stations with goods just in time. The goods come to the employee at the work station at the right time and in the right sequence. This reduces walking for the employee and significantly increases productivity and picking quality. At the Pick-it-Easy Evo work stations, the employees work intuitively and accurately.
User-friendliness and ergonomics are a further plus offered by the goods-to-person work stations. Employees working on site feel supported and motivated in their daily work, experiencing a new way of working. LED displays and touch screens with intuitive easyUse user interfaces and add-ons for quality assurance create a one-of-a-kind user experience.
Quality checks and shipping preparation
Before completed customer orders are dispatched, they go through several stations for quality checks to guarantee an error-free delivery and to increase customer satisfaction.
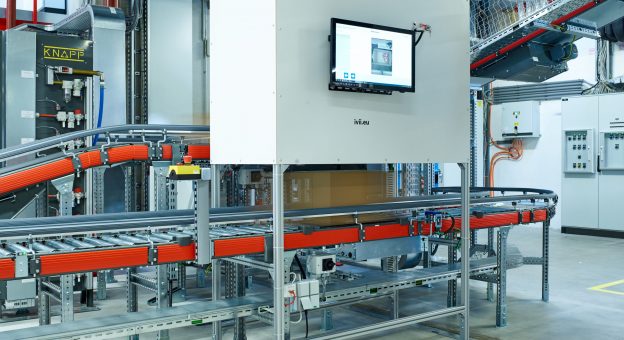
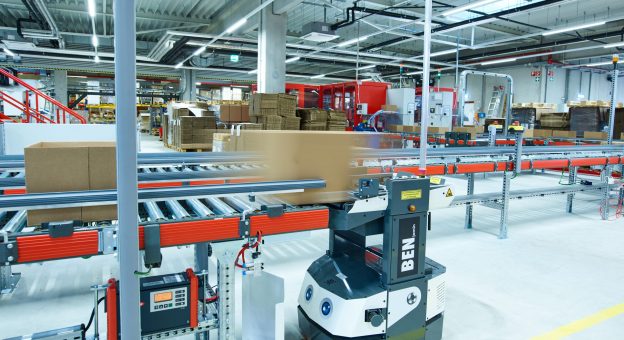
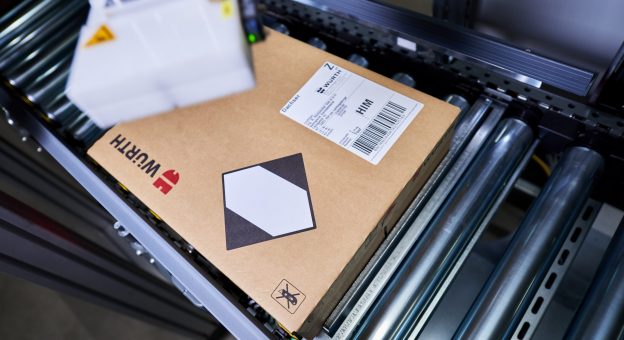
ivii.photostation
The pattern in which the cartons are arranged on the pallet is checked by an innovative image recognition technology. Any spaces are detected, then filled with biodegradable air pillows made from potato and corn starch. These are made of 100 percent renewable materials. This cushioning reduces possible damage as well as environmental impact through returns and double deliveries.
Open Shuttle
Cartons for which deviations were detected during weight check are transferred to a check station for further checks. The Open Shuttle picks up the cartons to be checked from the dispatch lane and brings them to the check station, relieving employees both from walking times and physical strain.
Folding and lidding
After the quality checks, the dispatch cartons are ready to be palletized and delivered to customers. The delivery note is inserted automatically and the cartons are then conveyed to the fully-automatic folding and lidding machines. The folding machine checks the height of the content and reduces the height of the carton to a minimum by using a special folding mechanism. Reducing the carton size in this way saves considerable space on the pallet and subsequently in the vehicle. After folding, the cartons are provided with a lid fully automatically.
Fully-automatic palletizing and dispatch
The new solution also includes 2 dispatch robots which take over the heavy labour. The articulated arm robots palletize the cartons and reusable containers fully automatically, thereby freeing the employees for vital but less strenuous tasks. Each robot works with 8 dispatch pallets simultaneously. They build the pallets space-effectively and in the correct sequence. Up to 7,000 packages per hour are placed on dispatch pallets which then go out to customers all across Austria. The new expansion has reduced the volume of shipping cartons. Using reusable packaging additionally saves 20 metric tons of plastic film per year.
In this video we present our solution at Würth Austria in detail.
https://www.youtube.com/watch?v=xgysJ_4XtXY
Further reading recommendations

As innovators, the continual development of our products is essential. This is how we remain strong and reliable partners for our customers worldwide.

In this challenging situation, how can we support KNAPP customers with proactive service? What advantages do targeted data analyses, service platforms and remote communication provide?

Together with our customers, we grow with every challenge, we keep improving and we keep boosting our know-how because “if you always do what you’ve always done, you’ll always get what you’ve always got”.
Mario Rauch tells us how we shape our work on a project with this positive attitude and together overcome challenges.
Additional Information
For more information on our logistic solutions, please write to us at blog@knapp.com.