When optimizing the entire logistics operation of a business, the supply chain is often the center of attention. But might it be better to focus on the value chain? And what is the real difference between value chain and supply chain?
Let’s start with the value chain: The value chain includes all business activities that create customer value. The more the sum of these activities meets a demand, the higher the customer value.
These activities include the exchange of material and immaterial goods, which are handled along the supply chain. The more efficient the exchange of goods, the higher their availability. And because the exchange of goods increases customer value, the supply chain is part of the value chain.
From the perspective of a supply chain manager, head of logistics or operations director, what makes more sense: optimizing the supply chain or the value chain? We did some research to find out. Check out the results!
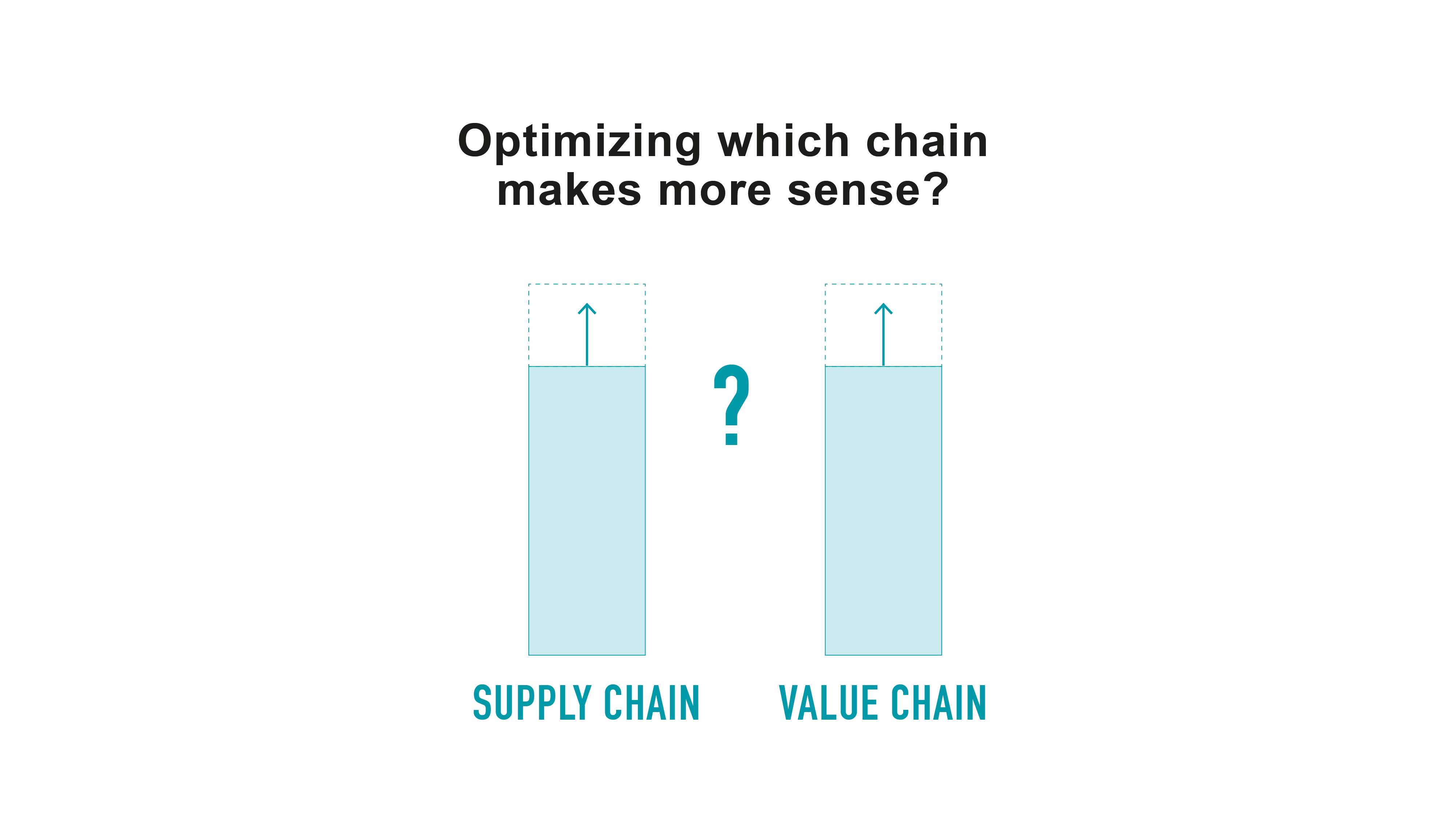
What is the supply chain?
The supply chain starts with the first step of production and ends with the product’s arrival at the customer’s door. Along this way, there are many points where material and immaterial goods are exchanged, such as raw materials, products, services, information and money.
A classic version of a supply chain covers goods exchange across production, distribution and the point of sale including the last mile.
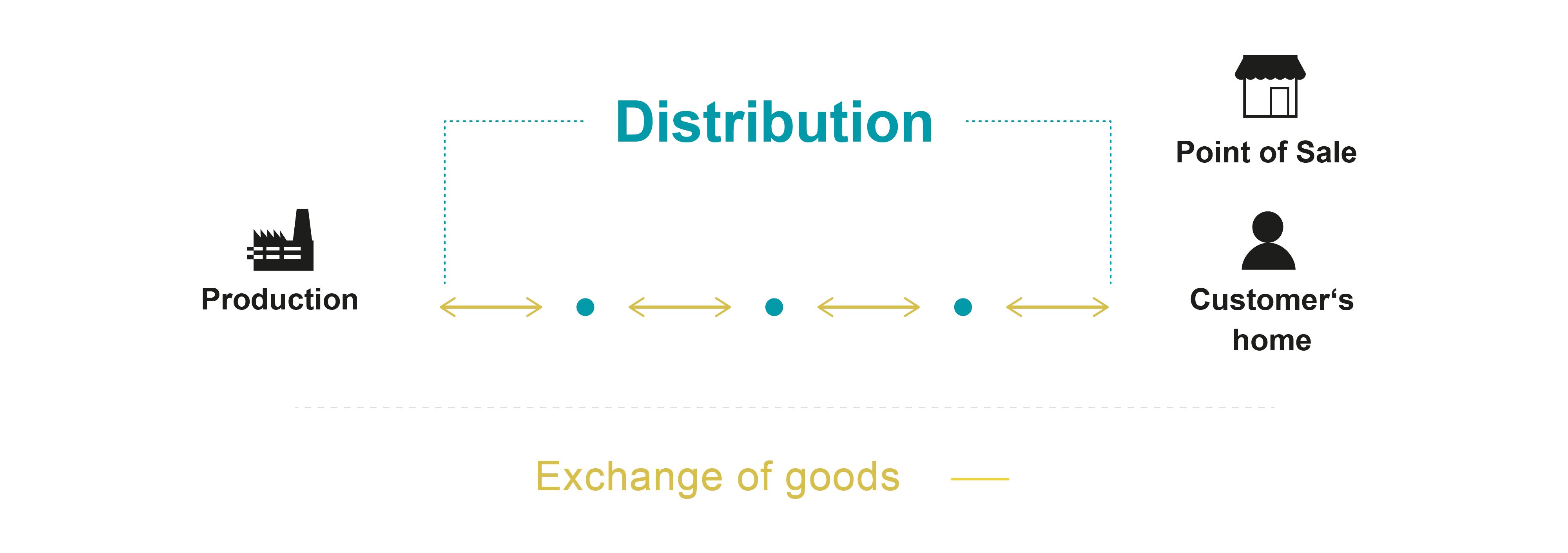
Example: a customer buys a computer
Many things are traded until a customer has their computer in their hands. First, raw materials are mined and processed to be assembled into computers. From central warehouses, they are shipped to stores or directly to the customer.
To ensure that the computer reaches the customer without delay, information about delivery times and available stock are exchanged as well as information pertaining to payment. After-sale services such as repairs are also part of the supply chain.
The goal: to make the exchange of goods as efficient as possible
Supply chain management focuses on achieving the utmost efficiency in the exchange of goods. It’s all about costs, quality, and time (e.g. delivery) involved in the trade of goods. When optimizing the supply chain, the goal is to improve one of these aspects individually, or several in combination. For example, providing better quality at a better price with faster delivery.
What is the value chain?
As with the supply chain, the value chain starts with production and ends with the customer. Along the value chain are points of intersection with the supply chain and nodes where customer value is created. These nodes can be companies, locations, people or computers. The value chain includes all activities involved in creating value, forming a network.
Example: a customer buys a new computer
A customer wants a new computer and is watching out for these three things: They need a computer with a fast processor because they want to edit videos. They need the computer as soon as possible for work, and naturally have a certain price in mind.
If the computer manufacturer wants to convince this customer to buy their product, they have to tailor their business activities to the customer’s expectations in order to generate maximum customer value. This means the manufacturer has to offer a computer with a fast processor that is available quickly and for an affordable price.
Besides key activities such as production and marketing, many other activities generate value for the customer. For example, the manufacturer may offer a service package together with the new computer, so that the customer doesn’t have to worry about where to go for repairs.
The goal: to add value for the customer
Value chain management also has a clear target: to generate added value. However, there are various influencing variables, such as trends, the overall state of the economy, influencers and the weather. When optimizing the value chain, the goal is to increase the customer value. Ideally, the product has a USP that gives the company a competitive edge.
The value chain is not only a network covering all business activities but companies have their own value chains too, which can be explained and depicted using Michael E. Porter’s value chain model. Porter’s model breaks down the value chain into primary and supporting activities. The five primary activities – inbound logistics, operations, outbound logistics, marketing and sales, and service – generate value directly, while supporting activities enable a company to perform their primary activities. The fact that inbound and outbound logistics play a deciding role in Porter’s model shows that the exchange of goods is essential for generating customer value.
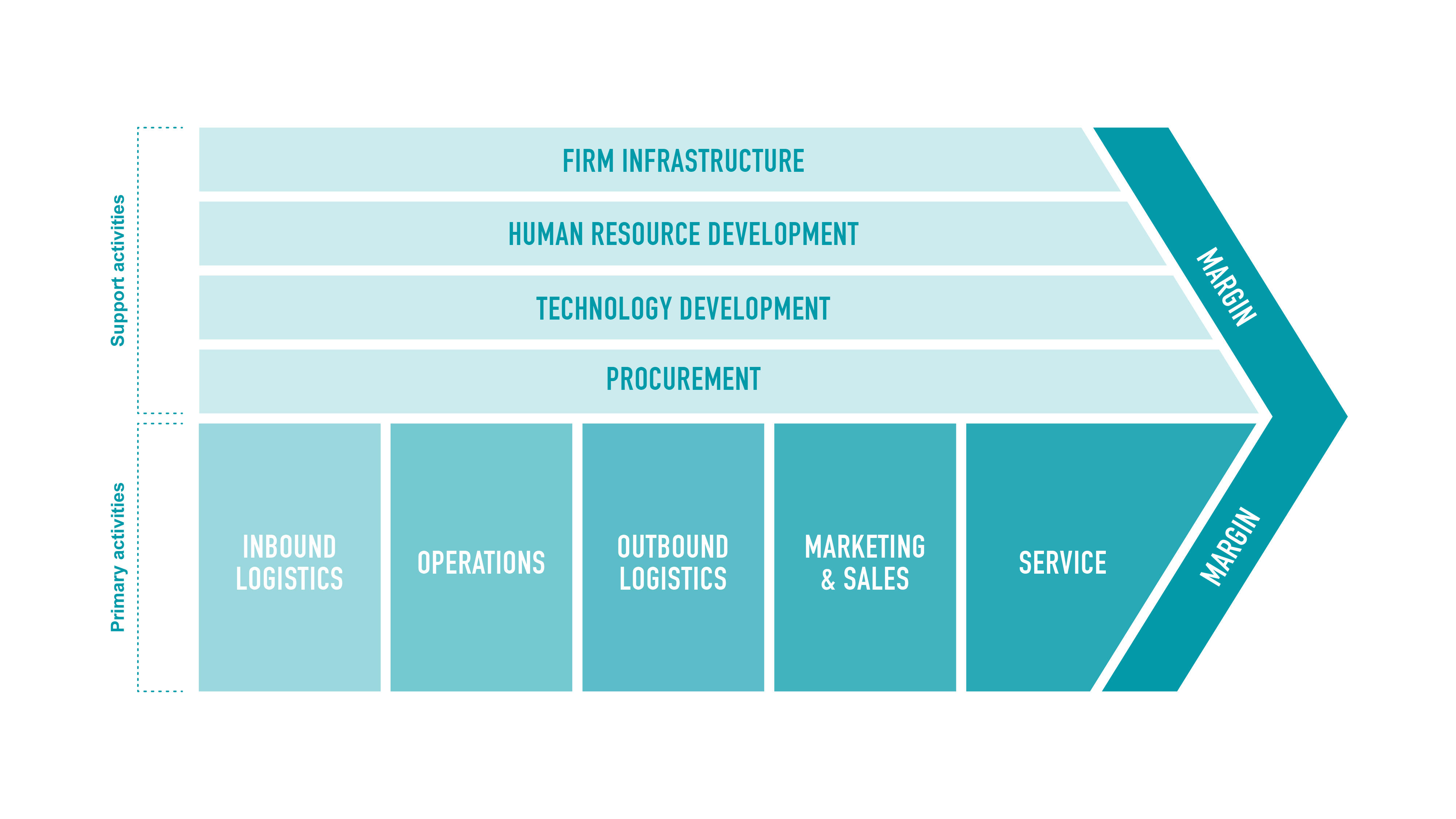
Supply chain vs value chain – the difference at a glance
The value chain is a network of activities stretching from production to the end customer that generates customer value. The key question is: How and why is something done? Customer value is created across the many nodes and interconnections in this network. Ideally, the sum of these values, collectively often called “value proposition”, gives companies an advantage over competitors.
The supply chain controls the exchange of goods between the interfaces and ensures the availability of material and immaterial elements. The key question is: What is being exchanged and how? And because the exchange of goods also increases customer value, the supply chain is part of the value chain.
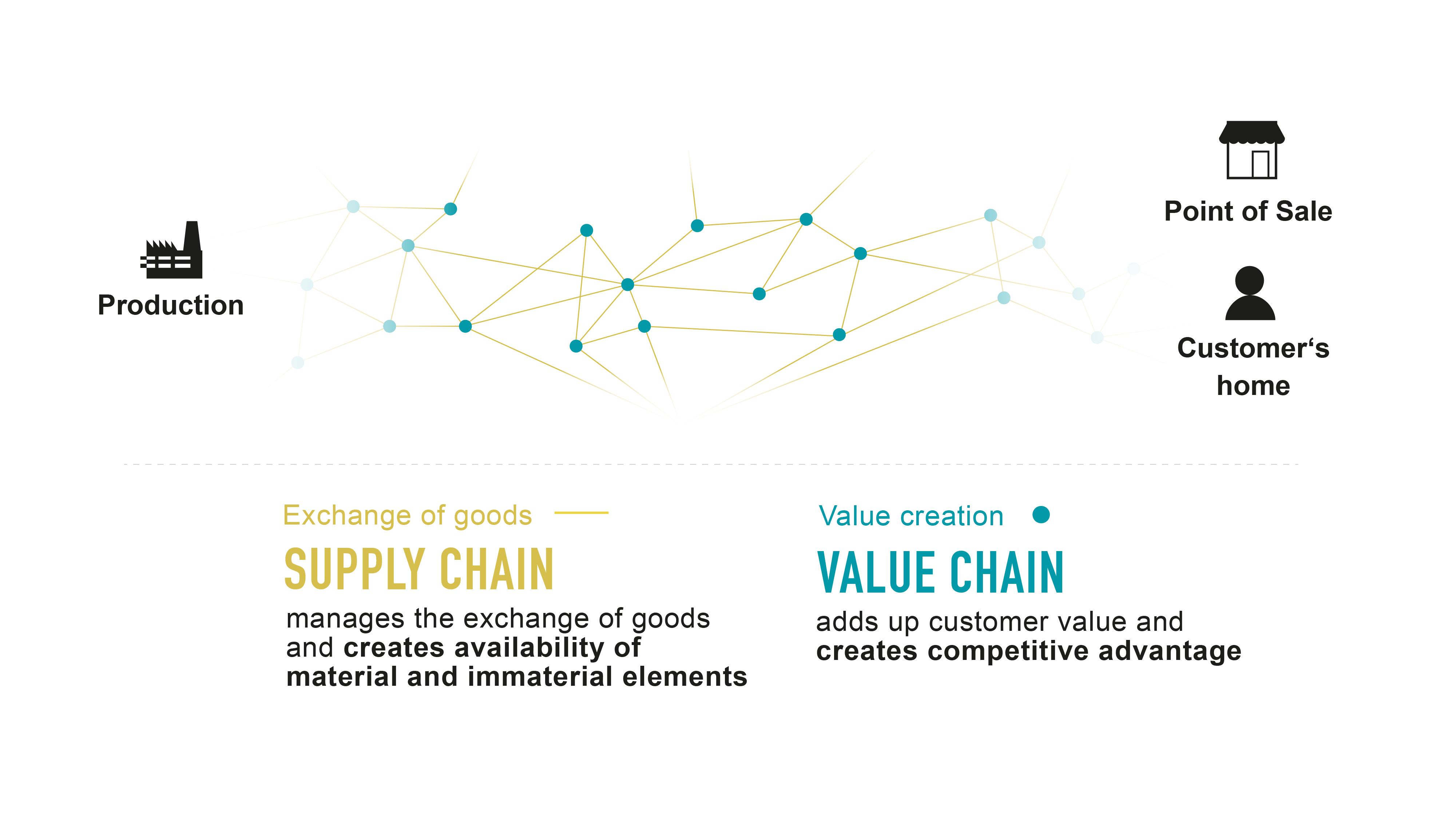
Here is another direct comparison:

The bottom line: thinking in value chains opens up new opportunities for optimization
As we have learned, the value chain focuses on all activities – whether material or immaterial – that create customer value. When comparing classic supply chain models with the value chain approach, it quickly becomes clear that thinking in supply chains is only half the story. The problem is that many supply chain models neglect that value can be created from immaterial processes too. The reason why these models have nevertheless been so successful is that, in the last decades, customer value has been generated through production and efficient distribution. However, recently, there has been a fundamental shift towards the importance of information as an immaterial customer value.
Customers want to buy products that match their lifestyle and solve a problem they have. They want to know as much as possible about the product, have the possibility to engage and be included in the process. To achieve this, companies and customers have to share a lot of information, which has an effect on production and distribution. This requires new ways of thinking.
Thinking in value chains, for example, means focusing on the customer and allows businesses to reinvent processes and products. Let’s take returns as an example: Instead of trying to handle returns as efficiently as possible (supply chain approach), you can offer better consultation at the point of sale to minimize or avoid returns in the first place (value chain approach). The value chain approach is also useful for assessing demand by analyzing customer behavior and weather forecasts. What’s more: These two examples would also be good news for the environment. Digitalization also makes a significant contribution here.
Viewing things from a value chain perspective, helps companies become more resilient. The value chain is like a blueprint for generating customer value. It holds the information on why a product is developed and how. Even if manufacturers or suppliers have to screech to a halt due to unexpected events such as natural disasters, pandemics or war, this blueprint remains. Companies can form partnerships with new businesses, making their value chains more robust.
So, there’s a clear winner in this comparison: Thinking in value chains means thinking about business activities as a whole and opens up many opportunities for designing and optimizing technologies, business models and skills.
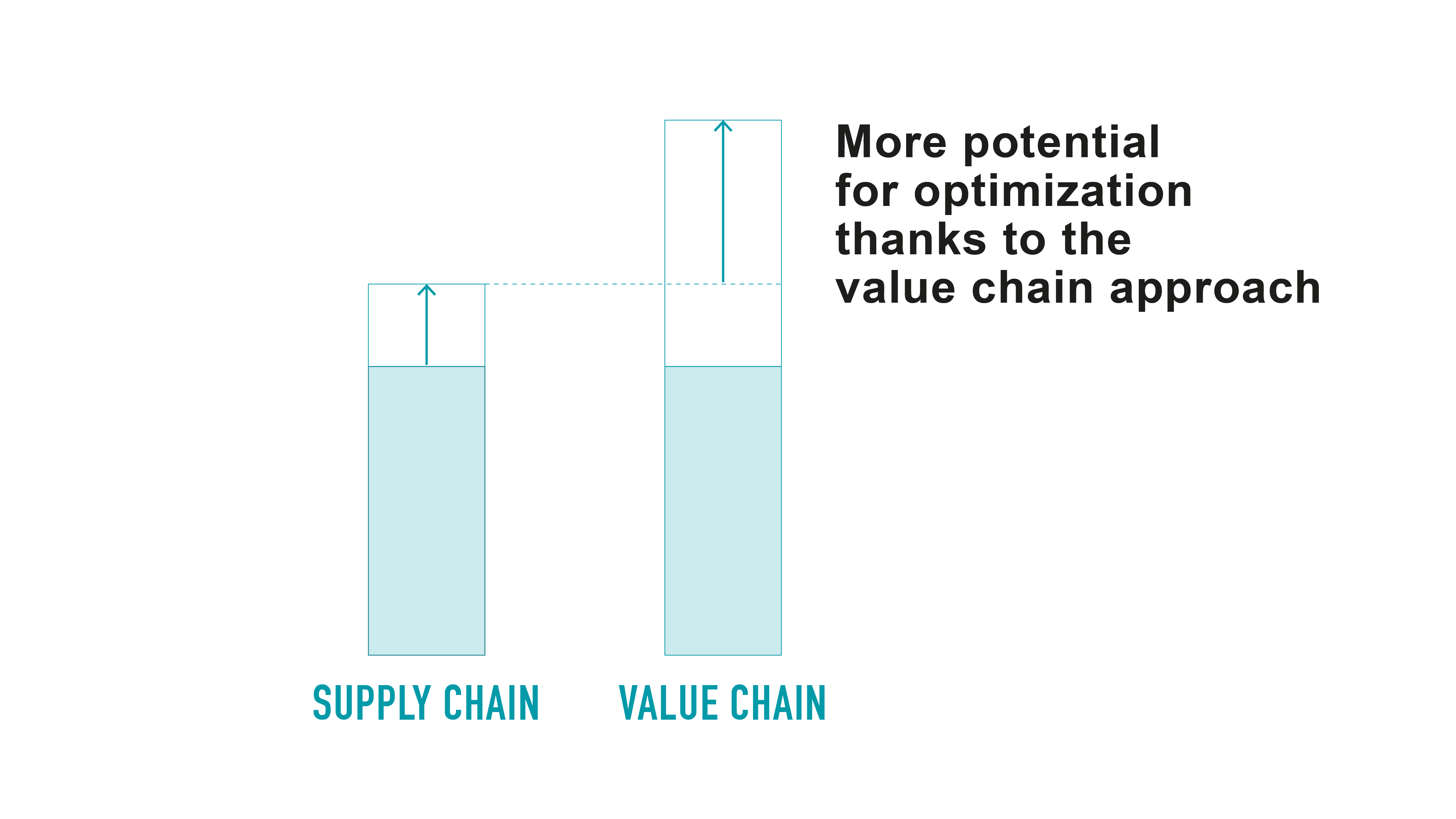
At KNAPP, we feel right at home in this new world of possibilities. As a value chain tech partner, we strive to harness the full potential of value chains together with our customers, helping them boost their success.
Interested in optimizing your value chain? Get in touch with us!
Further reading recommendations

For healthcare, textiles and fashion, retail, e-commerce and omnichannel retail, food retail and production, we offer flexible and creative solutions for the last mile. Our intelligent software works behind the scenes to keep things running smoothly. Together with our customers, we optimize their value chains.

Logistics strategies have become increasingly important in the past years. They often determine the success of companies, or lack thereof. The most important factors are the right positioning, the design of the logistics network and automation. A bottom-up integration into the software landscape can amplify these factors.

Data and information play a vital role in logistics. Real added value is generated along the entire value creation chain by intelligently integrating information and automated systems.