It’s that easy: Kramp relies on the Evo Shuttle
When the international Kramp Groep with headquarters in Varsseveld, the Netherlands, was founded in 1951, Johan Kramp was a one-man operation. Today, Kramp is Europe’s largest specialist for spare parts and supplies for the agricultural sector and is on course for strong growth. In preparation for this growth and to further improve the service for their customers, Kramp opted for an automation solution featuring the Evo Shuttle.
You are currently viewing a placeholder content from YouTube. To access the actual content, click the button below. Please note that doing so will share data with third-party providers.
More InformationLogistics made easy
Kramp. It’s that easy. The logistics at the company headquarters in Varsseveld was to function in keeping with the company slogan: Easy handling of more than 200,000 products of their large stock with the least amount of effort and delivered overnight to customers. The following challenges were to be mastered:
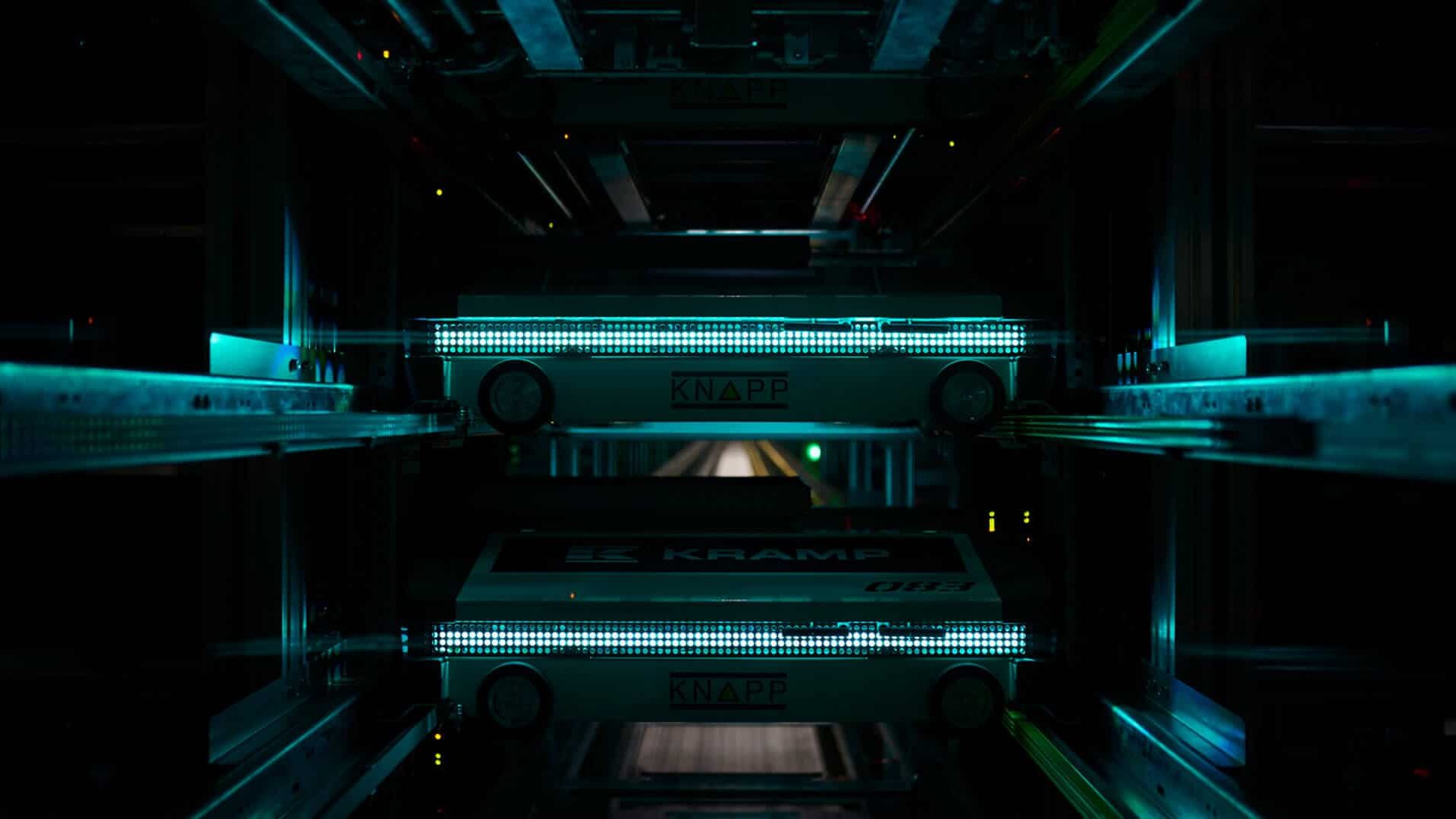

Ordered today, delivered tomorrow
The interplay between an innovative shuttle system, ergonomically designed work stations and an intelligent software solution support Kramp in continuously optimizing their service for customers.
- Intelligent software solution with KiSoft
- Evo Shuttle for fast-, medium- and slow-moving items as well as overstock
storage locations
Pick-it-Easy work stations
order lines per hour by project completion
For this modernization, Kramp wanted twice the storage capacity and four times the performance. Our Evo Shuttle 2D was able to fulfill these requirements and convince Kramp.
Evo Shuttle:
More than just an automatic storage system
The heart and highlight of the solution is the Evo Shuttle. The automatic storage system is 80 meters long, 25 meters wide and 18 meters high (roughly 260 x 82 x 59 feet). Currently, it comprises six rack line systems with 134,400 storage locations and 120 shuttles.
The distinctive system design of the Evo Shuttle offers the possibility of decoupling performance and storage capacity from one another. The shuttles can change between rack line systems if necessary, allowing them to access all the items on a single level. If higher performance is needed, several shuttles can also be installed on each level to increase throughput.
Thanks to its modular structure, the system can easily be extended step by step. By the end, the output will be 9,600 order lines per hour. The rack can be extended to 13 rack line systems with 291,000 storage locations. This provides plenty of room for storage and future growth.
Pick-it-Easy:
Ergonomics, performance and efficiency
Regardless of the sales channel, all the goods are picked according to the goods-to-person principle. There are eight ergonomically designed goods-to-person work stations from the Pick-it-Easy series for efficient manual single item picking. Employees always receive the goods in the right sequence and at a comfortable height. Intuitive easyUse user interfaces support them in the error-free processing of orders.
The Pick-it-Easy work stations also allow for efficient one-stop handling: The items are picked directly from the source cartons into the dispatch cartons. Each item is therefore handled only once before being shipped. The target container is directly fed to the Pick-it-Easy work station where order picking is completed. This boosts efficiency while simultaneously reducing the workload.
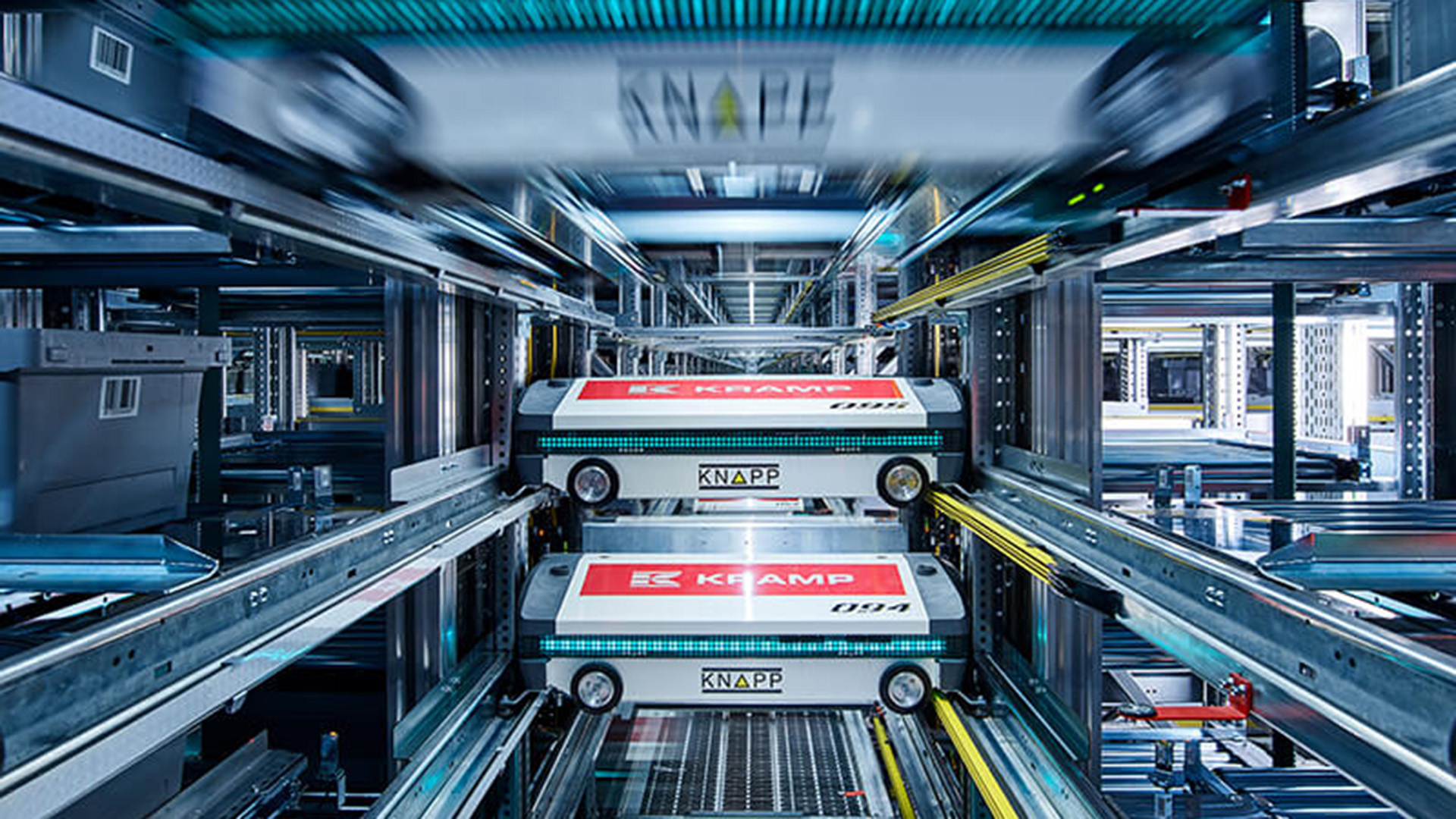
How does the automation solution benefit Kramp?
Data-driven system
All-in-one solution that includes software, a complete overview of the warehouse stock, highest availability and an intelligent system design
Dynamic access
All the items in the system can be accessed from any work station
Optimal space utilization
Flexible rack line system; streamlined system design; increased storage density of stored items
Performance on demand
Scalable number of shuttles and lifts mean that the design can be fine-tuned; shuttles can move lengthwise and crosswise within the rack and can switch between rack line systems
More than just storage
Central storage of stock and overstock; all important processes handled in one system: Buffering, precise sequencing, picking, supply of warehouse areas
KiSoft: The intelligence for optimal system use
KiSoft – the central software for the intelligent integration of human and machine – ensures that orders are picked correctly and delivered overnight. As early as during the storage process, KiSoft selects the ideal storage location for each item to ensure that the weight on the rack is distributed evenly and all the items can be accessed smoothly. By directly controlling all components in the warehouse, KiSoft makes each item available at the work stations in the required order and with maximum performance.
KiSoft makes it possible to optimally spread order processing throughout the day to smooth out peaks in the work load. If required, the orders can be buffered in the Evo Shuttle. The order is retrieved and prepared for shipping shortly before its dispatch time. This way, the space needed at the dispatch staging area is kept to a minimum and the dispatch process is kept as lean as possible.
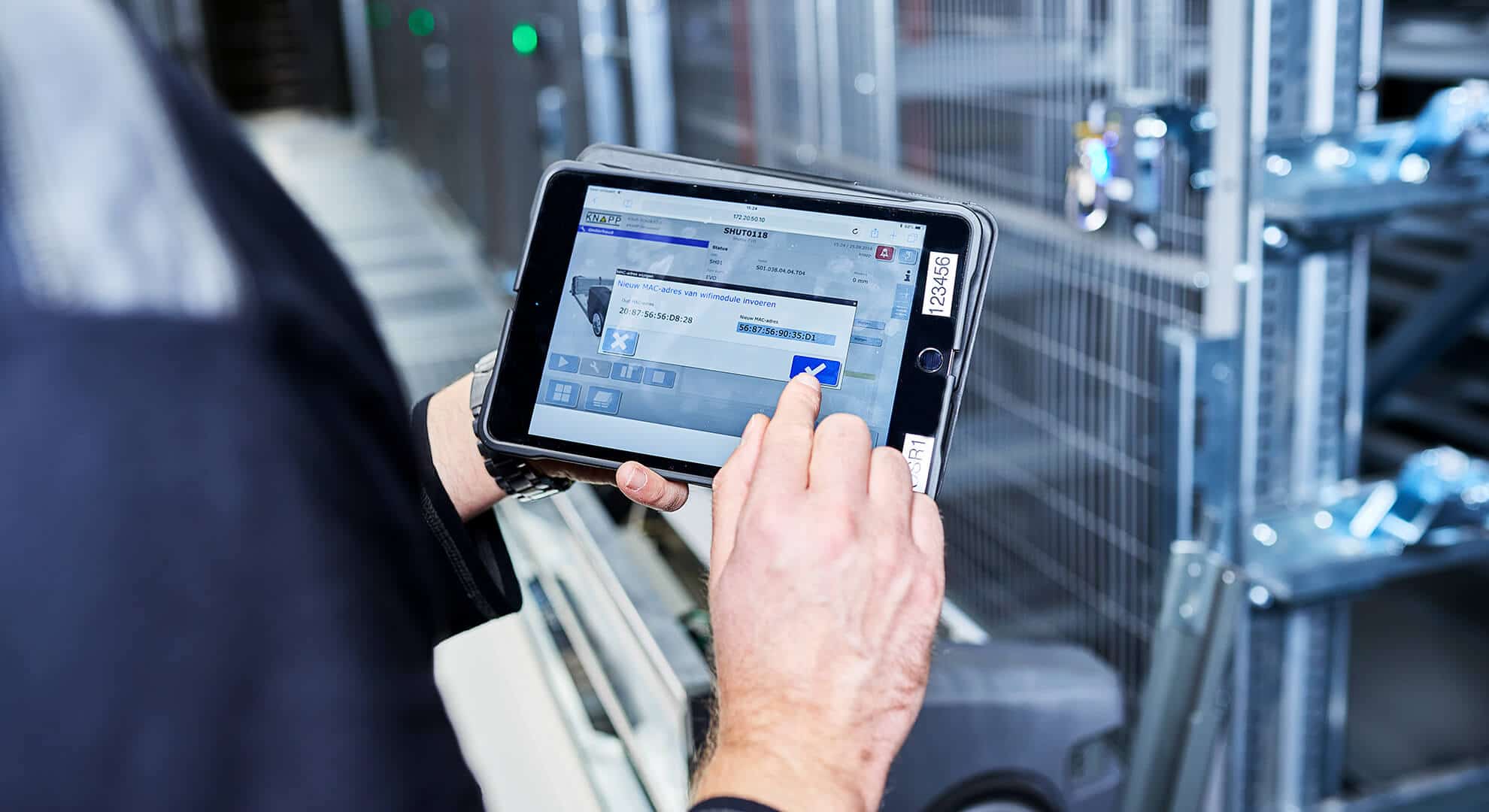
KiSoft SCADA
KiSoft SCADA provides a clear visualization of the entire system and complete overview of the technical state of all the components within the system. The software provides more than visualization, it also provides a key function in the maintenance of individual components. It can be used on a range of different end devices, for example at the control center using several monitors or on a tablet for maintenance work carried out directly on the component.
Do you want to learn more about logistics automation?
Get in touch with our experts today.