The requirements placed on production facilities today are immense. Costs should be cut, but not at the expense of productivity, which should be increased. At the same time, the required quality standards should be achieved.
KNAPP offers a range of different solutions for digitalizing the production industry. One of them is the ivii.smartdesk, a state-of-the-art work station for digitalizing manual processes. Work at the ivii.smartdesk involves a zero-error strategy and quality check for production, goods-in and goods-out procedures. What’s more, this work station is a great tool to mitigate the shortage of qualified personnel as it digitizes expert knowledge.
ivii.smartdesk wins Best Product of 2021 award at LogiMAT
This year, the perhaps most sought after prize in the intralogistics sector was again awarded during the LogiMAT.digital trade show. The prize is awarded to the winners by an independent jury, which includes representatives from business, science and the media. Today, we can proudly announce that our cutting-edge ivii.smartdesk work station has been selected as the best product of 2021.
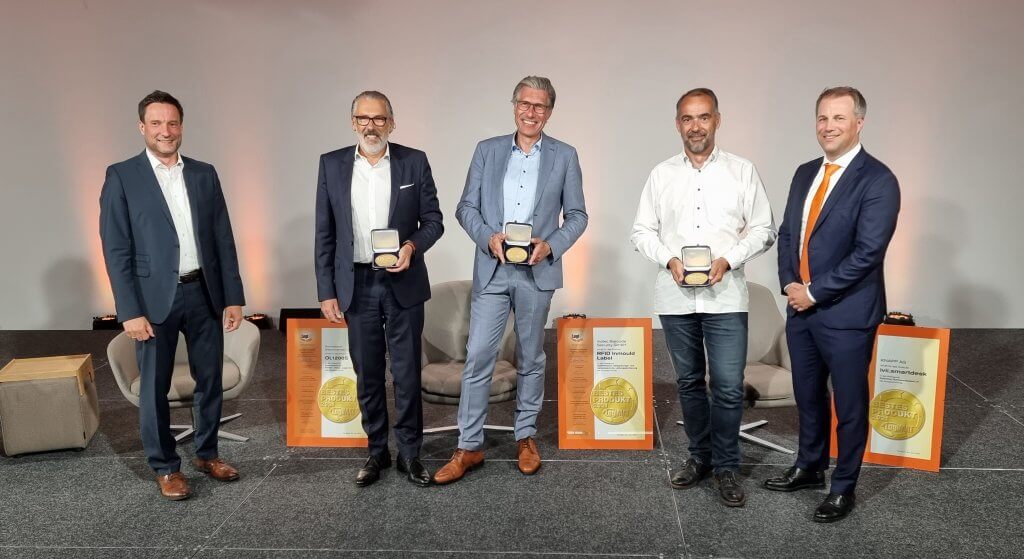
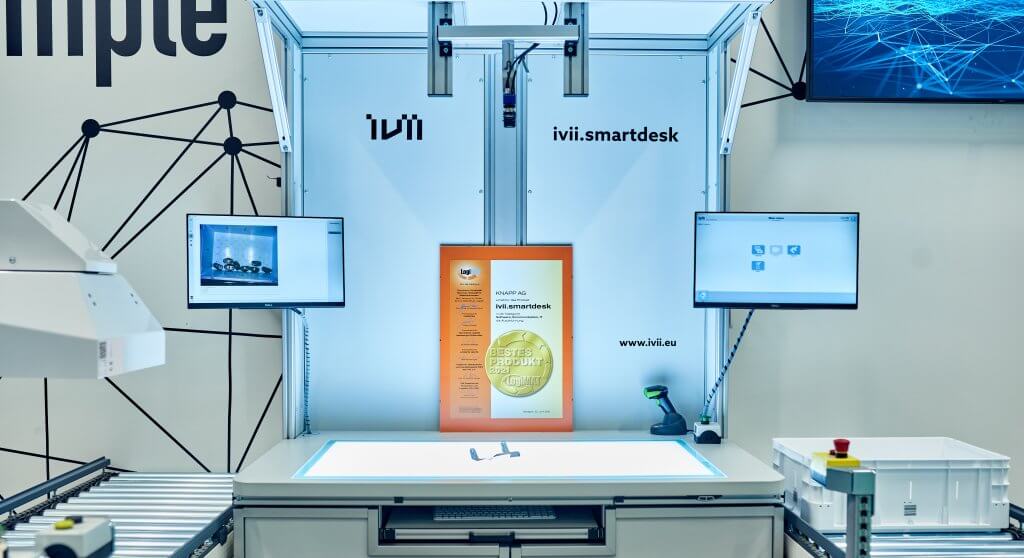
What is the ivii.smartdesk and what’s special about this work station?
The ivii.smartdesk serves as an assembly work station in production and is equipped with an image recognition and processing system. All assembly work is supported by software. The work station has an integrated real-time feedback system, which monitors every work step. This provides a zero-error strategy and end-to-end traceability for the assembly process. The ivii.smartdesk also plays an essential role in the production process controlled by KiSoft: The intelligent KiSoft software controls the supply of materials to the ivii.smartdesk and the conveyance of the products to other areas.
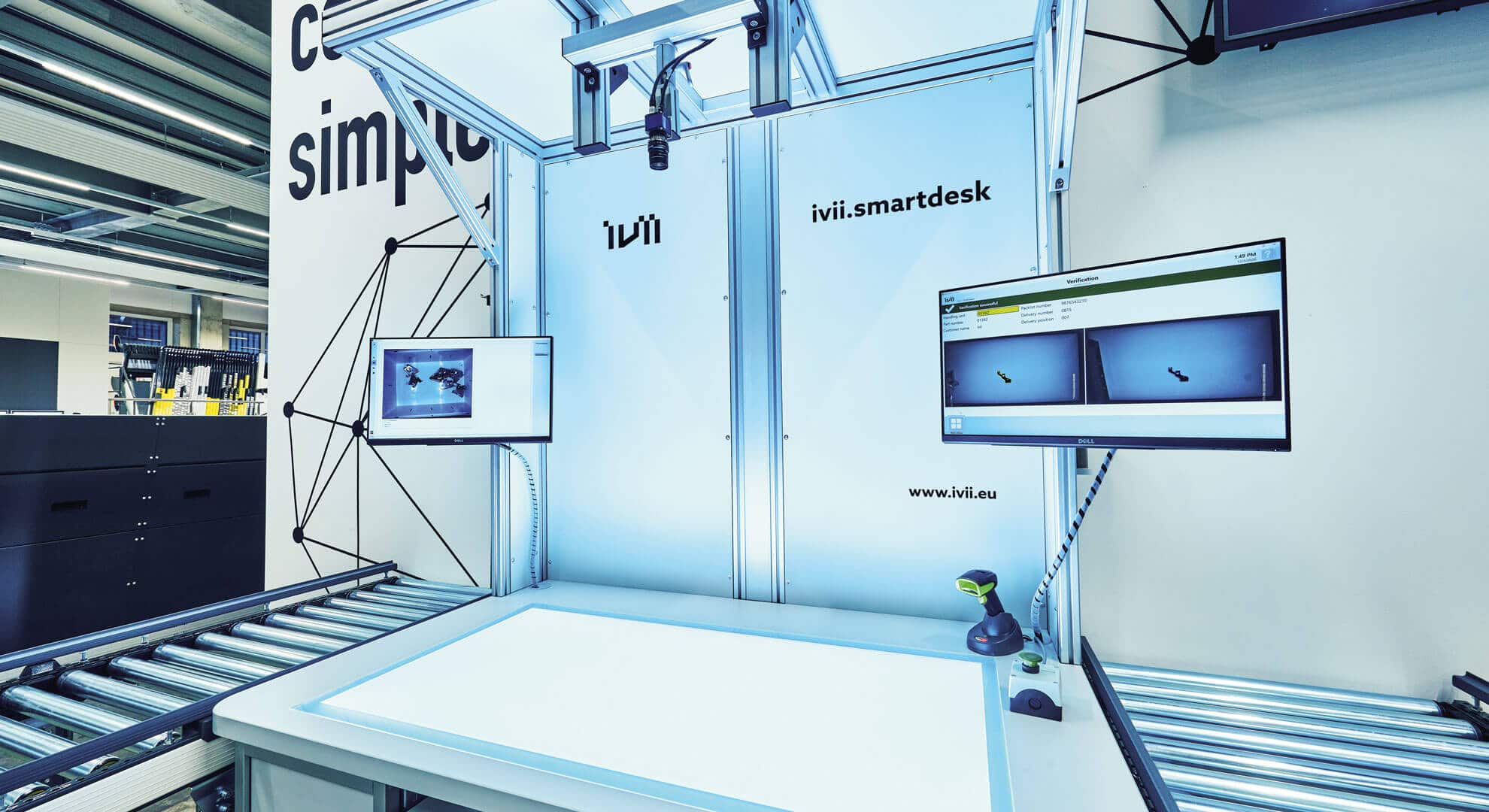
How can the ivii.smartdesk be used in production?
The image recognition and image processing system records all the components required for assembly. Each work step is checked and validated. The next work step is only possible when the image processing system has confirmed the previous one as “OK”. This way, all components are assembled in the right sequence and quality. Thanks to the real-time feedback system, employees receive immediate feedback on the quality of the work step.
Monitors provide an optimal overview of the work in progress at the assembly work station. While one of the monitors displays how the product is supposed to look – the other monitor displays the actual camera image. The components need to be assembled so that the theoretical and actual images match. As soon as the assembly process has been completed, the employee presses a button to begin the final check by the feedback system. One of the monitors shows the result to the employee. Green means that everything is OK, while red indicates that an error has occurred. The possible error is displayed on the monitor and can be corrected immediately by the employee. This is how error-free production becomes a reality.
.
Pankl Racing Systems AG in Kapfenberg, Austria, has also opted for cutting-edge image processing to ensure quality in the assembling process.
The ivii.smartdesk approach is incredibly motivating for our employees. The interaction with the system is almost playful. Our employees don’t view the feedback system as surveillance, but see it as a welcome support for achieving the best possible quality in their work within the quickest possible time in order to attain our goals.
The ivii.smartdesk is the best choice – including for goods-in and goods-out
In the goods-in area, the ivii.smartdesk is used to check whether all the goods have been delivered to the warehouse in the correct quantities and quality. The delivery is documented and saved for the burden of proof later on. This not only saves time, but also lowers costs for returned goods.
The ivii.smartdesk is also suitable for the goods-out procedure. In the goods-out area, the work station is used to check whether the right products are in the right container in the right quantity and quality. This application is perfectly suited for OEM suppliers in the automotive sector as the requirements in this industry are particularly high.
New feature! Recognizing items without barcodes
The ivii.smartdesk recognizes items in a split second without a conventional identifier such as a barcode. The ivii.smartdesk simply compares the item on the desk to data it has on characteristics for that item. This eliminates lengthy searches for an item’s identity in goods-in and goods-out, as well as for returns. With the article number being displayed, the employee can rapidly and correctly match the items. Employees can also easily and accurately enter new items in the system.
In the digital age, companies are constantly striving to balance quality, performance and costs. Jerich International has enhanced their picking work stations with image processing technology by ivii – all while keeping the focus on the person.
Process optimization has clearly progressed. We were able to reduce the six eyes principle to a two eyes principle. The employees can now focus on different activities in the process for which up to now no resources have been available. The table also looks great! Working with new technologies motivates our employees.
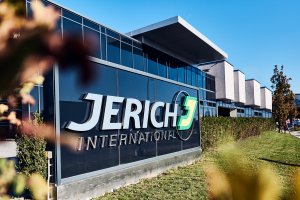
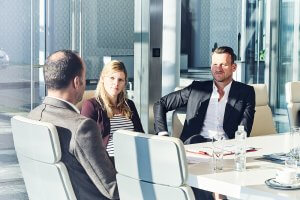
With quality and safety a top priority at Jerich International, opting for the ivii.smartdesk made all the sense in the world.
Humans remain the epicenter of action
The ivii.smartdesk supports workers in their day-to-day work. Thanks to the innovative work station, employees work confidently, knowing that they’re not making errors that are a hassle to correct later on. At the same time, the playful approach to the work steps – gamification – motivates employees, helping to establish a learning organization and increased employee satisfaction.
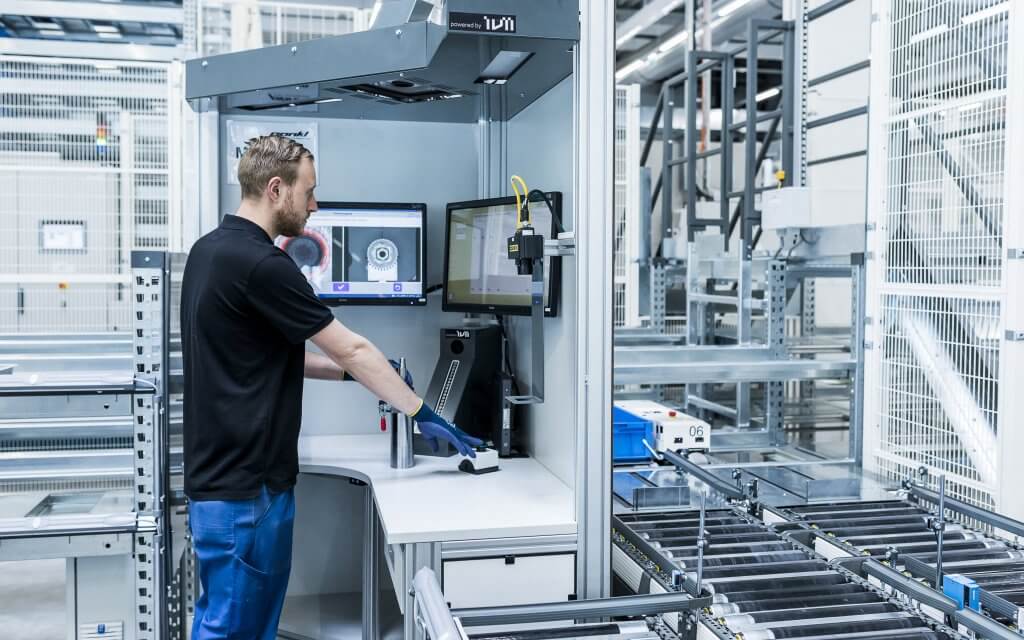
Why is the ivii.smartdesk the ideal choice?
When it comes to meeting and even exceeding current standards in quality, the ivii.smartdesk is the right solution. The innovative technology ensures error-free processes in goods-in and goods-out, thereby reducing costs for returns and the need to correct errors – all while increasing employee satisfaction. The work station also enables new employees to perform well right away, helping to cover the shortage of qualified personnel.
With the ivii.smartdesk, manual processes are digitalized so that quality, performance and safety are all efficiently increased.
The advantages of the ivii.smartdesk at a glance:
Find out more about ivii here.
Further reading recommendations

Optimize intralogistics processes and increase performance using automation. What is the right level of automation for your operation? In this post, we present various levels from innovative manual warehouses up to fully automatic systems.

In logistics, the last mile frequently includes many hurdles to jump that require significant resources. Perfect planning and flexible processes are key to turning these challenges into advantages, such as positive customer experience and reduced costs.
