Customization in the Healthcare business
using a highly-flexible Goods-to-person Solution
Mediq’s innovative service concept is based on customization. Customers ask for special delivery conditions, personalized products such as medicine, care articles, medical equipment or delivery to the patient. Mediq supports nursing staff in hospitals and in private homes in their important work for society. How can such a large range of products, services and different delivery conditions be reconciled? The goods-to-person solution based on OSR Shuttle™ technology enables central processing of the different business models in one warehouse.
You are currently viewing a placeholder content from YouTube. To access the actual content, click the button below. Please note that doing so will share data with third-party providers.
More InformationPerfectly possible with the shuttle technology
By grouping all articles in one warehouse, Mediq can flexibly respond to changing requirements. Furthermore, central storage saves costs. To efficiently organize the large number of different outbound deliveries, all orders must be consolidated in the warehouse and made available for dispatch. This task is performed by the OSR Shuttle™ , a shuttle system with three rack lines, explains Alex Jonker, Executive Vice President, Supply Chain and E-Business, Mediq:
20,000 different articles are stored in the OSR Shuttle™. They are all batch separated. In the medical business it’s important to track batches and they are tracked accordingly in the OSR Shuttle™ system.
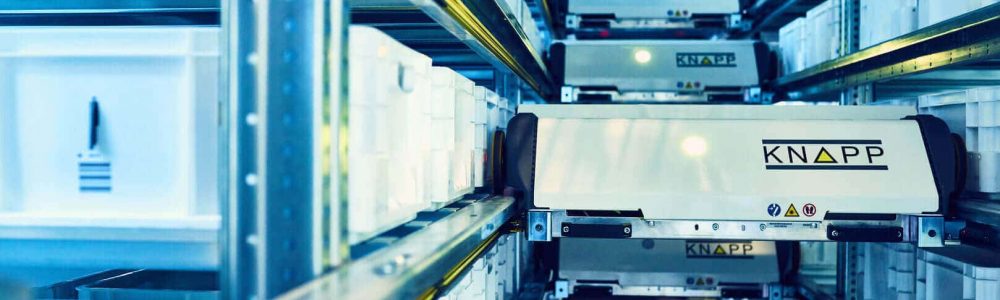
How are the goods stored?
First, the goods are decanted in the goods-in area: All delivered articles are repacked from cartons into storage containers for storage in the OSR Shuttle™. 10 stations are available for this purpose. Containers with sterile articles are automatically identified to ensure they remain closed during storage.
A normal element, which is important in the medical business is sterile articles. A large amount of our assortment needs to be handled sterile. KNAPP worked out a solution where the lids are automatically put on and taken off just before and after the picking process to make it easier for the order picker and also to guarantee the sterility of the articles. The OSR Shuttle™ offers the following advantages to Mediq:

The shuttle system is extremely space-effective thanks to the fact that articles are stored triple-deep.

The shuttle system can be expanded as the business grows.

In this way, either the number of storage locations or the system performance is increased.
How does picking become intuitive, ergonomic and error-free?
The goods-to-person work stations from the Pick-it-Easy series enable ergonomic, intuitive and error-free picking. Mediq opted for the especially ergonomic Pick-it-Easy Shop work stations.
When an order requires a certain article, a container is retrieved from the OSR Shuttle™ and brought towards the Pick-it-Easy stations. At that moment the pickers are picking the orders from the grey totes, put them into the cartons that go directly to the customer. And this is a very efficient process for order picking of slow-moving articles as previously the order picker had to walk towards the articles. In this OSR Shuttle™ system, the articles are retrieved by the robots and brought to the order picker. The goods-to-person principle is the real benefit we get from the KNAPP system.
For which articles is Pick-to-Light used?
Fast-moving articles and oversized units are picked using Pick-to-Light:
- Directly from pallets or
- From flow racks
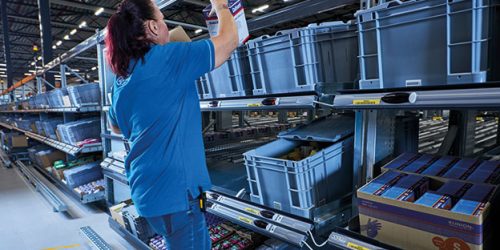
Curious about logistics automation?
Get in touch with our experts today.
How are the packing units prepared for dispatch?
Dispatch sorting and preparational tasks such as:
- Document insertion
- Dispatch carton erection and closing
- Address label application
are carried out automatically. Mediq uses two carton closing lines with document insert stations and address label printers. They process all outbound deliveries also on peak days, reduce unnecessary space in the carton by adapting the carton height and distribute the cartons to 15 dispatch ramps according to their carrier or priority.
Downstream of the KNAPP Pick-it-Easy station, the order proceeds to the check station, where we randomly check the quality of the orders and repack the smallest orders. After the check station, the orders continue their flow and go to the automatic closing station. The boxes are automatically closed, so all the unnecessary air is taken out and the boxes are closed. After that, the orders go to the ramps where they are sorted by carrier. Then, they proceed to the dispatch area to be loaded into the trucks.
What software is used?
All processes are integrated in a SAP® EWM system that seamlessly fits into the KNAPP software environment. This whole process only takes about 15 minutes. This is important for us in terms of the accuracy and the reliability towards our patients.
Both Mediq and KNAPP are very happy about the successful implementation:
KNAPP successfully implemented numerous projects in time and within the budgets of the customers. During the preparation for this project, we were furthermore impressed by how transparent KNAPP was in terms of communication about any topic.
About Mediq:
Mediq is market leader in 12 countries and an important player on the international healthcare market. The company with headquarters in Utrecht, Netherlands, currently employs about 3,000 people. Millions of patients and medical staff who enthusiastically cares for them rely on Mediq to supply them with medical equipment and solutions on a daily basis. As reliable partner for patients, healthcare professionals and health insurance companies, Mediq is constantly striving to increase the efficiency and affordability of healthcare products.