Shuttle storage systems are the backbone of countless automated applications in various industry branches. They are vital for supplying consumers with groceries, medicinal products and other convenience goods. How? These systems cover important processes and applications in a warehouse, such as picking, buffering and sequencing of goods and orders. But what happens if a storage system has been in operation for decades and its product life cycle is coming to an end? In this case, operating companies can either invest in a new system or they can consider a retrofit. Many companies opt for the latter due to the uncertain market situation and rising costs for storage space and raw materials.
When does a shuttle retrofit make sense?
When the parts and systems installed in your warehouse have been in operation for quite a few years, this is reflected in their product life cycle. Is the supply or availability of spare parts becoming a problem or has your business model changed over the years? Factors like these speak in favor of a retrofit, which replaces outdated components with new, innovative system technology to extend the product life cycle of your system. These adaptations prepare you for the challenges of your sector and allow you to benefit from higher operational reliability and spare parts availability.
However, a retrofit may not always be the best decision for your warehouse. That’s why the first step is to thoroughly evaluate your current situation. This immediately raises an important question: When would be the ideal time to do a retrofit?
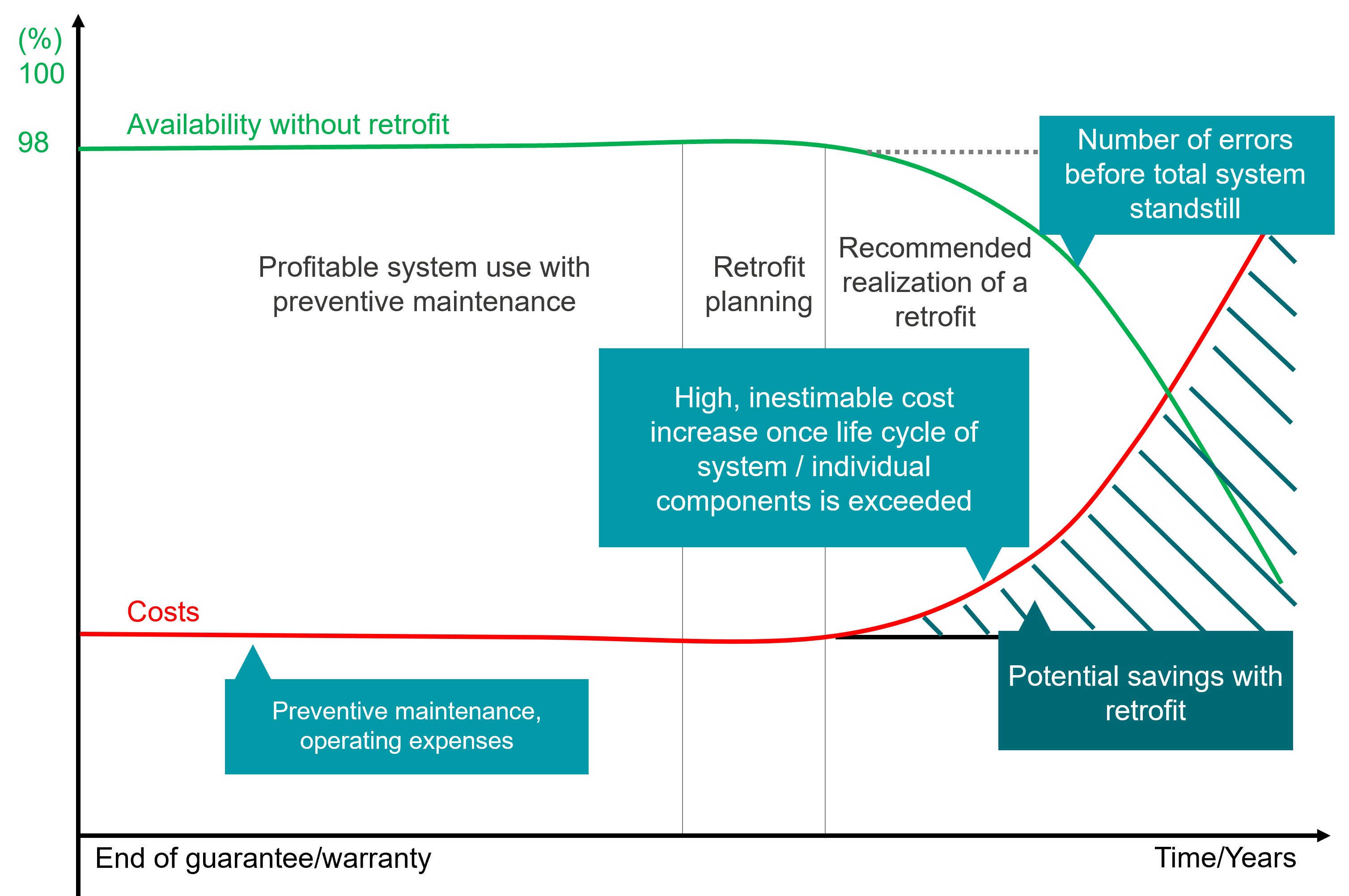
When is the most suitable time for a retrofit? [1]
Eight steps to successfully retrofit your shuttle storage system
Once the ideal time for a retrofit has been defined, it is implemented step by step. Since shuttle storage systems cover the most important processes in a warehouse – often truly the center of a logistics system – we’d like to show you a practical example of how a retrofit of such a system is carried out. In KNAPP Customer Service, we follow a step-by-step plan:
You are currently viewing a placeholder content from YouTube. To access the actual content, click the button below. Please note that doing so will share data with third-party providers.
More InformationAdvantages of retrofitting a shuttle storage system
Many customers are considering a retrofit due to the uncertain market situation and rising costs for storage space and raw materials. These might be the most obvious reasons, however retrofits come with many more advantages:
Reduces costs
- Significantly lower investment than purchasing a new installation
- Reduced operational costs, such as for maintenance and repair thanks to new components
Greener
- Reduced current consumption and emissions during the modification because the existing steel construction of the shuttle storage system remains intact
- Only planned standstills, normal operation continues
More safety and security
- Implementation of the latest hardware as well as electrical and mechatronic components
- Protection from cyber attacks thanks to the latest software versions
- Retrofit of your safety system according to the latest KNAPP standards (KNAPP Lock system, self-closing trap doors and more)
Retrofit for the long haul
- Ensured supply of original spare parts
Example: Reduction in CO2 emissions through shuttle storage system retrofit
To showcase the environmental friendliness of a retrofit project, picture this: An operating company has a logistics system with a shuttle storage system with the following dimensions:
- Surface area: 953 m² (~10,000 sq ft)
- Height: 5.6 m (~18 ft)
- Rack weight: 573 t
- No. of aisles: 8
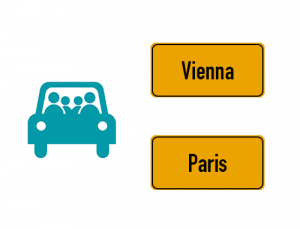
x 6,132
Retrofitting this system saves 1,486 tons of CO2 emissions compared to building a new shuttle storage system. The emissions saved by this retrofit equal a car driving from Vienna to Paris roughly 6,132 times. Therefore, retrofitting your warehouse not only prepares you for the future demands in logistics but is good for the environment as well.
A retrofit yields remarkable results
Retrofitting a shuttle storage system involves more than just upgrading the hardware and software or replacing old parts. We get down to the nitty-gritty by testing all the processes and components and designing a solution that meets the current requirements of operating companies.
Are you also facing the same challenges? Are you considering a retrofit? We are here to help! Together, we’ll find the best solution for your specific use case. Drop us a line and schedule a meeting with one of our retrofit experts.
New dimensions of knowledge

Love a technical challenge? Are you an open and communicative person? Then check out this interview with our colleague Seldin: He tells us all about his job as a Service Delivery Manager.

Your SAP® EWM has gone live. What’s next? What 6 questions should you ask yourself about SAP® EWM support after your system goes live? Read on and find out in this blog post.

Exciting, varied and challenging – the job of a software developer in KNAPP Customer Service is never dull. We sat down for an interview with our colleague Andreas Kraßnig. In this interview, Andreas tells us what his job entails and why he is so passionate about what he does.
Further reading recommendations

Love a technical challenge? Are you an open and communicative person? Then check out this interview with our colleague Seldin: He tells us all about his job as a Service Delivery Manager.

Your SAP® EWM has gone live. What’s next? What 6 questions should you ask yourself about SAP® EWM support after your system goes live? Read on and find out in this blog post.

Optimize intralogistics processes and increase performance using automation. What is the right level of automation for your operation? In this post, we present various levels from innovative manual warehouses up to fully automatic systems.