Have you ever asked yourself what a Central Belt System is, why we need lifecycle management or how cross-docking works? What does KNAPP mean by zero defect and why is our motto making complexity simple? Batch picking, decanting, retrofit – these are the ABCs of logistics. We explain terms from the complex world of value chains and illustrate them using pictures and videos. No query is left behind!
Automation
The aim of automation, for example in a warehouse, is to make repetitive tasks more efficient using automation technologies, thereby relieving strain on employees and increasing productivity. Depending on a company’s individual goals and business model, different degrees of automation can be implemented from semi-automatic to fully automatic. In this process, flexibility is the key as well as being able to respond to business changes. This can be achieved by combining intelligent technologies, such as automated storage systems, robots with AI, pocket sorter systems, autopickers, mobile robots and of course the right software solution.
Batch Picking
Order picking method in which an associate picks several items of the same SKU for multiple orders at the same time. The items are later consolidated for the individual final customer orders in a central work zone. Our semi-automatic solutions use Pick-to-Light or Put-to-Light technologies as well as voice-directed picking to assist employees during picking.
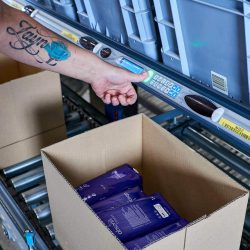
Central Belt System
The Central Belt System is an all-in-one solution for automatic article picking which is typically used in pharmaceutical wholesale and in the cosmetics retail sector. The solution is especially suited for high throughputs and high delivery quality, for example, to supply pharmacies several times a day. Different ejectors automatically eject the articles onto a conveyor belt – the central belt conveyor. An intelligent camera system carries out 100 percent checks as well as track and trace. By the way: our company founder, Günter Knapp, invented the first automatic picking machine and precursor of the Central Belt System.
Decanting
Decanting refers to the process of repacking goods into storage containers in the goods-in area before the containers are put away in a storage system such as the OSR Shuttle™ Evo. Repacking is carried out either by hand or automatically using our Pick-it-Easy Robot.
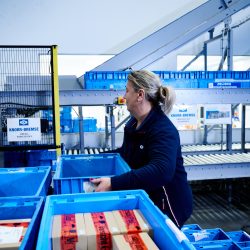
E-Commerce Fulfillment
The logistics for e-commerce retailers are often very complex. In a warehouse, it is important to bring order to the chaos. The pocket sorter system is the perfect solution. It transports all goods as single items in a system and enables fast handling of a large number of customer purchase orders and returns. Thanks to intelligent software tools, it becomes easy to prepare for sales peaks such as Black Friday.
FIFO
First in – First out. In warehouse logistics, this term refers to the process of first retrieving articles that have been stored first. This principle is above all used in the food retail sector where articles have a date mark.
Global Trade Item Number (GTIN)
Formerly known as the European Article Number (EAN), the Global Trade Item Number is a globally unique identification number used to label articles. It is often equated with the bar code.
Healthcare
Together with fashion, retail, food retail, wholesale and industry, healthcare is one of our core business areas. We cut our automation teeth in the healthcare sector, so our experience goes way back. We initially gained our expertise in single-item picking in this sector. Today, we provide support to more than 1,400 pharma companies in every aspect of their value chains. We provide solutions for production, pre-wholesale and wholesale, as well as for supplying healthcare facilities and pharmacies. At KNAPP, we are doing our part all over the world to create strong and safe value chains in the healthcare sector that customers and patients can rely upon.
Italy
The first foreign KNAPP subsidiary was founded in Italy in the 1990s. In the meantime, we now have 53 sites and more than 6,000 employees all around the world providing the best service to our customers.
Just in time delivery
Just in time delivery is the delivery of goods at a pre-arranged time to be used in production precisely when they are needed without being stored beforehand. By this, producing companies can greatly reduce their own warehouse stock.
KiSoft
Thanks to the logistics software KiSoft, KNAPP can provide tailor-made software solutions for all business processes. KiSoft doesn’t just cover vertical integration, such as machine control, warehouse control and warehouse management. It also makes horizontal integration possible along the entire value chain, all the way to the point of sale or end customer and all supported with analytics and transport management.
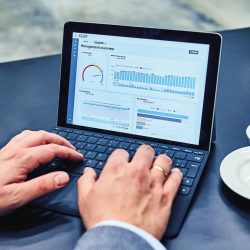
Lifecycle Management
This means ongoing support for our customers’ installations. We document the life cycle of the installed components by actively monitoring their KNAPP systems. We keep very close track of our suppliers and keep our customers up to date. To meet new requirements, we adapt and optimize existing systems and services. This type of agile partnership ensures the long-term success for our customers.
making complexity simple
We simplify the complex demands of value chains and using digitalization and intelligent automation. making complexity simple is more than a slogan, it is part of our philosophy and guides us in all our activities.
Network
Intelligent networks create new ways of interacting with customers and new opportunities for profitability. It is vital to think end-to-end. In the future, it will be increasingly important to create linked value chains that include production, distribution and the end customer. Smart technologies and processes will be the critical factors in making this success possible.
OSR Shuttle™ Evo
Our Order Storage & Retrieval system, an automated storage and picking system, has forever changed the face of intralogistics. The first OSR was put into operation in 2003. Initially scoffed at, it soon became state of the art. Shuttle systems are ideal for extremely high throughputs and bring new energy and ideas to order fulfillment.
Video: OSR Shuttle™ Evo – the new simplicity
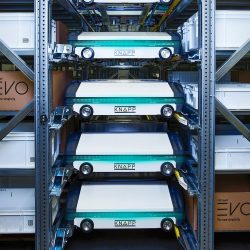
Pick-it-Easy Robot
The picking robot can be used in a variety of industries. Using its artificial intelligence, the Pick-it-Easy Robot is able to see and grip items (almost) like a person, so it can handle a broad item range gently and reliably. This includes items wrapped in film, glass bottles or floppy items such as socks.
Quality assurance
No more production errors. Within a fraction of a second, the ivii smartdesk checks each work step, thus ensuring that everything is done properly. Even better than the human eye, digital vision allows the ivii smartdesk to detect the smallest deviations as the system learns what the ideal looks like. Employees receive prompt feedback and can work confidently, knowing that they haven’t made any mistakes.
Retrofit
Retrofit is more than just the replacement of outdated components and installing technological innovations: we make our customer’s installations fit for the future. Besides the modernization through upgrades for mechatronics and software, it is also important to closely re-examine the system design. When based on the customer’s current and future business requirements, a retrofit ensures maximum sustainability and performance.
Shuttle technology
The autonomous mobile robots connect different areas within facilities quickly and efficiently, bringing goods, raw materials and components to where they need to be. This way, every work station can access every item in the central storage system, including work stations located at a distance and temporary work areas. Thanks to their innovative technology, Open Shuttles act with complete autonomy, they don’t need any aids, and they are 100 percent safe for people.
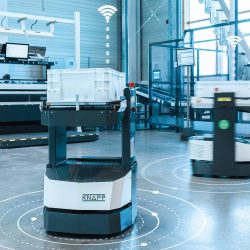
Twenty-four/seven (24/7)
Shop around the clock – this service is rapidly gaining value among consumers. Our solution for this is RetailStore. This is an in-store small robotic warehouse that handles the extensive range of products intelligently, storing them securely in minimal space. Features such as engaging interactive screens, a self-service checkout or a 24/7 vending compartment all make RetailStore an intelligent and attractive tool.
Usability
Usability is important to us. And for KNAPP software, easyUse is the design concept for all graphical user interfaces. The design makes human-machine communication a snap, providing the user with step by step guidance for error-free working. Uniform colors, simple symbols and precise instructions raise the quality in order processing for motivated and satisfied employees.
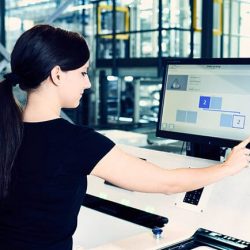
Value Chain Tech Partner
This is what we want to be for our customers: A strong partner for the long run who provides the right technologies for digitization and automation and links all steps of the value chain in a profitable way so your business can continue to grow.
Weighing and measurement systems
Weight, length, width and height are important master data and form the basis for smooth logics processes. With the automatic and reliable capture of dimension and weight data, MultiScan delivers the master data essential to optimizing supply chains at the push of a button.
X-Docking
Cross-docking describes a way of moving goods. The goods are not stored in the warehouse but are moved directly from receiving to shipping and on to the end customer. When being used successfully it reduces costs in the warehouse.
Yard Management
Yard management represents the bridge between transport and warehouse logistics. It comprises all measures and methods used for the cost- and time-optimized control of activities on the plant premises. This includes both company-owned and third-party vehicles.
zero defect
With this philosophy, KNAPP uses quality control and to make corrections directly in the process. Human and machine work hand in hand and employees receive immediate feedback on the quality of their work. This reduces costs and raises employee satisfaction. The core technology in the zero defect warehouse is the intelligent image recognition and image processing system.
Blog post: Error-free patient care thanks to zero-defect solutions